Materials:
- Concrete blocks: 500 pieces (measuring 8 inches by 8 inches by 16 inches)
- Cement: 10 bags (each weighing 50 pounds)
- Sand: 2 cubic yards
- Gravel: 3 cubic yards
- Mortar mix: 5 bags
- Reinforcing steel bars: 100 pieces (each measuring 0.5 inches by 3 feet)
DIY Steps:
- Site Preparation: Begin by clearing the construction area and leveling the ground to ensure a sturdy foundation for the project.
- Foundation Setting: Dig trenches for the footings, establish proper dimensions according to the building plan, and pour concrete to create a solid foundation.
- Block Layout: Mark the layout of the walls using strings and stakes, ensuring accurate placement and alignment of the concrete blocks.
- Block Installation: Apply mortar on the footing, lay the first layer of blocks, level each block using a spirit level, and continue stacking blocks with proper mortar application between each layer.
- Reinforcement Placement: Integrate reinforcing steel bars within the block walls at designated intervals for added structural strength.
- Wall Finishing: Apply a final layer of mortar on the top course of blocks for a polished finish.
Technical Aspects:
- Tools Required: Shovel, wheelbarrow, trowel, level, hammer, safety goggles, gloves, tape measure
- Timing Specifics: Plan for a continuous work schedule to maintain efficiency and avoid interruptions
- Critical Techniques: Proper mortar mixing consistency, accurate block placement, careful leveling to ensure a uniform structure
DIY Project Process:
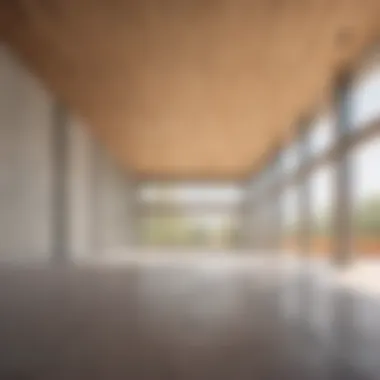
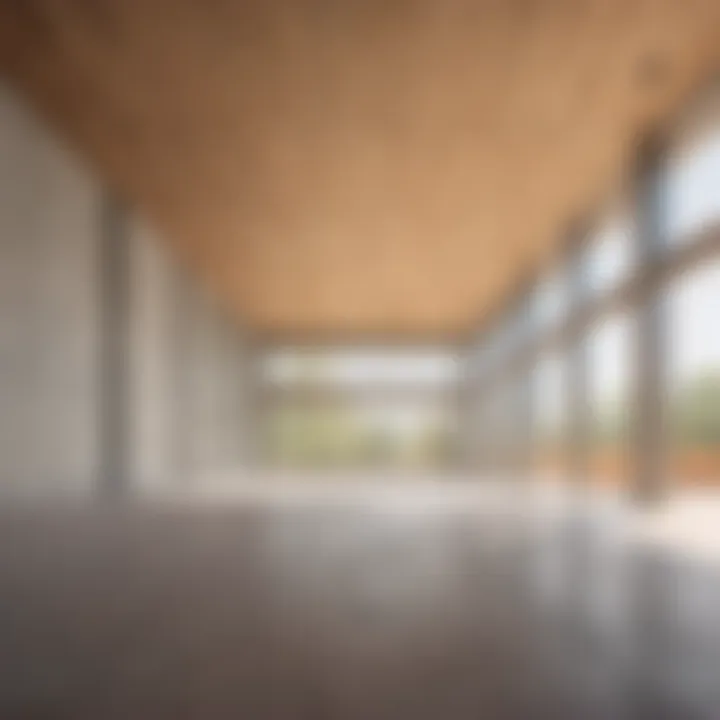
- Sequential Steps: Follow the block laying sequence systematically, ensuring each block is securely positioned and aligned for a professional finish
- Troubleshooting Tips: In case of uneven blocks, adjust the level and apply additional mortar for correction; for mortar setting too quickly, mix in small batches to maintain workability
Introduction
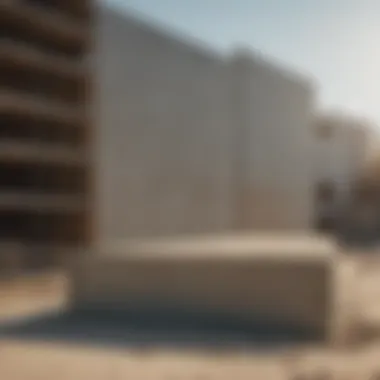
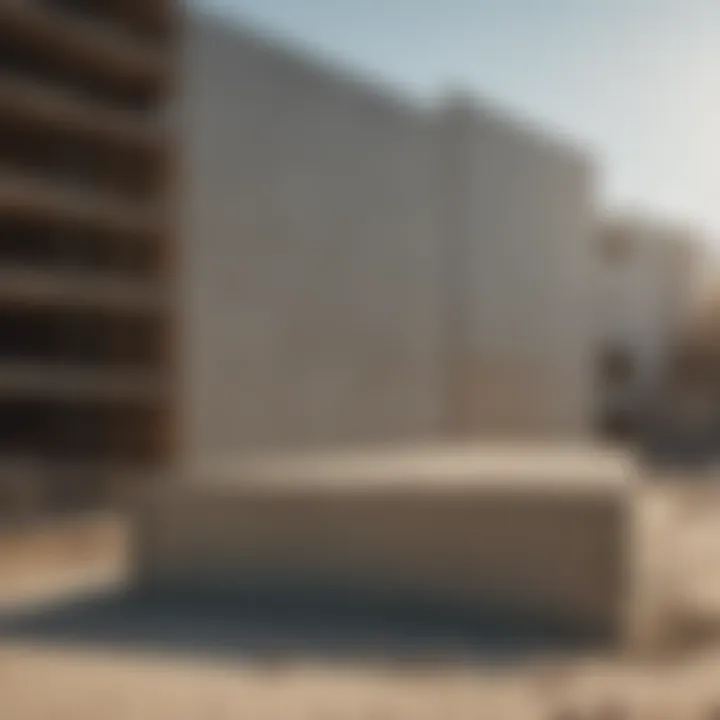
In the realm of construction, exploring the costs associated with concrete block building is of paramount importance. This article delves into the intricate details and factors that influence the financial aspects of such projects. Considerations span from the types of materials needed to the labor-intensive processes involved. Understanding the nuances of cost estimation and budgeting in this context is key to the success of any construction endeavor. By comprehensively analyzing the expenses tied to concrete block building, individuals can make informed decisions, streamline operations, and ensure efficient project execution.
Overview of Concrete Block Buildings
The foundation of any construction project starts with the choice of building materials. Concrete block buildings have long been favored for their durability, strength, and versatility in creating structurally sound edifices. These blocks, made from a mixture of cement, aggregates, and water, provide a robust base for various types of structures. The interlocking design of concrete blocks offers exceptional resilience against elements and structural stability. Exploring the features and benefits of concrete block buildings showcases why they remain a preferred option in the construction industry.
Significance of Estimating Building Costs
Accurately estimating building costs is a linchpin of project management in construction. The process involves evaluating material expenses, labor costs, equipment requirements, and site preparation expenditures. Proper cost estimation enables stakeholders to set realistic budgets, allocate resources effectively, and mitigate financial risks. Understanding the significance of this meticulous approach can prevent project delays, cost overruns, and quality compromises. Estimating building costs isn't just about numbers; it's about strategic planning, foresight, and ensuring the successful completion of construction projects.
Factors Affecting Costs
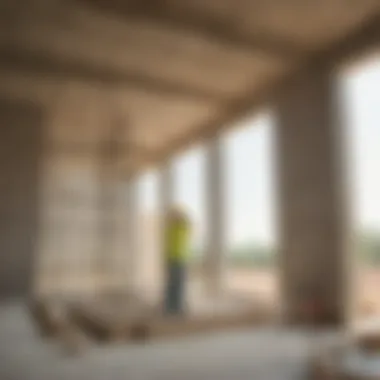
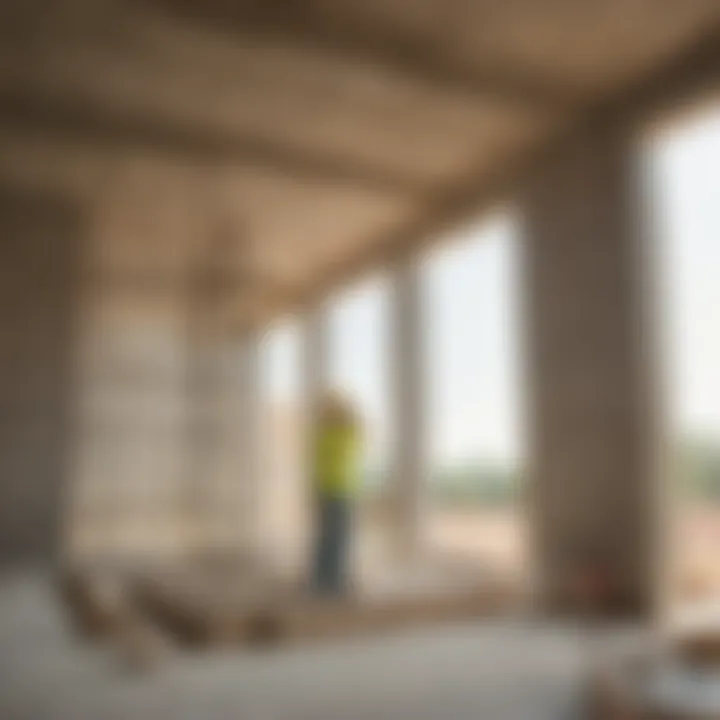
In the realm of concrete block building construction, understanding the factors influencing costs is paramount to successful project management and budgeting. These factors span across various categories, each playing a crucial role in determining the overall expenses involved in a construction project. By delving deep into the intricacies of material costs, labor expenses, equipment and machinery requirements, and site preparation costs, stakeholders can make informed decisions that impact the project's financial viability.
Material Costs
Types of Concrete Blocks
When it comes to material costs in concrete block construction, the choice of concrete blocks holds significant weight in determining the budget allocation. Various types of concrete blocks are available in the market, ranging from solid to hollow blocks, each offering distinct advantages and characteristics. Solid blocks provide robust structural support, ideal for load-bearing walls, while hollow blocks offer lighter weight and better insulation properties. Selecting the appropriate type of concrete block is crucial in balancing cost-effectiveness with structural requirements, ensuring optimal performance throughout the building's lifespan.
Cement and Aggregates
Cement and aggregates serve as the backbone of concrete production, directly impacting the quality and durability of construction projects. The correct ratio of cement to aggregates is essential for achieving the desired strength and integrity in concrete structures. While cement provides binding properties, aggregates add strength and stability. Understanding the properties of different types of cement and aggregates is key to optimizing material costs without compromising structural integrity.
Reinforcement Materials
Incorporating reinforcement materials such as steel bars or mesh into concrete blocks enhances their tensile strength and resistance to structural loads. Reinforcement materials play a critical role in mitigating cracks and improving the overall durability of concrete block buildings. By carefully selecting and incorporating the appropriate reinforcement materials, construction professionals can elevate the structural integrity of the building while managing costs effectively.
Labor Expenses
Skilled vs. Unskilled Labor
The choice between skilled and unskilled labor directly influences labor expenses in concrete block building construction. Skilled labor offers expertise and efficiency in executing complex construction tasks, ensuring precision and quality in the final output. On the other hand, utilizing unskilled labor may present cost-saving opportunities but could compromise the construction quality and timeline. Balancing the allocation of skilled and unskilled labor is crucial in optimizing labor expenses while maintaining construction standards.
Labor Hours Required
Estimating the labor hours required for a construction project is essential for budget planning and resource allocation. Calculating labor hours accurately enables project managers to optimize workforce utilization and mitigate potential delays or cost overruns. By leveraging historical data and project-specific parameters, construction teams can streamline labor requirements and enhance productivity, contributing to cost-efficient project execution.
Union vs. Non-Union Labor
Choosing between union and non-union labor involves complex considerations related to wages, regulations, and work dynamics. Union labor often commands higher wages but comes with established work standards and benefits, ensuring workforce stability and compliance. On the contrary, non-union labor may offer flexibility in labor costs but could introduce uncertainties in project timelines and quality standards. Selecting the appropriate labor type involves evaluating cost implications alongside regulatory compliance and project requirements.
Equipment and Machinery
Cost of Construction Machinery
The procurement and utilization of construction machinery directly impact project costs and efficiency in concrete block building construction. Investing in high-quality construction machinery offers enhanced productivity and precision in construction operations. However, the initial capital outlay for purchasing machinery must be weighed against the project's scope and duration to optimize cost-effectiveness. Utilizing cost-effective machinery solutions tailored to project requirements ensures smooth workflow and timely project completion.
Rental vs. Purchase Costs
Choosing between renting and purchasing construction equipment involves assessing short-term requirements and long-term cost implications. Renting equipment provides flexibility in project-specific needs without the burden of ownership costs. Conversely, purchasing equipment may yield long-term cost savings for frequent usage projects. Selecting the optimal approach, whether rental or purchase, hinges on evaluating the project duration, frequency of equipment use, and long-term financial considerations, aligning with the project's overarching cost strategies.
Site Preparation Costs
Excavation and Clearing
Site preparation costs encompass activities such as excavation and clearing, laying the groundwork for successful construction. Excavation involves the removal of soil and debris to prepare the site for foundation work, ensuring a stable building platform. Clearing the site of obstacles and vegetation is essential for creating a conducive environment for construction activities. Efficiently managing excavation and clearing tasks is integral to cost-effective project execution and timely commencement of construction activities.
Foundation Work
The foundation serves as the building's structural base, supporting the entire edifice and transmitting loads to the ground. Foundation work involves excavating, compacting, and constructing the foundation to withstand structural stresses and ensure stability. Choosing the appropriate foundation type and construction method is vital in balancing cost considerations with structural requirements. Effective coordination of foundation work minimizes delays, prevents structural issues, and optimizes construction costs for concrete block building projects.
Budgeting and Cost Estimation
Budgeting and cost estimation are crucial aspects of construction projects using concrete blocks. Planning and managing the financial aspects from the outset can significantly impact the project's success. By focusing on specific elements like material expenses, labor costs, and contingency funds, builders can ensure financial stability throughout the construction process.
Cost Breakdown Analysis
Detailed Cost Categories
Detailed cost categories play a vital role in accurately estimating and monitoring expenses in concrete block building construction. These categories encompass various aspects such as materials, labor, equipment, and other specific costs associated with the project. Understanding and categorizing expenses enable project managers to allocate resources efficiently and track expenditure meticulously. The detailed cost categories provide a transparent breakdown of where funds are allocated, aiding in budget control and decision-making. This comprehensive breakdown is essential for identifying cost-saving opportunities and ensuring an organized financial structure within the project.
Allocating Contingency Funds
Allocating contingency funds is a critical strategy in mitigating unforeseen circumstances and managing risks during construction projects. Setting aside a portion of the budget for unexpected expenses or fluctuations in material or labor costs helps safeguard the overall financial health of the project. Contingency funds provide a financial buffer, minimizing the impact of uncertainties and enhancing the project's financial resilience. While contingency funds add an extra layer of preparedness, excessive allocation can affect the project's profitability. Therefore, a balanced approach to allocating contingency funds is essential to maintaining financial efficiency and project continuity.
Professional Consultation
Professional consultation in the form of engaging architects, engineers, and quantity surveyors brings expert insight and specialized knowledge to the construction project. Collaborating with professionals in the field ensures high-quality design, structura
Efficiency Measures and Cost-Saving Strategies
Efficiency measures and cost-saving strategies play a crucial role in optimizing the costs associated with constructing buildings using concrete blocks. By focusing on specific elements such as material usage and labor efficiency, construction projects can achieve significant savings while maintaining quality standards. One key benefit of implementing these strategies is the ability to adhere to budgetary constraints without compromising the structural integrity of the building. Therefore, understanding and applying efficiency measures and cost-saving strategies are essential for successful and cost-effective construction projects.
Optimizing Material Usage
Minimizing Wastage
Minimizing wastage is a fundamental aspect of optimizing material usage in concrete block building construction. This approach involves carefully managing resources to reduce unnecessary material losses during the construction process. By minimizing wastage, construction teams can maximize the utilization of materials, lower expenses, and minimize environmental impact. The key characteristic of this practice lies in its ability to enhance cost-effectiveness by ensuring that materials are used efficiently and responsibly. While minimizing wastage requires meticulous planning and careful execution, its benefits in terms of cost savings and sustainability make it a popular choice for construction projects focusing on efficiency and resource optimization.
Bulk Purchasing Benefits
Bulk purchasing benefits play a significant role in optimizing material usage and overall project costs. By procuring materials in large quantities, construction stakeholders can capitalize on lower unit costs and discounts offered by suppliers. This approach not only reduces the cost per unit but also streamlines the procurement process, leading to savings in both time and money. One key characteristic of bulk purchasing benefits is their potential to generate substantial cost savings over the project's duration. Despite the advantages of bulk purchasing, considerations such as storage space requirements and material lifespan should be taken into account to ensure optimal outcomes for the construction project.
Streamlining Construction Processes
Lean Construction Principles
Implementing lean construction principles can significantly contribute to the efficiency and cost-effectiveness of concrete block building projects. These principles focus on eliminating waste, enhancing productivity, and improving overall project outcomes through continuous improvement and value maximization. A key characteristic of lean construction is its emphasis on delivering maximum value to the client while minimizing resources and time allocated to non-value-adding activities. By embracing lean construction principles, project teams can optimize processes, reduce delays, and enhance project quality, making it a beneficial choice for endeavors seeking to maximize efficiency and minimize costs.
Just-In-Time Delivery
Just-In-Time (JIT) delivery methodology is an essential aspect of streamlining construction processes in concrete block building projects. JIT delivery involves coordinating material arrivals precisely when they are needed, reducing inventory costs, and streamlining on-site logistics. The key characteristic of JIT delivery lies in its ability to minimize storage costs, improve project timelines, and increase overall project efficiency. While JIT delivery offers advantages such as reduced inventory holding costs and improved project scheduling, factors like transportation risks and supply chain disruptions should be carefully managed to ensure smooth project operations.
Energy-Efficient Design Considerations
Insulation and Thermal Performance
Insulation and thermal performance considerations are vital for enhancing energy efficiency in concrete block buildings. By selecting appropriate insulation materials and optimizing thermal performance through design choices, construction projects can reduce energy consumption, lower heating and cooling costs, and create a more comfortable indoor environment. The key characteristic of insulation and thermal performance solutions is their ability to provide long-term energy savings and environmentally friendly construction outcomes. Despite their advantages, challenges such as initial costs and material selection complexities need to be addressed to maximize the benefits of insulation and thermal performance solutions.
Sustainable Building Practices
Incorporating sustainable building practices can significantly contribute to the energy efficiency and environmental sustainability of concrete block building projects. These practices involve utilizing eco-friendly materials, implementing energy-efficient systems, and adhering to green building standards to reduce the project's environmental footprint. The key characteristic of sustainable building practices is their potential to create healthier indoor environments, lower operating costs, and enhance the overall value of the building. While sustainable practices offer numerous benefits, challenges such as higher upfront costs and specialized construction expertise should be considered to ensure successful integration into concrete block building projects.
Case Studies and Real-World Examples
In examining the costs of concrete block building construction, the inclusion of case studies and real-world examples serves as a pivotal component in providing practical insights and tangible illustrations of the concepts discussed throughout the article. These case studies offer a glimpse into actual construction projects, showcasing the application of various cost-saving strategies, efficient measures, and innovative techniques in real-life scenarios. By delving into these concrete examples, readers can extrapolate valuable lessons and best practices that can inform their own construction endeavors. Additionally, real-world examples serve to contextualize the theoretical aspects of cost exploration, bridging the gap between abstract concepts and tangible outcomes.
Residential Building Projects
Single-Family Homes
Multi-Unit Dwellings
In contrast to single-family homes, multi-unit dwellings encompass structures that accommodate multiple households within a single building. These dwellings include apartment complexes, townhouses, and condominiums, among others, fostering a sense of community living and shared amenities. Within the purview of cost exploration in concrete block building construction, multi-unit dwellings present economies of scale and potential savings in infrastructure and land utilization. The key characteristic of multi-unit dwellings lies in their efficient use of space and centralized resources, affording residents the benefits of shared maintenance and facilities. While optimizing construction costs through volume discounts and shared services, multi-unit dwellings also entail complexities in management and communal decision-making that need to be carefully considered in the cost estimation process.
Future Trends and Innovations
In the realm of concrete block building construction, staying abreast of future trends and innovations is paramount to driving advancements and enhancing efficiencies in the industry. This article recognizes the significance of discussing future trends and innovations, as they play a pivotal role in shaping the trajectory of construction practices. By exploring upcoming developments, stakeholders can adapt to changing landscapes and embrace strategies that promote sustainable growth and technological evolution.
Advancements in Building Materials
The evolution of building materials holds substantial importance in revolutionizing the construction sector. As technology progresses, new materials are being introduced to improve durability, sustainability, and efficiency in concrete block construction. From high-performance concrete blends to eco-friendly additives, advancements in building materials are enhancing the quality and resilience of structures. Architects and builders are increasingly incorporating these innovative materials into their designs to achieve greater structural integrity and longevity.
Smart Technologies in Construction
The integration of smart technologies in construction is revolutionizing how concrete block buildings are designed, constructed, and managed. From Building Information Modeling (BIM) software to drones for site surveys, these technologies streamline processes, promote collaboration, and enhance project outcomes. Smart sensors and IoT devices enable real-time monitoring of construction progress, ensuring adherence to timelines and budgets. Embracing smart technologies not only improves efficiency but also facilitates data-driven decision-making, leading to optimized project delivery and enhanced client satisfaction.
Conclusion
In delving into the realm of exploring the costs associated with concrete block building construction, it becomes evident that a thorough understanding of the financial aspects of such projects is paramount. The conclusion drawn from this detailed analysis is multifaceted, shedding light on various crucial elements that impact budgeting and decision-making in construction projects involving concrete blocks. One key aspect that stands out is the significance of accurate cost estimation, which serves as the foundation for successful project execution. By meticulously dissecting material expenses, labor costs, and other intricacies involved, stakeholders can gain valuable insights that enable them to make informed financial decisions.
Additionally, the conclusion emphasizes the importance of incorporating contingency funds into the budgeting process. Unforeseen circumstances and price fluctuations in materials or labor underline the necessity of having a buffer to mitigate potential financial risks. This proactive approach can help prevent budget overruns and ensure smooth progress throughout the construction phase. Moreover, evaluating the efficiency measures and cost-saving strategies discussed earlier can further optimize expenses and enhance the overall project outcome. By implementing strategies such as minimizing material wastage, streamlining construction processes, and considering energy-efficient design principles, stakeholders can achieve cost-effectiveness while maintaining quality standards.
Ultimately, the conclusion encapsulates the essence of meticulous planning, strategic decision-making, and prudent financial management as key pillars in the realm of concrete block building construction. By embracing these principles and leveraging the insights provided in this article, project stakeholders can navigate the complexities of cost estimation with confidence and tact, leading to successful project outcomes and sustainable construction practices.
Key Takeaways
- Cost estimation is a critical aspect of concrete block building construction, providing a foundational framework for budgeting and decision-making processes.
- Incorporating contingency funds is essential to account for unforeseen expenses and ensure financial stability throughout the project lifecycle.
- Efficiency measures such as optimizing material usage, streamlining construction processes, and embracing energy-efficient design considerations can contribute significantly to cost savings and project success.