Intro
The process of estimating the price for drywall sheets can seem overwhelming, but shold not be complicated. This exploration aims to enlighten the reader with comprehensive details necessary for undertandng what impacts the prices involved in drylwall purchases. Baring each effect is crucial, as decisions made during this phase will largly affect any construction or renovation project's overall budget.
Healthcare costs and general living expenses can negatively pinpoint those who push to DIY or hire out professional work. Learning about pricing adds more insight, particularly for house owners and housewifes striving for home improvement.
Materials:
Understanding what materials are necessary before starting a drywall project is crucial. A well-itemized list can vastly improve how much material is need and help avoid waste
List of Materials:
- Sheetrock or drywall sheets (standard 4-foot by 8-foot 1/2-inch thick)
- Drywall screws (1-5/8 inch)
- Joint compound (5-gallon bucket)
- Tape (mesh or paper)
- Corner beads (metal or plastic)
- Finishing sandpaper (240-grit)
DIY Steps:
Following the correct steps when handling drywall ensures that the project comes together smoothly. Each step should be done precicesly.
Detailed Instructions:
- Prepare the area: clear any furniture or obstacles, ensuring plenty of space.
- Measure walls: Determine and record the area
- Cut drywall sheets as needed: Make sure to cut sheets to size with a utility knife.
- Install drywall sheets securely to wall using drywall screws. Leave slight space for the pieces to expand.
- Tape seams using either mesh or paper tape,: ensuring smoothness etiquette practical.
- Apply joint compound neatly over the seams, feathering out edges.
- Sand surfaces while joint compound is dry: Ensure smooth prepping before painting goes on.
- Finish vertical edges: Repeat sanding address overall textures amateur builders often overlook.
Technical Aspects:
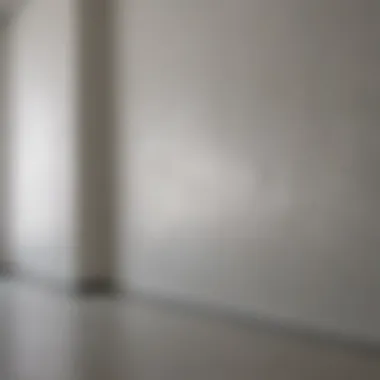
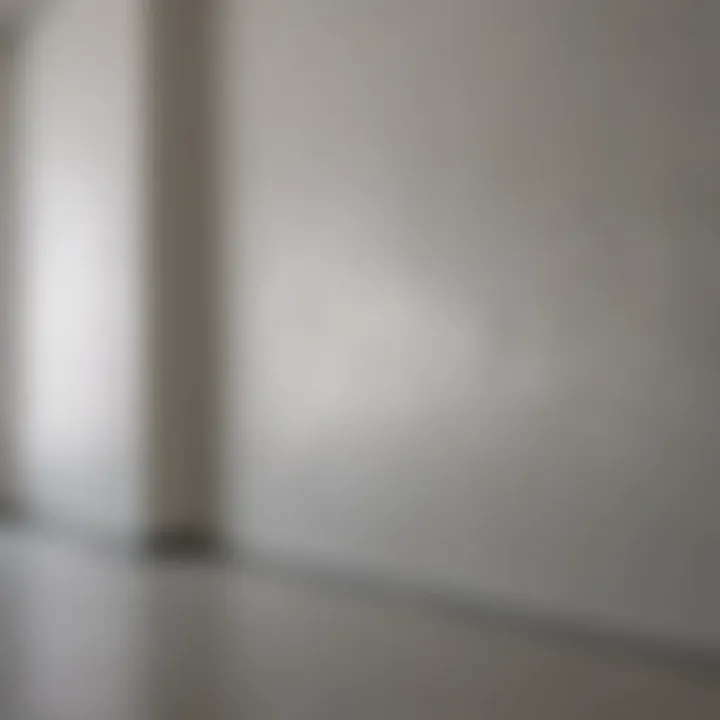
Widely recognized here are the major tools used in drywall projects. Owning skill comes with adequate knowledg, leading to excellent results.
Collection of Tools:
- Utility knife
- T-square (or drywall square)
- Cordless drill or power drill
- Drywall saw d- Tape measure
- Sanding block
Timing Specifics and Techniques:
Be aware that timings vary based on complexity or dimensions involved on repair. Precision makes or breaks projects like this. Ensuring areas are dry resembles terribly troublesome.
DIY Project Process:
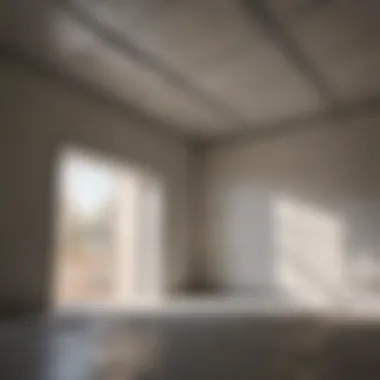
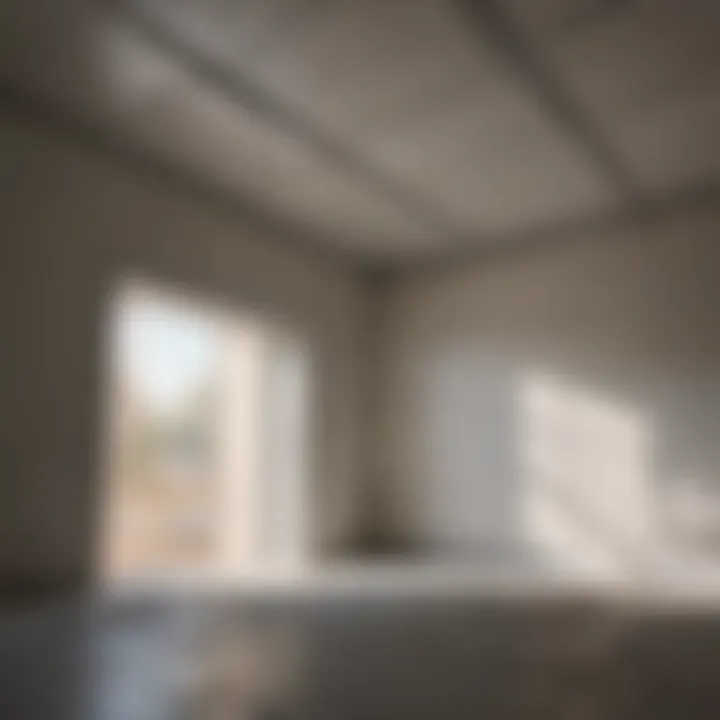
Thorough understanding enhances construction skills significantly. Not following you down won’t actually discourage you renovation process overall.
Detailed Installation Method & Timings:
- Trace steps as noted previously, reviewing each stage strictly.
- Leave time for filling nail holes before transitioning into treat elevating construction steps proficiently.
Tips for maximum quality construction: be gentle but earnest while compacting corners curves where visual chaos coolskin minimizes naturally indoors.
In construction, researching material fit to your interior necessities saves money on work needed down the line. On average, home renovations ensure not only gain improved durability but visual aesthetic appeal.
Troubleshooting Tips:
Despite our efforts, issues arise. Common mistakes are wide gaps or uneven placements. Here’s how to address them:
- When gaps occur between panels, avoid panicking. Simply skim-fill latitudes helps cause dealing simplifies minutia.
- Inconcistencies with seams can camouflage all others insotantly. Consult specialized forums at sites such as Reddit and material links on Facebook can provide valuable tips throughout.
Avoid recommending excessive wrong-kind installation to preserve structures purposely, Content promoting deep wandering approaches highlights importance backtracking continually reassesses remodeling solutions bringing competent solutions!
Prolusion to Drywall and Its Uses
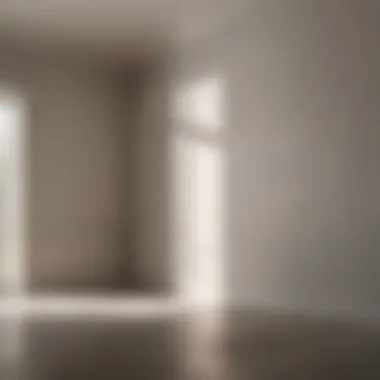
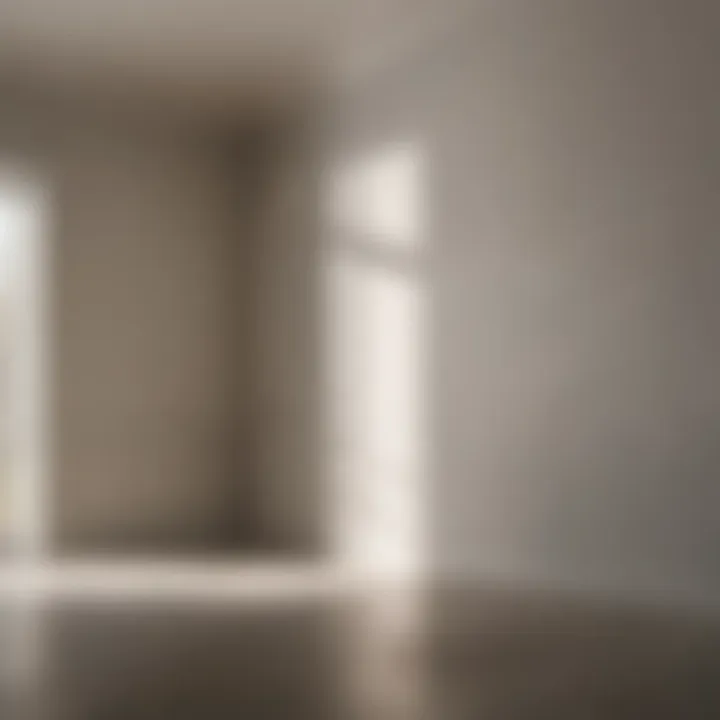
Understanding drywall is crucial in the context of construction and renovation. It is an essential material used in nearly every building project. Drywall's versatility and ease of installation make it a preferred choice for many contractors and homeowners.
Definition and Composition of Drywall
Drywall, also known as gypsum board or plasterboard, is primarily composed of a core of gypsum (a mineral) sandwiched between two sheets of heavy paper. The properties of gypsum—the ability to resist fire and assign thermal insulation—contribute to its significance in construction. Drywall panels typically come in standardized sizes, with thicknesses ranging between 1/4 inch to 1/2 inch. Variations exist that provide specific advantages in different types of construction projects.
Common Applications in Construction
Drywall is commonly used in interior wall and ceiling construction. Some common uses include:
- Residential construction: In homes, drywall provides a clean and finished appearance. It is used in living areas, kitchens, and bathrooms.
- Commercial places: Many office spaces rely on drywall for creating offices and conference rooms.
- Renovations and remodeling: Homeowners frequently use drywall during renovations to alter and refresh spaces.
- Fire-resistant needs: Certain types of drywall are specifically designed to meet fire codes in commercial buildings.
By comprehending the definition and common uses of drywall, homeowners can make educated decisions when choosing this material for their projects. Since drywall also substantially impacts cost, understanding its pricing dynamics is essential following this context.
Factors Affecting Drywall Sheet Pricing
When considering the various aspects of drywall sheet pricing, there are distinct factors that determine the cost. Understanding these factors is essential for both homeowners and contractors. Prices can vary significantly depending on material properties, manufacturing processes, and logistical dynamics. Elucidating these factors can help in gaining better insights and making informed purchasing decisions.
Material Quality and Type
The category of material used for drywall profoundly influences the price. Drywall is not a singular product; it comes in multiple forms such as standard, moisture-resistant, and soundproof options. Higher quality materials, such as mold-resistant drywall, typically encounter a hike in price due to their specialized manufacturing. On the other hand, basic types of drywall may offer lower costs but provide fewer benefits in specific applications.
Each type serves unique purposes, like standard drywall for general use and cement board for high-moisture areas, showcasing the variance in pricing influenced by quality and type.
Thickness Variations and Their Impact on Cost
Thicker drywall sheets often have a premium associated with them. A standard drywall sheet sold commonly comes in 1/2 inch thickness. However, for enhanced soundproofing or durability, some customers may choose heavier options like 5/8 inch thick sheets. These added millimeters for strength or insulation inherently lead to a price increase. Therefore, understanding the thickness necessary for your project is crucial for estimating overall costs.
Cost of Raw Materials and Production
Prices of raw materials fluctuate due to market conditions and availability. Key components of drywall include gypsum, paper, and additives. For example, a tight gypsum supply chain can inflate prices. Manufacturing costs also play a large role, encompassing labor, energy, and operational expenditures. An understanding of these underlying factors allows stakeholders to anticipate cost changes effectively based on raw material pricing trends.
Transportation Costs and Logistical Considerations
Once drywall is produced, transporting it to the desired location adds yet another layer to the pricing. Distance from the manufacturing plant to construction sites can affect the overall cost structure. Timely delivery and the choice between land or ocean freight can also lead to significant differences in incurred costs. For homeowners and builders, planning for these logistics is paramount, as long transport commitments often translate to higher expenses.
The effective distribution of drywall sheets requires a pronounced emphasis on logistics, influencing total pricing.
Regional Price Variations
Understanding regional price variations is key when dealing with drywall sheets in construction. The price of drywall is not uniform across different locations. Urban demand, population size, and distribution logistics create dynamic pricing scenarios that can significantly influence budgets for construction projects.
Price Differences Across Urban vs.
Rural Areas
In urban areas, the density of population typically raises demand. Various construction projects regularly occur, translating to consistent multi-family units or high-rise construction projects. Vendors are likely to keep ample stock to meet this demand. As a result, prices may sometimes be lower than in rural areas due to competition among suppliers.
In contrast, in rural regions, the limited number of houses can result in less frequent deliveries and a smaller pool of suppliers. This decreased competition often leads to elevated pricing on drywall sheets—prices can vary considerably here. For instance, rural homeowners may find themselves purchasing drywall at a premium because driving distance from suppliers adds to transport costs. Therefore, construction planning needs to carefully consider location and how this could impact the overall budget.
Impact of Local Market Conditions
Market conditions also play a significant role in drywall pricing. Local economic factors, including job growth and housing demands, can either inflate or depress prices. In there is a construction boom, the likelihood is that drywall manufacturers will increase prices in anticipation of demand surges.
Conversely, during economic downturns, decreased construction activity often lowers raw material or drywall prices. Local building codes could further affect supply chains, land costs, and thus the way drywall sheets are priced. When approaching a project, it is prudent to analyze local demand indicators carefully because they have a direct relationship to retail pricing. Title Companies and Local Builders often have relevant data on these trends.
State-Specific Regulations and Their Effect on Prices
Regulations set by specific states influence how drywall is priced. Every state might have different building codes that necessitate certain standards for drywall usage. Certain types, such as fire-resistant drywall, could be required depending on regulations demonstrated in that area.
Logistical factors created by these regulations mean additional handling, which can incur added costs. Manufacturers might also face strict environmental regulations or incentives that price the bulk jobs toward a tenant involvement condition.
Furthermore, any state-specific programs aimed at increasing energy efficiency can lead to increased demand for certain specialized drywall products. Recognizing these variations will help buyers make informed purchasing decisions. Consulting local norms and ideologies leads to smoother execution when planning buys or large orders ahead of tighter timetables.
Considering these diverse elements around regional price variations can offer potential advantages, maximizing budget effects when it comes to purchasing drywall sheets.
Current Trends Influencing Drywall Sheet Pricing
Understanding the current trends in drywall sheet pricing is essential for homeowners and construction professionals alike. The drywall market does not operate in a vacuum; there are various forces at play that influence prices. Recognizing these trends assists stakeholders in making d5etailed and informed decisions regarding purchasing and budgeting.
Market Demand and Supply Considerations
The relationship between market demand and supply plays a crucial role in determining the prices of drywall sheets. In recent years, the construction industry has witnessed fluctuations in demand, particularly due to housing market conditions and fluctuating economic factors. An increase in demand often results in higher prices, especially if supply cannot keep up. Conversely, if construction slows down, excess inventory may cause drywall prices to decline.
Stakeholders should be cautious about timing their purchases. Competing projects usually push demand higher, which might make it expensive during peak seasons, such as spring and summer. On the other hand, buying during off-peak seasons can yield better prices. It's wise to regularly monitor trends related to both demand and supply to optimize procurement strategies.
Technological Advances in Manufacturing
Technological advancements in manufacturing have a dual effect on pricing structures. On one hand, improvements in production processes can lead to more efficient production, thereby reducing overall costs. For instance, automation and newer machinery in drywall manufacturing can streamline operations, enabling quicker turnaround times without sacrificing quality.
Nevertheless, investing in cutting-edge manufacturing technology might increase initial costs. These manufacturing changes can eventually affect the wholesale prices of drywall sheets. Therefore, understanding the manufacturing technology landscape helps predict either a rise or fall in drywall prices.
Sustainability and Eco-Friendly Options
Today, there's a growing awareness of sustainability within the construction industry. This trend relates closely to drywall sheet pricing. Many homeowners desire eco-friendly materials, which are often marketed separately and can command a premium price. These greener options do not only include recycled drywall sheets but also products that are easier to recycle at the end of their life cycle.
While families seek sustainable options to reduce their carbon footprints, they must be aware that these green alternatives sometimes come with a higher price tag due to the costs associated with their manufacturing and recycling. However, the long-term savings on energy and maintenance can make such choices sound investments.
Integrating sustainable practices in drywall sourcing not only benefits homeowners' budgets but also the environment.
In summary, current trends in the drywall industry significantly impact pricing dynamics. Being proactive by staying informed about market demand, manufacturing technologies, and eco-friendly options can guide homeowners and construction stakeholders in their purchasing decisions and financial planning.
Estimating Costs for Different Types of Drywall
Estimating costs for different types of drywall is a crucial step for homeowners looking to undertake construction or renovation projects. Understanding these costs helps in budgeting and making informed decisions. Different drywall types come with unique properties, purposes, and varying price points. This section focuses on detailing these costs so you can align your needs with your financial considerations.
Standard Drywall Sheet Pricing
Standard drywall, often referred to as regular or whiteboard, is the most common type used in residential construction. Pricing for standard drywall sheets typically ranges from $10 to $15 each, depending on the dimensions and local market conditions. The standard size for drywall sheets is usually 4 feet by 8 feet. However, larger sizes such as 4 feet by 12 feet are also available and might incur slightly higher costs.
It is also essential to consider additional costs in your estimate. These include expenses for drywall installation, taping and finishing, and any necessary tools or preparation work required. The total cost will depend on your project scope.
Water-Resistant and Soundproof Variants
When you require specialized drywall variants, pricing can significantly differ. Water-resistant drywall, for instance, is designed for areas exposed to moisture, making it ideal for bathrooms and kitchens. Sheets of water-resistant drywall usually range from $15 to $20.
Soundproof drywall, another premium option, is engineered to reduce noise transmission. This type typically costs about $30 to $40 per sheet. Always assess your specific needs when choosing these variants, as the increased costs can be justified by the benefits they provide for particular environments in your home.
Fire-Resistant Drywall Costs
Fire-resistant drywall is constructed to provide an enhanced level of protection against fire, established by its core material. It is often used in garages, between townhouses, and in other spaces where fire safety regulations need to be met. Expect to pay around $12 to $20 per sheet for standard fire-resistant drywall. However, specific building codes and regulations may affect the necessary thickness and type of fire-resistant drywall you must use, which could influence the final cost.
Estimating costs for drywall requires careful planning and a clear understanding of the options available. Whether you are considering standard, water-resistant, soundproof, or fire-resistant varieties, each option carries different pricing structures that afect your budget planning. Connecting with local suppliers can provide insights on realistic pricing and product availability.
Tip: It is prudent to obtain several quotes before making a purchase, ensuring you receive the best deal for your needs while maintaining high-quality standards.
Where to Purchase Drywall Sheets
In any construction or renovation project, the sourcing of drywall sheets plays a key role. It influences not just the cost but also the quality of the final product. Understanding where to purchase these essential materials can help one make informed and strategic choices. The right source can provide excellent prices and valuable assistance, ensuring that you find the most suitable option for your project's specific needs. Below, we will examine various purchasing avenues for drywall sheets including home improvement retailers, specialized building supply companies, and online purchasing options.
Home Improvement Retailers
Home Improvement Retailers such as Home Depot and Lowe's are typically one of the first options for many homeowners. They offer a vast selection of drywall sheets suited for various applications. These retailers often carry standard drywall, as well as specialty types like water-resistant or soundproof drywall.
Benefits:
- Accessibility: Generally located in urban and suburban areas.
- Expertise: Knowledgeable staff can assist in making choices suited for your specific projects.
- Delivery Options: They may also offer delivery for bulk purchases.
Additionally, shoppers may benefit from seasonal discounts or sales events. However, prices can occasionally be higher compared to specialized suppliers due to higher overhead costs associated with operating retail storefronts.
Specialized Building Supply Companies
Specialized building supply companies, such as Berger Building Products or BC Building Supplies, often contribute significant value for more professional projects. These suppliers strictly focus on construction materials. They may have a deep inventory of different drywall types, including unique products that may not be available at standard retailers.
Considerations:
- Product Range: Often include specific drywall types like fire-rated options.
- Bulk Pricing: These suppliers usually provide competitive pricing for larger orders.
- Expert Consultations: The staff are often more specialized in construction aspects, able to give specific advice tailored to construction professionals.
Notably, shopping here may suit larger projects better, where purchasing in bulk can translate into savings.
Online Purchasing Options and Considerations
In recent years, online purchasing has carved a significant niche in the drywall market. Websites such as Lowe's online store, Home Depot's website, and other construction materials retailers can provide a convenient option for selections. Concurrently, platforms like Amazon are also creative sources for drywall purchases.
Benefits:
- Convenience: Available for purchase from the comfort of home.
- Variety: Access to various brands and adjustments in thickness or type without some spatial restrictions present in local shops.
- Comparison Shopping: Inputting a few values in a search box allows easy comparisons of multiple options side-by-side.
However, buyers should be cautious about shipping fees and lead times for delivery to ensure they factor in additional costs and scheduling into their overall planning.
Understanding where to buy drywall sheets is essential. It helps set the foundation for satisfying project outcomes and can save time and money in the long term. Searching through various channels requires careful consideration of benefits and potential drawbacks.
Epilogue
The conclusion serves a vital role in any detailed discussion about drywall pricing. It crystallizes the insights from the various sections and highlights the essential factors that influence costs. This article delves deep into the nuances of drywall pricing, which includes state-specific variations, specific product types, and modern trends in the industry.
Summary of Key Pricing Insights
When we analyze pricing for drywall sheets, several factors come into play. Price can be influenced by
- Material Quality: Higher grade materials often command higher prices.
- Type of Drywall: Specialized types like water-resistant or soundproof can bearings added costs.
- Thickness: The thicker the drywall, the higher the expense, which attributes to its durability.
- Transportation and Logistical Factors: The cost to ship sheets can vary significantly and incur additional expenses. The geographic specifics affect these factors, underscoring the local market conditions.
Furthermore, economic factors—both global and regional—exist, influencing the overall pricing. Keeping these insights on pricing in focus helps consumers make distressing decisions about their purchases.
Future Prospects for Drywall Pricing
Looking ahead, the drywall market seems poised for constant evolution. Demand fluctuates with trends in housing and construction. Innovations in manufacturing introduce eco-friendly options, likely affecting market dynamics as owners became more conscientious about their materials. Additionally:
- Potential price spikes could occur due to raw material shortages or increases in demand, suggesting consumers should keep abreast of market trends.
- Regulatory changes may arise at a state level, affecting packaging or material sourcing requirements.
It's fundamentally crucial to understand these upcoming shifts as they will directly set the pace for drywall costs. Being informed means homeowners can adapt, plan, and budget appropriately for their future construction projects. Reading this article equips readers for smarter purchases and optimal satisfaction from their renovations.