Intro
Understanding the specifics of 8 inch cinder blocks requires an examination of many factors that combine to influence cost. For housewives and homeowners, navigating through these pivotal elements can very much assist in determining a material and budget that works best.
Given their size and durability, these blocks are often a popular choice for various construction projects, including retaining walls, foundations, and more. Without a doubt, the necessity of planning is paramount in leveraging maximum value from one's budget when it comes to this essential construction material.
Materials:
The first step in any construction process is understanding the necessary materials. When planning for the use of 8 inch cinder blocks, it is imperative to create a thorough list of materials that includes each item with specific measurements. This not only streamlines your project route but also ensures that every element is accounted for.
List of Materials:
- 8 inch cinder blocks: Standard dimensions are 16 x 8 x 8 inches (each block weighs approximately 30-35 lbs).
- Mortar mix: About 1-2 bags, depending on slab or laying pattern. Each bag usually covers about 20 square feet.
- Rebar: Typically for additional support; cut lengths according to construction requirements.
- Sand: Often used depending on mortar specifications; 1 or 2 bags.
- Water: Required for mixing.
- Concrete mix (optional): If reinforcements are necessary, a couple of bags may be needed.
- Any surface treatments: Depending on desired finish for using on the block.
Before gathering everything, take the time to measure the area properly. This is essential for obtaining the right amount of material and avoiding waste, particularly when aiming for cost-efficiency.
DIY Steps:
Once materials are gathered, moving to DIY steps initiates. A detailed guide equips you with clarity and precision to successfully execute your construction project. Ensure each step follows logically and naturally from the one before.
- Step 1: Define the project specifications and layout on the ground.
- Step 2: Mix mortar to form a cohesive consistency.
- Step 3: Lay cinder blocks noting the alignment, ensuring straight lines while conforming to building codes if any apply.
- Step 4: Insert rebar if added support is required, securing appropriately within required blocks.
- Step 5: Allow for the mortar to dry – check dry times as per product guidelines to ensure structural integrity.
Horizontal reinforcement may lift the project's quality and it primarily avoids the shifting of the blocks with settling soil. Such rebar placement complements the project in long term stability.
Technical Aspects:
The tools required for the best outcome are just as critical as the materials themselves. Proper selection could elevate the kind of finish accomplished. Additionally, timing aspects play a significant role here.
List of Tools:
- Trowel: Assists in laying mortar and positioning blocks with ease.
- Level: Ensures layers remain uniform.
- Hammer or mallet: Helps adjust block positions during placements.
- Cutting tool: In case block adjustments are required.
- Tape measure: For precise measurements at every stage.
Be sure to refer to product-specific guidance on drying times of mortars or bonds, as work may often be time-sensitive depending on area humidity.
DIY Project Process:
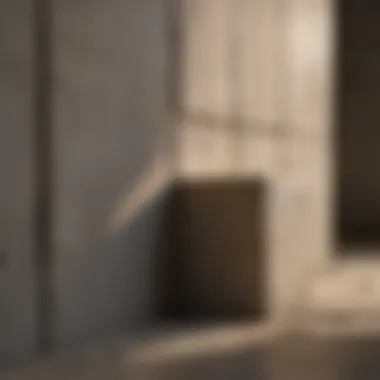
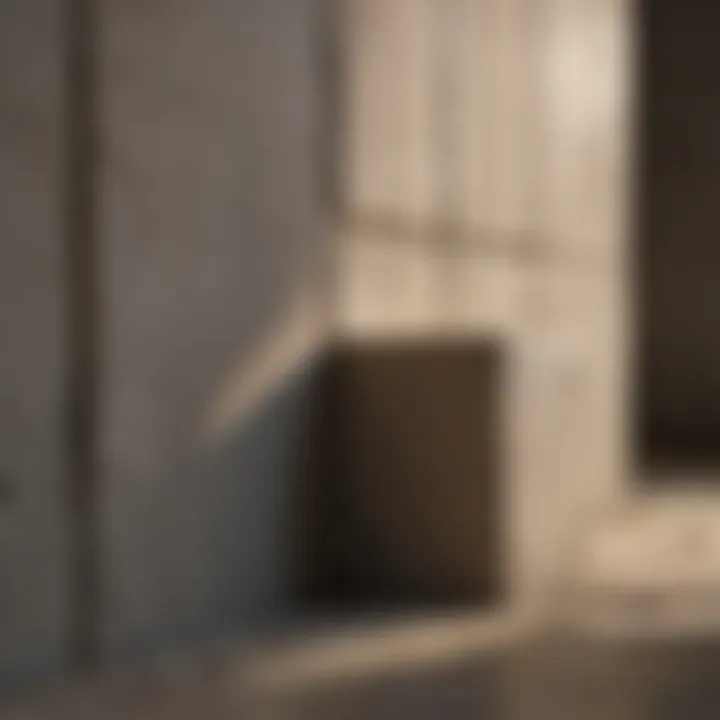
Transitioning to application follows through definitive sequential steps. This provides clearer stages and paves the path to smooth execution of your task.
Sequential Steps:
-
Prepare Site: Ensure it’s clean and ready. Remove debris and site material impairing the project.
-
Set Layout: Using stakes and string can delineate the boundaries ensuring perfect ground alignment.
-
Mix Mortar: Adapt utilising specified measurements for your batches.
-
Lay Start Points and Corners: Use the first block as the anchor for the pathway. Lay down the rest accordingly, using right angles.
-
Finalizing Alignment: Regularly check each side for calibration. Shift accordingly bit by bit.
-
Set Drying Time: After completing all blocks, the need for ample drying time is necessary so that no disturbances occur later.
Troubleshooting Tips:
Errors will happen; it is vital to prepare for probable issues in advance while addressing potential misalignments or other occurrences.
-
Misaligned blocks: Adjust while mortar is still wet; use a mallet carefully to manage placement while maintaining course language in designs.
-
Too fluid mortar mix: Dry mix quicker; consult with product guidance and re-measure taking guide steepness into effect.
Moving through this guide increases confidence, lowering unexpected occurrences. Targeted to both housewives and homeowners, each indicated segment equips you understanding critical necessities to better delineate the journey turn solid compliments to your home's architecture.
Investing time at the initial stages simplifies operation in following steps leading to a successful dining journey for home enhancement projects.
Prolusion to Cinder Blocks
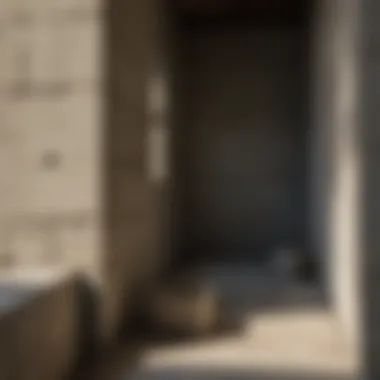
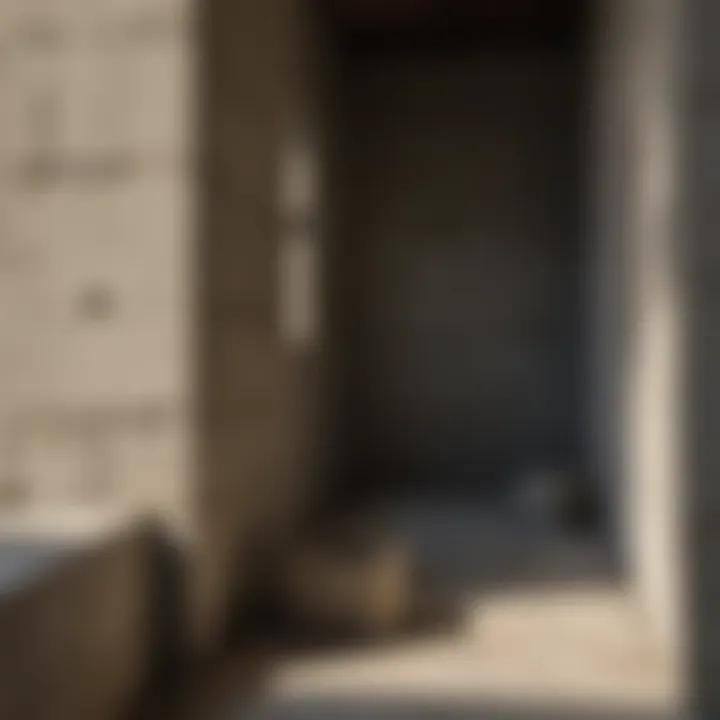
Cinder blocks are not merely an aspect of construction; they are pivotal contributors to structural integrity and design. Understanding cinder blocks, specifically the 8-inch variety, is essential when planning any building project. Their properties and application determine not only the quality of the build but also the cost efficiency over time.
Cinder blocks, made from a mixture of concrete and ash, offer tensile strength along with relative lightweight. They stand out for their insulation properties, enabling energy efficiency in buildings. When considering the investment in construction, they often represent savings in labor and maintenance in the long run. Any homeowner or house enthusiast should grasp their role in modern building practices.
In understanding their uses and advantages, we can make informed choices about construction methods and materials, hence gaining better insight into overall project safety, durability, and costs. The journey from planning through to execution becomes smoother with a clear grasp of such vital materials.
Definition and Purpose
Cinder blocks serve dual purposes: they provide structural support and insulation. This composite material functions well in varied environments. Understanding their definition is crucial for those venturing into construction or renovation. Traditionally referred to as concrete masonry units (CMUs), they come in varied sizes and have different properties based on composition.
The purpose of the cinder block is versatile. Aside from forming structural walls, they also act as barriers to moisture and sound. These_funcions_ make them a popular choice in both residential and commercial applications.
Common Applications in Construction
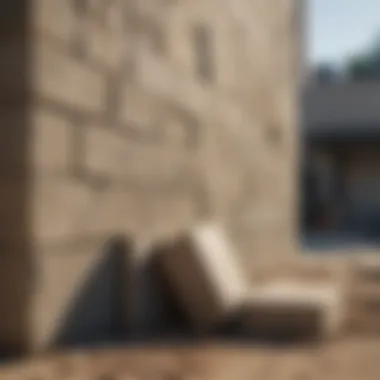
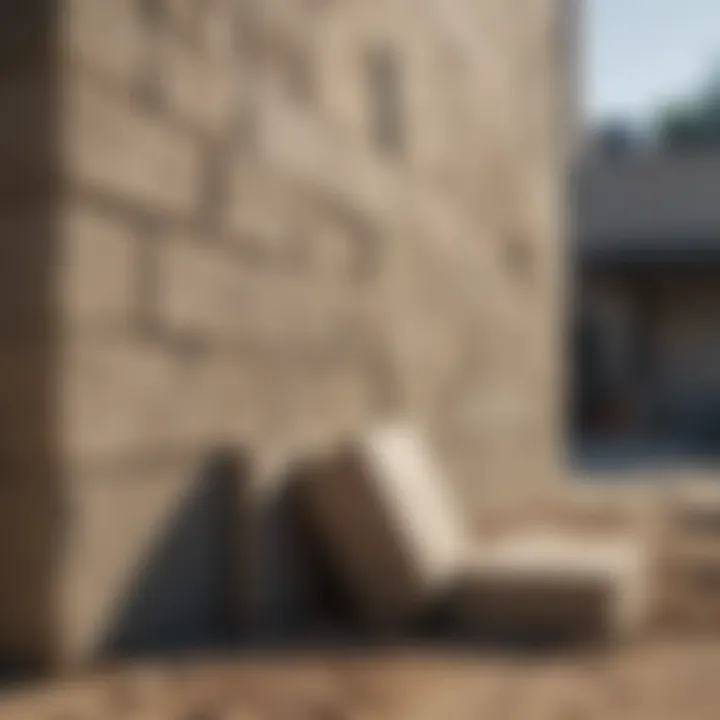
Cinder blocks find their applications in diverse construction settings. Common uses include:
- Foundation walls: Provide robust and stable bases for various structures.
- Building rooms: Offer modular advantages for quick assembly and customization.
- Exterior walls: Enhances appearance and resistance against the elements.
- Fireplaces: Selected for their thermal mass property, suitable for heat retention.
- Walls of gardens and other landscaping features: Used for creating attractive designs as well as functional barriers.
Their adaptability answers a variety of building needs and offers efficient solutions in architecture. From houses and garages to mailboxes, the utilization of cinder blocks is less about luxury and more about dependability and function.
Remember, the choice of using 8-inch cinder blocks can greatly influence overall construction time, financial budgeting, and long-term maintenance strategies.
Understanding Inch Cinder Blocks
Understanding the cost factors associated with 8 inch cinder blocks is crucial for anyone planning a construction project. The 8 inch dimension designates the height and thickness of the block, which directly influences the application in various structural contexts. Additionally, its standardized size allows for easier calculations regarding material needs and costs for potential projects.
The advantages of embracing 8 inch cinder blocks are evident. They offer better insulation, load-bearing capacity in comparison to smaller dimensions, and versatile application. An awareness of the specific roles and advantages of these blocks helps to craft informed buying decisions. Various uses could include building walls, foundations, or even landscape structures, thereby increasing the block's value for diverse projects. Considering these factors assists home owners and housewives navigate the expansive options in cinder blocks regarding practicality and overall impact on project expenses.
Dimensions and Specifications
The formal specifications of 8 inch cinder blocks extend beyond mere dimensions. Generally, an 8 inch cinder block typically measures 8 inches in height, 16 inches in length, and 8 inches in width. This measurement is fundamental, as it allows builders to easily determine the quantity needed for a given project. Each block covers 1.33 square feet. Additionally, the hollow cavity of the block can be utilized for reinforcement or insulation materials depending on the specific project requirement.
Advanced specifications may also touch on the manufacturing tolerances, such as variations in thickness not exceeding 0.5 inches in production, which affects load ratings and insulation qualities. Knowing these details allows individuals to predict performance and choose blocks that align directly with the intended use of the structure.
Material Composition
A profound understanding of material composition shapes both the cost implications and the performance attributes of 8 inch cinder blocks. These blocks are typically made from a mixture of cement, additives, and aggregates such as sand or gravel. Variances in the ratios of components contribute to differing strengths, weights, and thermal resistance.
Some blocks include more durable aggregates, enhancing their resilience in harsh conditions. Other cinder blocks may have additives for water resistance, which effectively enhances overall longevity. When evaluating options, buyers must consider how each variant aligns with the specific environmental demands of their construction site.
Cinder blocks can also fall under category classifications like light-weight or heavy-duty based on their internal structure and material consistency. Emphasizing the advantages of each type serves to delineate the thoughtful choices available, which allows for informed decision-making when it comes to meeting budget constraints while obtaining high-quality materials suitable for lasting applications.
"Understanding both dimensions and material composition allows buyers to make informed decisions that meet both structural needs and budget considerations."
This analysis ensures that prospective buyers can approach their projects fully informed, recognizing the relevance of each aspect, from dimensions to material choice, ultimately facilitating wiser purchases.
Factors Influencing the Cost of Inch Cinder Blocks
Understanding the various factors that influence the cost of 8 inch cinder blocks is essential for anyone involved in construction or renovation projects. The price of these blocks can vary significantly based on several elements that should be considered. Knowledge about raw material prices, manufacturing processes, and transportation costs can provide insights into how expenses compile. For homeowners or builders, functional financial planning relies on comprehending these factors since it greatly affects budgeting and overall project margins.
Raw Material Prices
The cost of raw materials is one of the most significant elements affecting the price of 8 inch cinder blocks. The core materials used in production include aggregates like sand and gravel, cement, and water.
The price fluctuations of these materials is often linked to economic factors such as market demand, availability, and regional extraction costs. For example, when cement prices rise due to decreased production or increased demand in construction from industries, the costs of cinder blocks consequently increase. There is attention to international price movements in commodities as well. This makes understanding regional sourcing options vital for effective budgeting.
- Sand and Gravel: The backbone aggregate needed in concrete mixtures.
- Portland Cement: Major material influencing both composition and price.
- Water: Despite being abundant, levels of treatment and distribution can incur costs.
Each of these components directly relates to the overall material costs. Examining suppliers for competitive rates can counterbalance excessive material costs.
Manufacturing Processes
Manufacturing processes directly impact the pricing structure of 8 inch cinder blocks. These processes generally include mixing, molding, curing, and quality control. The degree of automation in the procedure can heavily influence base costs.
When blocks are mass-produced in automated units, the costs generally lower due to less labor dependence. Conversely, smaller and manual operations may charge higher prices due to more labor and attention to detail.
Thus, understanding manufacturing methods is key:
- Batch Mixing: Involves combining components in predetermined ratios.
- Molding: Techniques vary, affecting block integrity and prices. Manual or complex molds often increase costs.
- Curing Time: Typical waiting period influences throughput and overhead costs.
Every production component correlates to quality and longevity in use. Knowing how blocks are made assists in judging their fair cost.
Loading and Transportation Costs
Lastly, loading and transportation costs are pivotal in setting the final sale prices for 8 inch cinder blocks. These costs take into account how far the blocks must travel, methods of loading, and route specific challenges.
Consider the following:
- Local Supply Proximity: Closer quarries usually mean lower transport costs.
- Transport Methods: Trucking and rail bring different expenses based on efficiencies.
- Handling Fees: Typically accrue when loading and unloading heavy blocks, affecting budgets.
Essentially, cinder block pricing reflects both logistical challenges and the destination of delivery. Proper cost evaluations often look at suppliers who prevent unnecessary transportation hikes.
In summary, understanding how raw material prices, manufacturing processes, and transport costs impact the selling price helps any buyer be more move diligent and strategic. Awareness with this knowledge enhances the capacity to budget effectively while optimizing site preparation using 8 inch cinder blocks.
Understanding these factors can help eliminate surprises during budgeting and streamline decision-making in construction projects.
Cost Variations Across Regions
Understanding the cost variations of 8 inch cinder blocks across different areas is crucial for several reasons. It can impact project budgets and determine sourcing locations. Regional pricing differences often stem from factors like availability of raw materials, transportation costs, and local demand. Each of these elements can significantly influence the total expenditure faced by a homeowner or contractor, thereby necessitating a careful review.
When evaluating costs, it’s essential to acknowledge that urban and rural areas may experience distinct economic conditions. Urban areas often see higher costs due to elevated demand and greater overhead expenses for suppliers. Conversely, rural areas might enjoy lower prices, yet they frequently face availability issues, which can drive costs up unexpectedly.
Urban vs.
Rural Pricing
Pricing for 8 inch cinder blocks in urban settings is often notably higher compared to rural surroundings. The reasons can usually be traced back to several dynamics:
- Increased Demand: Urban areas often have more contractual work. This leads supply companies to raise prices accordingly.
- Transportation Expenses: As delivery distances increase or the operation costs to maintain a connection to city centres rises, supplier pricing reflects this.
- Higher Overheads: Businesses in urban settings may account for additional costs, such as rent and labor, influencing the final price tag.
For homeowners, understanding these pricing patterns can lead to better decisions. Decisions about where to buy or how much of a certain material to purchase may save significant amounts of money. The knowledge serves homeowners who want to avoid high prices during implementation of projects.
Regional Supply and Demand Dynamics
The principles of supply and demand form a vital pillar in the pricing landscape of 8 inch cinder blocks. Individual markets exhibit unique characteristics based on the consumption needs found in different areas, leading to fluctuations in pricing that can be significant.
For instance, a market that is periodically flooded with building contracts may experience spikes in prices for cinder blocks. When demand exceeds supply in such situations, suppliers can charge noticeably more. On the other hand, a locality with less construction activity often sees stable and lower prices due to surplus supply. Here are key takeaways on Regional Supply and Demand Dynamics:
- Increasing Construction Projects: Areas experiencing growth in infrastructure get charged higher for raw materials like cinder blocks due to competition.
- Nearby Suppliers: Being closer to raw resource suppliers could drive down logstical and shipping costs in noticeable ways.
- Local Regulations and Subsidies: Certain regions may benefit from government policies guiding local building material costs which offers more value over similar blocks sourced elsewhere.
Overall, monitoring local market dynamics becomes vital for house owners or builders planning projects with a concrete foundations at their core. Understanding these factors allows smart budgeting and efficient planning actions to be carried out more effectively.
Market Trends and Economic Impact
Understanding market trends and their corresponding economic impact provides valuable insights into the pricing and availability of 8 inch cinder blocks. In a fluctuating market, timely knowledge of trends helps buyers make informed decisions in their procurement strategies.
Influence of Construction Demand
Construction demand serves as a significant factor impacting the pricing of cinder blocks. When construction projects surge, whether residential or commercial, the demand for building materials like cinder blocks heightens. This increase induces competition among buyers that may lead to price escalation due to the limited supply of products.
- Increased housing development drives demand for 8 inch cinder blocks.
- Infrastructure projects, such as schools and hospitals, raise the stakes in material sourcing.
- Individuals may face higher prices or longer wait times during peak building periods.
During these times, it becomes crucial for homeowners and builders to have alternatives or at least be prepared to adjust their budgets. Understanding the market draw can keep purchasers from making rash choices driven by urgency.
It is essential for buyers to gauge the trends actively, especially in four seasons when housing activity can shift.
Impact of Economic Fluctuations
Economic fluctuations notably influence the pricing landscape for materials, including 8 inch cinder blocks. The effects of inflation or recession can create ripple effects throughout the construction mosaic. When inflation rises, costs of production materials become unstable, elevating the end-user prices. In contrast, during recessive periods, construction might slow, causing a decrease in demand and a potential price drop.
Considerations for Homeowners:
- Keeping track of the economy signifies staying keen-eyed regarding market opportunities.
- Economic reports and local construction trends are imperative facts to analyze before typically spending sizable budgets.
- Adjustment strategies—such as opting for bulk purchases during economically favorable periods—can lead to savings.
By becoming informed in these areas, house owners can move in the direction of efficient construction planning and financially-responsible purchasing of cinder blocks.
Comparative Cost Analysis
Conducting a comparative cost analysis is essential when evaluating the use of 8 inch cinder blocks versus alternative building materials. This analysis emphasizes understanding costs in a broader context, not just purchasing price. By considering factors like installation, durability, and overall performance, buyers can achieve more informed decisions.
Cinder blocks tend to be valued for their unique qualities. They offer insulation and structural integrity. However, when placed alongside other materials like concrete, wood, or even steel, the evaluation becomes multi-dimensional.
Cinder Blocks vs Other Building Materials
When looking at costs, cinder blocks present competitive pricing points. Often, they are cheaper than materials like poured concrete but differ in application. For instance, both have excellent durability but vary in terms of thermal mass, production techniques, and labor costs associated with their use.
-
Cinder Blocks:
- Benefits: Affordable, strong, and fire-resistant.
- Usage: Commonly used for foundations and walls.
- Cost per Block: Generally ranges from $1.50 to $3.00 each, depending on the supplier.
-
Poured Concrete:
- Benefits: Provides better moisture resistance and a monolithic structure.
- Use Cases: Often favored for load-bearing applications.
- Cost Comparison: Generally more expensive when considering forming and labor costs.
-
Wood Products:
- Benefits: Aesthetically pleasing and offers natural insulation.
- Use Cases: Popular for framing and interior walls.
- Cost Aspect: Prices can be highly variable, making cost comparison complex due to supply chain fluctuations.
Doing a side-by-side analysis across materials helps in making feasible decisions according to project requirements and budget constraints. Each material has benefits tied to specific applications which should also influence choices.
Long-term Cost Considerations
Looking beyond initial expenditures is vital in understanding the true financial implications of cinder blocks. Long-term costs encompass maintenance, energy efficiency, and even longevity of structures built with different materials.
- Maintenance Costs: Cinder blocks require little upkeep compared to wood structures which suffer from rot or pest issues.
- Energy Efficiency: Cinder blocks can have superior thermal properties, meaning once built, they can lower energy costs for heating and cooling.
- Longevity: Structures made with cinder blocks often withstand environmental stressors better, leading to lower costs over time as repairs are minimized.
In summary, a comprehensive cost analysis not only aims to highlight upfront costs but also brings to light ongoing expenses associated with material performance.
Understanding these nuances encourages more intelligent purchasing decisions. Cinder blocks may stand more favorable when deliberately compared against alternatives. Contact realized options that suit both financial and functional project needs to maximize satisfaction and cost-effectiveness.
Practical Tips for Buying Cinder Blocks
Identifying Reliable Suppliers
Finding dependable provider is crucial in ensuring quality. Purchase from companies known for their materials in the construction industry. Local options are often preferable. They can offer better prices than national chains without having to pay high shipping costs.
Research Online and Offline:
- Check online reviews to see past customer experiences.
- Visit local hardware stores for physical insights.
- Engage with contractor communities online to get personal recommendations.
Lastly, consider checking their inventory. A good supplier should have consistent stock to maintain quality and consistency in your project.
Negotiating Prices Effectively
Once a reliable supplier is found, negotiating becomes essential. Suppliers often appreciate when customers are informed about market standards. Being hafquainted with competitive prices provides a good basis when requests for lowered rates arise.
Consider these strategies:
- Do your homework on local market prices.
- Build rapport with suppliers; they are more likely to offer a discount to regular clients.
- If elements of the contract, such as costs, feel transparent, analyze different quotes from various suppliers promptly.
Often suppliers may have rooms for discounts when purchasing multiple materials or in large amounts. It's worth investigating
Bulk Purchase Considerations
Buying in bulk can lead to lower costs per unit and reduce waste. Before making this decision, consider your project needs. Having about 10% extra blocks than initially estimated can help address uncertainties in your project duration.
Benefits of bulk buying:
- Cost Efficiency: Individual purchase prices tend to rise, but bulk orders typically result in significant discounts.
- Time-Saving: A single large order reduces the hassle of multiple trips to suppliers.
- Reduced Transportation Costs: Less frequent shipping means lowering transport fees.
Overall, strategic advance planning and consideration about the project and local options enable homeowners to maximize the benefits of their investment in 8 inch cinder blocks. Assembling this knowledge translates to frugality in your projects. Utilize local resources, negotiate thoughtfully, and weigh your purchase strategies carefully for more efficient project management.
Culmination
The conclusion serves as an essential segment of any comprehensive discussion, particularly about the cost of 8 inch cinder blocks. In this article, we have explored diverse factors influencing pricing. Recognizing the total cost implications of 8 inch cinder blocks supports homeowners and buyers in better planning their construction projects, ensuring budgets are adhered to closely.
Summarizing Key Insights
To summarize important takeaways:
- Understanding Material and Labor Costs: These couple the physical attributes of cinder blocks with location-specific pricing for labor. Knowing this aids decision making.
- Significant Regional Variations: The article illustrates how urban areas often exhibit higher costs compared to rural locations due to differing demands and availability.
- Importance of Bulk Purchasing: Buying in larger quantities generally results in cost efficiency, meaning significant savings are achievable for larger projects.
- Market Influence: Fluctuations in market dynamics must be watched closely, as they can quickly alter pricing and availability.
By embracing these insights, readers can approach purchasing cinder blocks with confidence and foresight.
Future Outlook for Cinder Block Pricing
Looking into the future, several trends will likely shape the cost of 8 inch cinder blocks. First, demand for cinder blocks may fluctuate alongside housing needs. As urbanization continues to rise, construction will frequently seek durable and efficient materials, enhancing cinder blocks' positions in this area.
Additionally, advancements in manufacturing processes could increase production efficiency, potentially stabilizing prices. New technologies might provide alternatives or variations in cinder block materials, further diversifying consumer choices.
Economic conditions are also crucial for predicting future prices. A recession can suppress demand, leading to countywide lower prices. Conversely, a robust economy often means construction booms—and thus higher pricing due to demand. Keeping these situations in mind will help you anticipate future market behaviors effectively.
In summary, understanding not just the cost but the broader dynamics of the market helps in strategic decision-making for your building projects.
Ensuring you remain well-informed and anticipative of future changes significantly benefits not only the immediate construction plans but also long-term investments.