Materials:
- Concrete sealant: 5 gallons
- Hydraulic cement: 3 bags
- Waterproofing compound: 2 gallons
- Caulk gun: 1
- Trowel: 1
- Putty knife: 1
- Wire brush: 1
- Safety goggles: 1 pair
- Gloves: 1 pair
- Cleaning detergent: 1 gallon
DIY Steps:
- Identify Leak Source: Begin by examining the concrete surface for any visible cracks or gaps where water may be seeping through. Use the wire brush to clean the area for a better inspection.
- Prepare Surface: Clean the leaking area with detergent to remove dirt and debris. Ensure it is completely dry before proceeding with repairs.
- Apply Hydraulic Cement: Mix the hydraulic cement according to the manufacturer's instructions and apply it to the cracks using the putty knife. Smooth out the surface with a trowel.
- Use Concrete Sealant: Once the cement has dried, apply a generous amount of concrete sealant over the repaired area. Use the caulk gun for an even application.
- Apply Waterproofing Compound: For added protection, coat the repaired section with waterproofing compound to prevent future leaks.
Technical Aspects:
- Timing: Allow ample time for each layer of repair to dry as per the product instructions.
- Tools: It is essential to have the caulking gun, trowel, and putty knife for accurate application.
- Techniques: Ensure thorough mixing of materials and smooth application to create a seamless finish.
DIY Project Process:
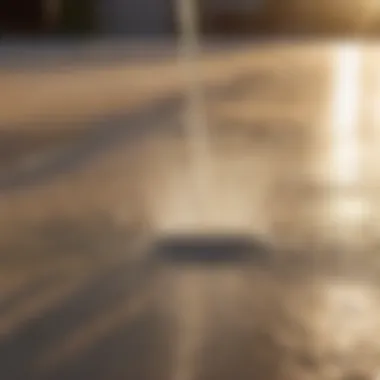
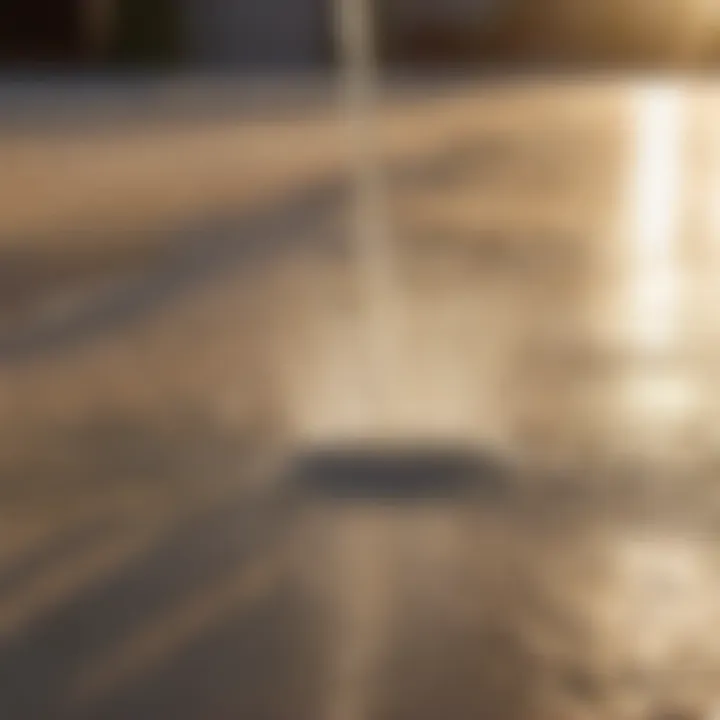
- Identification and Preparation: Thoroughly inspect and clean the leaking area to ensure a proper base for repair.
- Crack Sealing: Fill the cracks with hydraulic cement, working methodically to prevent any gaps.
- Sealant Application: Use the concrete sealant to create a durable barrier over the repaired area, sealing any remaining openings.
- Waterproofing: Finish the process by applying waterproofing compound to enhance the longevity of the repair and protect against future leaks.
Troubleshooting Tips:

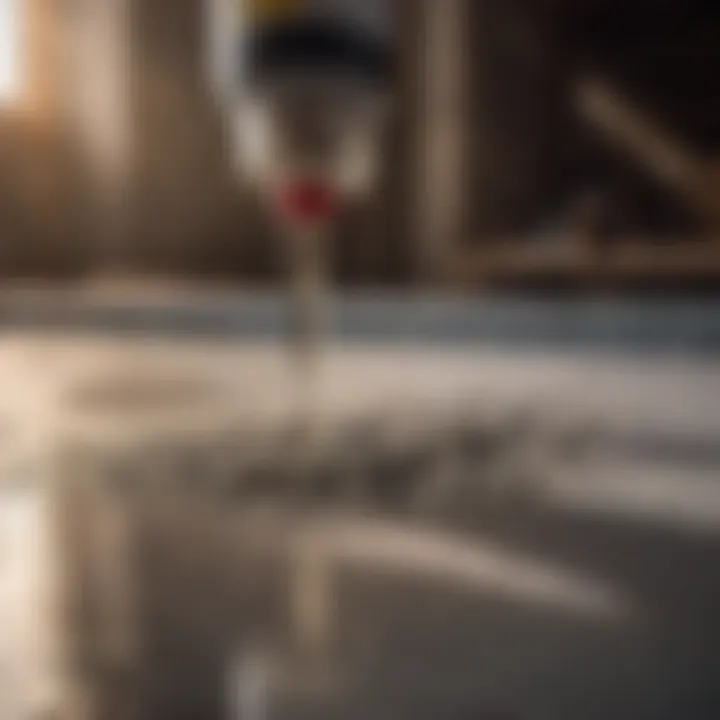
- If cracks reappear after repair, consider applying an additional layer of hydraulic cement.
- For persistent leaks, consult a professional to assess the extent of damage and recommend further solutions.
Understanding Concrete Leaks
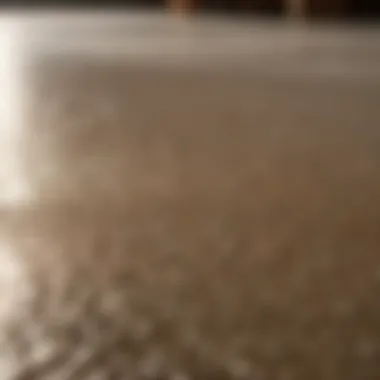
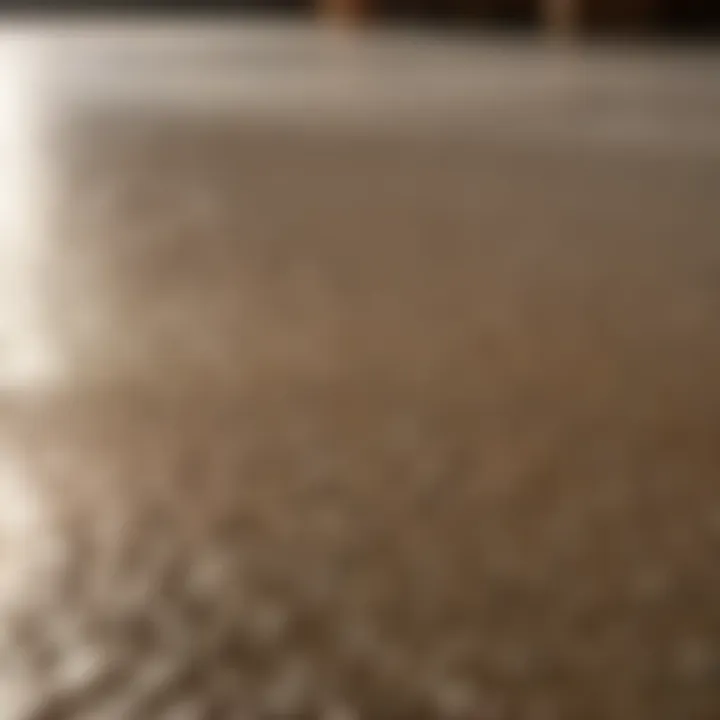
In this comprehensive article focusing on concrete leak repair, Understanding Concrete Leaks plays a pivotal role in providing insights into the root causes of leaks within concrete structures. By delving into the specific elements, benefits, and considerations surrounding Understanding Concrete Leaks, readers can gain a thorough understanding of why leaks occur and how they impact the integrity of concrete surfaces. Understanding Concrete Leaks is essential for individuals involved in concrete maintenance and repair as it sheds light on crucial preventive measures and effective repair strategies.
Causes of Concrete Leaks
Poor Construction Practices
Poor Construction Practices is a significant contributing factor to concrete leaks, primarily due to shortcuts taken during the construction phase. These practices involve subpar materials, inadequate curing methods, and lack of proper reinforcement, all of which compromise the structural integrity of concrete. The key characteristic of Poor Construction Practices lies in cutting corners to expedite the construction process, resulting in weak points vulnerable to water infiltration. While cost-effective in the short term, Poor Construction Practices prove costly in the long run as they lead to costly repairs and potential safety hazards.
Chemical Reactions
Chemical Reactions represent another common cause of concrete leaks, where interactions between concrete components or external substances trigger degradation. The key characteristic of Chemical Reactions is the gradual breakdown of concrete due to alkali-silica reaction or sulfate attack, weakening its waterproofing properties. Though unavoidable in some cases, managing the ingredients' compatibility during construction and regular monitoring can mitigate the risk of chemical-induced leaks. Understanding the unique nature of Chemical Reactions and their repercussions in concrete structures is crucial for devising effective repair solutions.
Cracking and Damage
Cracking and Damage are prominent factors contributing to concrete leaks, as they create pathways for water seepage into the concrete matrix. The key characteristic of Cracking and Damage is the compromise of the concrete's barrier against moisture intrusion, leading to potential leaks and structural deterioration. Whether caused by environmental factors, heavy loads, or inadequate surface protection, cracks and damage require immediate attention to prevent further water damage and maintain the structural integrity of the concrete. Recognizing the unique features of Cracking and Damage allows for targeted repair interventions tailored to address specific leak points.
Implications of Concrete Leaks
Structural Integrity Issues
Structural Integrity Issues resulting from concrete leaks pose a significant risk to the overall stability and safety of structures. The key characteristic of Structural Integrity Issues lies in the compromised strength and durability of concrete elements, leading to potential collapses or material deterioration. Addressing Structural Integrity Issues promptly is crucial to ensure the long-term reliability of concrete structures and prevent catastrophic failures that endanger occupants and property. While challenging to detect without proper diagnostic techniques, understanding the implications of Structural Integrity Issues is paramount in prioritizing effective repair methods and maintenance practices.
Water Damage
Water Damage resulting from concrete leaks can cause extensive harm to building materials, finishes, and internal systems. The key characteristic of Water Damage is its pervasive nature, spreading through structures via capillary action and causing gradual deterioration over time. Mitigating Water Damage requires a multi-faceted approach, including timely leak detection, efficient drainage systems, and robust waterproofing measures. Recognizing the unique features of Water Damage and its consequences empowers homeowners and maintenance personnel to proactively address leaks and protect the structural integrity of concrete surfaces.
Health Risks
Health Risks associated with concrete leaks stem from mold growth, indoor air quality issues, and the potential for respiratory illnesses. The key characteristic of Health Risks is the unseen threat posed by damp environments created by water infiltration, fostering the proliferation of harmful microorganisms. Understanding the unique features of Health Risks emphasizes the importance of prompt leak repairs, moisture control, and proper ventilation in mitigating health hazards. Safeguarding occupants' well-being and creating a healthy living environment necessitate a proactive stance against concrete leaks to minimize health risks and ensure indoor comfort and safety.
Diagnostic Techniques
In the realm of concrete leak repair, Diagnostic Techniques play a pivotal role in identifying and addressing underlying issues effectively. These techniques serve as the foundation for developing targeted repair solutions. By delving deep into the diagnostics, individuals can gain a comprehensive understanding of concrete structures' health and integrity. Notably, Diagnostic Techniques encompass a range of tools and methods that aid in the accurate assessment of leaks, ensuring precise and efficient repairs.
Visual Inspection
Surface Checks
Surface Checks are a fundamental aspect of Visual Inspections that involve examining the exterior of concrete surfaces for visible signs of damage or moisture penetration. These checks provide crucial insights into the condition of concrete, such as cracks, spalling, or discoloration, indicating potential areas of water ingress. Their non-invasive nature makes them a popular choice for initial assessments, offering a quick overview of the surface condition. However, Surface Checks may have limitations in detecting hidden or internal leaks, emphasizing the need for complementary diagnostic measures.
Staining Patterns
Staining Patterns analysis aids in detecting water-related issues by identifying discoloration caused by moisture seepage. This method relies on observing unique patterns or marks on concrete surfaces, indicating areas of potential leaks or humidity. By recognizing these distinct marks, individuals can pinpoint leak sources more accurately, guiding subsequent repair actions. While Staining Patterns offer valuable insights, they may not always reveal the full extent of underlying damage, necessitating further diagnostic investigation.
Moisture Testing
Electrical Methods
Electrical Methods for Moisture Testing involve the use of specialized equipment to measure electrical conductivity in concrete, helping assess moisture content and identify potential leak sources. This approach offers a quantitative analysis of water presence within structures, enabling professionals to pinpoint specific areas for targeted repairs efficiently. The key advantage of Electrical Methods lies in their precision and ability to detect moisture levels deep within concrete, aiding in comprehensive leak evaluations.
Non-Destructive Techniques
Non-Destructive Techniques provide a non-invasive means of assessing moisture intrusion without causing damage to concrete structures. These methods include technologies such as infrared thermography or capacitance meters, allowing for thorough moisture evaluations without disrupting the surface integrity. By utilizing Non-Destructive Techniques, individuals can obtain accurate readings of moisture content across varying concrete depths, ensuring holistic leak assessments while preserving structural integrity.
Invasive Investigations
Core Samples
Core Samples involve extracting cylindrical specimens from concrete structures to analyze moisture levels and assess material properties. This invasive method offers detailed insights into the composition and condition of concrete, facilitating targeted repairs based on comprehensive data. By examining core samples, professionals can identify the extent of water intrusion, enabling precise solutions to mitigate leaks effectively. While Core Samples provide thorough diagnostic results, the procedure may require careful planning and restoration post-sampling.
Thermal Imaging
Thermal Imaging utilizes infrared technology to detect temperature differentials on concrete surfaces, indicating potential areas of moisture accumulation. This non-contact method offers a quick and efficient means of identifying leaks by visualizing heat patterns associated with water ingress. The unique advantage of Thermal Imaging lies in its ability to detect hidden moisture issues not visible to the naked eye, enhancing leak detection accuracy and guiding focused repair efforts.
Repair Methods
Repair methods are a crucial aspect of concrete leak repair, playing a significant role in addressing and fixing leaks effectively. When it comes to repairing concrete structures, choosing the right method is essential for ensuring long-lasting solutions and preventing future issues. In this article, we will delve deep into the various repair methods available, discussing their specific elements, benefits, and considerations to help you make informed decisions for your concrete repair needs.
Surface Repairs
Surface repairs are an integral part of concrete leak repair, focusing on addressing leaks that occur on the exterior of structures. Two commonly used surface repair techniques include:
Epoxy Injection
Epoxy injection is a specialized process that involves injecting epoxy resin into cracks and voids within concrete structures. This method is highly effective in sealing off leaks and preventing water intrusion. The key characteristic of epoxy injection is its ability to bond seamlessly with concrete surfaces, creating a durable and watertight seal. One of the main advantages of epoxy injection is its quick curing time, which allows for expedited repairs. However, one potential disadvantage is that it may not be suitable for all types of concrete structures depending on the extent of damage.
Polymer Modified Mortar
Polymer modified mortar is another surface repair technique that involves using mortar mixed with polymers to enhance adhesion and flexibility. This method is popular for its high strength and durability, providing long-lasting protection against leaks. The key characteristic of polymer modified mortar is its excellent bonding properties, ensuring robust and waterproof repairs. One of the unique features of this method is its ability to withstand environmental factors and mechanical stress. While polymer modified mortar offers exceptional protection, it may have limitations in certain applications where higher levels of flexibility are required.
Internal Repairs
Internal repairs are essential for addressing leaks within the core of concrete structures, ensuring comprehensive sealing and reinforcement. Two commonly utilized internal repair methods are:
Crack Injection
Crack injection is a specialized technique used to fill and seal cracks within concrete, preventing water infiltration and reinforcing the structure. The key characteristic of crack injection is its ability to penetrate deep into cracks, effectively sealing off leaks and strengthening the affected areas. This method is beneficial for its precise application and ability to address small cracks efficiently. However, one potential drawback is that it may be less effective for larger or more extensive cracks.
Cementitious Grouts
Cementitious grouts are versatile materials used for sealing leaks, voids, and cracks in concrete structures. The key characteristic of cementitious grouts is their flexibility and adaptability, allowing them to conform to various shapes and sizes. This method is popular for its ease of application and cost-effectiveness, providing effective solutions for a wide range of repair needs. One unique feature of cementitious grouts is their ability to cure quickly, minimizing downtime during repairs. While cementitious grouts offer excellent sealing properties, they may require proper maintenance to ensure long-term durability and performance.
These repair methods play a vital role in addressing concrete leaks effectively, providing tailored solutions to meet specific repair requirements and safeguarding the integrity of concrete structures. By understanding the nuances of each technique and their associated benefits and considerations, individuals can make informed decisions when tackling concrete leak repair projects.
Preventive Measures
Preventive measures in concrete leak repair play a crucial role in ensuring the longevity and durability of concrete structures. By proactively addressing potential sources of leaks, individuals can mitigate future damage, reduce repair costs, and maintain the structural integrity of their property. Incorporating preventive measures into concrete maintenance schedules is key to avoiding larger issues down the road. Regular inspections and timely repairs are fundamental aspects of preventive maintenance that can help detect and address vulnerabilities before they escalate. By adopting a proactive approach to maintenance, homeowners and property managers can safeguard their investments and enhance the overall lifespan of their concrete structures.
Waterproofing
Surface Coatings
Surface coatings are a pivotal component of concrete waterproofing, providing a protective layer that shields the concrete from water infiltration. These coatings act as a barrier against moisture, preventing leaks and minimizing the risk of water damage. The key characteristic of surface coatings lies in their ability to form a seamless, impermeable layer over the concrete surface, ensuring long-lasting protection. A notable advantage of surface coatings is their versatility, as they can be applied to various types of concrete surfaces, including walls, floors, and roofs. However, it's essential to consider the substrate's condition and the specific environmental factors when selecting the appropriate coating system. While surface coatings offer effective waterproofing solutions, proper surface preparation and application are critical to achieve optimal results.
Membrane Systems
Membrane systems also play a vital role in concrete waterproofing, offering a durable and reliable barrier against water intrusion. The key characteristic of membrane systems is their ability to provide seamless protection over large surface areas, effectively sealing off potential leak paths. One of the primary advantages of membrane systems is their flexibility, allowing for easy adaptation to different concrete configurations and shapes. Additionally, membrane systems are known for their excellent chemical resistance and UV stability, ensuring long-term performance in various environmental conditions. However, proper installation and maintenance are essential to maximize the effectiveness of membrane systems and prolong their service life.
Maintenance Practices
Regular Inspections
Regular inspections are essential preventive measures that help identify early signs of concrete damage or potential leak points. By conducting routine visual assessments and utilizing specialized tools, homeowners can detect anomalies such as cracks, spalling, or discoloration that may indicate water seepage. The key characteristic of regular inspections is their proactive nature, enabling homeowners to address minor issues promptly before they escalate into more significant problems. Incorporating regular inspections into a maintenance routine facilitates early intervention and timely repairs, preserving the structural integrity of concrete elements. However, thorough training and proper equipment are essential for accurate inspections and precise defect identification, ensuring comprehensive maintenance practices.
Timely Repairs
Timely repairs are crucial components of effective concrete maintenance, preventing minor issues from developing into extensive damage or structural failure. The key characteristic of timely repairs lies in their swift response to identified defects or leaks, minimizing the impact on the overall structure and reducing repair costs. Addressing issues promptly can prevent water infiltration, corrosion of reinforcing steel, and deterioration of concrete surfaces, preserving the aesthetics and functionality of the structure. Furthermore, timely repairs contribute to prolonged asset lifespan and ensure the safety and stability of the concrete elements. While prompt intervention is vital for successful repairs, attention to detail and quality workmanship are paramount to achieving lasting results and maintaining the structural integrity of the concrete.