Materials:
- Microfiber cloths (10 count)
- All-purpose cleaner (32 oz)
- Glass cleaner (16 oz)
- Vacuum cleaner
- Dustpan and brush set
- Mop and bucket
DIY Steps:
- Begin by decluttering the targeted section to ease cleaning access.
- Use a vacuum cleaner to remove loose debris and dust from surfaces.
- Apply the all-purpose cleaner to surfaces and wipe down with microfiber cloths.
- Utilize the glass cleaner for mirrors and windows, ensuring a streak-free finish.
- Mop the floors using the appropriate cleaner, focusing on high-traffic areas.
- Empty the dustpan and brush set and ensure all residues are properly disposed of.
Technical Aspects:
- Tools: Vacuum cleaner, mop, bucket, dustpan, brush set
- Timing: Estimate 1-2 hours depending on section size
- Techniques: Circular motions for wiping, proper handling of cleaning agents
DIY Project Process:
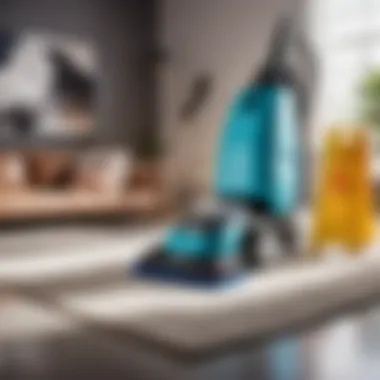

- Start with decluttering to make cleaning more manageable.
- Vacuum all surfaces to remove loose dirt and debris effectively.
- Apply cleaners as directed and ensure thorough coverage.
- Use separate cloths for different surfaces to prevent cross-contamination.
- Mop floors systematically, starting from furthest corner towards exit.
- Check for missed spots and make necessary touch-ups for a flawless finish.
Troubleshooting Tips:


- For streaks on mirrors or glass, utilize a dry microfiber cloth for a final polish.
- In case of stubborn stains, allow cleaning solution to sit for a few minutes before wiping.
- If floors appear dull after mopping, consider using a specialized floor restorer.
Understanding Sectional Cleaning Costs
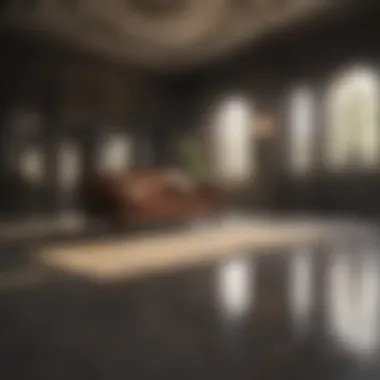

In the realm of efficient cleaning practices, understanding sectional cleaning costs plays a crucial role in managing expenditure and optimizing resources effectively. It serves as the cornerstone for developing cost-saving measures and implementing strategic decisions that can significantly impact the overall cleaning budget. By delving into the intricate details of sectional cleaning costs, individuals can gain a comprehensive understanding of the various factors influencing pricing structures and operational expenses. This section aims to elucidate the significance of comprehending sectional cleaning costs within the broader context of efficient cleaning management.
Factors Affecting Cleaning Costs
Size of the Sectional Area
The size of the sectional area is a pivotal factor that directly affects cleaning costs. Larger sectional areas necessitate more time, effort, and resources to ensure thorough cleaning. Understanding the size of the area enables cleaning professionals to allocate resources efficiently, determine appropriate staffing levels, and streamline operational processes. While larger areas may incur higher cleaning expenses, strategic planning based on the size of the sectional area can lead to optimized cleaning routines and enhanced cost-effectiveness.
Type of Surfaces
The type of surfaces within a sectional area significantly impacts cleaning costs due to varying cleaning requirements. Different surfaces, such as hardwood, carpet, tile, or glass, entail distinct cleaning methods and materials, influencing overall expenses. By considering the type of surfaces present in the area, cleaning managers can tailor cleaning procedures to suit specific needs, thereby minimizing wastage and optimizing cleaning efficiency. Understanding the characteristics of each surface type is key to determining the most suitable cleaning approach that balances efficacy and cost-effectiveness.
Frequency of Cleaning
The frequency of cleaning operations directly correlates with total cleaning costs over time. Regular cleaning intervals ensure consistent hygiene standards but may lead to higher cumulative expenses. Conversely, infrequent cleaning may result in deeper cleaning processes to maintain cleanliness, impacting labor and material costs. By analyzing the optimal frequency of cleaning based on usage patterns and cleanliness requirements, cleaning managers can devise schedules that strike a balance between effective maintenance and cost efficiency.
Specialized Cleaning Requirements
Specialized cleaning requirements, such as stain removal, disinfection protocols, or specific safety measures, can significantly elevate cleaning costs. Addressing specialized cleaning needs demands tailored solutions, specialized equipment, and trained personnel, adding an extra layer of expense to cleaning operations. By understanding and accommodating specialized cleaning requirements efficiently, cleaning managers can ensure thorough cleanliness while optimizing costs through targeted resource allocation and strategic planning.
Strategies to Reduce Sectional Cleaning Expenses
In the realm of sectional cleaning, the significance of reducing expenses through strategic measures cannot be overstated. As highlighted in this comprehensive analysis, employing efficient cost-saving strategies is essential for optimal budget management and resource utilization. By delving into specific elements such as efficient resource allocation, implementing green cleaning practices, and exploring outsourcing vs. in-house cleaning teams, readers can gain valuable insights to streamline their cleaning operations and maximize cost-effectiveness. The meticulous scrutiny of cost-cutting methods and the implementation of sustainable practices outlined in this section pave the way for enhanced efficiency and financial savings in sectional cleaning.
Efficient Resource Allocation
Efficient resource allocation is a cornerstone of cost optimization in sectional cleaning operations. Within this framework, two key aspects stand out: optimal staffing levels and inventory management. Effective management of these resources not only contributes to the overall cleanliness and hygiene standards but also plays a pivotal role in controlling costs and enhancing operational efficiency.
Optimal Staffing Levels
Optimal staffing levels are crucial in ensuring that the right number of cleaning personnel is deployed to handle the cleaning tasks effectively. By striking a balance between manpower and workload, organizations can enhance productivity while minimizing labor costs. The unique characteristic of optimal staffing levels lies in its ability to align workforce capacity with the demand for cleaning services, thus optimizing operational efficiency and cost-effectiveness. However, achieving the optimal balance may pose challenges in terms of workforce planning and scheduling, requiring careful analysis and constant monitoring to reap the full benefits of this staffing strategy.
Inventory Management
Inventory management plays a pivotal role in streamlining cleaning operations and controlling expenses. By efficiently managing cleaning materials, supplies, and equipment inventory, organizations can avoid unnecessary costs associated with overstocking or stockouts. The key characteristic of effective inventory management lies in its ability to ensure that the right quantity of cleaning resources is available when needed, minimizing waste and enhancing cost-efficiency. However, maintaining optimal inventory levels requires meticulous planning, monitoring, and coordination to avoid disruptions in cleaning operations and optimize resource utilization.
Implementing Green Cleaning Practices
The integration of green cleaning practices into sectional cleaning operations offers a multitude of benefits, ranging from environmental sustainability to improved indoor air quality and occupant well-being. Within this context, two primary aspects take center stage: environmentally friendly products and energy-efficient equipment. By embracing these practices, organizations can not only reduce their environmental footprint but also achieve long-term cost savings and operational enhancements.
Environmentally Friendly Products
The usage of environmentally friendly cleaning products is a key aspect of green cleaning practices, emphasizing the importance of sustainability and eco-friendliness in cleaning operations. The key characteristic of these products lies in their biodegradable, non-toxic, and low-impact formulations, which contribute to a healthier indoor environment and reduced environmental pollution. The unique feature of environmentally friendly products is their ability to deliver effective cleaning results without compromising environmental and human health, making them a popular choice for organizations seeking to adopt sustainable cleaning practices.
Energy-Efficient Equipment
Energy-efficient cleaning equipment plays a vital role in reducing energy consumption and operational costs while maintaining optimal cleaning performance. The key characteristic of energy-efficient equipment lies in its ability to deliver high cleaning efficacy with minimal power usage, translating into cost savings and reduced environmental impact. The unique feature of these equipment lies in their advanced technologies and design innovations that prioritize energy efficiency without sacrificing cleaning performance. However, the adoption of energy-efficient equipment may entail higher initial investment costs, which can be offset by long-term energy savings and operational efficiencies.
Outsourcing vs. In-House Cleaning Teams
The decision between outsourcing cleaning services and maintaining an in-house cleaning team is a critical aspect that directly impacts costs, quality, and operational efficiency. Within this discourse, two essential considerations come to the fore: cost-effectiveness comparison and quality assurance considerations. By evaluating these factors, organizations can determine the most suitable cleaning service delivery model that aligns with their strategic objectives and budgetary constraints.
Cost-Effectiveness Comparison
Comparing the cost-effectiveness of outsourcing vs. in-house cleaning teams is essential in determining the most financially prudent approach for cleaning operations. The key characteristic of this comparison lies in analyzing the direct and indirect costs associated with each model, including labor, materials, equipment, and overhead expenses. By conducting a thorough cost-benefit analysis, organizations can pinpoint the most cost-effective option that delivers the desired cleaning outcomes while optimizing operational expenditures. The unique feature of cost-effectiveness comparison is its ability to provide a comprehensive overview of the financial implications and benefits of each cleaning service model, enabling organizations to make informed decisions that align with their budgetary constraints.
Quality Assurance Considerations
Ensuring quality assurance in cleaning operations is paramount for maintaining high cleaning standards, customer satisfaction, and operational reliability. The key characteristic of quality assurance considerations lies in implementing robust quality control measures, performance evaluations, and feedback mechanisms to uphold cleaning quality and service excellence. The unique feature of quality assurance considerations is their focus on delivering consistent and reliable cleaning outcomes that meet or exceed customer expectations, safeguarding the reputation and credibility of the organization. However, overlooking quality assurance considerations may result in subpar cleaning results, customer dissatisfaction, and operational inefficiencies, highlighting the importance of prioritizing quality management practices in sectional cleaning operations.
This detailed exploration of cost optimization strategies in sectional cleaning offers a comprehensive roadmap for organizations seeking to enhance efficiency, reduce expenses, and elevate cleaning standards. By dissecting key elements such as resource allocation, green cleaning practices, and outsourcing considerations, organizations can achieve a harmonious balance between cost-effectiveness and operational excellence in their cleaning operations. The integration of sustainable practices, informed decision-making, and quality assurance measures outlined in this analysis empowers organizations to navigate the complexities of modern cleaning challenges and emerge as leaders in cost-effective and environmentally responsible cleaning solutions.
Technology Integration for Cost Optimization
In the realm of sectional cleaning costs, technology integration plays a pivotal role in optimizing expenses and streamlining operations. Embracing cutting-edge technologies can revolutionize the way cleaning tasks are performed, leading to enhanced efficiency and cost-effectiveness. By incorporating innovative solutions, such as robotic cleaners and smart sensors, into cleaning processes, businesses can achieve a higher level of precision and productivity while reducing overall operational costs.
Automation in Cleaning Processes
Robotic Cleaners
Robotic cleaners represent a significant advancement in the cleaning industry due to their autonomous operation and ability to perform tasks with minimal human intervention. These intelligent machines are equipped with sensors and sophisticated algorithms that enable them to navigate through various spaces, ensuring thorough cleaning with precision. The key characteristic of robotic cleaners lies in their efficiency and consistency, which contribute significantly to the overall goal of cost optimization. Their ability to access hard-to-reach areas and perform repetitive tasks tirelessly makes them a popular choice for businesses seeking to enhance their cleaning processes. Despite their advantages, robotic cleaners may face limitations in handling complex cleaning scenarios that require human intervention or delicate handling.
Smart Sensors
Smart sensors play a crucial role in enhancing cleaning processes by providing real-time data and insights into the cleanliness of different spaces. These advanced sensors can detect levels of dust, moisture, and other contaminants, allowing cleaning teams to target specific areas that require immediate attention. The key characteristic of smart sensors lies in their ability to gather accurate data and adjust cleaning strategies accordingly, making them a valuable asset for cost optimization initiatives. The unique feature of smart sensors is their capacity to automate cleaning tasks based on predefined parameters, reducing manual intervention and enhancing operational efficiency. While smart sensors offer numerous advantages in terms of data-driven cleaning, they may face challenges related to initial setup costs and the need for calibration to ensure accurate readings.
Data Analytics for Predictive Maintenance
Predictive Analysis Tools
Predictive analysis tools leverage data analytics to predict maintenance requirements and optimize cleaning schedules for maximum efficiency. By analyzing historical data and performance metrics, these tools can identify patterns and trends that help forecast potential issues before they escalate, thus minimizing downtime and reducing maintenance costs. The key characteristic of predictive analysis tools is their ability to provide actionable insights for proactive maintenance, aligning with the overall goal of cost optimization. The unique feature of predictive analysis tools lies in their capacity to prioritize maintenance tasks based on criticality and urgency, improving operational resilience and performance. While predictive analysis tools offer significant advantages in terms of predictive maintenance, they may require integration with existing systems and training for effective implementation.
Maintenance Scheduling Optimization
Maintenance scheduling optimization focuses on refining cleaning schedules to maximize efficiency and resource utilization. By fine-tuning cleaning routines based on predictive analytics and real-time data, businesses can ensure optimal use of labor and equipment while minimizing wastage and redundancies. The key characteristic of maintenance scheduling optimization is its ability to balance preventive maintenance tasks with operational requirements, fostering a proactive approach to maintenance planning. The unique feature of maintenance scheduling optimization is its flexibility to adapt to changing circumstances and dynamic cleaning environments, enabling businesses to respond swiftly to emerging needs. While maintenance scheduling optimization offers benefits in terms of efficiency and productivity, it may pose challenges in terms of initial setup and adjustments to existing workflows.
Case Studies and Best Practices
In the spectrum of optimizing sectional cleaning costs, delving into case studies and best practices is crucial for gaining practical insights and actionable strategies. Real-life examples serve as practical benchmarks, offering tangible scenarios where cost management strategies have been successfully implemented. These case studies provide a roadmap for understanding the nuances of cost optimization, highlighting the challenges faced and the innovative solutions deployed.
Success Stories in Cost Management
Real-Life Examples:
Real-life examples play a pivotal role in elucidating the effectiveness of various cost management strategies. By examining specific instances where cost reductions were achieved through strategic approaches, readers can draw parallels to their own cleaning operations. These examples showcase the potential impact of implementing efficient cleaning practices and the transformation they can bring about in cost efficiencies. Understanding how different organizations tackled cost challenges can inspire readers to adopt similar approaches tailored to their specific needs.
Top Strategies Implemented:
Top strategies implemented represent the pinnacle of cost-effective measures in sectional cleaning. These tried-and-tested approaches have demonstrated their efficacy in not only reducing cleaning expenses but also enhancing overall cleanliness and maintenance standards. By highlighting the most successful strategies, readers can identify key methods that have consistently delivered results in various contexts. Implementing these top strategies can lead to sustainable cost savings and improved operational efficiency, making them invaluable assets for any facility or household management.
Industry Recommendations
Key Takeaways:
Industry recommendations distill collective wisdom and best practices from cleaning professionals and experts. These key takeaways encapsulate essential insights garnered from industry research, market trends, and real-world experiences. By following industry-recommended practices, readers can align their cleaning operations with proven methodologies that drive cost optimization and long-term sustainability. Embracing these key takeaways ensures a comprehensive approach to cleaning cost management, setting the foundation for achieving optimal results.
Long-Term Cost Control:
The focus on long-term cost control underscores the significance of implementing strategies that yield sustainable benefits over extended periods. By prioritizing long-term cost control measures, organizations and households can mitigate financial risks, safeguard resources, and maintain consistent cleaning standards. This proactive approach to cost management involves strategic planning, periodic assessments, and continuous improvement initiatives to foster cost-efficient practices. Investing in long-term cost control initiatives translates into enduring financial prudence and operational resilience, positioning entities for long-term success.