Materials:
When it comes to calculating concrete cost per square foot, the first step is gathering all the necessary materials. To ensure accurate estimations, you will need:
- Concrete mix: Specify the brand and type of concrete mix suitable for your project, ensuring it meets required standards.
- Measuring tools: Include a tape measure, level, and chalk to outline the area for concrete placement accurately.
- Calculator: A calculator is essential for precise calculations to determine the exact amount of concrete needed.
- Protective gear: Safety is paramount, so make sure to have gloves, goggles, and a mask to protect yourself during the concrete mixing and pouring process.
- Reinforcement material: Depending on the project scope, reinforcement like rebar or mesh may be necessary to enhance concrete strength.
DIY Steps:
With the materials in hand, proceed to calculating the concrete cost per square foot with these step-by-step instructions:
- Measure the area: Use the measuring tools to accurately determine the dimensions of the concrete pour area, calculating the square footage.
- Calculate concrete quantity: Utilize the calculator to determine the amount of concrete needed based on the area's measurements and desired thickness.
- Consider mixing materials: Factor in the cost of mixing equipment or ready-mix concrete services if required, ensuring all expenses are accounted for.
Technical Aspects:
To enhance the accuracy of your calculations and ensure a successful concrete project, consider the following technical aspects:
- Tools: Have a wheelbarrow, shovel, and trowel ready for mixing and pouring concrete.
- Timing specifics: Understand the setting time of the concrete mix used to plan the pouring and finishing process effectively.
- Critical techniques: Learn proper concrete mixing ratios and pouring techniques to achieve a durable and aesthetically pleasing result.
- Uniqueness: Explore decorative concrete options or staining techniques to add a personalized touch to your project.
DIY Project Process:
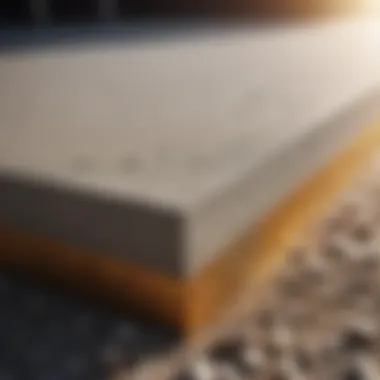
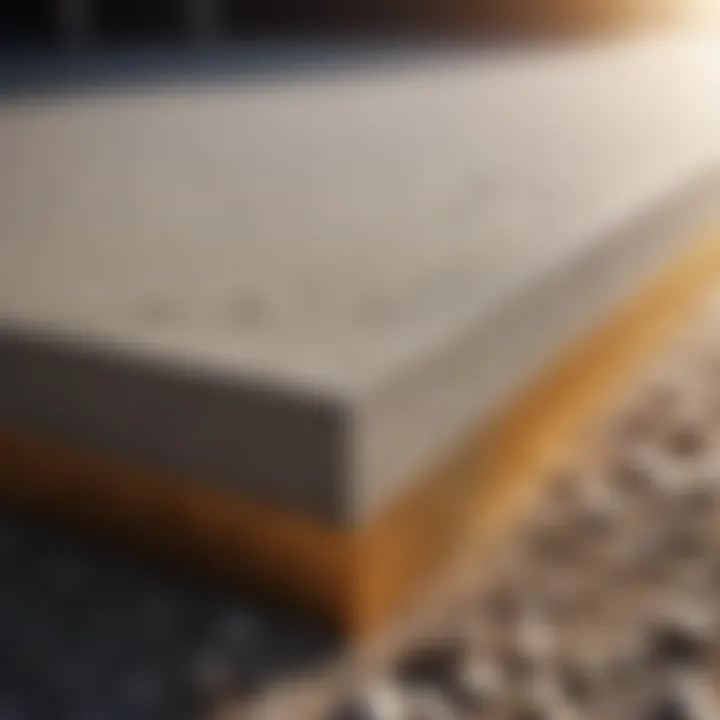
As you delve into the project, follow these sequential steps for a successful concrete cost calculation and pouring process:
- Mixing instructions: Follow the concrete mix manufacturer's instructions carefully, maintaining proper water-to-concrete ratios for optimal results.
- Pouring technique: Level and smooth the concrete surface evenly, ensuring no air pockets or inconsistencies that could affect the final cost per square foot.
- Troubleshooting: In case of cracks or uneven surfaces, learn proper repair techniques and consider factors that may impact future durability.
By meticulously preparing with the right materials, following detailed steps, understanding technical aspects, and implementing troubleshooting tips, you can calculate concrete cost per square foot accurately and achieve a successful DIY project.
Factors Affecting Concrete Cost
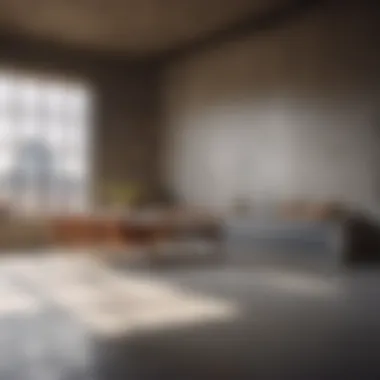
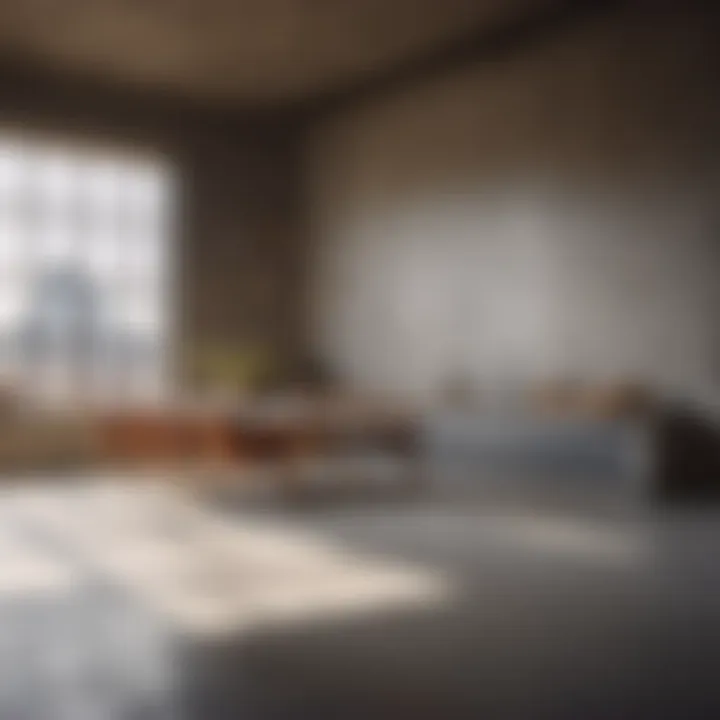
Understanding the various factors influencing concrete costs is crucial when planning any construction project. In this comprehensive guide, we delve into the intricate details that impact the overall expenses. By examining material costs, labor costs, equipment costs, and project specifics, we equip readers with in-depth knowledge to make informed decisions regarding concrete expenses.
Material Costs
When it comes to material costs, several key aspects play a significant role in determining the overall expenditure of a concrete project. Types of concrete, cement quality, aggregates, and admixtures are all vital components that influence pricing. Each material choice has distinct characteristics that contribute to the overall quality and durability of the concrete structure.
Types of Concrete
Different types of concrete offer various strengths and compositions tailored for specific project requirements. For example, high-performance concrete is known for its exceptional durability and strength, making it a popular choice for heavy-duty applications. On the other hand, lightweight concrete is favored for its reduced density, enhancing ease of handling and transportation. Understanding the unique features of each type of concrete enables project planners to select the most suitable option based on construction needs and budget constraints.
Cement Quality
The quality of cement used in a concrete mix directly impacts the structural integrity and longevity of the project. High-grade cement ensures optimal bond strength and reduces the risk of cracks or deterioration over time. By prioritizing cement quality, contractors and homeowners can enhance the overall quality of their concrete structures, promoting longevity and structural stability.
Aggregates
Aggregates, such as sand, gravel, or crushed stone, are essential components in concrete production. The choice of aggregates affects the workability, strength, and durability of the concrete mix. Selecting the right mix of aggregates based on project requirements and environmental conditions is critical to achieving the desired concrete quality and performance.
Admixtures
Admixtures are additional substances added to the concrete mix to alter its properties and enhance performance. From improving workability and durability to reducing water requirements, admixtures offer a range of benefits depending on the project's needs. Incorporating suitable admixtures can increase the efficiency and quality of the concrete mix, resulting in a more robust and cost-effective construction outcome.
Labor Costs
Labor costs comprise a significant portion of concrete expenses. The choice between skilled and unskilled labor, labor availability, and the utilization of union or non-union labor all impact budget allocation and project timelines. Understanding the advantages and disadvantages of each labor category is vital for optimizing costs and ensuring timely project completion.
Equipment Costs
Equipment costs play a crucial role in concrete construction, affecting both project efficiency and overall expenses. Concrete mixers, compactors, and finishing tools are essential equipment items that contribute to project success. The quality and efficiency of equipment directly influence the speed and quality of construction tasks, highlighting the importance of selecting the right tools for each project phase.
Project Specifics
Project specifics, such as size, site accessibility, and weather conditions, are key considerations that directly affect concrete costs. The scale of the project, ease of site access, and environmental factors all influence material and labor requirements. By meticulously evaluating these project aspects, planners can accurately estimate costs and mitigate potential challenges that may arise during construction.
Calculating Concrete Cost
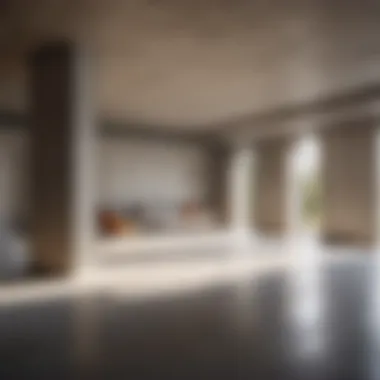
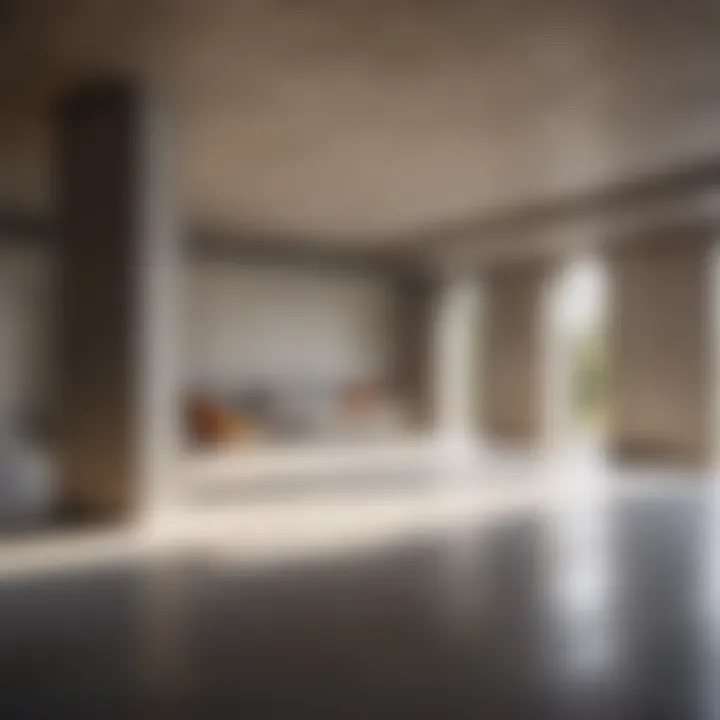
In the realm of construction projects, particularly ones involving concrete work, calculating the cost involved is of utmost importance. This section aims to shed light on the intricacies of determining the financial aspects of a concrete project. Emphasizing the significance of accurate cost calculation, this guide equips readers with essential knowledge to navigate the financial aspect of their construction endeavors. By understanding the nuances of costing, individuals can make informed decisions, avoid budget discrepancies, and ensure the smooth progress of their projects.
Determining Volume of Concrete Needed
Area Calculation
Area calculation is a fundamental aspect of determining the volume of concrete needed for a project. By accurately calculating the area to be covered by concrete, project managers can avoid under or overestimating material requirements, leading to cost savings and efficient resource allocation. The key characteristic of area calculation lies in its precision, as even minor miscalculations can have significant cost implications. Utilizing advanced measuring tools and techniques can enhance the accuracy of area calculations, making it a pivotal step in the concrete cost estimation process.
Thickness Calculation
Thickness calculation plays a crucial role in determining the volume of concrete required for a project. This calculation involves evaluating the thickness of the concrete layer to be poured, taking into account factors such as load-bearing capacity, structural integrity, and durability requirements. The key characteristic of thickness calculation is its direct influence on material costs, as thicker concrete layers necessitate higher material quantities. While thicker concrete offers enhanced strength, it also escalates expenses, making it essential for project managers to strike a balance between structural needs and budget constraints when determining thickness.
Estimating Material Costs
Price per Cubic Yard
The price per cubic yard is a significant factor in estimating material costs for a concrete project. This metric indicates the cost of one cubic yard of concrete, serving as a foundation for calculating the total material expenses. Understanding the price per cubic yard enables project stakeholders to make accurate budget projections, negotiate favorable deals with suppliers, and optimize material procurement strategies. The unique feature of this metric lies in its direct correlation to overall project costs, making it an indispensable component of concrete cost estimation.
Concrete Mix Design
Concrete mix design is a critical element in estimating material costs, as it defines the proportions of various constituents in the concrete mix. By customizing the mix design based on project requirements and performance criteria, project managers can control material expenses while ensuring the desired strength and durability of the concrete structure. The unique feature of concrete mix design is its versatility, allowing for tailored solutions that align with specific project needs. Balancing cost considerations with performance objectives, selecting the optimal mix design is key to optimizing material costs in concrete projects.
Incorporating Labor and Equipment Costs
Labor Hourly Rates
Labor hourly rates significantly impact the overall cost of a concrete project, as labor expenses constitute a substantial portion of the total budget. Understanding labor hourly rates involves assessing the wages of skilled and unskilled labor, considering factors such as experience, specialized skills, and project complexity. The key characteristic of labor hourly rates is their direct influence on project profitability, as efficient labor management can contribute to cost savings and timely project completion. By analyzing and optimizing labor expenses, project stakeholders can enhance budget efficiency and resource utilization.
Equipment Rental Rates
Equipment rental rates play a vital role in concrete cost estimation, particularly for projects requiring specialized machinery and tools. By evaluating the rental rates for equipment such as concrete mixers, compactors, and finishing tools, project managers can accurately project equipment expenses and incorporate them into the overall budget. The unique feature of equipment rental rates lies in their flexibility, allowing project stakeholders to choose cost-effective rental options based on project duration and equipment requirements. By leveraging competitive rental rates and optimizing equipment usage, project managers can streamline costs and maximize project efficiency.
Factoring in Overheads and Contingencies
Overhead Percentage
The overhead percentage constitutes indirect costs incurred during a concrete project, including administrative expenses, utilities, and supervision fees. Factoring in the overhead percentage is essential for comprehensive cost estimation, as it accounts for miscellaneous expenses beyond direct material and labor costs. The key characteristic of overhead percentage is its impact on project feasibility, as inaccurate overhead calculations can lead to budget overruns and financial challenges. By meticulously calculating and allocating overhead costs, project managers can ensure financial transparency and adherence to budgetary constraints.
Contingency Funds
Contingency funds serve as a buffer against unforeseen circumstances and project uncertainties, providing financial insulation for unexpected expenses or variations in project scope. The unique feature of contingency funds lies in their risk mitigation function, offering project stakeholders a financial safety net to address challenges without compromising project progress. Establishing contingency funds based on realistic risk assessments and industry benchmarks is crucial for prudent financial management in concrete projects. By allocating contingency funds wisely and proactively, project managers can safeguard project viability and mitigate financial risks effectively.
Comparing Quotes and Finalizing Costs
In the realm of calculating concrete cost per square foot, the stage of comparing quotes and finalizing costs plays a pivotal role. It serves as the culmination of meticulous planning and evaluation, where decisions are honed to precision. One of the primary benefits of this step is the ability to gain a comprehensive overview of the financial aspects of the project. By scrutinizing quotes from different contractors, individuals equip themselves with the necessary information to make informed choices. This comparison not only leads to potential cost savings but also ensures that the selected contractor aligns with the project's requirements and budget constraints.
From a strategic standpoint, comparing quotes aids in identifying discrepancies and inconsistencies in pricing structures. It allows for a detailed examination of the services, materials, and labor included in each quote, facilitating a transparent understanding of the proposed costs. Moreover, this process fosters a sense of competitiveness among contractors, compelling them to offer their most competitive rates and services to secure the project. By engaging in quote comparisons, individuals can negotiate effectively, ultimately leading to optimal cost-efficiency.
The process of finalizing costs brings a sense of closure to the intricate web of budgeting and estimation. It involves synthesizing all gathered information, negotiating terms, and reaching a mutual agreement with the chosen contractor. This formalization of costs marks a significant milestone in the project timeline, paving the way for concrete actions to commence. Overall, comparing quotes and finalizing costs are indispensable components of the concrete cost estimation process, providing clarity, control, and confidence to individuals embarking on construction endeavors.
Requesting Quotes from Contractors
Detailed Quote Analysis:
The key aspect of detailed quote analysis lies in its ability to dissect and evaluate the intricacies of each contractor's proposal. This analytical process involves a meticulous examination of the scope of work, pricing breakdown, timelines, and any additional services offered by the contractor. A detailed quote analysis serves as the foundation for decision-making, offering insights into the cost components and deliverables associated with each quote.
One of the primary benefits of detailed quote analysis is its capability to reveal hidden costs and discrepancies that may not be immediately apparent. By delving deep into the specifics of each quote, individuals can identify any ambiguities or exclusions that could impact the overall project budget. This thorough evaluation empowers individuals to make informed comparisons and select a contractor whose quote aligns most closely with their expectations and requirements.
Clarifying Inclusions and Exclusions:
When it comes to clarifying inclusions and exclusions, the focus shifts towards elucidating the scope of services covered within the quoted price and those that may incur additional charges. This aspect plays a crucial role in preventing misunderstandings and disputes during the project execution phase. By clearly defining what is included in the contract and what falls outside its purview, both parties can establish mutual understanding and avoid unwarranted financial surprises.
The key characteristic of clarifying inclusions and exclusions lies in its ability to set transparent boundaries and expectations. It enables individuals to ascertain the comprehensiveness of the contractor's offering and determine whether any essential services are omitted from the contract. By addressing potential ambiguities upfront, parties can mitigate risks and ensure a smoother contractual process, thereby enhancing project outcomes and minimizing budgetary discrepancies.
Conclusion
In the realm of calculating concrete cost per square foot, the conclusion serves as a pivotal stage in ensuring the accuracy and success of the overall estimation process. It is essential to understand that the conclusion encapsulates the culmination of all preceding steps and factors discussed in this guide. By delving into the conclusion, individuals can ascertain the precision of their cost estimations and make informed decisions for their projects.
One of the critical elements of the conclusion is the emphasis on regular updates to cost estimates. By regularly updating cost estimates, project stakeholders can adapt to fluctuating material prices, labor rates, and unforeseen circumstances effectively. This proactive approach not only enhances accuracy but also aids in budget management, ultimately leading to streamlined project execution.
Furthermore, seeking professional advice emerges as a cornerstone in the conclusion of this guide. Professional insights offer a wealth of expertise and industry knowledge that can elevate the quality of cost estimations. By consulting with professionals, individuals can gain valuable perspectives, identify potential pitfalls, and optimize their budget allocations for optimal project outcomes. The proactive engagement with professionals underscores a commitment to precision and excellence in every phase of the concrete cost estimation process.
Overall, the conclusion segment plays a vital role in reinforcing the importance of accuracy and meticulousness in cost estimation. By leveraging the insights and recommendations outlined in this guide, individuals can navigate the complexities of calculating concrete costs per square foot with confidence and efficacy, ensuring the success of their construction endeavors.
Ensuring Accuracy in Cost Estimation
When it comes to ensuring accuracy in cost estimation for concrete projects, two key aspects—regularly updating cost estimates and seeking professional advice—take center stage in guaranteeing precision and reliability.
Regularly Updating Cost Estimates
A crucial facet of cost estimation maintenance is the practice of regularly updating cost estimates. This involves consistently revisiting and refining initial calculations to align with current market dynamics and project-specific requirements. By updating cost estimates at regular intervals, stakeholders can proactively account for any price fluctuations in materials, labor, and equipment, thus promoting financial prudence and budgetary transparency.
Regular updates to cost estimates introduce a dynamic element to project planning, enabling stakeholders to adapt swiftly to changing circumstances and make informed decisions regarding resource allocation. This responsive approach fosters efficiency and accountability in cost management, positioning projects for success and mitigating the risk of budget overruns.
Seeking Professional Advice
Another vital component in ensuring accuracy in cost estimation is the earnest pursuit of professional advice. Collaborating with seasoned industry experts and consultants offers a wealth of benefits, including access to specialized knowledge, industry best practices, and tailored solutions to complex cost estimation challenges.
Professional advice serves as a valuable resource for validating and optimizing cost estimates, drawing upon diverse experiences and methodologies to enhance the robustness of project budgets. Through expert consultations, individuals can leverage expert insights to refine cost projections, mitigate potential risks, and align their financial strategies with project objectives effectively.
In essence, the incorporation of professional advice into the cost estimation process empowers stakeholders to make informed decisions, optimize resource allocations, and navigate cost uncertainties with clarity and confidence. By embracing the guidance of professionals, individuals can elevate the accuracy and reliability of their concrete cost per square foot estimates, setting a solid foundation for successful project outcomes.