Intro
Polished concrete floors have gained popularity for their durability, aesthetic appeal, and ease of maintenance. Many homeowners seek to achieve this modern look not only for its practical benefits but also for the unique character it brings to a space. This guide will cover everything a homeowner needs to know to create beautiful, polished concrete floors. From the initial planning stages to the final touches, this comprehensive resource is tailored for those looking to enhance their homes.
Materials:
Creating polished concrete floors requires several materials. Here is a detailed list:
- Concrete mix: 1 cubic yard. Choose an appropriate strength, usually around 4000 psi.
- Water: Depends on the quantity of concrete mix; typically 3-5 gallons.
- Curing compound: As per manufacturer’s instructions (usually one gallon for 200 square feet).
- Floor grinder: 1 unit. Ensure the model can handle concrete.
- Diamond grinding pads: Various grits, typically 30, 60, 120, and 200 (one pad of each).
- Polishing pads: 400, 800, 1500, and 3000 grit (one of each).
- Sealer: One gallon, suitable for polished concrete.
- Trowel: 1 unit, for spreading the concrete mix.
- Edging tools: 1 set, for smooth edges.
- Safety gear: Gloves, goggles, and dust mask.
DIY Steps:
Step-by-step process:
-
Planning: Assess the area for the installation. Calculate the amount of concrete needed and gather all materials.
-
Preparation of the area: Clear the space of furniture, debris, and old flooring. Ensure the subfloor is clean and dry.
-
Mixing concrete: Follow the guidelines on the concrete mix package. Combine water and concrete mix in a mixer until consistent in texture.
-
Pouring concrete: Spread the mixed concrete evenly using a trowel, covering the area thoroughly. Working in sections may help manage larger spaces.
-
Leveling the surface: Use a screed board to level the concrete. Ensure that it is even to avoid any imperfections.
-
Curing the concrete: Allow the concrete to cure as the guidelines recommend, usually 28 days for full strength.
-
Grinding the surface: Once cured, use the floor grinder to grind the surface with 30-grit pads until the desired smoothness is reached.
-
Polishing: Gradually switch to higher grit polishing pads, progressing to 3000 grit for a high sheen. This may take several passes and should be done carefully.
-
Sealing the floor: After polishing, apply the suitable concrete sealer using a roller or sprayer. Allow it to dry as per the manufacturer's instructions.
-
Final inspection: Check for any imperfections, unevenness, or spots that may need additional polishing or sealing.
Technical Aspects:
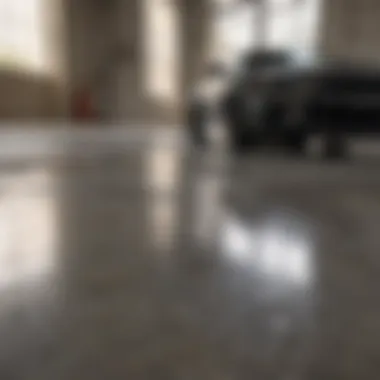
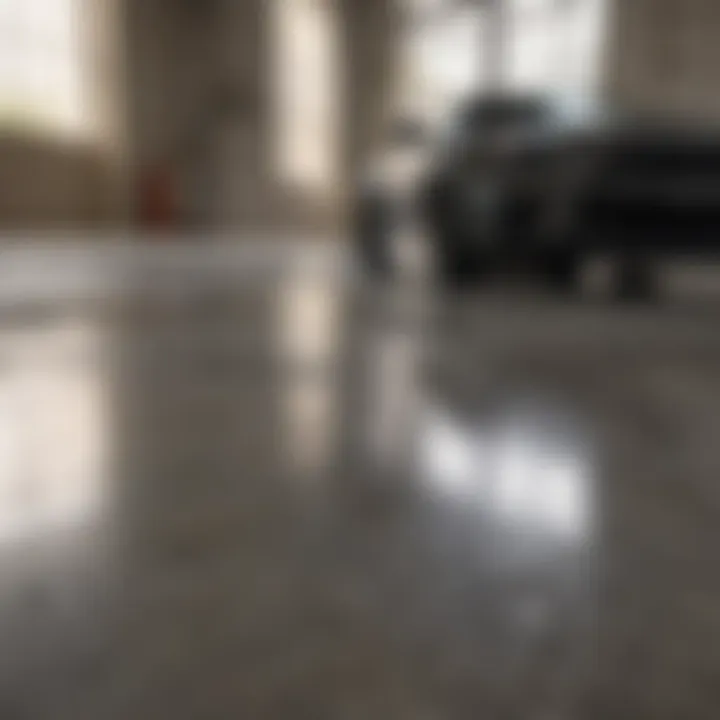
Tools needed:
- Concrete mixer.
- Trowel.
- Floor grinder with diamond pads.
- Polishing machine.
- Rollers or sprayers for sealing.
Timing specifics:
- Mixing and pouring should take about 1-2 hours.
- Curing time can vary; plan for at least 28 days for maximum strength.
- Grinding and polishing can take from several hours to days depending on the size of the floor.
Techniques to elevate results:
- Ensure consistent application of concrete.
- Use water for dust control while grinding.
- Change grinding pads regularly to avoid overheating.
DIY Project Process:
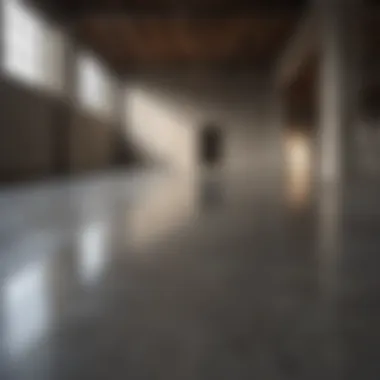
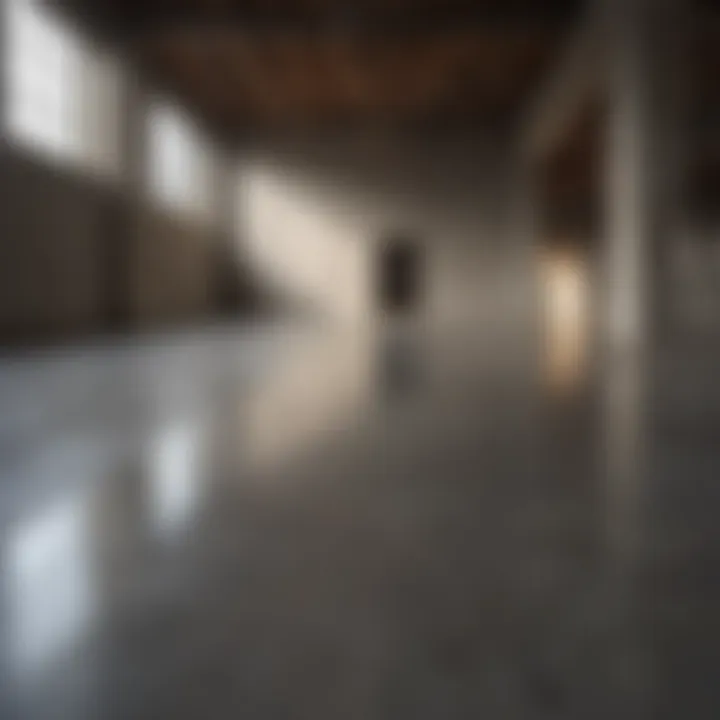
Sequential Steps:
- Initial site preparation.
- Concrete mixing.
- Pouring and leveling.
- Curing period, which is critical.
- Grinding and polishing in sequence.
- Sealing the polished surface.
Troubleshooting Tips:
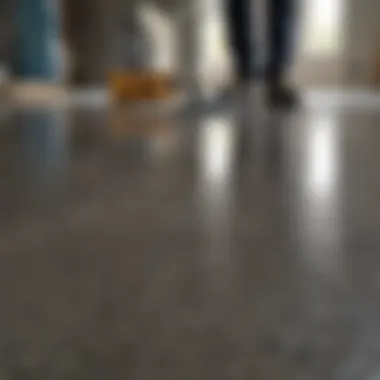
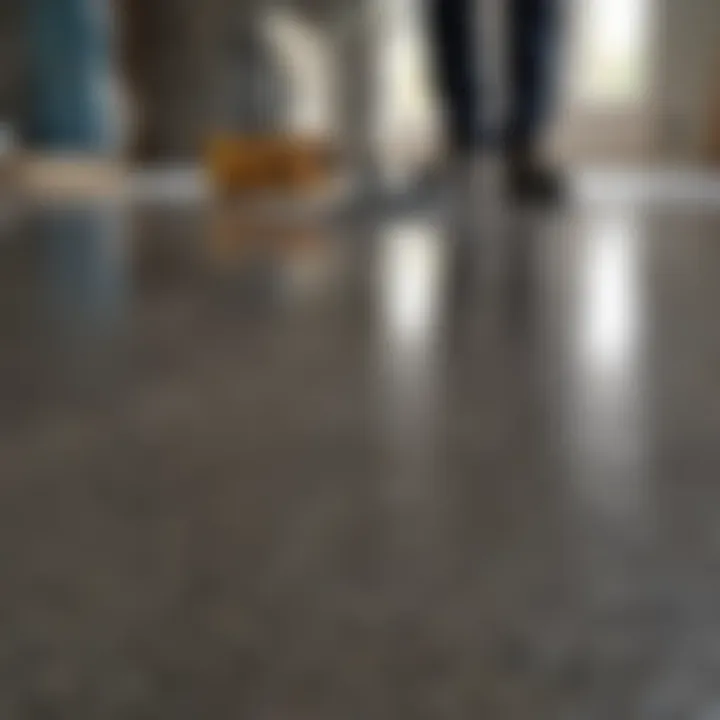
- If the surface is rough, consider additional grinding with lower grit pads.
- Overly shiny areas might need a lower grit polish to reduce gloss.
- Uneven application of sealer can lead to discoloration; ensure even coverage.
Important: Always wear safety gear during the grinding and polishing stages to avoid injuries.
By following these materials, steps, and techniques carefully, homeowners can achieve impressive polished concrete floors that add value and beauty to their spaces.
Understanding Polished Concrete
Understanding polished concrete is crucial for anyone considering this flooring option. It encompasses the fundamental aspects of the material, its applications, and key benefits. Knowing the relationship between the properties of polished concrete and its environmental impact provides a solid groundwork for making informed decisions.
Definition and Characteristics
Polished concrete refers to concrete that has been mechanically ground, honed, and polished to achieve a shiny, smooth surface. The process enhances the concrete’s durability while maintaining its integrity. The key characteristics of polished concrete include its gloss finish, low porosity, and suitability for various settings—ranging from residential to commercial. The surface can vary from a matte to high-gloss appearance, depending on desired aesthetics.
Benefits of Polished Concrete Floors
Polished concrete presents various advantages that make it a favored choice for homeowners and builders alike. The benefits can be broken down as follows:
Durability
Durability is a hallmark quality of polished concrete. It withstands heavy traffic and remains resilient against wear and tear, making it ideal for high-usage areas. This durability provides peace of mind, particularly for those with active households.
The key characteristic of durability in polished concrete is its resistance to scratches and stains. This provides significant benefits since it requires less frequent replacement compared to other flooring materials. The unique feature of durability is its ability to maintain its appearance over time, reducing long-term costs associated with flooring maintenance.
Low Maintenance
One of the standout features of polished concrete is its low maintenance requirements. Minimal cleaning is necessary, often just regular sweeping and mopping to keep the surface in good condition.
This low maintenance aspect contributes to its appeal for busy homeowners and working spaces, where time is a precious commodity. The unique feature here is the absence of carpets or intricate tile patterns, which require more rigorous care. In this context, low maintenance promotes efficiency and hygiene within the living environment.
Eco-Friendly Options
Polished concrete can also be an eco-friendly choice. Many polishing processes utilize existing concrete, reducing the environmental impact associated with new materials. Additionally, various sealers and additives can enhance sustainability further.
The characteristic of eco-friendliness is pertinent due to the reduced emissions during production. The unique feature lies in the option for reclaimed materials, which integrates ecological consciousness into home design. This aspect not only aids in sustainability but also appeals to homeowners seeking greener alternatives.
Cost Efficiency
Polished concrete is often noted for its cost efficiency. The initial investment may be comparable to other flooring options, but the savings accumulate over time through reduced maintenance and longevity.
The key characteristic of cost efficiency is its durability leads to lower life-cycle costs. Homeowners benefit from not needing frequent replacements or heavy maintenance schedules. Thus, the unique feature of cost efficiency becomes evident when factoring in both short-term and long-term financial perspectives.
"Polished concrete floors represent a blend of aesthetics and practicality, making them a prime choice for diverse environments."
In summary, polished concrete encapsulates numerous benefits, such as durability, low maintenance, eco-friendliness, and cost efficiency. Understanding these advantages lays the foundation for effective planning and execution in creating polished concrete floors, ensuring they meet both aesthetic and functional needs.
Preparation for Polishing
Preparation for polishing is a crucial part in achieving high-quality polished concrete floors. Proper preparation ensures a smooth surface, maximizing the effectiveness of subsequent polishing steps. This section details the key elements involved in preparing the concrete surface, assesses the tools needed, and outlines the benefits of thorough preparation.
Assessing the Existing Concrete Surface
Checking for Cracks and Damage
Before polishing begins, examining the existing concrete surface is essential. Checking for cracks and damage helps identify areas that need repair. Small cracks can disrupt the integrity of the polished appearance. If not addressed, these imperfections can lead to bigger issues down the line.
The important characteristic here is accurate identification. Not all damage is visible at first glance. Taking time to assess the surface ensures that repairs are made where necessary, resulting in a better final product. This process is beneficial because it sets a solid foundation for polishing. It is a popular choice among professionals, as it prevents future complications.
The unique feature of checking for cracks involves the use of specialized tools, such as crack injectors or fillers. These items provide smooth finishes and enhance the durability of the polished surface. The primary disadvantage might be the additional time required for repairs, but this is often outweighed by the long-term benefits of a quality finish.
Identifying Surface Sealer or Coatings
Identifying if any surface sealer or coatings are present is another key step before polishing. This evaluation assists in determining the approach to the polishing process. Coatings can interfere with bonding during polishing, affecting the final outcome.
The key characteristic here is understanding the composition of the existing surface. Surface sealers can vary, and knowing their type can help choose the right removal method. This step is beneficial because it prevents potential issues from arising during the polishing phase, ensuring a more effective finish.
A unique feature of identifying sealants involves tests such as water droplet tests. These help determine how to proceed with stripping or grinding the surface. However, the disadvantage is that certain coatings can be challenging or time-consuming to remove, sometimes requiring professional help.
Cleaning the Surface
Debris Removal
Debris removal is a fundamental part of preparing the concrete. A clean surface allows for more efficient grinding and polishing. Dirt, dust, and other contaminants can interfere with the adhesion of the polishing pads.
The key characteristic of debris removal is thoroughness. By ensuring a clean surface, the process maximizes efficiency. This makes it a popular choice among those seeking to achieve the best result. Additionally, a clean surface allows for better visibility during assessment, helping to spot any problematic areas more easily.
A unique feature of this step is the use of industrial vacuum systems. These systems not only remove debris but also minimize dust generation during the process. The primary disadvantage can be the need for additional equipment investment, which might deter some homeowners.
Stain Treatment
Stain treatment is another vital component of surface preparation. Stains can affect the overall aesthetics of polished concrete floors. Therefore, addressing them prior to polishing is crucial for a satisfactory outcome. Proper treatment can enhance the appearance and durability of the finished floor.
The important characteristic of stain treatment is its ability to restore the original look of the concrete. By applying appropriate stain removers, even significant discoloration can often be remedied. This is particularly beneficial for home settings where visual appeal is a priority.
Unique features of this step include the variety of stain removal methods available. These can range from chemical treatments to mechanical scrubbing for tough stains. However, some stains may require professional intervention, which can add to the overall cost.
Gathering Necessary Tools and Materials
Grinding Machines
The right grinding machine is fundamental for successful polishing. These machines serve as the primary tools for surface preparation and finishing. Choosing the correct equipment not only affects efficiency but also the quality of the polished surface.
The key characteristic of grinding machines is their ability to adjust RPMs and diamond grit sizes according to the specific needs of the project. This adaptability makes them a popular choice among contractors and DIY-enthusiasts. The unique feature is that some machines can be operated in a wet or dry state, providing flexibility to the user.
Potential disadvantages include the initial investment costs of purchasing these machines. However, this can be mitigated by considering rentals for one-time projects.
Polishing Pads
Polishing pads are essential for achieving the desired finish on concrete floors. They come in various grits, allowing gradual refinement of the surface. Selecting the appropriate pads for each stage is crucial.
The key characteristic here is multi-purpose usage across different stages of polishing. This versatility enhances the polishing process and helps achieve the desired sheen effectively. Such flexibility results in their popularity among flooring professionals and homeowners alike.
A unique feature is the range of pad types available, such as resin-backed or metal-backed pads. Each serves different purposes and offers advantages. However, a disadvantage might be the learning curve associated with knowing which pad to use and at what stage.
Concrete Densifiers
Concrete densifiers play a significant role in the polishing process. They enhance the strength and durability of the concrete surface. By filling the pores and hardening the concrete, densifiers prepare the surface for fine polishing.
The key characteristic of densifiers is their ability to improve stain resistance and increase overall toughness. This property makes them a beneficial addition to the polishing process, showing great popularity among professionals.
The unique feature of densifiers is the variety of chemical options available, which can suit different concrete types. One potential disadvantage is the requirement for proper application techniques, as improper use may lead to less effective results.
The Polishing Process
The polishing process is a critical component in achieving a high-quality polished concrete floor. This stage not only enhances the aesthetic appeal but also contributes to the durability and resilience of the surface. A well-executed polishing process can significantly elevate the value of a space, whether it's a residential home or a commercial setting.
In this section, we will delve deeply into the various stages of polishing, emphasizing the tools, techniques, and considerations needed to ensure an optimal finish. Each step plays a vital role, influencing not just the appearance but also the long-term maintenance and functionality of the floor.
Initial Grinding
Choosing the Right Grit
Choosing the right grit is fundamental to the grinding process. Grit refers to the size of the abrasive particles in grinding pads. A lower grit number signifies a coarser pad, while a higher number means a finer pad. The selection often depends on the current condition of the concrete surface and the desired finish.
A key characteristic of selecting the appropriate grit is its direct impact on the efficiency of the grinding. Using too coarse a grit when unnecessary could lead to excessive removal of material, while a grit that is too fine may not effectively eliminate surface irregularities. Finding the balance in grit selection is crucial as it sets the groundwork for subsequent polishing stages.
Using the Grinding Machine
Using the grinding machine correctly greatly influences the overall outcome of the polished concrete project. This machine is equipped with different attachments that allow for various operations. The grinding machine should be handled with care to maintain consistency and control.
The integral feature of this equipment is its ability to adapt to multiple tasks with interchangeable disks. It allows for flexibility in addressing different surface conditions. However, users must be vigilant about the machine’s height and speed settings to avoid potential damage to the surface. A poorly handled grinding machine might inadvertently create deeper scratches or uneven surfaces.
Densifying the Concrete
Application of Densifiers
The application of densifiers plays a vital role in enhancing the surface density of concrete. Densifiers are chemical compounds that react with the concrete to fill in the pores and strengthen the matrix. This makes the floor more resistant to wear, stains, and moisture infiltration.
One unique aspect of using densifiers is the improvement in the final appearance of the flooring. A densified surface is typically smoother and can lead to a higher gloss finish. However, it is important to apply these compounds evenly to avoid spots of uneven hardness, which could affect the polishing later on.
Benefits of Densification
Densification benefits the polished concrete process by providing increased durability. This process allows for a denser surface that can withstand heavier foot traffic and impact over time. The increased hardness also aids in resisting staining, making maintenance simpler.
A notable characteristic of densification is its long-term advantage. While the application might add time to the overall polishing project, the result is a floor that requires less frequent repairs or refinishing throughout its lifecycle. Achieving a high-performing polished concrete floor hinges significantly on effective densification.
Fine Grinding
Transitioning to Finer Grits
Transitioning to finer grits is essential in the final stages of the polishing process. As the initial grinding has prepared the surface, moving to finer grits refines the finish. This step enhances the aesthetic while ensuring that any scratches from the previous grinding are smoothed out.
The key characteristic of using finer grits is its contribution to achieving a high-gloss finish. Through gradual transitioning, the surface becomes more reflective, enhancing light play across the floor. However, skipping grits can lead to a finish that lacks the finesse and uniformity desired for polished concrete.
Honing Techniques
Honing techniques are vital in creating a smoother, almost glass-like finish on the concrete. These methods focus on a differential application of pressure and speed, allowing for controlled removal of material. Incorporating honing techniques aids in achieving a consistent appearance throughout the floor.
The significant feature of honing is its ability to control the level of sheen produced. This step can influence the final outcome, making the surface not just smoother but also visually appealing. Finishing processes that fail to use honing may end up with an uneven sheen, detracting from the overall look and quality of the polished surface.
Polishing and Buffing
Choosing the Final Grit
Choosing the final grit is another important decision point in the polishing process. This grit will determine the ultimate appearance and feel of the concrete floor. Generally, the final grit should be selected based on the desired gloss level and the intended use of the space.
A trait of selecting the final grit is its direct impact on the surface's reflectiveness. Higher grits will typically yield a shinier finish, creating a more modern appearance. However, it's crucial to acknowledge that a very high gloss may show imperfections more easily, requiring thorough preparation.
Achieving Desired Gloss Level
Achieving the desired gloss level is often the pinnacle of the polishing process. This stage can significantly enhance the overall impact of the flooring. Several factors influence this step, including the type of concrete mix, the densifying agents used, and the techniques of polishing applied.
The key characteristic of this final step is its importance in meeting the project’s aesthetic goals. A properly executed polish can make a space appear larger and more inviting. However, one must weigh the challenges of maintaining such a finish against the visual benefits. Overall, striking the right balance between gloss and functionality is essential for successful polished concrete flooring.
Post-Polishing Care
Post-polishing care is a critical component of maintaining the beauty and functionality of polished concrete floors. After investing time and resources into the polishing process, proper care ensures the longevity of the surface. Establishing a routine for sealing and maintenance prolongs the shine and integrity of the flooring. In this section, we will explore sealing the polished surface and maintenance practices that are essential for keeping polished concrete floors in optimal condition.
Sealing the Polished Surface
Selecting Appropriate Sealers
Selecting the right sealers is vital for protecting polished concrete. Sealers act as a barrier against stains, moisture, and various contaminants. A key characteristic of sealers is their ability to enhance the gloss and depth of the concrete surface. Popular options include penetrating sealers and acrylic sealers.
Penetrating sealers are beneficial as they infiltrate the concrete, offering strong protection without altering the floor's appearance significantly. On the other hand, acrylic sealers provide a top layer of shine, making them ideal for enhancing aesthetics. However, they may require reapplication more frequently than penetrating alternatives. Each type has unique advantages and challenges, demanding careful consideration based on individual needs and conditions.
Application Techniques
Application techniques also play an important role in the effectiveness of sealing. A common method involves applying the sealer with a roller or sprayer, ensuring even distribution across the surface. The key characteristic of these techniques is that they promote uniform coverage, preventing streaks or missed areas.
Using a consistent application method is a beneficial choice as it helps to maximize the sealer's effectiveness. A unique feature of proper application techniques is the ability to blend multiple sealer types for customized protection and finish. However, one must be cautious during application, as incorrect methods can lead to uneven surfaces or compromised seal protection.
Maintenance Practices
Regular Cleaning Procedures
Regular cleaning procedures are necessary to preserve the polished surface. This involves routine sweeping or dust mopping to remove loose debris and prevent scratches. The key characteristic of these procedures lies in their simplicity and low cost, making maintenance manageable for most homeowners.
A unique feature of regular cleaning is the use of pH-neutral cleaners that protect the surface without compromising the shine. Avoiding harsh chemicals is crucial, as they can dull the polish over time. Adopting consistent cleaning routines not only maintains cleanliness but also supports the structural integrity of the polished concrete.
Repairing Minor Damage
Repairing minor damage promptly is paramount to maintaining polished concrete floors. This includes addressing chips, cracks, or any surface imperfections. The key characteristic of this practice is the preventative nature of timely repairs, as ignoring damage can lead to larger problems.
Using a concrete repair filler can be an effective way to restore compromised areas. A unique feature of this method is its ease of application, allowing homeowners to perform repairs without needing extensive skills. However, it is essential to match the color and finish of the repair material with the existing floor for optimal results. Failure to do so may lead to visible patches that detract from the flooring's overall appeal.
Maintaining polished concrete floors is not just about aesthetics; it is about preserving your investment and ensuring a safe and clean living environment.
In summary, post-polishing care involves both sealing techniques and regular maintenance practices. Recognizing the importance of these elements will ensure that polished concrete floors remain attractive and durable for years to come.
Challenges in Polishing Concrete
Understanding the challenges in polishing concrete is essential to ensure a successful project outcome. Each phase comes with its unique set of problems that can impact the final appearance and durability of the floor. Being aware of these challenges allows homeowners and contractors to devise better strategies and solutions. Recognizing issues before they escalate ensures that the polished concrete floors not only meet aesthetic standards but also withstand the test of time.
Common Issues Encountered
Uneven Surfaces
Uneven surfaces present a significant barrier in the polishing process. They can arise from various factors including poor initial installation, settling of the substrate, or improper overlays. These surfaces can complicate the grinding and polishing phases, affecting the final result. A key characteristic of uneven surfaces is their potential to create noticeable dips and rises. This not only affects the overall appearance but can also impact the leveling process. In this article, we will discuss strategies to identify and manage uneven surfaces and help assure a level and smooth final product.
Allergies to Dust and Chemicals
The production of dust and the use of chemical agents during concrete polishing present health risks, particularly for individuals with allergies or respiratory sensitivities. Dust generated from grinding can linger in the air, leading to discomfort or health issues for sensitive individuals. Additionally, the chemicals used as sealers or densifiers may also cause allergic reactions. Awareness about this issue is crucial for maintaining a safe environment during the polishing process. Proper ventilation and the use of suitable personal protective equipment can mitigate these risks, ensuring that the flooring project remains safe and accessible to all.
Solutions and Tips
Professional Help
Engaging professional help can significantly ease the burden of dealing with the challenges presented in concrete polishing. Experts bring a wealth of knowledge and experience in identifying issues and implementing solutions effectively. The key characteristic of professionals in this field lies in their finished projects, which often showcase their quality work. Many homeowners find that investing in professional services results in superior outcomes with less risk of mistakes. While costs may vary, the benefits of hiring experienced hands typically outweigh the potential complications of a DIY approach.
Proper Equipment Usage
Proper equipment usage is crucial for a successful polishing job. The tools used can make or break the process, as each stage of the polishing requires specific machinery and techniques. This ensures not just efficiency but also precision. A key characteristic of using the correct equipment is the direct correlation to the finished product quality. Selecting appropriate grinding machines, pads, and polishers not only enhances the work but can prevent major errors. Proper usage also safeguards against potential equipment-related accidents, making it a wise choice in any flooring endeavor.
"Understanding the challenges and solutions in polishing concrete floors can elevate the final results to a new standard."
Final Considerations
In the journey towards creating polished concrete floors, final considerations play a vital role. This last section focuses on important elements that help homeowners and contractors make informed decisions. From cost implications to suitability for various spaces, understanding final considerations can lead to better outcomes.
Cost Analysis
Initial Investment
The initial investment for polished concrete floors involves several components including preparation, materials, and labor. Understanding these costs is essential to manage overall budgets effectively. A key characteristic of initial investment in polished concrete is its upfront cost. While some might view this as a drawback, the durable nature of polished concrete can justify the expense. Polished concrete requires less frequent repairs and replacements compared to other flooring options, making it a complex but beneficial choice. However, homeowners should consider potential fluctuations in prices for materials based on local market conditions.
Long-Term Savings
Long-term savings associated with polished concrete floors stem from their low maintenance needs and durability. Over time, these savings can outweigh any initial expenditure. The ability of polished concrete to resist stains and scratches leads to reduced spending on cleaning products and repairs. Additionally, the energy efficiency of polished concrete can result in lower utility bills, offering a compelling financial argument. The unique feature of long-term savings is the peace of mind it brings. Homeowners can focus on enjoying their spaces rather than worrying about floor upkeep.
Suitability for Different Spaces
Residential Applications
Polished concrete is often favored for residential applications due to its aesthetic flexibility and performance. Homeowners appreciate its versatility in design, allowing it to complement various styles from modern to rustic. The key characteristic of residential applications is the ability to customize finishes easily. Some may prefer a high-gloss shine, while others might select a more matte appearance that aligns better with their interior decor. However, it is essential to ensure the right finish is chosen to meet personal preferences and usage needs in high-traffic areas.
Commercial Settings
For commercial settings, the durability and low maintenance of polished concrete shine. Businesses enjoy the benefits of a flooring solution that can withstand heavy foot traffic and machinery. The capacity of polished concrete to minimize dust and allergens is also favorable for both employee and customer health. One unique feature of commercial applications is their often larger scale. This can lead to economies of scale during installation, possibly reducing per-square-foot costs. Nevertheless, business owners must weigh the initial investment against long-term benefits carefully to optimize their choices.
The careful evaluation of polished concrete outcomes in different settings is crucial for gaining maximum benefits.
These final considerations should guide readers toward a holistic understanding of polished concrete flooring. Whether for residential or commercial use, making these decisions can significantly affect functionality and satisfaction with the final product. Understanding costs and suitability can empower homeowners and business owners alike to make the best decisions for their specific needs.