Materials:
-
Concrete mix: 50 lbs bag x 10, ensuring a sturdy foundation for the garage floor.
-
Aggregate: 1 ton to enhance durability and strength of the concrete mixture.
-
Reinforcement mesh: 6 rolls of 7.5ft x 15ft for added support and resistance to cracking.
-
Wood forms: 12 pieces of 2x4 lumber at 12ft length each to create shape and boundaries.
-
Plastic sheeting: 2 rolls of 10ft x 25ft to prevent moisture from seeping into the concrete.
-
Concrete sealer: 5 gallons to protect the surface and extend longevity.
DIY Steps:
-
Prepare the Area: Clear out the garage and ensure a clean, level surface for optimal results.
-
Mix Concrete: Combine concrete mix, aggregate, and water in a wheelbarrow based on recommended ratios until a uniform consistency is achieved.
-
Pour Concrete: Fill the prepared area with the concrete mixture and use a screed board to level the surface evenly.
-
Install Reinforcement: Place the reinforcement mesh within the concrete to provide structural integrity.
-
Create Forms: Construct wood forms around the perimeter to contain the concrete during pouring and drying.
-
Smooth Surface: Utilize a bull float and trowel to smooth out any imperfections on the concrete surface.
Technical Aspects:
-
Required Tools: Wheelbarrow, shovel, screed board, bull float, trowel, level.
-
Timing Specifics: Allow 24-48 hours for the concrete to cure before walking on it, and 7 days for full curing.
-
Critical Techniques: Vibrating the concrete during pouring to remove air bubbles and ensure a solid finish.
DIY Project Process:
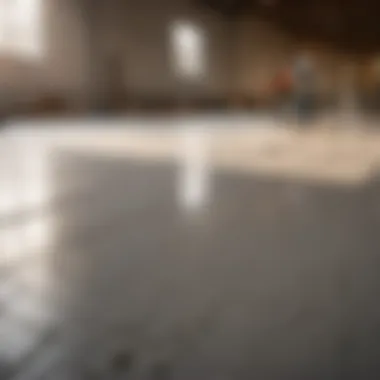
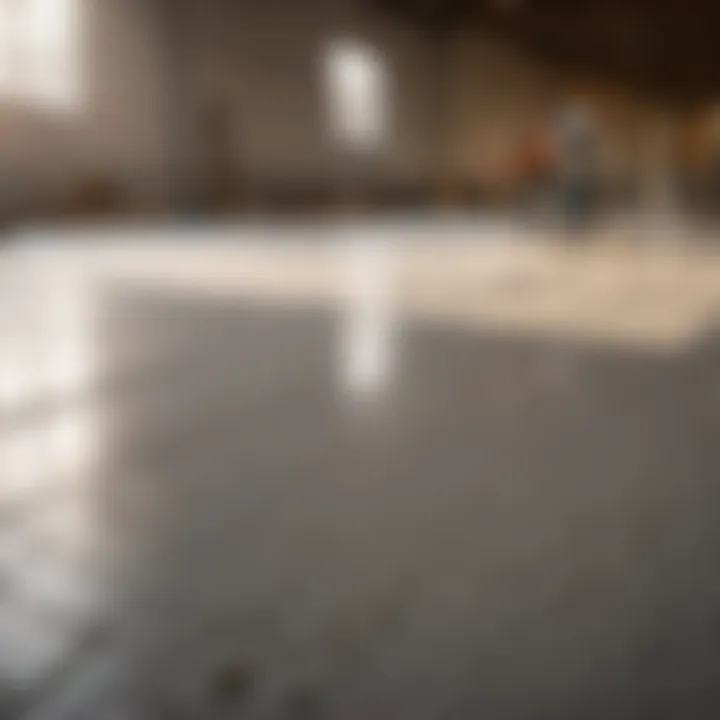
-
Sequential Steps: Follow a specific order in mixing, pouring, reinforcing, and finishing to achieve a professional result.
-
Troubleshooting Tips: In case of cracks, patch with a concrete filler and reapply sealer for a seamless look and added protection.
Introduction
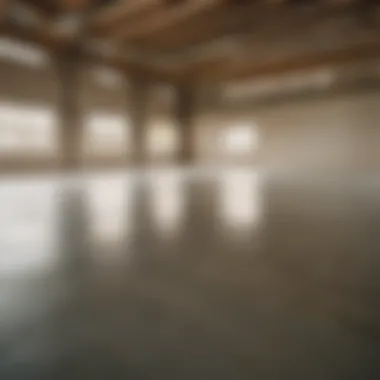
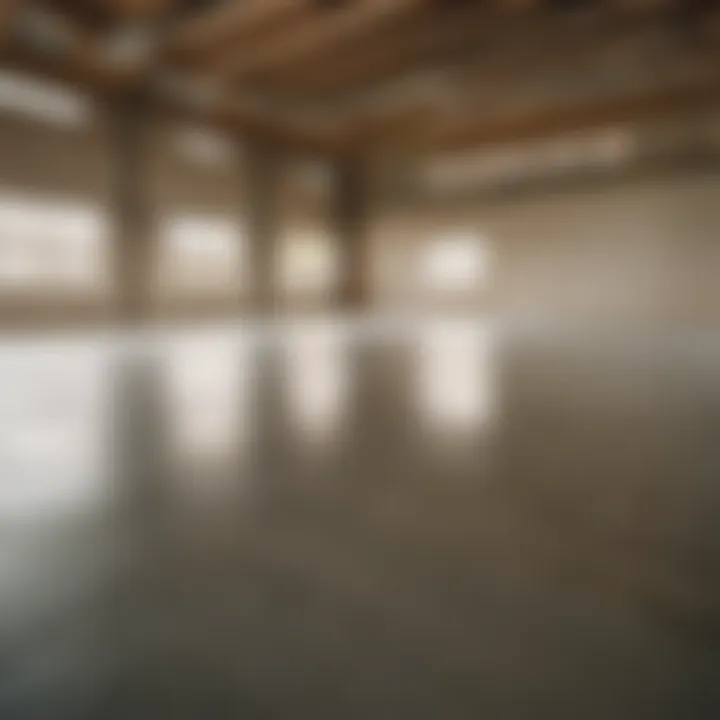
Concrete garage flooring is a crucial element in any garage construction project, offering durability, functionality, and aesthetic appeal. Understanding the costs associated with installing a concrete floor is vital for homeowners and housewives alike. This article delves into the intricate details of cost analysis for concrete garage flooring, outlining the different factors that influence overall expenses. From material costs to labor expenses and long-term maintenance considerations, a comprehensive overview is provided to aid readers in budgeting effectively.
Overview of Concrete Garage Flooring:
When it comes to garage flooring, concrete stands out as a popular choice due to its strength, versatility, and longevity. Concrete floors can withstand heavy loads, resist wear and tear, and are relatively easy to maintain. Whether for residential garages or commercial spaces, concrete flooring offers a stable and lasting foundation for various activities. Understanding the nuances of concrete garage flooring is essential for making informed decisions about installation, maintenance, and repair.
Purpose of the Cost Analysis:
The primary objective of conducting a cost analysis for concrete garage flooring is to provide clarity on the financial aspects associated with such projects. By dissecting the expenses involved in material procurement, labor fees, permits, and maintenance, homeowners can gain a comprehensive understanding of the monetary commitments required. The cost analysis serves as a guide for effective budget planning, ensuring that individuals can make informed decisions and avoid financial surprises during the project.
Significance of Understanding Costs:
Grasping the intricacies of concrete garage flooring costs is paramount for prudent financial management. By comprehending the breakdown of material expenditures, labor costs, and long-term maintenance expenses, homeowners can create realistic budgets and prevent overspending. Understanding the significance of costs also enables individuals to prioritize investments based on their preferences and needs, whether focusing on enhancing aesthetics, maximizing durability, or minimizing ongoing maintenance requirements.
Material Costs
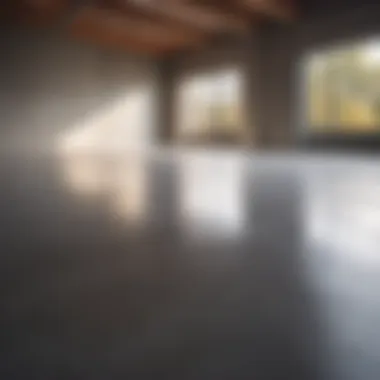
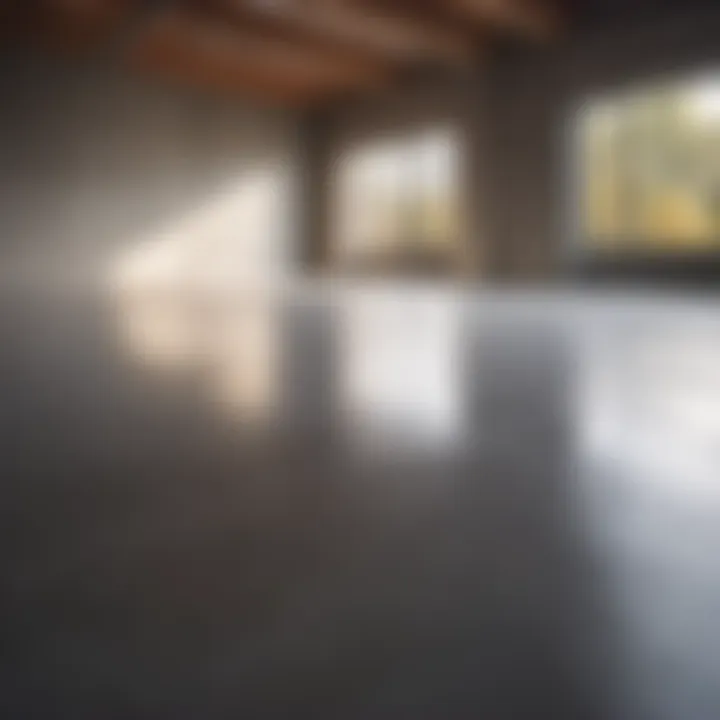
In the realm of concrete garage flooring installations, understanding the intricacies of material costs is paramount. Material costs represent a significant portion of the overall expenditure when considering a project of this nature. Whether you opt for basic concrete or specialized mixes, the materials you choose can influence the quality, durability, and aesthetic appeal of your garage floor.
When delving into the specifics of material costs, it's crucial to analyze various elements such as the types of concrete materials, reinforcement materials, surface finishes, and any additional expenses that might arise throughout the installation process. By grasping the nuances of material costs, homeowners can make informed decisions that align with their budget constraints and desired outcome for their garage flooring.
Types of Concrete Materials
Different grades of concrete
Different grades of concrete play a pivotal role in determining the strength and durability of your garage floor. Each grade offers distinct characteristics that cater to specific project requirements. For instance, higher-grade concrete, such as M30 or M40, provides enhanced durability and is ideal for heavy-duty applications. On the other hand, lower-grade concrete, like M10 or M15, may suffice for less demanding projects.
Choosing the appropriate grade of concrete depends on factors such as the garage's intended use, load-bearing capacity, and environmental conditions. Homeowners seeking long-term durability and structural resilience often opt for higher-grade concrete to ensure the longevity of their garage flooring.
Specialty concrete mixes
Specialty concrete mixes introduce a level of customization and refinement to concrete flooring projects. These specialized blends are formulated to enhance specific characteristics such as strength, moisture resistance, and aesthetic appeal. Popular options include fiber-reinforced concrete, self-leveling mixes, and decorative overlays.
Incorporating specialty concrete mixes can elevate the overall quality and visual impact of your garage floor. Whether you prioritize strength and longevity or seek to create a visually stunning surface, these specialized blends offer tailored solutions to meet your unique preferences.
Additional Material Expenses
Reinforcement materials
Reinforcement materials, such as steel rebars or mesh, bolster the structural integrity of concrete garage flooring. These materials prevent cracking, improve load distribution, and enhance overall stability. While adding to the initial cost, investment in reinforcement materials pays off by extending the lifespan of the garage floor and reducing maintenance needs.
Choosing the right reinforcement materials involves evaluating factors like the garage's size, expected traffic load, and long-term usage. By incorporating quality reinforcement components, homeowners can fortify their garage floor against wear and tear, ensuring a robust and long-lasting concrete surface.
Surface finishes
Surface finishes dictate the final look and feel of your concrete garage floor. From polished finishes to textured coatings, there is a myriad of options to customize your flooring's appearance. Surface finishes not only enhance aesthetics but also contribute to durability, stain resistance, and ease of maintenance.
Selecting the appropriate surface finish involves considering factors such as desired aesthetics, functionality, and budget constraints. Whether you prefer a glossy sheen or a slip-resistant texture, finding the right surface finish can transform your garage floor into a polished and practical space.
Labor Costs
Labor costs play a crucial role when considering the overall expenditure for installing concrete garage flooring. The expense associated with labor can significantly impact the project's budget and its successful completion. Understanding the nuances of labor costs is essential in planning and executing a cost-effective flooring solution.
Professional Installation vs. DIY
In determining labor costs for concrete garage flooring, one must weigh the options between hiring professionals for installation or opting for a do-it-yourself (DIY) approach. Professional installation offers the expertise and efficiency of trained professionals, ensuring high-quality workmanship and timely completion. On the other hand, undertaking DIY work can lead to cost savings but may require more time, effort, and knowledge on the part of the homeowner. Considering factors such as skill level, available time, and desired outcome is crucial in deciding between professional installation and a DIY project.
Factors Affecting Labor Costs
Complexity of the project
The complexity of the garage flooring project significantly influences labor costs. Projects that involve intricate designs, customized finishes, or structural modifications often require more time and expertise from professionals, inevitably increasing labor expenses. However, the investment in a complex project can result in a unique and aesthetically pleasing garage floor, enhancing the overall value of the property. Homeowners should carefully assess the level of complexity they desire against the associated labor costs to ensure a balanced decision that aligns with their budget and aesthetic preferences.
Local labor rates
Local labor rates directly impact the overall cost of installing concrete garage flooring. Variations in labor rates across different regions can affect budget considerations, as higher rates may inflate total project expenses. Understanding and researching local labor rates can help homeowners accurately estimate labor costs, plan their budget effectively, and potentially negotiate for more competitive pricing. Balancing quality workmanship with affordable labor rates is key in achieving a cost-effective and satisfactory outcome for garage flooring projects.
Additional Considerations
Permit Costs
Permit costs are a pivotal aspect of installing concrete garage flooring, as they are often mandatory for construction projects. These costs cover the fees required to obtain necessary permits from local authorities to commence the flooring installation. Factors such as the size of the project and specific regulations in the area can influence permit costs. It is essential for homeowners to factor in permit costs when budgeting for their garage flooring project to avoid unexpected expenses and ensure compliance with local building codes.
Maintenance Expenses
Maintenance expenses are an essential consideration for concrete garage flooring to prolong its lifespan and preserve its appearance. Sealing and resealing costs are a key component of maintenance, as they help protect the concrete surface from damage caused by moisture, oil, and chemical spills. By investing in regular sealing and resealing, homeowners can prevent cracks, stains, and deterioration, ultimately extending the longevity of their garage flooring.
Sealing and Resealing Costs
Sealing and resealing costs involve applying a protective sealant to the concrete surface to enhance its durability and resistance to wear and tear. This process creates a barrier that shields the flooring from moisture penetration and contaminants, reducing the risk of cracking and maintaining its aesthetic appeal. Homeowners can choose from various sealant options based on their specific needs, with options ranging from acrylic sealers to penetrating sealers.
Sealing and resealing costs are essential expenses that contribute to the overall maintenance budget for concrete garage flooring. While these costs may vary depending on the type of sealant used and the size of the area, they offer substantial benefits in terms of preserving the flooring's condition and increasing its longevity. By prioritizing regular sealing and resealing, homeowners can safeguard their investment and enjoy a durable, attractive garage floor for years to come.
Long-term Durability Benefits
One of the significant advantages of concrete garage flooring is its long-term durability, making it a practical choice for homeowners seeking a resilient and low-maintenance flooring solution. The robust nature of concrete makes it resistant to wear and tear from vehicles, foot traffic, and heavy equipment, ensuring that the garage floor remains intact for a prolonged period.
Additionally, the inherent strength of concrete minimizes the need for frequent repairs and replacements, saving homeowners time and money in the long run. By investing in concrete garage flooring, individuals can enjoy peace of mind knowing that their flooring can withstand the rigors of daily use without deteriorating quickly. The long-term durability benefits of concrete flooring make it a smart investment for homeowners looking for a reliable and enduring flooring option.
Conclusion
In the realm of concrete garage flooring projects, the conclusion serves as the cornerstone that encapsulates the essence of the entire cost analysis process. It is the culmination of meticulously reviewing all the elements that contribute to the financial considerations involved in installing a concrete floor in a garage. The conclusion acts as a compass, guiding individuals towards informed decision-making and effective budgeting strategies for their garage flooring projects.
Within this article, the conclusion section plays a pivotal role in distilling the insights garnered from exploring material costs, labor expenses, and additional considerations. By summarizing the complex web of cost factors, it offers clarity and direction to individuals embarking on concrete flooring ventures. It sheds light on the nuances of budget allocation and the importance of foresight in anticipating expenses to ensure a seamless project execution.
Moreover, the conclusion delves into the long-term implications of budgeting for concrete garage flooring. It emphasizes the significance of not only considering initial installation costs but also factoring in maintenance expenses and long-term durability benefits. This holistic approach empowers individuals to make well-informed decisions that align with their financial capabilities and future maintenance requirements.
In essence, the conclusion section serves as the lynchpin that ties together the intricacies of cost analysis, providing a roadmap for individuals to navigate the financial landscape of concrete garage flooring projects with prudence and foresight.