Materials:
- Concrete blocks: 100 units of 8x8x16 inches
- Gravel: 2 cubic yards
- Landscape fabric: 100 square feet
- Drainage pipe: 20 feet
- Compactable base material: 3 cubic yards
- Concrete adhesive: 5 tubes
DIY Steps:
-
Site Preparation
- Measure and mark the area where the retaining wall will be installed
- Clear the site of any debris or vegetation
- Excavate the area to the required depth
-
Base Installation
- Spread and compact the base material evenly
- Check for levelness using a carpenter's level
- Compact the base material using a compactor
-
Block Placement
- Start laying the first row of blocks, ensuring they are level
- Stagger the blocks on the subsequent rows for stability
- Use concrete adhesive to secure the blocks in place
-
Drainage Installation
- Lay the drainage pipe behind the first row of blocks
- Fill the area behind the wall with gravel for proper drainage
- Cover the backfilled area with landscape fabric
Technical Aspects:
- Tools: Shovel, wheelbarrow, level, compactor
- Timing: Plan for 2-3 days depending on the wall size
- Techniques: Ensure proper base compaction for long-lasting stability
DIY Project Process:
Sequential Steps
- Excavate the area and level the ground
- Lay the base material and compact it thoroughly
- Start placing the blocks, checking for levelness after each row
- Install drainage pipe and backfill with gravel
- Secure the top row of blocks with concrete adhesive
Troubleshooting Tips:
- If the wall is not level, disassemble and realign the blocks
- Ensure proper drainage to prevent water buildup behind the wall
This detailed guide provides a comprehensive overview of the materials, steps, technical aspects, and troubleshooting tips involved in installing a block retaining wall, ensuring a successful DIY project for housewives and homeowners.
Factors Impacting Block Retaining Wall Installation Costs

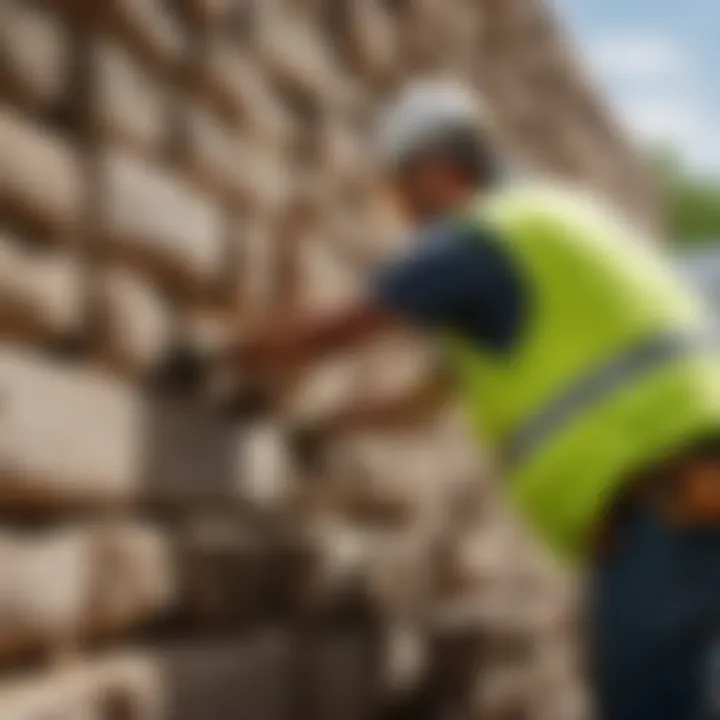
In the realm of block retaining wall installation, costs are a crucial aspect that requires meticulous consideration. Understanding the different elements that influence these costs is integral to planning and executing a successful project. Factors impacting block retaining wall installation costs encompass a range of essential components that shape the financial implications of such an endeavor. By delving into the specifics of materials, labor, site preparation, and additional expenses, individuals embarking on block retaining wall construction gain invaluable insights into the complexities of cost management.
Materials
Types of Blocks
The choice of blocks for a retaining wall plays a pivotal role in determining not only the structural integrity but also the overall aesthetics of the finished project. Various types of blocks are available, each with its unique characteristics and benefits. Selecting the right type of blocks can significantly impact the cost efficiency and durability of the structure. Opting for high-quality blocks ensures longevity and minimizes maintenance needs.
Quality of Blocks
The quality of blocks used in the construction of a retaining wall directly correlates with its strength and longevity. Investing in superior quality blocks may incur higher initial costs but proves to be a cost-effective decision in the long run. High-quality blocks offer superior performance in terms of load-bearing capacity and resistance to environmental elements, thereby enhancing the overall value of the structure.
Additional Materials (e.g., drainage pipes, geogrid reinforcement)
In addition to the primary blocks, several supplementary materials contribute to the stability and functionality of a retaining wall. Drainage pipes facilitate proper water management, preventing water buildup behind the wall that can lead to structural issues. Geogrid reinforcement enhances the stability of the wall, especially in high-pressure scenarios. While these additional materials incur extra expenses, they are crucial for ensuring the longevity and performance of the retaining wall.
Labor
Skilled vs. Unskilled Labor
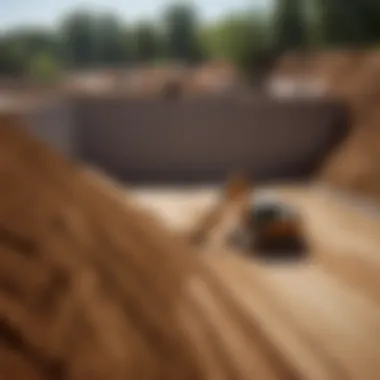
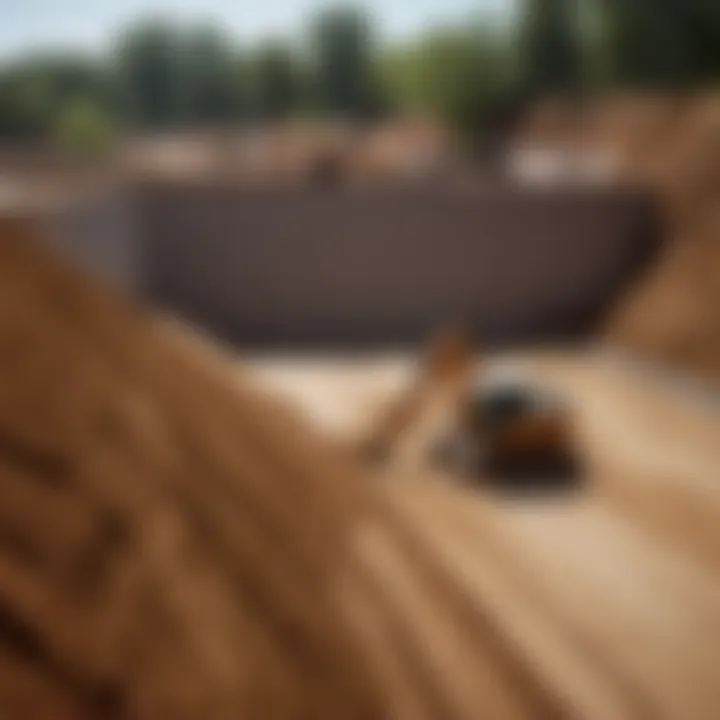
The choice between skilled and unskilled labor can significantly impact the quality and efficiency of block retaining wall installation. Skilled labor brings expertise and precision to the construction process, resulting in a structurally sound and visually appealing final product. On the other hand, unskilled labor may lead to errors, rework, and potential safety hazards, ultimately increasing costs and causing delays.
Union vs. Non-union Workers
Another consideration in labor costs is the employment of unionized or non-unionized workers. Union workers often come with standardized wages, benefits, and work hours, which can impact the overall labor costs. Non-union workers may offer flexibility in terms of rates but could lack the oversight and professional standards that unions provide.
Labor Costs per Hour
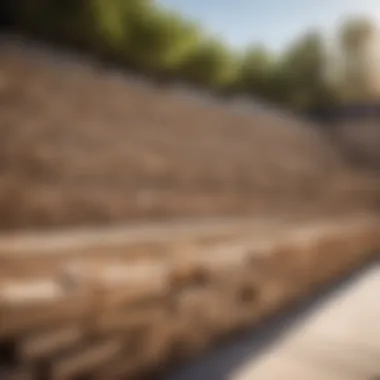

Understanding the labor costs per hour is essential for accurate budgeting and project estimation. Labor costs contribute significantly to the overall expenditure of block retaining wall installation. By analyzing and comparing the hourly rates of different labor sources, project managers can make informed decisions to optimize costs while ensuring quality craftsmanship and timely completion.
Site Preparation
Excavation
Excavation is a fundamental aspect of site preparation for block retaining wall installation. Proper excavation ensures a stable foundation and adequate space for the wall structure. The depth and extent of excavation required can vary based on soil conditions, local regulations, and the specific design of the wall. Quality excavation is crucial for the long-term stability and performance of the retaining wall.
Grading
Grading the site involves leveling the ground and creating a uniform surface layout for the retaining wall installation. Proper grading facilitates proper drainage, prevents erosion, and enhances the overall aesthetics of the project. Attention to detail in grading contributes to the structural integrity and visual appeal of the retaining wall.
Clearing Obstacles (e.g., trees, rocks)
Clearing obstacles such as trees and rocks from the site is vital to ensure a smooth construction process and prevent potential hazards. Removing impediments allows for unobstructed access and workspace for the installation team, promoting efficiency and safety. Clearing obstacles upfront minimizes disruptions and delays during the construction phase.
Additional Expenses
Permits and Inspections
Securing permits and undergoing inspections are necessary steps in ensuring compliance with local building codes and regulations. Permit costs vary depending on the location, project size, and complexity of the retaining wall design. Professional inspections contribute to quality assurance and adherence to safety standards, warranting additional expenses but ensuring peace of mind for homeowners.
Equipment Rental
Renting specialized equipment for block retaining wall installation is a common practice that incurs additional costs. Equipment such as excavators, compaction tools, and masonry saws are essential for efficient and precise construction. While equipment rental adds to the overall expenses, it streamlines the installation process and enhances productivity.
Waste Disposal
Proper disposal of construction waste and debris is a crucial component of any building project, including block retaining wall installation. Waste disposal costs typically involve transportation fees, landfill charges, and recycling expenses. By factoring in waste disposal considerations from the planning stage, homeowners can ensure a clean and environmentally responsible construction process.
Cost Breakdown of Block Retaining Wall Installation
When embarking on the journey of constructing a block retaining wall, understanding the intricacies of the cost breakdown becomes paramount. This section aims to delve deep into the core elements that shape the overall expenses associated with such a project. From material costs to labor expenditures and equipment fees, every aspect plays a crucial role in determining the financial implications of block retaining wall installation.
Cost Components
Material Costs
Material costs form a significant component of the overall expenses incurred in constructing a block retaining wall. The quality and types of blocks chosen for the project, along with any additional materials such as drainage pipes and geogrid reinforcement, directly influence the final budget. Opting for high-quality blocks can enhance longevity and durability, albeit at a higher initial cost. However, selecting budget-friendly options may compromise on long-term durability. Balancing quality with cost-effectiveness is key when considering material costs.
Labor Costs
Labor costs contribute significantly to the cost breakdown of block retaining wall installation. Deciding between skilled and unskilled labor, union and non-union workers, and understanding the labor costs per hour are pivotal factors that impact the budget. Skilled labor often demands higher wages but brings expertise to the project, ensuring quality workmanship. On the other hand, unskilled labor may offer cost savings but could compromise on the project's execution quality. Careful consideration of labor costs is essential to strike a balance between budget constraints and project excellence.
Equipment Costs
Equipment costs play a vital role in the overall cost breakdown, as specialized machinery and tools are essential for efficient construction. The type and quantity of equipment required, along with any rental fees, need to be factored into the budget. Investing in modern and well-maintained equipment can streamline the construction process, potentially reducing labor hours and overall project duration. However, equipment costs can escalate quickly, emphasizing the need for prudent planning and budget allocation in this area.
Permit and Inspection Costs
Permit and inspection costs are often overlooked but are critical aspects of the cost breakdown for block retaining wall installation. Acquiring the necessary permits and undergoing inspections ensures compliance with local regulations and standards. Permit fees vary based on the project scope and location, with additional costs incurred for re-inspections or modifications. Prioritizing permit and inspection costs safeguards the project against potential legal issues and ensures a smooth construction process.
Miscellaneous Expenses
Miscellaneous expenses encompass various additional costs that may arise during the construction of a block retaining wall. These can include expenses related to permits and inspections, equipment rental, and waste disposal. While individually these costs may seem insignificant, collectively they contribute significantly to the overall budget. Budgeting adequately for miscellaneous expenses is crucial to avoid unforeseen financial strains and delays in project completion.
Calculating Total Costs
Estimating Materials Needed
Estimating the materials required for constructing a block retaining wall is a fundamental step in calculating total costs. Accurately gauging the quantity of blocks, adhesive, and additional materials ensures that the budget aligns with the project's needs. Overestimating can lead to unnecessary expenses, while underestimating may delay the project and incur additional costs for rush orders. Precision in estimating materials is essential for cost-effective project execution.
Determining Labor Hours
Determining the labor hours needed for the project is a critical factor in calculating total costs. Efficiently scheduling labor tasks, optimizing productivity, and minimizing idle time are key strategies to control labor expenses. Allocating the right amount of labor hours based on the project complexity and scope prevents budget overruns and ensures timely completion. Careful planning and supervision are essential in maximizing labor efficiency and cost-effectiveness.
Factoring in Equipment Rental
Factoring in equipment rental costs is a vital aspect of calculating total expenses for block retaining wall installation. Evaluating the need for specialized equipment, comparing rental prices, and negotiating favorable terms are essential steps in budgeting for equipment costs. Utilizing equipment efficiently to minimize rental duration and coordinating equipment usage with labor tasks optimizes cost-effectiveness. Strategic planning and oversight of equipment rental contribute to overall project savings.
Including Permit Fees
Including permit fees in the cost estimation is a non-negotiable aspect when calculating total expenses for block retaining wall installation. Ensuring compliance with building codes and regulations requires obtaining permits, which come with associated fees. Ignoring permit fees can result in legal complications, project delays, and unforeseen expenses. Proactive budgeting for permits and fees is indispensable for a smooth and hassle-free construction process.
Accounting for Contingencies
Accounting for contingencies in the cost breakdown is a prudent practice to mitigate unforeseen circumstances that may affect project costs. Contingencies account for unexpected events such as material price fluctuations, weather delays, or design modifications. Allocating a contingency fund within the budget serves as a financial buffer, providing flexibility to address unforeseen challenges without derailing the project timeline or budget. Thoughtful consideration of contingencies is essential for prudent financial management and project success.
Cost Variances
Regional Pricing Disparities
Regional pricing disparities can significantly impact the cost variations in block retaining wall installation projects. Differences in material costs, labor rates, and permit fees across regions influence the overall project budget. Understanding and adapting to regional pricing disparities help in budget planning and cost optimization. Local market analysis and strategic sourcing play a crucial role in mitigating the effects of regional price variations and ensuring cost efficiency.
Seasonal Fluctuations
Seasonal fluctuations can introduce cost uncertainties in block retaining wall installation projects. Weather conditions, demand fluctuations, and supply chain disruptions during different seasons can affect material prices and labor availability. Anticipating seasonal challenges and adjusting project timelines or resource allocation according to seasonal trends minimizes cost escalations. Strategic project scheduling and proactive risk management are essential to navigate seasonal fluctuations effectively and maintain budget integrity.
Customization and Design Complexity
Customization requirements and design complexity of block retaining walls introduce cost variations based on project specifications and intricacies. Tailored design elements, intricate patterns, or unique material selections elevate costs due to increased labor, material, and design expenses. Balancing customization desires with budget constraints is crucial to prevent budget overruns. Collaborating closely with design professionals and contractors to streamline intricate designs and optimize construction methods ensures cost-effective customization while maintaining project quality and aesthetics.
Strategies for Cost Efficiency
When delving into the complexities of block retaining wall installation costs, the aspect of cost efficiency becomes paramount. Strategies geared towards maximizing cost efficiency play a pivotal role in ensuring that the project stays within budget parameters while not compromising on quality. By focusing on specific elements such as material selection, labor optimization, and efficient project management, homeowners and builders can significantly impact the overall expenditure involved in this construction endeavor. Embracing cost-efficient strategies can lead to substantial savings and a smoother, more effective project execution.
Material Selection
Exploring Budget-friendly Block Options
Exploring budget-friendly block options is a critical component when aiming for cost efficiency in block retaining wall installation. By carefully selecting affordable yet durable blocks, individuals can achieve a balance between cost-effectiveness and structural integrity. Budget-friendly blocks offer a cost-effective solution without sacrificing the quality and aesthetics of the final structure. Homeowners and contractors benefit from the affordability and ease of use of these blocks while ensuring that the overall project remains within budget constraints.
Opting for Local Suppliers
Opting for local suppliers can significantly contribute to cost efficiency in block retaining wall installation. Local suppliers often offer competitive pricing, reduced transportation costs, and faster delivery times. By sourcing materials locally, individuals can minimize expenses related to shipping and logistics, ultimately leading to cost savings. Additionally, supporting local businesses fosters community engagement and may result in personalized service and tailored solutions catering to specific project requirements.
Bulk Purchases for Discounts
Bulk purchases for discounts present a strategic approach to cutting costs in block retaining wall installation projects. By buying materials in large quantities, homeowners and contractors can leverage volume discounts and negotiate better deals with suppliers. Bulk purchases not only reduce the per-unit cost of materials but also ensure an uninterrupted supply chain, thus streamlining the construction process. While upfront costs may be higher, the long-term savings associated with bulk purchases make it a favorable choice for those seeking cost-efficient solutions.
Labor Optimization
Efficient Work Scheduling
Efficient work scheduling holds immense value in optimizing labor costs during block retaining wall installation. By developing a well-organized schedule that maximizes productivity and minimizes downtime, project timelines can be expedited, thereby reducing labor expenses. Efficient work scheduling ensures that labor resources are utilized judiciously, with tasks sequenced in a logical order to enhance efficiency and mitigate unnecessary costs. Through meticulous planning and coordination, homeowners and contractors can achieve significant cost savings without compromising on the quality of work.
Reducing Unnecessary Labor Hours
Reducing unnecessary labor hours is a key aspect of labor optimization in block retaining wall installation projects. By identifying inefficiencies and implementing streamlined processes, individuals can minimize unnecessary labor costs and enhance overall project efficiency. Strategies such as task prioritization, workflow optimization, and proactive problem-solving can help in reducing labor hours while maintaining the project timeline. Efficient utilization of labor resources plays a fundamental role in achieving cost efficiency and project success.
Negotiating Competitive Rates
Negotiating competitive rates with labor providers is an essential strategy for optimizing labor costs in block retaining wall installation. By engaging in effective negotiations and seeking multiple bids, individuals can secure competitive labor rates that align with their budgetary constraints. Negotiating competitive rates not only helps in controlling costs but also fosters better working relationships with labor providers. By ensuring fair compensation for services rendered, homeowners and contractors can build a cooperative partnership that benefits both parties involved.
Project Management
Clear Communication with Contractors
Clear communication with contractors is vital in ensuring cost efficiency and project success in block retaining wall installation endeavors. Establishing open and transparent communication channels enables all parties to stay informed, aligned, and proactive throughout the construction process. Clarity in project expectations, timelines, and deliverables facilitates smooth coordination and problem resolution, reducing the likelihood of costly errors or delays. By fostering a collaborative relationship built on effective communication, individuals can enhance project outcomes while effectively managing costs.
Regular Progress Monitoring
Regular progress monitoring plays a crucial role in overseeing costs and maintaining project efficiency in block retaining wall installation. By regularly tracking project milestones, expenses, and resource utilization, individuals can identify potential cost overruns or delays early on, allowing for timely corrective action. Progress monitoring helps in staying on course with the budget, ensuring that expenditures remain within predefined limits. Through systematic monitoring and performance evaluation, homeowners and contractors can proactively manage project costs and optimize resource utilization.
Adhering to Timelines
Adhering to timelines is a fundamental aspect of successful project management and cost efficiency in block retaining wall installation. Striving to meet established timelines and milestones helps in controlling labor costs, avoiding schedule disruptions, and mitigating budget deviations. By adhering to project timelines, individuals can minimize additional expenses associated with prolonged construction periods, subcontractor overtime, or delayed deliveries. Embracing a disciplined approach to project scheduling and execution lays the foundation for cost-effective project completion and customer satisfaction.
Conclusion
Diving deep into the final thoughts section
Final Thoughts
Understanding the Full Scope of Costs
Understanding the full scope of costs encompasses dissecting every element involved in block retaining wall installation. From material expenses to labor costs and unforeseen expenditures, a comprehensive understanding of the financial implications is paramount. By unraveling the intricacies of cost components, individuals can avoid budget overruns and streamline their project for efficiency. This section serves as a beacon of financial awareness, shedding light on the critical importance of cost estimations and prudent financial management within the realm of construction projects.
Importance of Thorough Planning
The importance of thorough planning cannot be overstated when embarking on a block retaining wall installation journey. Thorough planning sets the foundation for success, encompassing aspects such as material procurement, labor allocation, and timeline adherence. By meticulously mapping out each phase of the project, individuals can preempt potential setbacks, control costs, and ensure a seamless construction process. This section underscores the significance of foresight and strategic planning in yielding desirable outcomes and a hassle-free construction experience.
Ensuring Quality Workmanship
Ensuring quality workmanship stands as a cornerstone in the realm of construction projects, particularly when it comes to block retaining wall installation. Quality workmanship transcends mere assembly; it embodies precision, durability, and finesse in every block laid and every joint sealed. By prioritizing quality in the execution phase, individuals can guarantee the longevity and resilience of their retaining wall, elevating both aesthetic appeal and structural integrity. This section accentuates the value of investing in skilled labor and superior craftsmanship to achieve a lasting and visually appealing end result.