Intro
Concrete stands as one of the most fundamental materials in construction. Whether you’re laying a driveway or constructing a foundation, understanding the costs associated with its delivery can be a bit of a puzzle. Not only does it require foresight in budgeting, but also the ability to navigate the intricacies that come along with pricing.
As you embark on any project involving concrete, knowing what drives these costs in your area can save you from a fair bit of hassle and potentially a chunk of change. This guide will help you join the dots, leading you from the planning stage to the enjoyment of your completed project, with confidence and clarity.
Materials:
When undertaking a concrete project, it’s essential to have a clear list of materials you’ll need. Here's a breakdown of what you might consider:
-
Ready-Mix Concrete:
- Type: Standard mix
- Quantity: Typically sold by the cubic yard; determine based on your project.
-
Gravel:
- Size: 3/4 inch - this provides stability.
- Quantity: About 0.5 cubic yards for a small project like a walkway.
-
Reinforcement Bars (Rebar):
- Size: #4 or #5 (for added strength)
- Quantity: Depends on the dimensions of your pour.
-
Sub-base Material:
- Type: Crushed stone or sand
- Quantity: Approximately 2 inches deep beneath your concrete slab.
-
Plastic Sheeting:
- Thickness: 6 mil, to prevent moisture loss.
- Size: Measure according to your pour area.
-
Curing Compound:
- Type: Liquid, helps maintain moisture in curing concrete.
-
Formwork Materials:
- Type: Plywood or lumber to shape your concrete.
- Dimensions: Varies with your project size.
-
Tools:
- Concrete mixer (if not ordering ready-mix)
- Trowels, screeds, and float tools.
- Wheelbarrow or shovel for handling mixed concrete.
DIY Steps:
Now that you have your materials, let’s dive into the step-by-step process:
-
Planning:
- Begin by sketching your project to determine required measurements and materials.
-
Prepare the Area:
- Clear the site where the concrete will be installed. Remove any dirt, grass, or debris to ensure a solid base.
-
Lay the Sub-base:
- Using gravel or crushed stone, create a 2-inch layer for drainage and stability.
-
Set Up Formwork:
- Construct the formwork using plywood or lumber, ensuring it’s leveled correctly.
-
Mix the Concrete:
- If you're mixing on-site, combine the concrete mix with water in a concrete mixer following the manufacturer’s instructions. For delivered concrete, make sure you’re ready to pour when it arrives.
-
Pour the Concrete:
- Pour concrete into the forms steadily, starting at one end, and use a shovel or trowel to spread it evenly.
-
Leveling and Finishing:
- Use a screed board to level the surface, followed by a trowel or float for finishing.
-
Curing:
- Spray a curing compound over the surface or cover with plastic sheeting to retain moisture and cure properly. Allow to cure for at least a week.
Technical Aspects:
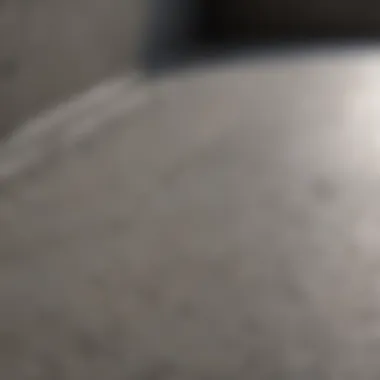
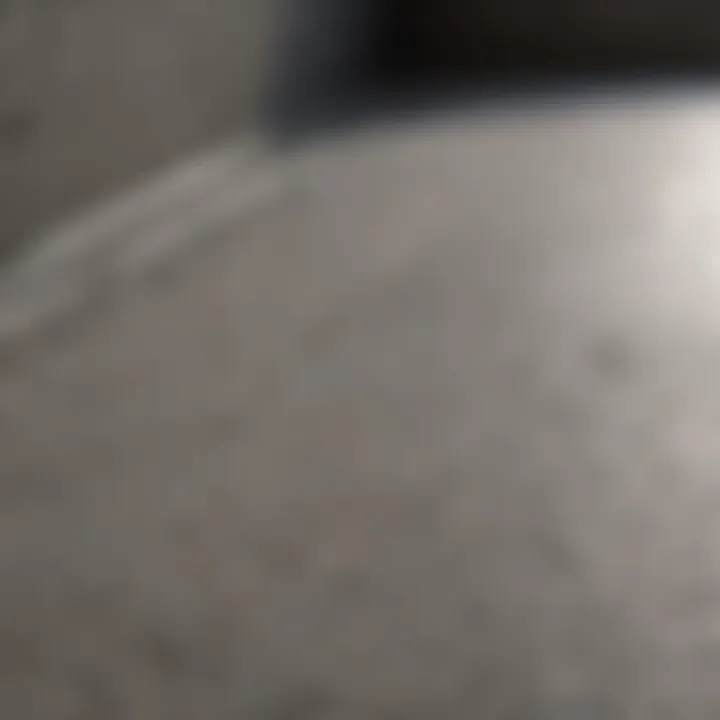
Here are some technical details to keep in mind:
-
Tools Needed:
- Concrete mixer, trowels, screws, wheelbarrow, and vibrators for settling mix if using large volumes.
-
Timing:
- Aim for a complete pour within 90 minutes of mixing. Allow adequate time for curing, which can vary depending on weather and specific materials.
-
Techniques:
- Be sure to compact the sub-base firmly before pouring, and use a bull float right after pouring for a smooth finish.
DIY Project Process:
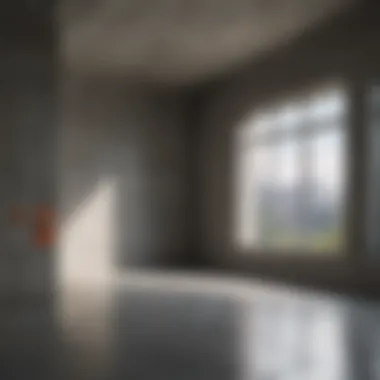
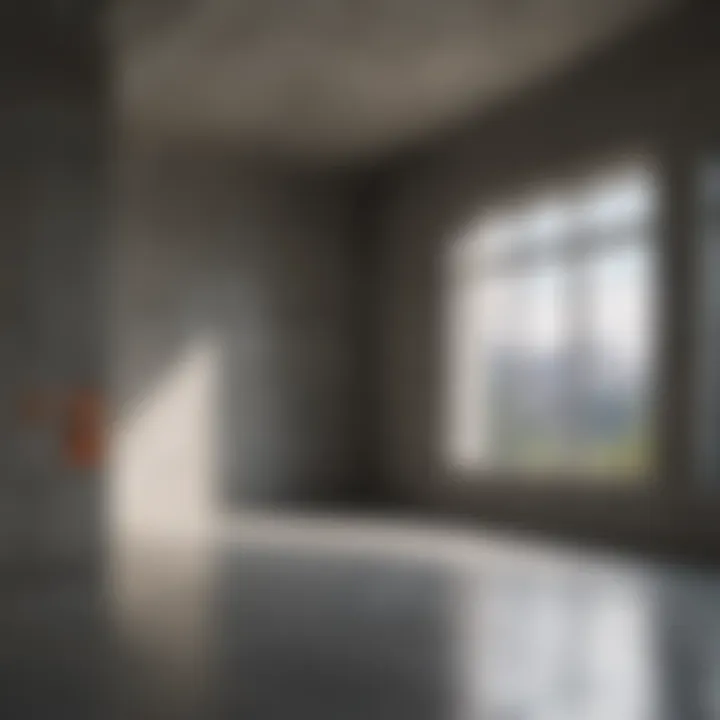
This outlines the overall project installation:
-
Pre-pour Setup:
- Secure formwork and compact the sub-base thoroughly; ensure everything is level.
-
Pouring Method:
- When it comes to pouring, start at the farthest point from the exit to avoid stepping on wet concrete.
-
Troubleshooting Tips:
- If the concrete is too dry, add a bit of water but be careful not to overdo it. If it's too wet, avoid adding more water; instead, use a trowel to create a smooth surface and let it settle.
-
Final Checks:
- Check for any air bubbles or uneven areas post-pour. If found, re-flatten using a float.
Taking into account all these elements allows homeowners and project DIYers to approach their concrete projects with a well-informed perspective. Understanding the nuances of material selection, preparation steps, and project execution can greatly impact the final result.
"A small investment in planning can save you a mountain of trouble down the line."
By arming yourself with the necessary knowledge beforehand, you’ll be on the right track to creating spaces that are not just functional but also a delight to look at.
Overview of Concrete Pricing
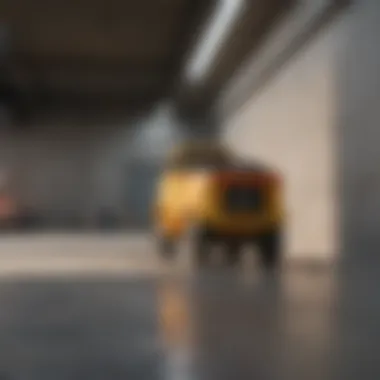
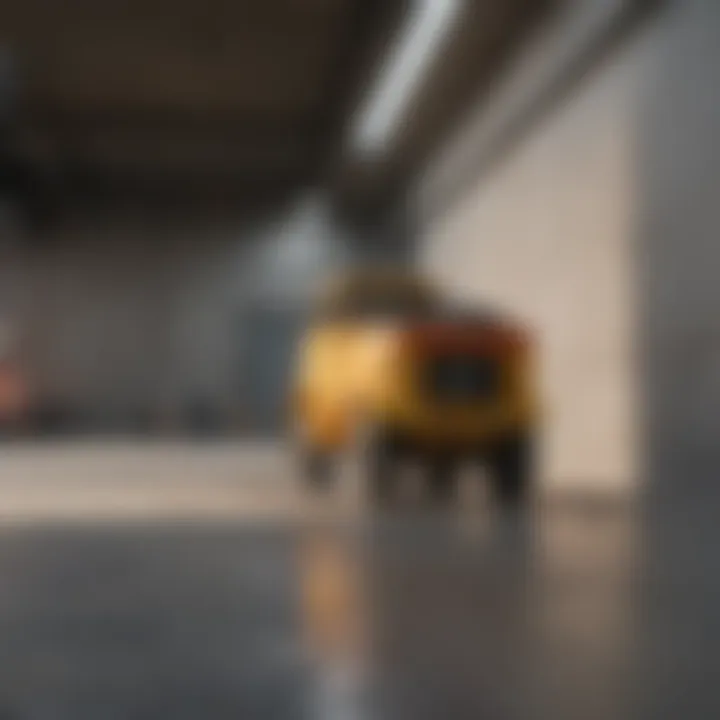
Understanding the cost of concrete delivery involves grasping various fundamental aspects related to pricing. This section provides a foundation for the entire article, emphasizing how concrete pricing serves as a crucial cog in the wheel of construction projects.
When tackling a concrete project, having a clear picture of pricing is key to budgeting accurately. It prevents the unpleasant surprise of escalating costs, helping you avoid pitfalls that might otherwise throw a wrench in your plans. Several elements feed into this dynamic; mix types, local rates, and additional charges can all affect the final price tag.
Understanding Concrete Mix Types
Basics of Concrete Mixes
An essential component of any concrete pricing discussion is understanding the basics of concrete mixes. Different mixes cater to distinct purposes, impacting not only the strength and durability but also the cost involved. For instance, a standard mix for driveways typically uses a basic blend but may include additives to enhance performance in weather conditions.
One key characteristic of this basic mix is its versatility—it can be tailored for various projects without breaking the bank, making it a popular choice among homeowners. The unique feature here is the balance between quality and affordability, streamlining the decision-making process when selecting a mix.
Common Types of Concrete Mix
Diving deeper, there are common types of concrete mixes, each with its specific advantages and drawbacks. For example, ready-mix concrete has gained traction for residential projects due to its convenience. Homeowners appreciate the ease of delivery and uniformity.
However, while ready-mix often boasts consistent quality, its main drawback can be higher costs compared to site-mixed options. This trade-off calls for careful consideration, aligning the choice of mix with the project’s requirements and budget constraints.
Factors Influencing Mix Selection
Factors influencing mix selection also loom large in the concrete equation. Here, you might think about structural requirements, environmental conditions, and intended usage. When choosing a mix, the unique feature is adaptability—whether you need high strength for a foundational slab or a decorative finish for a patio, there’s a mix designed to fit that need.
On the downside, selecting the wrong mix can lead to issues such as cracking or inadequate strength. Therefore, doing your homework on what each type offers is absolutely crucial.
Key Components of Concrete Pricing
Material Cost Breakdown
Now turning to the material cost breakdown, an essential piece of the pricing puzzle. Understanding this breakdown allows homeowners to dissect pricing into its core components—each contributing to the final cost. The primary materials—cement, aggregates, and water—neatly categorize into various cost brackets, allowing you to pinpoint where higher costs may arise.
The key characteristic here is transparency; grasping how these materials contribute to the overall price empowers you, the homeowner, to make informed choices. A unique feature lies in the possibility of sourcing materials locally, which could lead to reduced expenses—something worth investigating.
Labor Costs Associated with Delivery
Labor costs associated with delivery also play a significant role in the overall pricing structure. These costs often fluctuate based on market demand and the specific expertise required. For example, specialized labor, like that needed for decorative concrete finishing, typically incurs higher rates.
The main characteristic to highlight is that identifying reputable labor can make or break your project. Investing in skilled labor might initially seem steep, but it often saves costs in the long run, reducing issues that arise from poor installation.
Transportation Expenses
Last but not least, we need to look at transportation expenses, as they can unexpectedly lift the price tag of your concrete delivery. These costs can hinge on various factors—such as distance from the supplier, regional fuel prices, and overall logistics.
A particular aspect to consider is that some suppliers offer delivery schedules that can help cut costs and minimize fees. However, last-minute changes could rapidly escalate these expenses, so planning ahead is key to sealing a good deal.
Overall, understanding these components not only aids in demystifying the concrete pricing landscape but also sets a path toward seamless budgeting for your construction needs.
By thoroughly assessing these factors, you can ensure that your project budget remains intact while adequately preparing for potential fluctuations in costs.
Factors Affecting Concrete Delivery Costs
When it comes to understanding the cost of concrete delivery, several factors play a pivotal role that cannot be overlooked. These vary widely based on local conditions, demand levels, and market practices. Looking closely at the factors affecting concrete delivery costs helps homeowners and contractors make better decisions, achieve budget targets, and avoid unexpected fines. By grasping the elements such as geographical considerations, seasonal impacts, and volume discount opportunities, you can paint a clearer picture of what your project may entail financially.
Geographical Considerations
Urban vs. Rural Pricing Dynamics
The distinction between urban and rural areas is where the rubber meets the road in concrete pricing. For instance, concrete might be more expensive in city limits due to higher operational costs. Urban areas often face the challenge of limited space, leading to logistical headaches that can drive prices up. A construction company in a bustling metropolis is likely to incur higher transportation costs compared to a rural supplier who may have a smoother delivery flow. This difference means that when budgeting for a project, understanding your location's dynamics can lead to significant savings.
- Key Characteristic: Urban zones generally have tighter regulations and higher costs associated with operations.
- Unique Feature: While urban pricing is often higher, access to multiple suppliers can create competition, occasionally bringing prices back down.
Distance from Supplier Influence
Distance often dictates how much you’ll end up paying for concrete. The farther you are from the supplier, the more you might pay due to fuel costs and time spent in transit. If you're looking at a project that requires a large pour, that additional mileage can really add up.
- Key Characteristic: Each mile typically accounts for a certain extra cost in your final tally.
- Unique Feature: On the upside, suppliers may offer discounts for larger orders, potentially balancing the increased transport fees.
Local Market Variations
Local market dynamics must also be taken into consideration. In some areas, the competition among concrete suppliers is fierce, leading to better prices and promotions. In others, fewer suppliers may result in inflated prices, particularly if there’s a surge in demand.
- Key Characteristic: The availability of suppliers can greatly impact cost efficiency.
- Unique Feature: Monitoring local markets may reveal times when prices dip, making it an ideal moment to execute your concrete needs.
Seasonal and Climatic Effects
Impact of Weather on Concrete Production
Weather can truly make or break your concrete project. Extreme temperatures, either too hot or too cold, can influence how concrete sets and performs. If a project is delayed due to bad weather, costs can spiral out of control, as both labor and material expenses may go up.
- Key Characteristic: Weather conditions can dictate how quickly or slowly a pour can happen.
- Unique Feature: Planning around favorable weather can save both time and money, as contractors won’t face the risk of delays or the need for extra precautions.
Seasonal Demand Fluctuations
Concrete prices can sway wildly depending on seasonal demand. Spring and summer often see a boom in construction activity, causing prices to rise. Conversely, winter might lead to lower prices due to decreased demand. Knowing these variations allows you to decide when to buy your concrete.
- Key Characteristic: Spring and summer typically see hikes in demand.
- Unique Feature: During off-seasons, negotiating better rates becomes easier due to lower demand and supplier willingness to close deals.
Timing and Scheduling Factors
When you schedule your deliveries can significantly impact your costs. If you order last-minute, you may find yourself facing surcharges. It’s crucial to plan ahead to give yourself the best chances to negotiate favorable terms.
- Key Characteristic: Timely orders can help avoid penalties.
- Unique Feature: Advanced planning allows you to lock in prices during times of lower demand, helping you keep costs in check.
Volume Discounts and Offerings
Bulk Pricing Mechanisms
Ordering concrete in bulk can unlock substantial savings. Rather than paying for smaller loads repeatedly, many suppliers offer lower rates for larger orders. If you know you’ll need a lot, it’s worth exploring these bulk pricing mechanisms.
- Key Characteristic: Bulk orders reduce transportation costs per cubic yard.
- Unique Feature: It’s essential to assess if you have adequate storage space to avoid spoilage; buying too much at once can be a double-edged sword.
Negotiating Delivery Contracts
Negotiating a delivery contract can save you a pretty penny. It’s not uncommon for suppliers to be open to discussions on prices, especially if you’re committing to larger quantities. Putting in the effort to negotiate can yield rewards.
- Key Characteristic: Many contracts have wiggle room that can lead to unexpected savings.
- Unique Feature: Building rapport with suppliers may lead to better offers and priority service down the line.
Promotions and Special Offers
Many suppliers run promotional offers or time-limited discounts that savvy homeowners can take advantage of. Keeping an eye out for these opportunities can lead to considerable price reductions.
- Key Characteristic: Regular promotions can make a significant difference in your overall expenditure.
- Unique Feature: Often, signing up for a supplier’s newsletter can give you a heads-up about upcoming deals.
Remember: Knowledge is power when it comes to concrete delivery!
By understanding these factors, you can chop and change aspects of your project to help optimize costs while ensuring quality materials and reliable services.
Estimating Total Costs
When it comes to concrete delivery, nailing down the total costs is not just a minor detail; it’s a cornerstone for any successful project. Being aware of all the financial elements involved can save you a heartache—both emotionally and financially—later down the line. Accurate estimates help in budgeting wisely, ensuring you’re not caught off guard when it’s time to settle the bill.
There are several aspects to consider when estimating these costs. Knowing your concrete volume requirements, delivery charges, and any potential add-on fees is crucial. Overlooking any of these can lead to unforeseen expenses that could have been easily avoided by proper planning. Ultimately, this meticulous approach can make the difference between a smooth project execution and a financial headache.
Calculating Concrete Volume Needs
Understanding Cubic Yards
Understanding the concept of cubic yards is essential in calculating how much concrete you need. This unit is straightforward, representing a three-dimensional volume—specifically, a cube measuring one yard on each side. Why is this important? Because knowing this helps you accurately gauge the amount of concrete necessary to fill a particular area.
In practical terms, each cubic yard can typically fill about 80 square feet at a depth of four inches. This characteristic makes it an efficient, user-friendly way to estimate how much concrete to order without jumping through hoops. However, a unique challenge lies in its calculation, as factors like spillages or variations in depth may affect the final volume required.
Using Calculators for Estimation
Using calculators for estimating concrete volume is like having a cheat sheet in your back pocket. Countless online resources and apps simplify the math involved, ensuring accuracy in your calculations. Most concrete calculators require basic input like length, width, and depth to yield a quick estimate.
This method stands out for its convenience and speed. One can just enter dimensions, and voilà! A rough estimate appears. But here’s the rub: calculators generally produce estimates that may need adjusting based on site-specific variables. Depending on your specific needs and conditions, relying solely on these tools could lead to underestimating the requirements.
Common Measurement Mistakes
Common measurement mistakes can turn a well-planned project into a costly saga. Often, issues arise from measuring incorrectly, such as forgetting to convert feet to yards, or miscalculating the depth of concrete required. These little blunders can lead to insufficient amounts of concrete or wasted funds on excess material.
Key characteristics of these errors include their frequency and impact on budgeting. This makes recognizing and addressing potential pitfalls crucial for anyone involved in concrete projects. Ultimately, staying vigilant in your measuring practices can save you not only money but also time - a win-win for any homeowner or contractor.
Breaking Down Delivery Charges
Understanding Base Rates
Understanding base rates can help untangle the web of charges that come with concrete delivery. Generally, the base rate covers the cost of transporting the concrete from a batching plant to your site. This price usually factors in the distance, vehicle type, and the concrete pour size.
What’s important to note here is that these base rates are influenced by local market conditions. They can vary significantly from one area to another, so what works in one locality might not apply in another. Recognizing this helps you gauge whether you’re paying a fair price.
Add-On Fees and Surcharges
Add-on fees and surcharges are often the sneaky culprits that can inflate your concrete delivery bill. These extra costs may come from a variety of sources: late orders, special delivery times, or even the geographical location of the delivery site.
While these fees may be laid out in the fine print of a contract, understanding their presence is crucial. Such charges can significantly affect your final estimates, and if you aren't aware of them, it can feel like a punch in the gut once the final bill arrives.
Example Cost Analysis
Carrying out an example cost analysis can be an enlightening exercise when estimating your concrete delivery expenses. Let’s imagine for a moment that you're ordering fifteen cubic yards of concrete at a base rate of $130 per cubic yard. Add to that a delivery charge of $80 and then some add-on fees that take the total to an unexpected $2,000.
Such an analysis highlights how quickly costs can escalate, compelling homeowners to evaluate their choices thoroughly. By dissecting these components, one can gain insight into where the money is actually going. Not only does this provide clarity but it also lays the groundwork for more informed decisions in the future.
Comparing Concrete Delivery Services
When embarking on any construction project, the importance of comparing concrete delivery services can't be emphasized enough. Just like one wouldn’t jump into a car lease without understanding the monthly costs and maintenance fees, it’s equally vital to assess your concrete suppliers regarding their service offerings. The right decision can affect not just your budget but also the quality and timeliness of your work.
Evaluating Local Suppliers
Service Quality Indicators
Service quality indicators play a crucial role in determining which local suppliers should make the cut. These indicators often encompass how promptly a company addresses inquiries, the clarity of their communication, and the professionalism exhibited during initial contacts. A key characteristic of effective service quality is the ability to provide a detailed timeline for delivery. This attention to detail is a hallmark of companies that have honed their craft, showing they value the client's time.
A standout feature in choosing suppliers is how well they educate clients on various concrete mixes and their applications. This knowledge not only provides peace of mind but can save time in project planning. However, there can be downsides—some companies might focus too heavily on service quality without ensuring the most competitive rates, leading one to possibly overspend without even realizing it.
Reputation and Reviews Assessment
Next up is reputation and reviews assessment. In today’s digital age, where information flows like a river, it’s easier than ever to find feedback about services. Checking online platforms for reviews shines a light on a supplier’s reliability and quality. The key characteristic here is transparency; suppliers with a history of providing quality service often have many reviews to back it up.
One unique aspect of conducting a thorough reputation check is the ability to see patterns in feedback—both positive and negative. For example, if numerous reviewers mention prompt delivery but criticize the customer service, you can weigh the pros and cons. While you might find a supplier with overwhelmingly positive reviews, it's necessary to dig deeper, as they may not be the perfect fit for your needs.
Response Times and Reliability
Response times and reliability can't be overlooked when comparing concrete delivery services. In this context, response time refers to how quickly a supplier addresses inquiries and follows up on orders. A significant aspect of reliability is whether the supplier consistently meets delivery schedules. A beneficial characteristic of reliable suppliers is their ability to provide contingency plans in unpredictable situations, such as bad weather or logistical delays.
For instance, a supplier known for being responsive and having backup protocols may be more valuable than one only slightly cheaper but with a history of delays. It’s often those delays that can stack up and cause major setbacks, leading to increased project costs. So while modern amenities and tech-savvy booking systems are great, if a supplier has poor delivery history, those bells and whistles won't matter much.
Analyzing Quotes and Proposals
Moving on to analyzing quotes and proposals. This phase is where the rubber meets the road. Taking the time to compare detailed estimates from different suppliers can effectively safeguard against any unforseen expenses.
Components of a Comprehensive Quote
A comprehensive quote should cover all bases—everything from the cost per cubic yard of concrete to additional fees that may come into play. Knowing these specifics allows clients to make informed decisions. The key characteristic in this aspect is clarity. A well-structured quote leaves no room for confusion about what is included.
For instance, a supplier who clearly delineates materials, delivery charges, and labor costs is likely more trustworthy. On the flip side, vague estimates make it hard for any client to assess value, increasing the risk of surprises later down the line.
Identifying Hidden Costs
Hidden costs can be the bane of a homeowner’s project budgeting. Recognizing them requires vigilance. This entails assessing quotes for any vague terms that might hide potential charges. The notable feature of a solid cost analysis is being upfront about everything, ensuring there are no nasty surprises later.
An essential step one can take is directly asking suppliers if there are additional fees not covered in the original estimate. When they respond transparently, it can provide the reassurance you need to move forward confidently.
Assessing Value for Money
Finally, one must assess value for money. The heart of any business transaction revolves around whether what you're getting is worth what you're paying. Evaluating how a supplier’s pricing aligns with their service quality and delivery reliability can be a game-changer. The key characteristic here is balance—finding that sweet spot between cost, quality, and reliability is where the magic happens.
Another unique aspect is the opportunity of negotiating with suppliers. Often, larger jobs can lead to negotiations that swing favorably for the client, reducing final costs without sacrificing service quality. However, it’s essential not to pin your hopes too much on this; being realistic about your needs keeps you grounded.
Practical Tips for Cost Optimization
When it comes to managing expenses related to concrete delivery, every penny counts. Practical tips for cost optimization not only help homeowners and project managers keep budgets in check but also ensure that projects run smoothly from start to finish. Understanding these strategies is crucial because they directly influence the overall quality and speed of the work being done. These tips focus on strategic planning, efficient use of resources, and understanding the full delivery process to avoid unexpected costs.
Strategic Planning for Projects
Timely Ordering Practices
Timely ordering of concrete isn't just about placing an order ahead of time; it's about understanding the flow of your project. The key characteristic of this practice is its emphasis on precision and foresight. By ordering concrete when it’s needed, you can avoid rush charges and potential delays in delivery. This choice is often popular because it minimizes disruptions on-site and allows for better coordination with other trades involved in a project.
A unique feature of timely ordering is the flexibility it offers in scheduling. By ensuring you have the concrete delivered exactly when it’s needed, you can maintain a consistent workflow, keeping your team productive. However, it’s important to recognize that misjudgment in timing can lead to either surplus or shortfalls, both of which can incur costs.
Batching and Scheduling Deliveries
Batching concrete – essentially grouping orders based on project needs – is another effective optimization strategy. The key feature of batching is that it allows for a coordinated supply chain where deliveries are grouped for efficiency. This practice can significantly reduce transportation costs and ensure a timely arrival of materials. House owners find this approach beneficial as it minimizes delays caused by waiting for truck arrivals.
Another advantage of batching is that it helps manage labor effectively. When deliveries are planned well, workers can focus on the task at hand without unnecessary interruptions. However, poor planning can lead to complexities where mismatched schedules might throw off the whole system.
Avoiding Last-Minute Orders
Last-minute orders are often a recipe for disaster when it comes to cost. This is a practice that should be avoided at all costs. The key characteristic of avoiding last-minute orders is basically preventing emergency situations where all costs skyrocket. It’s a common practice when people underestimate their requirements, leading to frantic last-minute purchases that often come with hefty surcharges.
By planning well in advance, the unique benefit is the ability to secure better pricing and delivery terms with suppliers. You also reduce stress and the risk of errors that can crop up in a rush. It’s worth noting that making quick decisions under pressure can lead to cost overruns; thus, careful forethought is an invaluable quality in project management.
Maximizing Material Efficiency
Optimizing Mix Designs
Optimizing mix designs is another layer of efficiency in concrete delivery costs. It focuses on customizing the concrete to meet specific project needs while minimizing costs. The key characteristic of optimizing mix designs is tailoring the constituent materials to perform best for a given task. This can lead to savings by ensuring that you aren't over-specifying materials that are more expensive than necessary.
In this article, the benefit of optimizing mix designs is seeing a direct reflection on quality and durability of the work as well as savings on materials. A unique challenge arises when trying to strike that balance between performance and cost — overdoing the specs can quickly break the bank, while too little can compromise the structural integrity.
Reducing Waste on-site
Reducing waste on-site is about practice and planning as well. The fundamental aspect here is implementing efficient practices that ensure materials are used to their fullest extent. By keenly managing labor and time, not only is the disposal cost minimized, but the overall environmental footprint of the project can also be reduced.
A noteworthy feature of this approach is how it can foster a culture of responsibility among workers who feel accountable for the materials they use. Valuable materials can be left to spoil if not properly managed, which in turn can lead to extra costs for onsite disposal and replacements. This highlights the importance of continuous training for workers about best practices in material handling.
Recycling and Reusing Materials
Finally, the topic of recycling and reusing materials comes under the umbrella of maximizing efficiency in concrete delivery. This practice not only helps in conserving resources but can also yield significant cost benefits over time. A key characteristic of such an approach is its sustainability aspect—where materials like concrete can be crushed and repurposed for future projects.
What makes this method beneficial is the long-term savings it can provide, especially in large projects where millions of pounds of concrete are used. However, not all types of recycled concrete are suitable for all applications, and the challenge lies in distinguishing what is reusable and ensuring quality control in the recycled material. Balancing these aspects can greatly influence project cost savings while promoting environmentally friendly practices.
"Efficient planning can save significant costs in concrete delivery, keeping both the budget and schedule in check."
By considering these practical tips for cost optimization, homeowners can approach their concrete projects with a clearer strategy, ensuring they get the best value for their investment.
Closure on Concrete Delivery Pricing
When we talk about concrete delivery pricing, it’s important to grasp not just the figures involved but also the broader implications that these costs carry. Many assume that price per cubic yard is the end of the story, but it’s just scratching the surface. Understanding the overall landscape can position you better in making choices that suit your project.
Concrete delivery isn’t just a transaction but a significant part of your construction journey. Reflecting on key factors such as proximity to suppliers, the season, and your specific needs can alter your budget drastically. Knowing these details helps in getting the best value for your investment. It’s about being savvy, asking the right questions, and avoiding pitfalls that can come with this essential material.
For homeowners and housewives looking to save some bucks while not compromising on quality, the importance of planning can’t be overstressed. From the type of concrete to the amount you need, a little foresight can lead to considerable savings.
Summation of Key Takeaways
The cost of concrete delivery isn’t one-size-fits-all. Considerations include:
- Type of Concrete: Different mixes have different price points and properties.
- Location: Proximity to concrete plants can affect delivery costs.
- Timing: Seasonal demand may change pricing; ordering ahead can lead to savings.
- Market Trends: Keeping an eye on pricing trends can prepare you for future costs and help you plan financially.
Recognizing these elements arms you with the information necessary to negotiate better deals and make informed decisions, ultimately contributing to a smoother, more economical project.
Future Trends in Concrete Pricing
Looking ahead, several trends are shaking up the concrete delivery market, and being aware of them can be a game-changer for your projects.
Emerging Technologies in Concrete Production
As the world turns increasingly to innovative solutions, features like 3D printing and self-healing concrete are becoming more common. These technologies emphasize strength and efficiency, not to mention sustainability.
- Key Characteristic: Greater precision in production reduces waste.
- Unique Feature: The incorporation of recycled materials can mitigate costs and environmental impact.
This trend signals a shift towards making concrete production more resource-efficient, a boon for both contractors and homeowners.
Impacts of Sustainability on Pricing
Sustainability practices are no longer just a buzzword. It involves responsible sourcing and environmentally friendly production methods influencing pricing.
- Key Characteristic: Eco-friendly concrete options may come at a premium but lead to savings in waste management.
- Unique Feature: The demand for green materials can elevate the initial cost, but long-term benefits often outweigh these.
This focus on sustainability shifts the conversation about costs, where investing in greener options enhances not just the industry but the environment too.
Market Predictions
Future estimates suggest shifting dynamics in pricing. Being aware of these can offer insights into budgeting for your needs.
- Key Characteristic: Increasing demand coupled with supply chain considerations could elevate costs.
- Unique Feature: Volatile raw material costs, influenced by global events, could impact the bottom line.
Anticipating these changes prepares you for pricing fluctuations and helps in planning your finances effectively, whether you are a homeowner or a contractor.
Final Thought: Concrete delivery is a multifaceted topic with many layers influencing its cost. By being informed and strategic, you can navigate this landscape effectively, ensuring that your construction project proceeds smoothly and financially sound.