Materials:
- Vinyl siding panels: 1000 sq ft
- J-channel: 150 linear ft
- Corner posts: x4
- Starter strip: 100 linear ft
- Nails: 1.5-inch and 2-inch
- House wrap: 1000 sq ft
- Utility knife
- Tape measure
- Hammer
- Level
- Caulk gun
- Ladder
- Siding removal tool
DIY Steps:
-
Preparation: Measure the walls to determine the amount of siding needed. Remove any existing siding and repair any damaged areas on the walls.
-
Installation of House Wrap: Cover the walls with the house wrap, starting from the bottom and working upwards, ensuring it overlaps properly.
-
Installing Starter Strips and J-Channels: Begin by attaching the starter strip at the bottom edge of the wall and the J-channel around windows and doors for a clean finish.
-
Cutting and Fitting Siding Panels: Cut the vinyl siding panels to size using a utility knife, ensuring they lock into place securely.
-
Attaching Siding Panels: Start installing the siding panels from the bottom, ensuring they overlap correctly and are nailed securely to the wall.
Technical Aspects:
-
Timing Specifics: Allocate 1-2 weekends for a typical siding installation project, depending on the size of the building.
-
Tools: Ensure you have all necessary tools mentioned above for a smooth installation process.
-
Critical Techniques: Use a level frequently to ensure straight alignment and proper overlap of siding panels.
DIY Project Process:
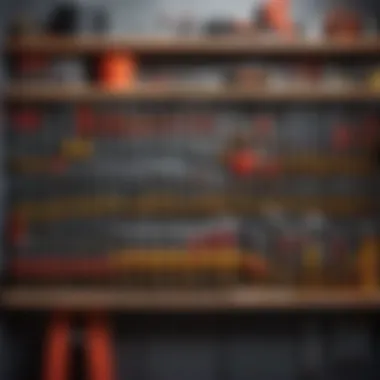
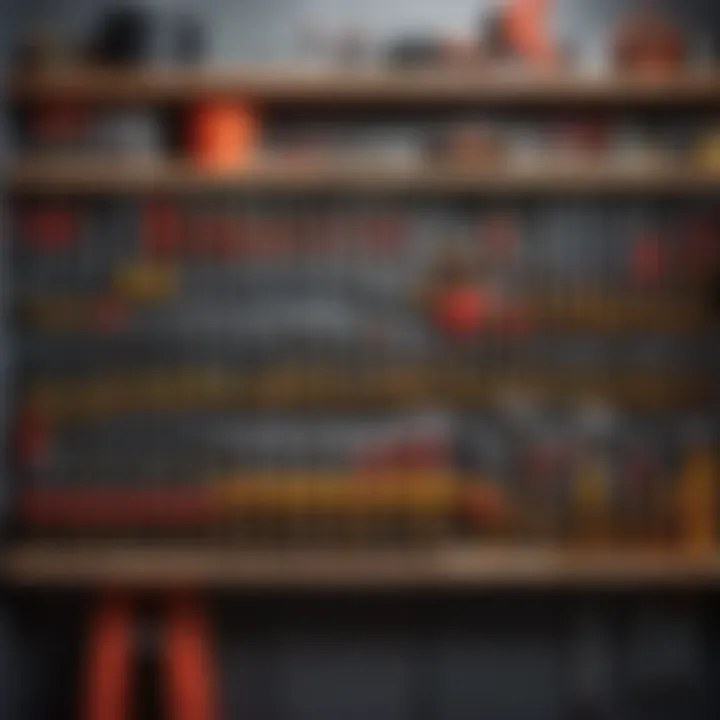
-
Step-by-Step Installation Method: Follow a systematic approach, starting with preparation, house wrap installation, adding starter strips and J-channels, cutting and fitting siding panels, and finally, attaching them securely.
-
Key Techniques and Timings: Pay close attention to ensuring proper overlap of panels, especially at corners and edges, to prevent water infiltration.
-
Troubleshooting Tips: If panels do not align correctly, check for proper nailing and adjust as needed. Ensure all corners and edges are sealed with caulking for added protection.
Remember, attention to detail and precision are crucial in achieving a professional-looking siding installation that enhances both the aesthetics and functionality of your building.
Factors Affecting Labor Costs
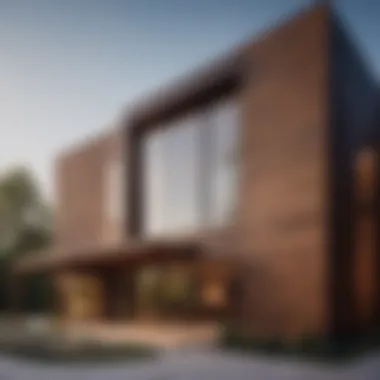
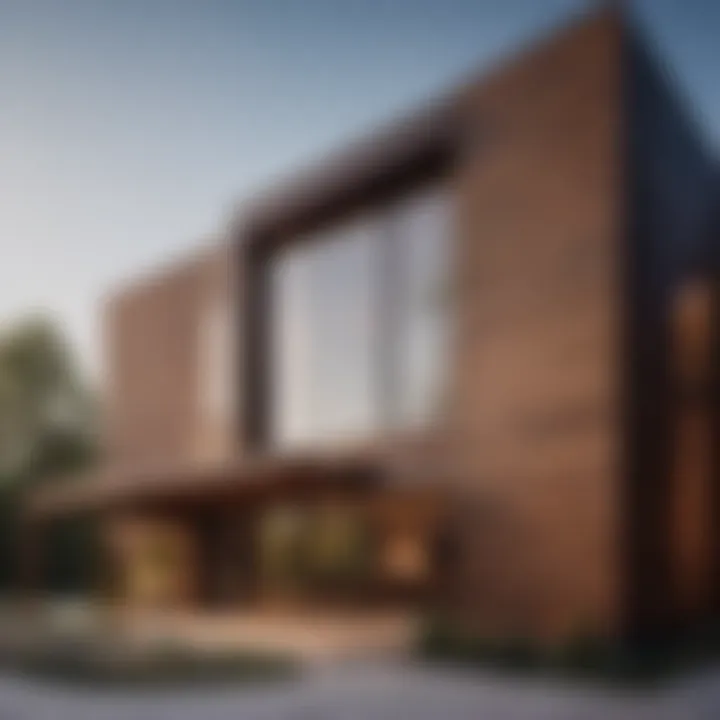
In this article, the discussion around factors influencing labor costs in siding installation is paramount. Understanding the nuances of labor costs is vital for individuals considering a siding project. Various elements come into play when determining labor expenses, each with its own impact on the overall cost. By delving into these factors, readers can grasp the intricacies of labor pricing and make informed decisions.
Type of Siding Material
When it comes to siding installation, the type of material chosen significantly influences labor costs. Different siding materials require distinct installation techniques, affecting the amount of time and effort required from professionals. For instance, vinyl siding may be quicker to install compared to wood siding, as it is more lightweight and easier to manipulate. Consequently, labor prices may vary based on the complexity of working with a specific material. Homeowners should consider the trade-offs between the visual appeal and durability of the siding material against the corresponding labor costs.
Size of the Project
The size of a siding project directly correlates with labor costs. Larger projects demand more time and manpower to complete, leading to higher labor expenses. Extensive projects such as siding an entire multi-story home will naturally incur greater labor costs compared to smaller-scale projects. Additionally, the scale of the project can impact the efficiency of the installation process. Contractors may offer pricing structures that take into account economies of scale, providing cost advantages for larger projects that require more labor hours.
Location and Accessibility
The location of a property and its accessibility play crucial roles in determining labor costs for siding installation. Properties situated in remote areas or locations with challenging terrain may require additional logistical planning and resources, leading to higher labor expenses. Accessibility to the project site also influences the ease of transporting materials and equipment, which can impact the efficiency of the installation process. Moreover, local labor market conditions and demand can affect pricing, as contractors may adjust their rates based on the prevailing economic factors in a specific region.
Average Labor Prices Across Different Types of Siding
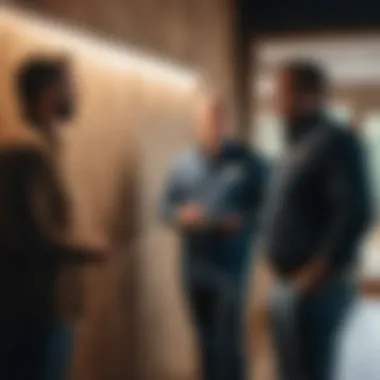
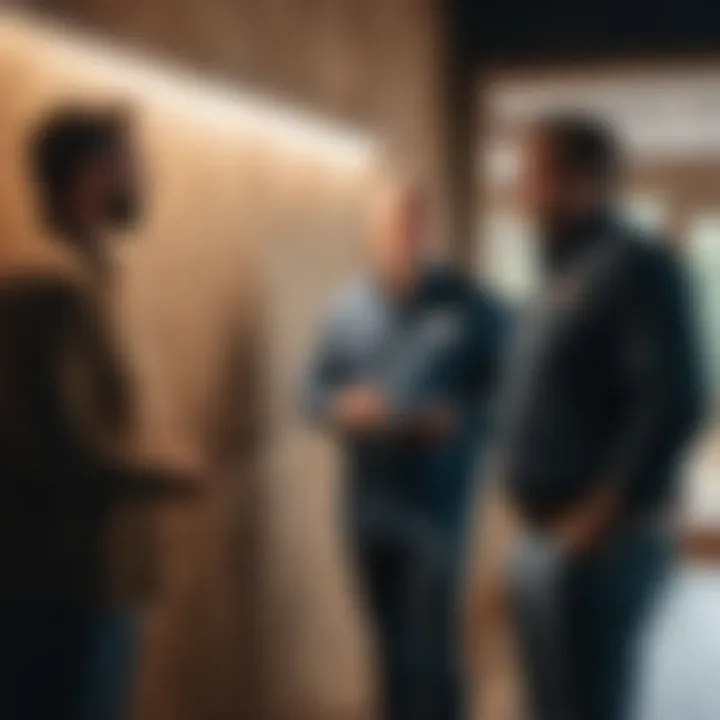
When considering the labor prices associated with installing siding, it is crucial to understand the average costs across different types of siding materials. This section provides valuable insights into the pricing variations based on the type of siding selected. By delving into the specifics of labor costs for various siding materials, readers can make informed decisions regarding their siding installation projects.
Vinyl Siding
Single-story Homes
Exploring vinyl siding for single-story homes reveals a cost-effective and visually appealing option for homeowners. Vinyl siding is known for its durability and low maintenance requirements, making it a popular choice among many. Its ease of installation adds to its appeal, with a wide range of colors and styles to choose from. However, while vinyl siding offers great value for money and longevity, its susceptibility to cracking in extreme temperatures may be a drawback worth considering.
Multi-story Homes
When it comes to multi-story homes, vinyl siding continues to be a practical choice. Its lightweight nature makes it easier to work with on taller structures, reducing labor costs associated with installation. Vinyl siding's resistance to moisture and fading makes it a long-lasting option for homes requiring multiple stories. Despite its many advantages, it's important to note that extreme weather conditions can affect vinyl siding's performance over time, warranting regular inspections and maintenance.
Wood Siding
Cedar Siding
The allure of cedar siding lies in its natural beauty and timeless appeal. Cedar siding exudes a sense of warmth and character, enhancing the visual aesthetics of any property. Its longevity and eco-friendly qualities make it a sought-after choice for homeowners looking to blend sustainability with elegance. However, cedar siding may require more maintenance compared to other materials, as it is prone to rot and insect damage if not properly treated and preserved.
Engineered Wood Siding
Engineered wood siding offers a balance between affordability and durability. Composed of wood strands and resins, this type of siding mimics the look of natural wood while providing enhanced performance against weather elements. Engineered wood siding is engineered to resist moisture and pests, making it a low-maintenance alternative to traditional wood options. Despite its benefits, engineered wood siding may not offer the same level of authenticity and charm as natural wood siding.
Fiber Cement Siding
Cost Factors
Examining the cost factors associated with fiber cement siding sheds light on its position as a premium siding material. Fiber cement siding combines the strength of cement with the versatility of wood fibers, creating a durable and robust cladding option. Despite its higher upfront costs, fiber cement siding delivers exceptional longevity and resistance to fire, moisture, and pests. Its ability to mimic the appearance of natural wood or stucco adds to its appeal, making it a popular choice for homeowners seeking a high-end siding solution.
Metal Siding
Metal siding presents a modern and sleek option for homeowners looking for a contemporary aesthetic. Its exceptional durability and resistance to elements make it a practical choice for those prioritizing longevity. Metal siding requires minimal maintenance and offers excellent protection against fire, rot, and pests. However, the reflective nature of metal siding can create glare and heat retention in certain environments, impacting energy efficiency. Despite this consideration, metal siding remains a standout choice for its clean lines, adaptability, and lasting performance.
Additional Labor Costs
When it comes to installing siding, additional labor costs play a crucial role in the overall expenses. These costs are a significant aspect that can impact the budgeting and planning of a siding installation project. Understanding the importance of additional labor costs is essential for homeowners as it allows for proper financial preparation and prevents any surprises along the way.
Exploring the elements of additional labor costs provides insight into the comprehensive nature of siding installation expenses. Factors such as the removal of old siding, structural repairs, and trim work contribute to these costs. By delving into each of these elements, homeowners can make informed decisions about their siding installation project and ensure that all necessary work is accounted for in their budget.
Removal of Old Siding
The removal of old siding is a critical step in the siding installation process that requires a significant amount of labor. Before installing new siding, the existing siding must be carefully removed to ensure a clean surface and proper attachment of the new materials. This process involves labor-intensive work, including dismantling and disposing of the old siding materials.
Additionally, the removal of old siding may uncover underlying issues such as water damage, mold, or pest infestations that need to be addressed before proceeding with the new installation. These unexpected repairs can add to the labor costs but are essential for the long-term durability and structural integrity of the building.
Structural Repairs
Structural repairs are another aspect of additional labor costs that are vital for ensuring the stability and safety of the building. During the siding installation process, contractors may discover structural issues such as rotting wood, damaged frames, or compromised foundations that require repairs.
Addressing these structural concerns involves skilled labor and expertise to ensure that the building's framework is sound and can support the new siding materials. While structural repairs can increase labor costs, neglecting these issues can lead to more significant problems in the future, making it essential to allocate resources for these repairs during the siding installation project.
Trim Work
Trim work is a meticulous and detailed aspect of siding installation that requires precision and attention to detail. The installation of trims around windows, doors, corners, and edges enhances the aesthetics of the siding and provides a finished look to the exterior of the building.
Trim work involves measuring, cutting, and fitting trim pieces accurately to achieve a seamless and polished appearance. Skilled labor is necessary to ensure that the trims are installed correctly and enhance the overall visual appeal of the siding. While trim work may add to the labor costs, it is an essential component of a well-executed siding installation project that elevates the curb appeal and functionality of the building.
Choosing the Right Contractor
When embarking on a siding installation project, one of the most critical decisions you will make is selecting the right contractor. This pivotal choice can significantly impact the overall success and longevity of the project. In this article, we delve deep into the importance of choosing the right contractor, focusing on essential elements that housewives and homeowners should consider for a seamless siding installation experience.
Key Elements to Consider:
1. Experience and Expertise: Opting for a contractor with a solid track record in siding installations can instill confidence in the quality of work to be delivered. Their experience can guide you through various siding options, techniques, and potential challenges, ensuring a smoother process from start to finish.
2. Reputation and Reviews: Prioritize contractors with a stellar reputation and positive reviews from past clients. Testimonials and feedback can offer valuable insights into the contractor's professionalism, reliability, and dedication to customer satisfaction.
3. Licensing and Insurance: Ensure that the contractor possesses the necessary licenses and insurance coverage. Licensed contractors are likely to adhere to industry standards and regulations, providing you with legal protection in case of any untoward incidents during the project.
4. Communication and Transparency: Effective communication is key to a successful contractor-client relationship. Look for contractors who are transparent about their processes, timelines, costs, and any potential setbacks that may arise. A contractor who keeps you informed every step of the way can alleviate stress and build trust.
Benefits of Choosing the Right Contractor:
Selecting a reputable and reliable contractor can yield numerous benefits for your siding installation project. From impeccable workmanship to adherence to timelines and budget constraints, the right contractor brings peace of mind and assurance that your investment is in capable hands.
Considerations for Choosing the Right Contractor:
It is crucial to conduct thorough research, request multiple quotes, and schedule in-person consultations before making a final decision. Take the time to ask pertinent questions, discuss your expectations, and assess the contractor's knowledge and communication style to ensure a harmonious working relationship.