Materials:
- Twisted Pair Cable: 500 feet
- Electrical Tape: 3 rolls
- Wire Cutter: 1 piece
- Wire Stripper: 1 piece
- Terminal Blocks: 10 pieces
- Wire Nuts: 15 pieces
DIY Steps:
- Measure and cut the twisted pair cable to required lengths using a wire cutter.
- Strip the insulation from the ends of the cable using a wire stripper.
- Connect the wires to the terminal blocks following the project schematic.
- Use wire nuts to secure the connections.
- Insulate the connections with electrical tape.
Technical Aspects:
- Tools: Wire cutter, wire stripper
- Timing: 2 hours
- Critical Techniques: Proper wire stripping, accurate terminal block connections
DIY Project Process:
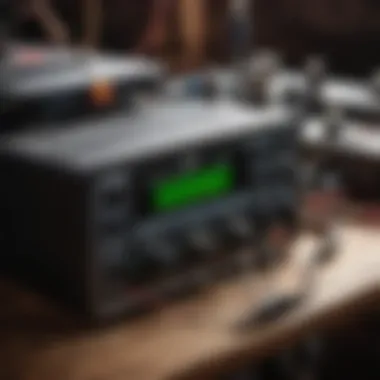
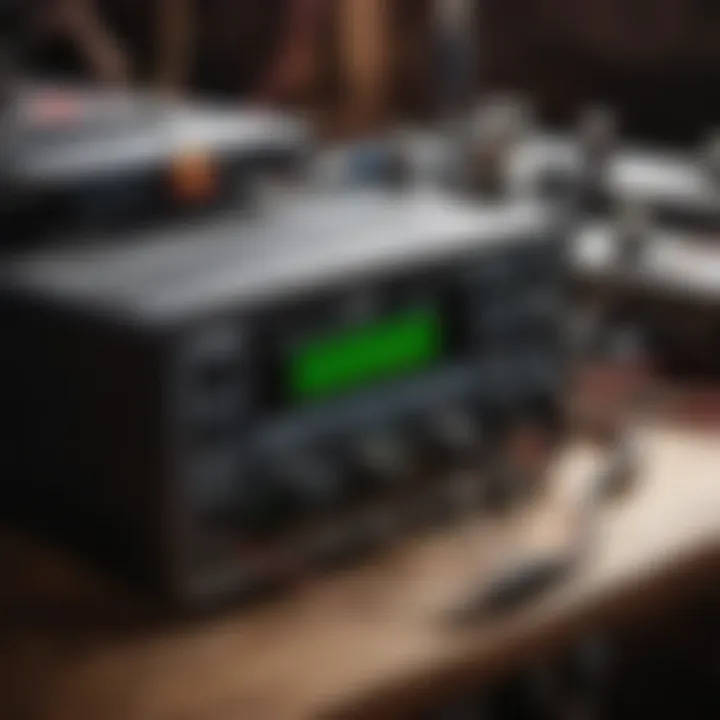
- Start by measuring and cutting the twisted pair cable to the specified lengths.
- Carefully strip the insulation from the cable ends to expose the wires.
- Connect the wires to the terminal blocks according to the project diagram.
- Use wire nuts to fasten the connections securely.
- Wrap electrical tape around the connections for insulation and protection.
- troubleshoot any issues by double-checking wire connections and insulation.
Introduction
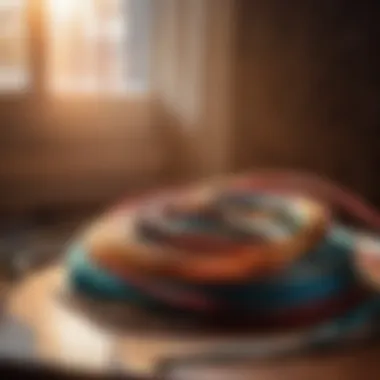
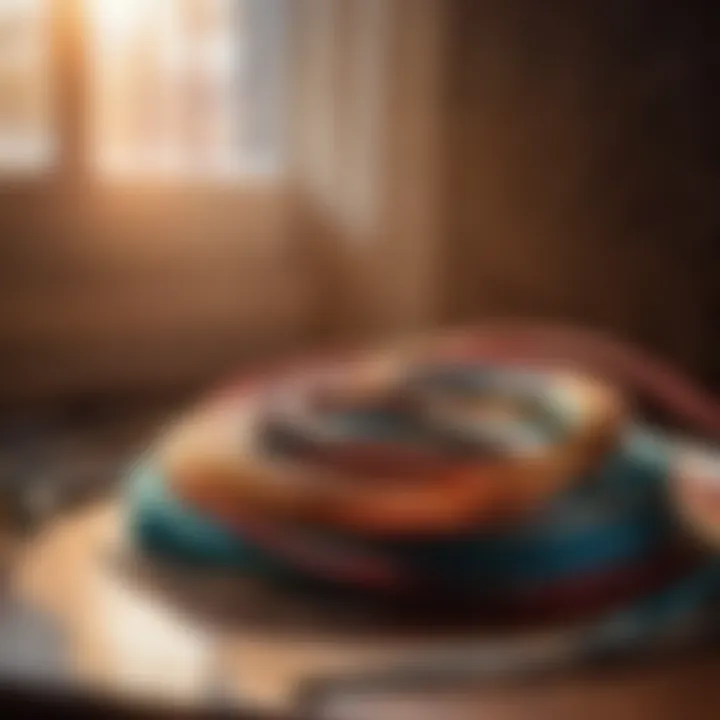
In the realm of electrical work, understanding the intricacies of wire cost is paramount. The backbone of any electrical system, wires are the silent heroes that ensure the smooth flow of electricity throughout our homes, offices, and industrial spaces. This article embarks on a journey to unravel the multifaceted factors that influence the pricing of electrical wires. From the fundamental material composition to the intricate insulation types, every element contributes significantly to the final cost.
Delving deeper, it becomes evident that material composition is a cornerstone in the pricing structure of wires. The choice between copper, aluminum, or copper-clad aluminum wires not only impacts performance but also plays a pivotal role in determining the overall expenses of a project. Copper wires, known for their excellent conductivity and durability, come at a higher price point compared to aluminum wires, which are valued for their lightweight nature. Meanwhile, copper-clad aluminum wires offer a middle-ground solution, balancing cost efficiency with acceptable performance levels.
Going beyond material considerations, wire gauge acts as another critical factor in cost determination. Thicker gauges provide lower electrical resistance but come at a higher price tag, while thinner gauges offer affordability but may compromise on long-term performance. Insulation type further adds a layer of complexity, with options like PVC, THHN, and XLPE insulation influencing both functionality and cost.
By unraveling the layers of material composition, wire gauge, and insulation types, this article aims to equip readers with a comprehensive understanding of the nuances involved in estimating electrical wire costs. Whether planning a residential, commercial, or industrial project, a robust knowledge of these intricacies is crucial in formulating accurate budget projections and ensuring the success of electrical installations.
Factors Affecting Electrical Wire Cost
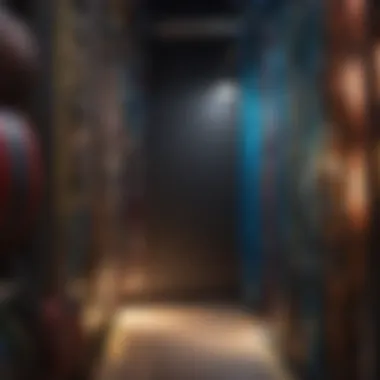
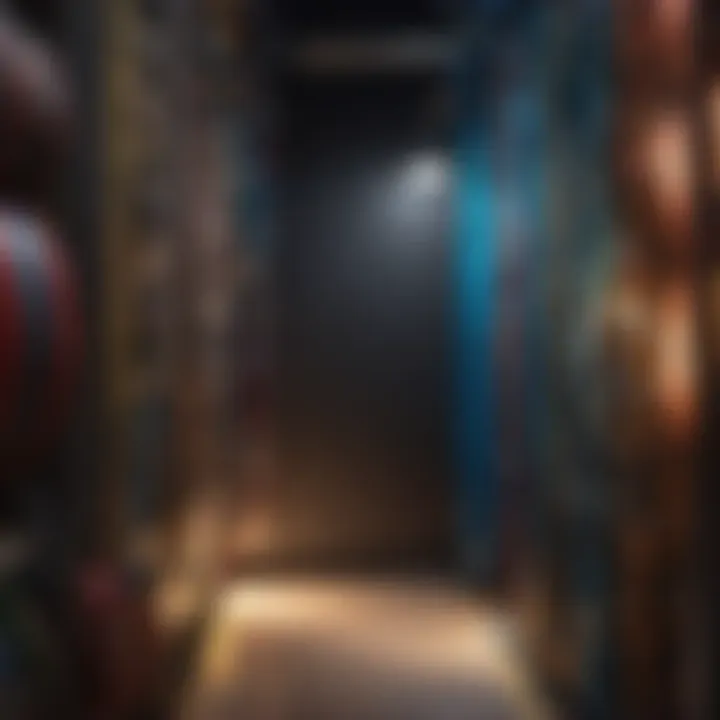
In this section, we unravel the intricate web of factors that significantly impact the cost of electrical wires. Understanding the nuances of these factors is crucial for anyone embarking on a project involving wiring installations. By delving into the material composition, wire gauge, and insulation type, we can unravel the intricacies involved in estimating electrical wire costs.
Material Composition
Copper Wires:
Diving into the realm of copper wires reveals a pivotal aspect of electrical wiring. Copper, known for its superior conductivity and durability, stands prominently in the electrical industry. Its ability to efficiently transmit electricity makes it a popular choice for wiring applications. Although slightly more expensive than aluminum, the benefits of copper, including resistance to corrosion and high tensile strength, outweigh the costs in the long run. Understanding the unique characteristics of copper wires equips individuals with the knowledge to make informed decisions when selecting wiring materials.
Aluminum Wires:
Aluminum wires present a cost-effective alternative to copper, yet they possess lower conductivity and are more prone to oxidation. Despite these drawbacks, the lightweight nature of aluminum makes it an attractive choice for electrical wiring in specific applications where cost considerations play a significant role. By illuminating the distinct features of aluminum wires, individuals can weigh the advantages and disadvantages when making wiring material choices.
Copper-Clad Aluminum Wires:
A hybrid of copper and aluminum, copper-clad aluminum wires combine the conductivity of copper with the lightweight properties of aluminum. This fusion results in a wire that offers adequate conductivity at a reduced cost compared to pure copper. However, considerations must be made regarding potential galvanic corrosion between the copper and aluminum layers. By exploring the intricacies of copper-clad aluminum wires, individuals can determine whether this blend aligns with their project requirements.
Wire Gauge
Thicker Gauges vs. Thinner Gauges:
The selection of wire gauge, whether thicker or thinner, plays a crucial role in determining the cost and performance of electrical wiring systems. Thicker gauges boast lower resistance and are suitable for high-current applications. Conversely, thinner gauges, while cost-effective, may face limitations in handling heavier loads. By evaluating the unique features and trade-offs between thicker and thinner gauges, project planners can make informed decisions that align with their specific requirements.
Insulation Type
PVC Insulation:
Polyvinyl chloride (PVC) insulation offers a versatile solution for electrical wires due to its flexibility and resistance to moisture. Widely used in various applications, PVC insulation ensures optimal safety and protection for wiring systems. Understanding the characteristics of PVC insulation enhances the ability to select suitable wires for diverse projects.
THHN Insulation:
Thermoplastic High Heat-resistant Nylon (THHN) insulation combines heat resistance with durability, making it a go-to choice for many electrical installations. Its robust construction and resistance to abrasion contribute to its popularity in demanding environments. By exploring the unique features of THHN insulation, individuals can appreciate its benefits and applications across different projects.
XLPE Insulation:
Cross-linked polyethylene (XLPE) insulation provides excellent thermal and chemical resistance, making it ideal for outdoor and industrial applications. With high dielectric strength and resistance to environmental factors, XLPE insulation ensures reliable performance in challenging conditions. Understanding the advantages and disadvantages of XLPE insulation enables individuals to make informed choices regarding wire insulation for specific project needs.
Cost Comparison Across Wire Types
Copper Wires vs. Aluminum Wires
Pros and Cons of Each Type
When comparing Copper Wires and Aluminum Wires, it's vital to delve into the Pros and Cons of each type to make an informed choice. Copper Wires are known for their excellent conductivity, making them ideal for high-power applications. However, they tend to be more expensive. On the other hand, Aluminum Wires are more cost-effective but have lower conductivity. Understanding these nuances is crucial in selecting the most suitable option based on project requirements.
Price Discrepancies
Exploring the Price Discrepancies between Copper Wires and Aluminum Wires sheds light on the varying costs associated with each type. While Copper Wires are pricier due to their superior conductivity and reliability, Aluminum Wires offer a more budget-friendly alternative. Balancing cost considerations with performance requirements is key when deciding between these two options, ultimately impacting the overall budget of the electrical project.
Copper Wires vs. Copper-Clad Aluminum Wires
Cost Efficiency Analysis
Comparing Copper Wires with Copper-Clad Aluminum Wires necessitates a thorough Cost Efficiency Analysis to understand the financial implications of each choice. Copper Wires are renowned for their reliability and conductivity, albeit at a higher price point. Conversely, Copper-Clad Aluminum Wires offer a cost-efficient alternative while compromising slightly on performance. Evaluating cost efficiencies is crucial in optimizing project expenses without compromising on quality.
Performance Variations
Examining the Performance Variations between Copper Wires and Copper-Clad Aluminum Wires elucidates the differences in functionality and reliability. While Copper Wires excel in performance and durability, Copper-Clad Aluminum Wires provide a balance between performance and cost-effectiveness. Understanding these nuances is essential in aligning the wire choice with the specific requirements of the electrical project, ensuring optimal performance within budget constraints.
Project Specifics and Wire Cost Estimation
In this section of the article, we delve into the crucial importance of understanding project specifics and wire cost estimation when dealing with electrical wiring projects. The accurate estimation of wire costs is paramount in ensuring that projects stay within budget constraints and are executed efficiently. By meticulously considering various factors such as material selection, project scope, and installation requirements, individuals can make well-informed decisions that impact the overall success of their wiring endeavors.
Residential Projects
Single-Family Homes
Single-family homes represent a significant segment of residential projects where electrical wire cost estimation plays a pivotal role. These dwellings typically require a specific amount and type of wiring to cater to the household's electrical needs adequately. The key characteristic of single-family homes lies in their standalone nature, which necessitates a tailored approach to wiring solutions. Opting for customized wiring configurations in single-family homes enables homeowners to optimize energy usage and enhance overall safety levels within the property. While the unique feature of single-family homes lies in their autonomy, it also poses challenges in terms of potential wiring extensions or renovations that may require expert intervention to ensure compliance and safety.
Multi-Unit Dwellings
In comparison, multi-unit dwellings present a distinct set of considerations regarding wire cost estimation. These properties, encompassing apartment complexes or condominiums, require a comprehensive approach to wiring that accounts for the shared electrical infrastructure among multiple units. The key characteristic of multi-unit dwellings is their collective consumption of electrical resources, leading to the need for efficient wiring layouts that promote both individual unit functionality and building-wide electrical stability. The unique feature of multi-unit dwellings is their emphasis on centralized electrical distribution systems, presenting advantages in terms of simplified maintenance and troubleshooting. However, managing wiring complexities in multi-unit dwellings can pose challenges related to accessibility and scalability for future electrical upgrades or modifications.
Commercial Projects
Office Buildings
Office buildings represent a critical sector where meticulous wire cost estimation directly influences operational efficiency and safety standards. The key characteristic of office buildings lies in their diverse electrical requirements, spanning from lighting and HVAC systems to complex data networks and communication infrastructure. Opting for efficient wiring solutions tailored to office settings is crucial in ensuring uninterrupted business operations and minimizing potential downtime due to electrical issues. The unique feature of office buildings lies in their integration of advanced electrical technologies, offering advantages in terms of energy savings and workspace adaptability. However, the challenges of wire cost estimation in office buildings include addressing varying occupancy rates and fluctuating electrical demands that may necessitate dynamic wiring solutions.
Retail Spaces
Retail spaces represent a dynamic environment where wire cost estimation plays a vital role in supporting the unique electrical needs of businesses. The key characteristic of retail spaces is their consumer-oriented design, requiring tailored lighting and power options to enhance the shopping experience. Opting for strategic wiring layouts in retail settings enables businesses to create visually appealing displays and ensure efficient operational workflows. The unique feature of retail spaces lies in their focus on customer engagement through effective lighting and electrical setups, offering advantages in terms of brand visibility and customer satisfaction. However, challenges in wire cost estimation for retail spaces include balancing aesthetic requirements with energy efficiency standards to create a harmonious retail environment.
Industrial Projects
Manufacturing Facilities
Manufacturing facilities represent a sector where precise wire cost estimation is essential for maintaining production continuity and workplace safety. The key characteristic of manufacturing facilities lies in their high-power electrical demands, driven by machinery, equipment, and production processes that require robust wiring solutions. Opting for dependable wiring configurations in manufacturing settings is crucial in ensuring operational resilience and adherence to industry-specific electrical standards. The unique feature of manufacturing facilities is their reliance on heavy-duty electrical infrastructure, offering advantages in terms of production efficiency and equipment reliability. However, challenges in wire cost estimation for manufacturing facilities stem from intricate machinery interconnections and evolving production layouts that may necessitate adaptable wiring solutions to accommodate future expansions.
Warehouses
Warehouses present a unique context where wire cost estimation influences logistical operations and overall workplace functionality. The key characteristic of warehouses lies in their expansive layouts that necessitate strategic wire routing to cater to lighting, security, and equipment connectivity needs. Opting for streamlined wiring solutions in warehouse environments enables businesses to enhance operational productivity and warehouse safety measures. The unique feature of warehouses lies in their storage-focused electrical requirements, offering advantages in terms of inventory management and space utilization optimization. However, challenges in wire cost estimation for warehouses include addressing fluctuating storage configurations and evolving operational demands that may require agile wiring setups to accommodate dynamic warehouse functionalities.
Installation Factors Impacting Cost
In the realm of electrical wire costs, understanding the installation factors that influence the overall expense is pivotal. The installation phase is where the theoretical planning transitions into practical implementation, making it a crucial juncture in cost determination. Factors such as distance covered, labor costs, and time constraints all play vital roles in shaping the final budget for electrical wiring projects. By delving into the nuances of installation factors, one can gain a more comprehensive understanding of how these elements impact the overall cost structure. It is essential to consider these factors meticulously during the planning stages to ensure a well-executed and cost-effective electrical wiring project.
Distance Covered
Long-Distance Installations
Long-distance installations refer to electrical wiring projects that span considerable distances, requiring extensive wire lengths to connect various points. These installations are characterized by the need for longer wires, which can significantly impact material costs. While long-distance installations may incur higher material expenses due to increased wire lengths, they are often necessary for connecting distant points efficiently. The key advantage of long-distance installations lies in their ability to establish robust electrical connections across expansive areas, serving as a reliable solution for projects demanding widespread electrical coverage. However, the main disadvantage of long-distance installations is the higher material costs associated with acquiring and using longer wires.
Short-Distance Installations
Conversely, short-distance installations encompass electrical wiring projects that involve connecting points within closer proximity. These installations require shorter wire lengths, leading to reduced material costs compared to long-distance counterparts. Short-distance installations are advantageous in scenarios where electrical connections need to be established over shorter distances, optimizing material utilization and minimizing expenses. The unique feature of short-distance installations lies in their cost efficiency and suitability for projects where wire lengths are limited. While short-distance installations offer savings on material costs, they may present challenges in situations that require wiring over extended distances, as multiple segments or connections may be necessary, resulting in additional installation complexity.
Labor Costs
Skilled Labor vs. General Labor
Labor costs constitute a significant portion of the overall expenses in electrical wiring projects, with the choice between skilled and general labor impacting budget considerations. Skilled labor, typically consisting of experienced electricians or specialists, commands higher wages due to their expertise and proficiency in handling complex wiring tasks. Opting for skilled labor ensures precision and adherence to industry standards, reducing the likelihood of errors or rework. On the contrary, general labor, while more cost-effective, may lack the specialized knowledge required for intricate wiring processes, potentially leading to inefficiencies or safety hazards. The primary advantage of skilled labor lies in their proficiency and ability to handle intricate wiring tasks with precision, ensuring high-quality results. However, the disadvantage is the higher hourly rates associated with skilled professionals, which can elevate overall labor expenses.
Time Constraints
Urgent Projects vs. Standard Timelines
Time constraints play a crucial role in determining the cost of electrical wiring projects, especially when distinguishing between urgent projects and those following standard timelines. Urgent projects demand accelerated timelines for completion, often requiring additional resources and manpower to expedite the installation process. While urgent projects prioritize swift implementation, they may incur higher costs due to expedited material procurement and increased labor expenses. In contrast, projects adhering to standard timelines allow for more structured planning and resource allocation, potentially resulting in cost savings through optimized scheduling and utilization of resources. The unique aspect of urgent projects lies in their emphasis on rapid deployment and operational efficiency, catering to time-sensitive requirements. Despite the advantages of meeting urgent project deadlines, the disadvantages include potential cost escalations associated with expedited services and resource mobilization.
Regulatory Requirements and Compliance Costs
In the realm of electrical wire costs, understanding and adhering to regulatory requirements and compliance costs are paramount. The regulations put in place serve as a safeguard to ensure the safety and efficiency of electrical installations. Compliance with these regulations not only protects the residents but also plays a crucial role in avoiding potential hazards and costly issues.
When it comes to construction projects involving electrical works, complying with building codes is non-negotiable. These codes encompass a wide array of guidelines that dictate how electrical systems should be designed, installed, and maintained. Failure to comply with building codes can result in severe consequences, including fines, project delays, and even legal action.
Building Codes
National Regulations
National regulations refer to the overarching standards set by the federal government that aim to unify practices across the country. These regulations ensure that electrical installations meet a certain level of safety and quality. One key characteristic of national regulations is their consistency and applicability across different states, providing a standardized framework for electrical work. While adhering to national regulations may involve some initial costs for compliance, the long-term benefits in terms of safety and legal protection far outweigh the expenses.
Local Codes
On the other hand, local codes focus on regulations specific to a particular region or municipality. These codes may introduce additional requirements or specifications based on local conditions or needs. Local codes are beneficial as they address nuances that national regulations may not cover, ensuring that electrical installations align with specific local requirements. However, the downside of local codes lies in the potential variation in standards from one jurisdiction to another, leading to complexities for contractors operating in multiple areas.
Safety Standards
Safety standards play a vital role in ensuring that electrical installations are safe for occupants and meet industry best practices. Two primary bodies responsible for setting safety standards in the electrical sector are OSHA (Occupational Safety and Health Administration) and NFPA (National Fire Protection Association).
OSHA Guidelines
OSHA guidelines focus on the safety of workers involved in electrical installations. These guidelines outline best practices for ensuring a safe working environment, reducing the risk of accidents and injuries. By following OSHA guidelines, contractors can minimize workplace hazards, maintain worker safety, and avoid costly penalties for non-compliance.
NFPA Requirements
NFPA sets forth requirements aimed at preventing fires and establishing fire protection standards. These requirements cover aspects such as electrical system design, installation methods, and maintenance practices to reduce the risk of fire incidents. Adhering to NFPA requirements not only enhances safety but also contributes to the longevity and reliability of electrical systems, ultimately saving property owners from potential fire-related damages.