Materials:
- Refractory panels (quantity: 3, dimensions: 24" x 28" x 1")
- High-temperature mortar (quantity: 1 bag, weight: 50 lbs)
- Trowel (size: 12")
- Bucket for mixing mortar
DIY Steps:
- Start by removing damaged refractory panels from the fireplace.
- Clean the fireplace area thoroughly to ensure proper adhesion of new panels.
- Mix the high-temperature mortar according to manufacturer's instructions.
- Apply mortar to the replacement panel using a trowel, ensuring even coverage.
- Press the panel firmly into place and allow it to set as per mortar specifications.
- Repeat the process for all damaged panels.
Technical Aspects:
- Tools required: Trowel, bucket
- Timing specifics: Allow mortar to set for 24 hours before lighting a fire
- Critical techniques: Ensure uniform mortar application for structural integrity
DIY Project Process:
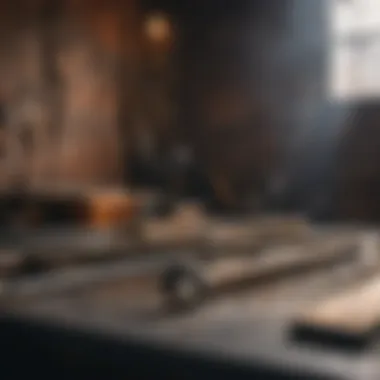
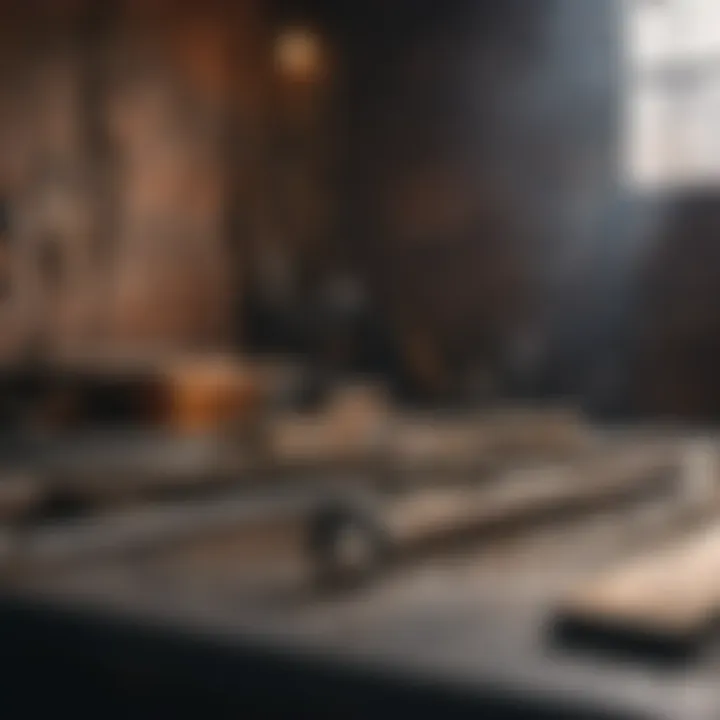
- Carefully align panels for a snug fit
- Apply mortar in a consistent thickness to prevent cracks
Troubleshooting Tips:
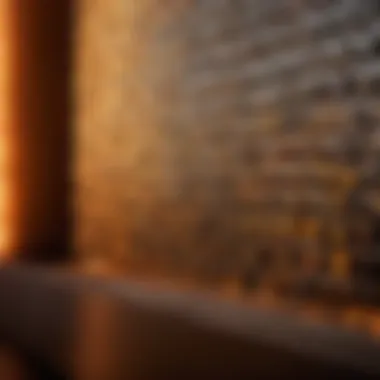
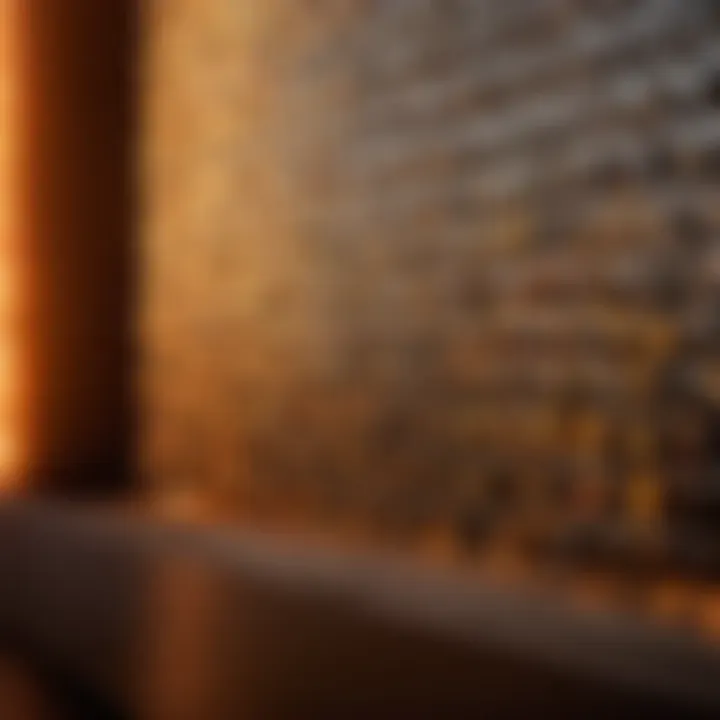
- If mortar dries too quickly, mist with water for extended work time
- In case of misalignment, gently tap panels into place using a rubber mallet
Introduction
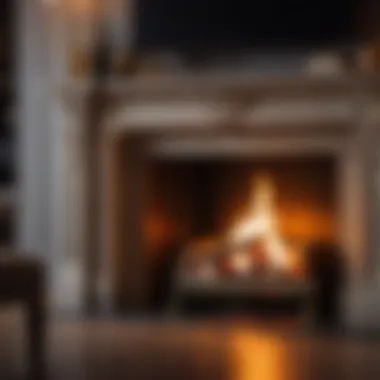
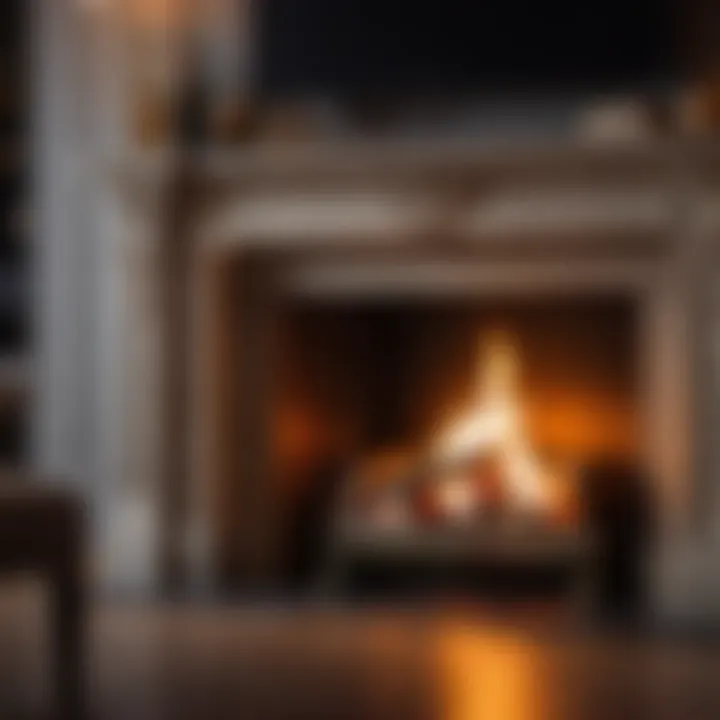
What are Refractory Panels?
Refractory panels are specialized heat-resistant panels constructed to withstand high temperatures within fireplaces. Made from materials like ceramic fibers and refractory cement, these panels line the walls of fireboxes to shield surrounding structures from excessive heat. Refractory panels are essential for ensuring the safety and longevity of fireplaces, as they prevent heat transfer to combustible materials, reducing the risk of fire hazards.
Importance of Refractory Panel Repair
The significance of refractory panel repair lies in maintaining the structural integrity and efficiency of fireplaces. Cracks, spalling, and warping are prevalent issues that can compromise the functionality and safety of these panels. Repairing refractory panels ensures optimal heat reflection and containment, preventing damage to the fireplace and surrounding areas. By prioritizing timely repairs and adhering to proper maintenance practices, homeowners can enhance the performance and lifespan of their fireplace, ultimately creating a safe and efficient heating environment for their homes.
Common Issues with Refractory Panels
In the realm of fireplace maintenance, addressing common issues with refractory panels is paramount to ensuring the longevity and functionality of these essential components. Refractory panels serve as a protective barrier between the flames and the structure of the fireplace, safeguarding against heat damage and maintaining the efficiency of heat transfer. By understanding and tackling common issues promptly, homeowners can avoid costly repairs and ensure a safe and enjoyable fireplace experience.
Cracking
One of the prevalent challenges faced with refractory panels is cracking. These cracks can develop due to various reasons, including exposure to extreme heat, age-related wear and tear, or improper installation. Cracking in refractory panels not only compromises their efficiency in containing heat but also poses safety concerns due to the potential risk of fire spreading to surrounding areas. It is essential to address cracks promptly to prevent further damage and maintain the structural integrity of the fireplace.
Spalling
Another critical issue that homeowners may encounter with refractory panels is spalling. Spalling refers to the flaking or peeling of the refractory material, typically caused by moisture penetration, frequent exposure to high temperatures, or physical impacts. Spalling can weaken the structural integrity of the panels, leading to potential hazards such as falling debris and reduced insulation properties. Addressing spalling promptly through appropriate repair techniques is vital to preserving the functionality and safety of the fireplace.
Warped Panels
Warped panels present yet another common challenge in the realm of refractory panel maintenance. Warping can occur due to prolonged exposure to intense heat or improper installation, leading to deformities in the panel's shape and compromising its ability to provide adequate heat containment. Warped panels not only detract from the aesthetic appeal of the fireplace but also hinder its overall performance. Proper assessment and repair of warped panels are essential to restore their functionality and ensure optimal heat retention in the fireplace.
Materials Needed for Refractory Panel Repair
Refractory Cement
Refractory cement is a key component essential for repairing refractory panels. This specialized cement is designed to withstand high temperatures, making it ideal for fireplace applications. When applying refractory cement, it is crucial to follow the manufacturer's instructions carefully to achieve optimal results. The cement acts as a bonding agent, ensuring the new repair seamlessly integrates with the existing panel structure, creating a durable and long-lasting solution.
When selecting refractory cement, consider factors such as temperature resistance, cure time, and application method. Opting for high-quality refractory cement will enhance the resilience of the repaired panels, prolonging their lifespan and maintaining the efficiency of the fireplace.
Wire Brush
The wire brush is an indispensable tool for preparing the damaged panels before applying refractory cement. Its abrasive bristles help remove debris, old mortar, and contaminants from the panel surface, creating a clean and rough texture for optimal bonding with the new repair material. Properly cleaning the damaged area with a wire brush ensures that the refractory cement adheres effectively, preventing detachment and enhancing the structural integrity of the repaired panels.
When selecting a wire brush, choose one with sturdy bristles that can withstand the rigorous cleaning process. Ensure that the brush is compatible with the panel material to avoid causing any damage during preparation. Investing in a high-quality wire brush will facilitate the repair process and contribute to the overall success of restoring the refractory panels.
Safety Gear
Prioritizing safety during the refractory panel repair process is paramount, making the inclusion of appropriate safety gear crucial. Safety gear such as goggles, gloves, and a dust mask protects individuals from potential hazards associated with handling refractory materials and performing repairs. Goggles shield the eyes from debris and dust, reducing the risk of injury, while gloves offer protection against abrasions and chemical exposure.
A dust mask helps prevent the inhalation of harmful particles generated during panel preparation and cement application, safeguarding respiratory health. Safety gear not only ensures the well-being of individuals conducting the repair but also promotes a secure working environment, minimizing accidents and injuries. By incorporating safety gear into the repair process, homeowners can undertake refractory panel restoration with confidence and peace of mind.
Step-by-step Refractory Panel Repair Guide
Refractory panels in fireplaces are subjected to high heat and wear over time, leading to damage that can affect both the efficiency and safety of the fireplace. This section will provide a comprehensive guide on repairing refractory panels, ensuring the longevity and optimal performance of your fireplace.
Assessment of Panel Damage
Before starting the repair process, it is crucial to assess the extent of the damage to the refractory panels. Common signs of damage include cracks, spalling, and warping. Carefully inspect the panels to determine the areas that require repair. Take note of any structural weaknesses or signs of deterioration that may impact the overall functionality of the fireplace.
Preparation of the Fireplace
Preparation is key to ensure a successful refractory panel repair. Begin by removing any debris, ash, or old refractory material from the fireplace. Clean the surface thoroughly to ensure proper adhesion of the new refractory cement. Use a wire brush to scrub off stubborn residue and create a smooth base for the repair material.
Application of Refractory Cement
The next step involves applying refractory cement to fill in cracks, cover spalling areas, and repair any damaged sections of the panels. Use a trowel to carefully apply the cement, ensuring even coverage and smooth finishing. Pay special attention to sealing any cracks or gaps that could compromise the integrity of the panels.
Curing Process
Once the refractory cement is applied, allow an adequate curing time as per the manufacturer's instructions. Proper curing is essential to ensure the strength and durability of the repair. Avoid exposing the newly repaired panels to excessive heat or moisture during the curing process to prevent any potential damage.
Tips for Maintaining Refractory Panels
Maintaining refractory panels is a vital aspect of ensuring the longevity and efficiency of your fireplace. By following these maintenance tips, you can extend the lifespan of your refractory panels and enhance the overall performance of your fireplace.
Regular Inspection:
Regular inspection of your refractory panels is crucial in identifying any potential issues early on. By conducting regular visual checks, you can spot cracks, spalling, or other forms of damage that may affect the functionality of the panels. Inspections should be done at least once every season change to catch any problems before they escalate. It is recommended to use a flashlight to get a better view of the panels' condition, especially in hard-to-reach areas.
Cleaning Guidelines:
Proper cleaning of refractory panels not only keeps them looking good but also helps maintain their effectiveness. Start by removing any debris, dust, or soot accumulation on the panels using a soft-bristled brush or vacuum cleaner. Avoid abrasive cleaning agents that can damage the panels. For tougher stains, a mixture of mild detergent and water can be used to gently scrub the surfaces. Ensure the panels are completely dry before lighting a fire to prevent any issues.
Avoiding Excessive Temperatures:
One key factor in maintaining refractory panels is to avoid subjecting them to excessive temperatures. While refractory panels are designed to withstand high heat, exposing them to extreme temperatures can cause cracking and spalling. Ensure proper airflow around the fireplace to prevent the panels from overheating. Monitor the temperature of the fireplace regularly, especially during prolonged use or intense fires. Additionally, avoid closing the damper too quickly after extinguishing a fire to allow for gradual cooling.