Materials:
- Concrete: 500 sq. ft. at 4 inches thickness
- Lumber: 20 pieces of 2x4s and 10 sheets of plywood
- Nails: 5 pounds of various sizes
- Garage door: 2 single-car garage doors
- Roofing materials: Shingles or metal sheets
- Windows: 2 standard sized windows
DIY Steps:
- Site Preparation: Clear the area, level the ground, and mark the layout for the garage foundation.
- Foundation: Dig footings, pour concrete, and let it cure before building on top.
- Frame Construction: Build the walls, roof trusses, and attach them securely.
- Roofing: Install roofing materials ensuring proper insulation and ventilation.
- Siding: Put up exterior siding for protection and aesthetics.
- Doors and Windows: Install garage doors and windows securely.
- Finishing Touches: Add trim, paint, and any additional features for a polished look.
Technical Aspects:
- Tools Required: Hammer, nails, saw, drill, level, tape measure, and ladder.
- Timing Specifics: Foundation takes 1-2 weeks, framing 2-3 weeks, roofing/siding 1 week each.
- Critical Techniques: Ensure proper support for load-bearing walls, waterproofing foundation, and sealing joints for energy efficiency.
DIY Project Process:
- Foundation: Excavate, set forms, pour concrete, and reinforce accordingly.
- Framing: Erect walls, install trusses, and ensure structural integrity.
- Roofing/Siding: Water barrier under roofing, proper overlap for siding, and seal edges.
- Windows/Doors: Securely install with proper weather-stripping and insulation.
- Finishing: Apply trim, paint, and any additional features as desired.
Troubleshooting Tips:
- If walls are not level, double-check foundational elements before proceeding.
- Leaks can often be traced to improper sealant application around windows and doors.
- Insufficient ventilation can lead to moisture buildup - ensure adequate airflow.
Keep these details in mind for a successful and well-executed garage construction project!
Introduction
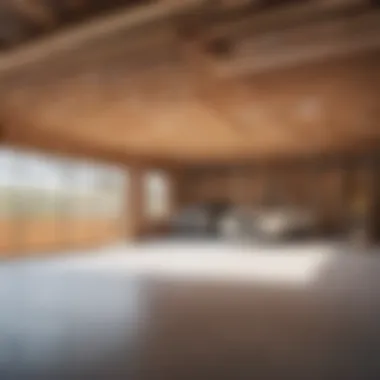

In the realm of home improvement projects, constructing a 2.5 car garage stands out as a significant endeavor requiring meticulous planning and financial consideration. This article delves into the essential components of the cost breakdown associated with building a 2.5 car garage, offering invaluable insights for housewives and homeowners contemplating such a project. From selecting optimal materials to abiding by local regulations, every detail plays a crucial role in determining the overall expenses involved in this construction venture.
To embark on the journey of understanding the intricacies of building a 2.5 car garage, individuals must grasp the fundamental factors that influence the financial outlay. This article meticulously dissects each element, ensuring a comprehensive guide for readers interested in the nitty-gritty of garage construction costs. With a focus on practicality and precision, this exploration aims to empower readers with the knowledge necessary to make informed decisions and embark on their garage construction endeavors with confidence and clarity.
Factors Affecting Cost
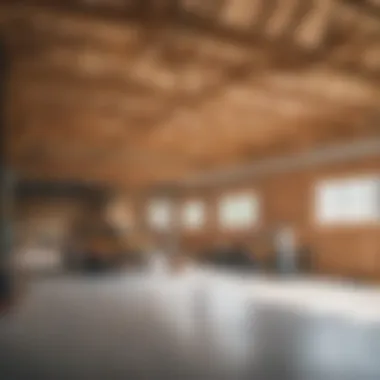

Constructing a 2.5 car garage involves various factors that significantly influence the overall cost. It is crucial to understand these factors to make informed decisions throughout the project. Each element plays a vital role in determining the financial implications and ensuring a successful outcome. By comprehensively exploring the size of the garage, materials used, location, labor costs, and permits and regulations, individuals can strategically plan and budget for their garage construction project.
Size of the Garage
The size of the garage is a fundamental factor that directly impacts the total cost of construction. A larger garage will require more materials and labor, leading to increased expenses. Considerations such as the number of vehicles the garage needs to accommodate, additional storage space, and future needs should guide the decision-making process. Optimizing the size to fit your requirements while managing costs efficiently is essential for a cost-effective garage construction project.
Materials Used
The selection of materials for the garage construction contributes significantly to the overall cost. High-quality materials may incur a higher initial expenditure but can result in long-term durability and reduced maintenance costs. Factors such as the type of foundation materials, frame materials, roofing materials, and siding materials should be carefully considered to strike a balance between quality and budget. Exploring different material options and assessing their cost-effectiveness is essential in planning a financially sustainable garage construction project.
Location
The geographical location of the construction site can impact construction costs due to varying labor rates, material availability, and building regulations. Urban areas may have higher labor costs and stricter zoning regulations, influencing the overall budget for the project. Evaluating the location-specific factors and adapting the construction plan accordingly can help optimize costs and streamline the building process.
Labor Costs
Labor costs constitute a significant portion of the overall expenses in garage construction. The complexity of the project, local labor rates, and the expertise of the hired professionals can all affect labor costs. Allocating budget for contractor fees and additional labor costs is essential for a smooth construction process. Prioritizing skilled labor and efficient workflow can help manage labor expenses effectively.
Permits and Regulations
Obtaining the necessary permits and complying with building regulations are essential steps in garage construction. Permit costs and regulatory requirements vary by location and project scope. Understanding the permit process, zoning regulations, and associated expenses is crucial for avoiding delays and additional costs during construction. Adhering to legal requirements and ensuring compliance with regulations are integral to a successful garage construction project.
Material Costs
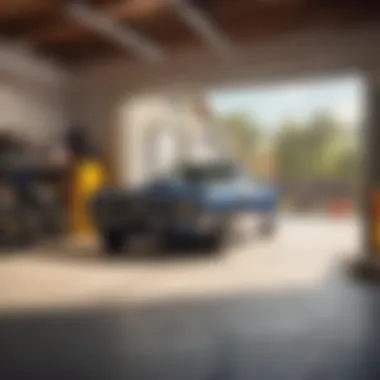

In the realm of constructing a 2.5 car garage, one of the most pivotal aspects to consider is the breakdown of material costs. The significance of delving into material costs within this article lies in its ability to provide a comprehensive understanding of the financial outlays involved in the construction process. By dissecting the material expenses, individuals embarking on a garage project can better prepare themselves financially, ultimately leading to a smoother and more efficient build.
Exploring material costs encompasses a range of crucial elements. Firstly, the quality of materials chosen plays a substantial role in the durability and longevity of the garage structure. Opting for high-quality materials may initially incur higher costs but can translate into cost savings in maintenance and replacements over time. Moreover, understanding the benefits of different materials, such as their insulation properties, weather resistance, and aesthetic appeal, is fundamental in making informed decisions during the planning and execution stages of the project.
Considerations about material costs extend beyond the mere monetary aspect. It involves evaluating the environmental impact of various materials, the availability of sustainable options, and the compatibility of materials with local building codes and regulations. By factoring in these considerations, individuals can not only create a structurally sound garage but also contribute positively to environmental sustainability and compliance with legal requirements.
Foundation Materials
When it comes to laying the groundwork for a 2.5 car garage, foundation materials are of paramount importance. The foundation serves as the base on which the entire structure stands, providing stability and preventing shifting or settling over time. Concrete is a popular choice for foundation materials due to its strength, durability, and ability to withstand varying weather conditions.
Key considerations when selecting foundation materials include the soil composition of the building site, the load-bearing capacity required to support the garage, and the local climate factors that may impact the stability of the foundation. Additionally, factors such as drainage systems, waterproofing measures, and insulation properties should be taken into account to ensure the longevity and structural integrity of the foundation.
Frame Materials
The frame of a 2.5 car garage serves as the skeleton that supports the overall structure, imparting strength and rigidity to the building. Common materials used for garage framing include wood, steel, and aluminum, each offering unique advantages depending on the desired aesthetics, budget constraints, and structural requirements.
Wood frames are popular for their affordability, ease of customization, and natural insulating properties. However, they require regular maintenance to prevent decay and termite damage. On the other hand, steel frames are known for their durability, resistance to pests, and minimal maintenance requirements but may be susceptible to corrosion if not properly treated. Aluminum frames offer a lightweight and rust-resistant alternative, ideal for coastal or humid environments.
Roofing Materials
Choosing the right roofing materials for a 2.5 car garage is crucial for safeguarding the interior space against the elements while enhancing its visual appeal. Popular roofing materials include asphalt shingles, metal roofing, and clay tiles, each with distinct advantages in terms of durability, cost, and design versatility.
Asphalt shingles are a budget-friendly option that offers a range of colors and styles, suitable for various architectural designs. Metal roofing, such as steel or aluminum panels, provides excellent resistance to adverse weather conditions, longevity, and low maintenance requirements. Clay tiles impart a timeless aesthetic, exceptional durability, and natural insulation properties, albeit at a higher initial cost.
Siding Materials
The choice of siding materials can significantly impact the curb appeal, energy efficiency, and maintenance requirements of a 2.5 car garage. Common siding options include vinyl, wood, fiber cement, and stucco, each offering unique attributes in terms of aesthetics, durability, and cost-effectiveness.
Vinyl siding is favored for its affordability, low maintenance, and wide array of colors and textures, making it a versatile choice for many homeowners. Wood siding provides a natural and classic look but requires regular upkeep to prevent rot and pests. Fiber cement siding blends durability with a realistic wood-like appearance and resistance to moisture and fire. Stucco offers a textured and durable finish, ideal for enhancing thermal insulation and noise reduction properties.
Labor Expenses
Moreover, the size and complexity of the garage project can also impact labor expenses. Larger garages or those with intricate designs may require more time and effort, consequently increasing labor costs. It is essential to discuss these details with the contractors to have a clear understanding of how labor expenses will be allocated throughout the construction process.
Additionally, the location of the project site can influence labor expenses. Remote or hard-to-access areas may lead to higher labor fees due to transportation costs or the need for specialized equipment. Proper planning and communication with the contractors can help mitigate these potential cost escalations, ensuring a smoother construction process.
Considering these factors when evaluating labor expenses for building a 2.5 car garage is essential in creating a realistic budget and timeline for the project. By recognizing the specific elements that contribute to labor costs, individuals can make informed decisions and effectively manage their expenses throughout the construction phase.
Contractor Fees
Contractor fees are a crucial component of labor expenses when constructing a 2.5 car garage. Hiring a reputable and experienced contractor is imperative to ensure the project is completed efficiently and to high standards. Contractors typically charge a fee based on the scope of work, complexity of the project, and their level of expertise.
It is essential to research and compare quotes from different contractors to find one that offers a balance between cost and quality. While opting for the cheapest offer may seem appealing, it is important to consider the contractor's reputation and track record to avoid potential issues or delays during the construction process.
Additionally, transparency in communication regarding pricing, payment schedules, and project timelines is key to establishing a good working relationship with the contractor. This not only helps in avoiding misunderstandings but also ensures that both parties are aligned in terms of expectations and outcomes.
Contractor fees encompass a range of services, including project management, procurement of materials, labor coordination, and overall supervision. Understanding the breakdown of these fees and negotiating them upfront can lead to a more harmonious construction experience and a successful outcome for the 2.5 car garage project.
Additional Labor Costs
In addition to contractor fees, there are often additional labor costs that should be accounted for when budgeting for a 2.5 car garage construction. These costs may arise from unexpected circumstances, changes in project scope, or the need for extra manpower to meet deadlines.
Anticipating potential overruns in labor expenses is essential, and budgetary flexibility should be built into the initial cost estimates. This can help prevent financial strain or project delays if unforeseen labor requirements emerge during the construction phase.
Furthermore, communication with the contractors regarding potential supplementary labor costs is key to managing expectations and avoiding disputes. Clear agreements on how additional labor will be charged and authorized can prevent misunderstandings and ensure that the project stays on track both financially and timewise.
By proactively considering and planning for additional labor costs, individuals can mitigate financial risks and uncertainties associated with building a 2.5 car garage. Being prepared for unexpected labor expenses not only demonstrates foresight but also reflects a proactive approach to managing the overall construction budget.
Permit and Regulation Costs
In the realm of constructing a 2.5 car garage, permit and regulation costs play a pivotal role in ensuring a smooth and compliant building process. These costs encompass various elements that are crucial to the legality and structural integrity of the garage project. First and foremost, obtaining building permits is a mandatory step that cannot be overlooked. Building permits serve as official approval from the local authorities, affirming that the garage construction plans comply with safety and zoning regulations. While the process of securing permits may involve some paperwork and fees, it ultimately guarantees that the project meets the necessary standards.
Furthermore, zoning regulations are another essential aspect to consider when delving into permit and regulation costs. Zoning regulations dictate how the garage can be built in relation to property lines, neighboring structures, and overall land usage. Adhering to these regulations is vital to avoid any legal issues or setbacks during or after the construction process. Assessing zoning regulations early on helps in planning the garage layout effectively within the permissible boundaries, ensuring a hassle-free journey from project initiation to completion. In essence, complying with building permits and zoning regulations not only streamlines the construction process but also safeguards the investment in the long run, emphasizing the significance of meticulous attention to these permit and regulation costs.
Building Permits
When it comes to building permits for a 2.5 car garage, homeowners need to navigate through a series of steps to secure the necessary approvals. The process typically involves submitting detailed construction plans, paying applicable fees, and obtaining reviews from local authorities. Building permits serve as a form of quality control, ensuring that the garage design and construction align with safety standards and local regulations. Moreover, these permits provide a sense of assurance to the homeowners that their garage project meets all legal requirements and is structured to endure for years to come.
Zoning Regulations
Zoning regulations govern how properties can be used within a specific area, playing a crucial role in dictating where and how a 2.5 car garage can be built. These regulations set forth guidelines regarding property setbacks, maximum building heights, and the overall aesthetic of the neighborhood. By understanding and adhering to zoning regulations, homeowners can avoid potential conflicts with local authorities and neighboring properties. Additionally, staying compliant with these regulations ensures that the garage construction progresses smoothly and is in harmony with the surrounding environment, underscoring the importance of considering zoning regulations as part of the overall permit and regulation costs.
Additional Features
When considering the construction of a 2.5 car garage, it is important to think beyond just the basic structure. Additional features play a crucial role in enhancing the functionality and aesthetics of the garage. These extra elements not only provide convenience but also add value to your property. Features such as electricity installation, storage solutions, and lighting fixtures can significantly improve the overall usability of the garage. It's essential to carefully plan and incorporate these features to create a space that meets your specific needs and preferences. Attention to detail in the selection and design of additional features can elevate your garage from a simple storage space to a versatile and organized area that enhances your daily life.
Electricity Installation
Electricity installation is a key feature that can transform your garage into a fully functional workspace. By adding electrical outlets, lighting, and possibly even heating or cooling systems, you create a conducive environment for various activities. Whether you plan to use the garage for woodworking, car maintenance, or as a hobby space, reliable electric supply is essential. It enables you to power tools, charge equipment, and illuminate the space effectively. When designing the electricity layout, consider the placement of outlets for optimal usability, safety regulations, and future expansion needs. Consulting with an electrician ensures that the installation meets local building codes and your specific requirements.
Storage Solutions
Efficient storage solutions are crucial for keeping your garage organized and clutter-free. From shelves and cabinets to overhead storage racks and pegboards, there are numerous options to maximize space and create a systematic storage system. Tailoring storage solutions to your needs – whether for sports equipment, tools, gardening supplies, or seasonal items – helps streamline access and retrieval, contributing to a well-structured and functional garage. Consider factors such as accessibility, weight capacity, and durability when selecting storage solutions to ensure long-term usability and organization within the space.
Lighting Fixtures
Proper lighting is essential for a well-designed garage that serves various purposes effectively. Adequate lighting fixtures not only improve visibility and safety but also create a welcoming environment. A combination of overhead lights, task lighting, and possibly even natural light sources can enhance the functionality and ambiance of the space. Factors such as brightness, color temperature, and energy efficiency should be taken into account when choosing lighting fixtures. Strategically placed lights facilitate tasks such as car maintenance, woodworking, or simply locating items within the garage. Thoughtful consideration of lighting fixtures ensures a well-lit and inviting atmosphere in your garage for any activity or project.