Intro
Raising a cement slab can be a complex task, often requiring a firm grasp of the methods available and the potential pitfalls involved. For homeowners and DIY enthusiasts, understanding the techniques and considerations before embarking on this endeavor is crucial. This guide aims to provide extensive information about the materials needed, the steps to follow, the tools involved, and troubleshooting tips.
Taking the time to learn about these aspects can lead to successful outcomes, enhancing the property value and ensuring safety. Here, we will break down the process into clear segments, starting with the essential materials required for slab raising.
Preamble to Slab Raising
Raising a cement slab is a crucial topic for property management and construction. It focuses on the integrity of structures. Foundations can settle over time due to several factors, leading to uneven surfaces. Addressing this issue is essential. Not only does it enhance safety, but it also improves aesthetics and functionality. Ignoring slab settling can lead to more severe problems. Thus, understanding the processes involved in slab lifting is necessary for informed decision-making regarding repair methods.
Understanding Slab Settling
Slab settling occurs due to shifting soil beneath a foundation. The weight of the slab compresses the soil, sometimes leading to a void beneath it. This void causes areas to sink. Additionally, environmental conditions, such as heavy rainfall, can accelerate this process. Poor drainage and soil composition also contribute. As a homeowner, recognizing these signs early can prevent more extensive damage. Unified structures are critical to long-term stability. Awareness of this concept makes it possible to take timely actions.
Common Causes of Slab Movement
There are several reasons for slab movement. Some of the most common include:
- Soil Erosion: Water can wash away the supporting soil, creating a weak foundation.
- Expansive Clay: In some regions, clay soil expands when wet and shrinks when dry, prompting movement.
- Tree Roots: Roots can penetrate and destabilize soil, causing the slab to shift.
- Foundation Issues: Settling related to initial construction flaws can be exacerbated over time.
Understanding these causes helps in prevention. By identifying factors affecting your cement slab, proactive measures can be taken to reinforce structures. Small changes can lead to significant improvements. This knowledge empowers homeowners to maintain their properties effectively.
Assessment of the Slab Condition
Assessing the condition of a cement slab is a crucial first step in the slab raising process. An accurate evaluation can significantly influence the method chosen for lifting the slab. Ignoring this step can lead to inappropriate techniques being used that may not address the root cause of the problem or, worse, result in further damage to the property.
There are several specific elements to consider during this assessment. First, it involves recognizing the signs of slab settlement. Common indicators include noticeable cracks in the surface, uneven elevation, or the presence of gaps between the slab and adjoining structures. Early detection can help to mitigate extensive repairs later. Additionally, reasons for the slab's movement need to be comprehended. External factors such as soil erosion, moisture levels, and tree roots can all contribute to settling issues.
Another significant aspect of this assessment is the benefit of identifying the underlying cause before proceeding with any lifting method. Each method of raising, whether it be mudjacking or foam injection, comes with its own set of prerequisites and suitability depending on the specific slab issues identified. A well-informed assessment promotes resource efficiency and might save homeowners from unnecessary expenditure.
Furthermore, comprehensive evaluation aids in understanding the longevity of the solution. If the causes of slab movement are not addressed, problems are likely to resurface after a lift. Therefore, a deep dive into the conditions surrounding the slab, along with inspection techniques, forms the foundation of effective slab raising.
Visual Inspection Techniques
Visual inspection is a straightforward yet effective method for assessing slab condition. Begin the inspection by walking around the slab, carefully observing its surface and surroundings. Look for visible signs of damage, such as chips, cracks, and discoloration.
Pay attention to the area where the slab meets walls or other adjoining structures. Gaps or irregularities in these connections can hint at settling. Note whether any drainage issues exist that may contribute to moisture buildup, further exacerbating the problem. This information can be used to guide further action.
In some cases, homeowner can take documentation of the issues through photographs for later reference. Key indicators can change over time, and maintaining records allows for better comparative analysis during future inspections.
Utilizing Leveling Tools
Utilizing leveling tools is essential for an accurate assessment. One effective tool is a leveling laser, which can provide a clear visual representation of any elevation changes across the slab. This type of equipment allows for precise measurement and identifies areas that require attention.
Alternatively, a simple two-foot level can also work for smaller inspections. Place the level across various points on the slab to determine any slopes or dips. Recording these measurements can help in selecting the most appropriate lifting method later on.
Moreover, various apps and software are available for smartphones that offer leveling features, enhancing the practicality of this assessment task.
These tools not only assist in the assessment but also reinforce the importance of the preparation phase before executing slab raising methods effectively. A thorough understanding of the current slab condition leads to better decisions regarding repairs and can prevent future complications.
Methods for Raising a Cement Slab

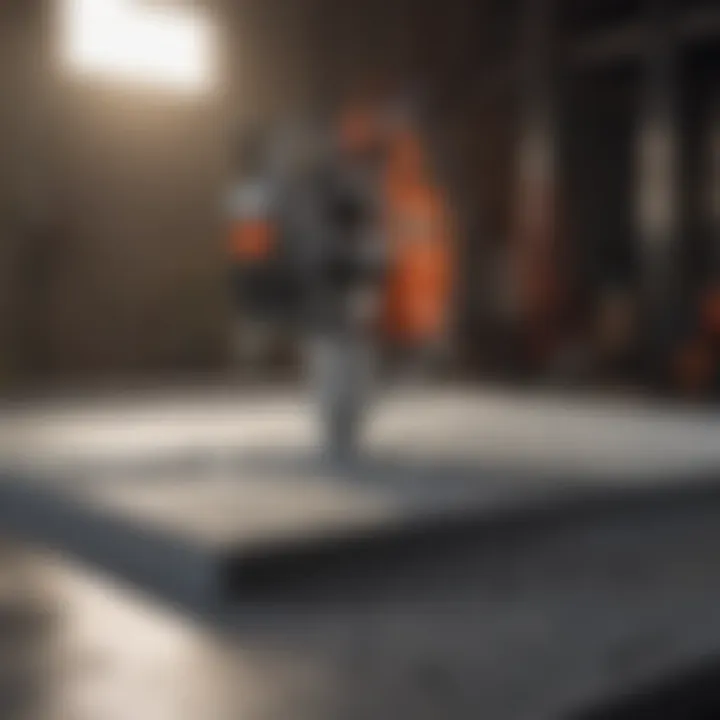
Raising a cement slab is a crucial procedure for many homeowners and property managers. It addresses uneven surfaces that can cause damage to structures and pose safety risks. Understanding the methods available for slab raising is essential in selecting the right approach for specific situations. Each method has unique benefits and considerations that can significantly impact the overall effectiveness and cost of the project.
In this article, we will examine three primary methods for raising cement slabs: mudjacking, polyurethane foam injection, and other innovative techniques. Picking the proper method is vital for successful results, and it should align with the specific needs of the property.
Mudjacking Overview
Mudjacking has been a common method for repairing uneven slabs. The process involves injecting a concrete slurry mixture beneath the slab to raise it back to its original position. This technique is effective for large areas and can restore the function of sidewalks, driveways, and patios.
The advantages of mudjacking include:
- Cost-effective compared to complete slab replacement.
- Quick process with minimal disruption.
- Long-lasting results when done correctly.
However, mudjacking also has downsides. The mixture might not bond as strongly to the existing concrete, leading to potential future issues. The visible holes created for injection, while typically small, may not appeal to all homeowners.
Polyurethane Foam Injection
Polyurethane foam injection is an innovative alternative to traditional mudjacking. This method uses high-density foam that expands upon injection, filling voids and lifting the slab. The benefits include:
- Lightweight; it reduces the risk of further settlement.
- Less invasive, requiring smaller holes for injection.
- Quick curing time, allowing for immediate use of the surface.
Many property owners find the foam injection method aesthetically pleasing, as the injection points are minimal. However, the initial cost can be higher, which can lead to hesitation among some homeowners.
Other Techniques and Innovations
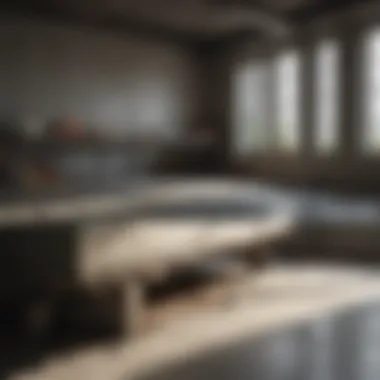
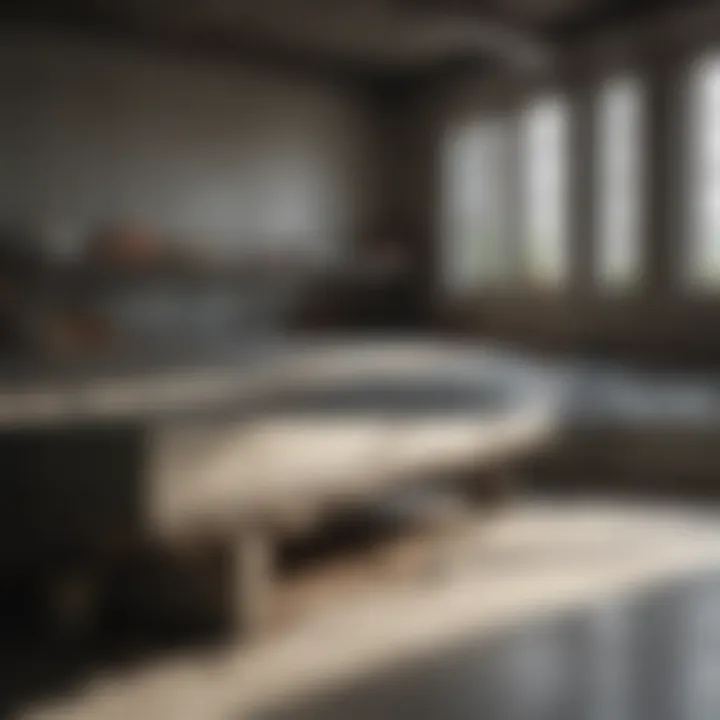
Apart from mudjacking and polyurethane foam injection, there are continuing innovations in the field. These might include methods like slab stabilization or the use of compaction grouts. Understanding new and upcoming technologies can provide options that may better fit specific needs.
Key considerations when exploring these methods:
- Soil conditions under the slab: This can affect stability and the choice of method.
- Future maintenance plans: How often will the area require attention?
- Environmental factors: Weather and climate can play a role in the effectiveness of certain techniques.
Mudjacking Explained
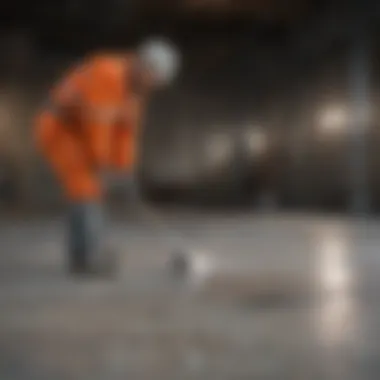
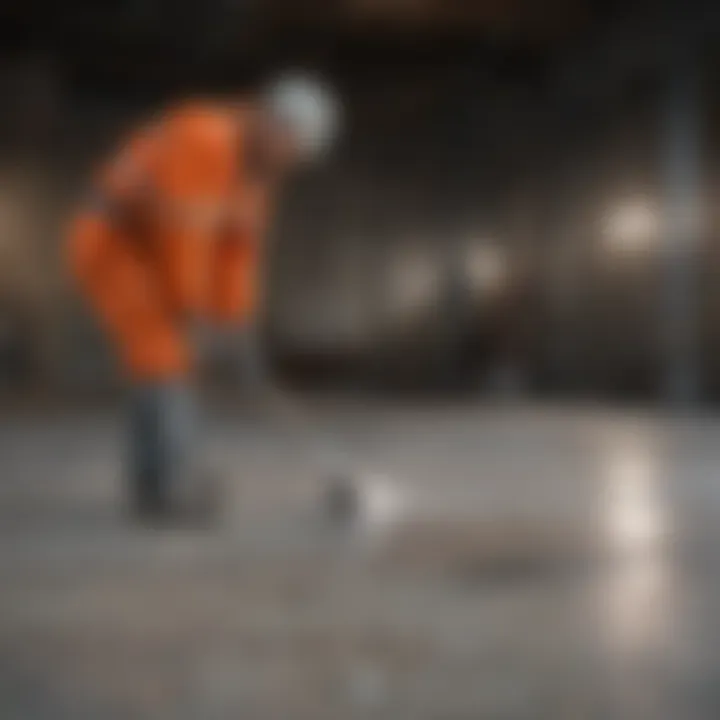
Mudjacking is a pivotal technique for restoring the level of cement slabs that have settled over time. It is essential to understand this method as it provides both a practical solution and a cost-effective approach to achieving structural integrity. Homeowners often face challenges with uneven surfaces that can lead to various issues, such as water drainage problems or safety hazards. Thus, mudjacking offers a remedial measure that is often less intrusive and more affordable than replacing the slab entirely.
Process and Equipment Involved
The mudjacking process involves several key steps that require careful execution. Initially, a thorough inspection of the slab's condition is conducted. This assessment helps to identify the areas needing elevation. The next phase involves drilling small holes in the concrete slab's surface to allow for the injection of the mud mixture.
Once the holes are ready, a specific mixture of cement, soil, and water is prepared. This mixture, commonly referred to as mud, is pumped under the slab at high pressure. The introduction of this material lifts the slab back to its desired level. Monitoring the process closely is crucial to ensure that the lifting occurs evenly and does not create additional stress on the surrounding structures.
The primary equipment used in mudjacking includes:
- Drilling Machines: For creating precise holes on the surface.
- Mud Pumps: To inject the mud mixture.
- Leveling Tools: To assess the height of the slab during the process.
Advantages and Disadvantages
Mudjacking carries several advantages but also comes with potential drawbacks. Understanding both sides can aid homeowners in making informed decisions.
Advantages:
- Cost-Effective: Compared to slab replacement, mudjacking typically costs much less.
- Quick Installation: The process can often be completed within a few hours, allowing homeowners to use their spaces sooner.
- Minimal Disruption: Mudjacking does not require large-scale construction, which helps preserve existing landscaping and surrounding structures.
Disadvantages:
- Limited Longevity: This method may not be a permanent solution, especially if the underlying soil continues to settle.
- Weather Dependent: Mudjacking may not be effective in very wet conditions, which can affect the curing of the material.
- Not Suitable for All Cases: Severely damaged or cracked slabs may not respond well to this technique, necessitating alternative solutions.
It's crucial to weigh these advantages and disadvantages to determine if mudjacking aligns with your specific needs and circumstances, especially considering the inherent property characteristics.
In summary, mudjacking is a viable option for homeowners seeking to remediate settled slabs effectively. Understanding the process and evaluating the pros and cons helps in making a prudent choice for maintaining structural integrity.
Polyurethane Foam Injection Detailed
Polyurethane foam injection has become a notable method in the realm of slab raising techniques. This approach stands out due to its efficiency and effectiveness in addressing the common issues associated with settling concrete. Unlike traditional methods, polyurethane foam not only fills voids but also expands, providing a unique advantage in stabilizing and lifting uneven slabs. In this segment, we will explore the mechanics of foam injection as well as its associated costs and overall efficiency.
How Foam Injection Works
Foam injection involves several key steps that highlight its practical application in slab lifting. Initially, small holes are created in the concrete slab, typically measuring around five-eighths of an inch in diameter. Through these holes, a special polyurethane foam mixture is injected. Once this material is introduced, it undergoes a chemical reaction that causes it to expand significantly, often up to 30 times its original volume.
While expanding, the foam effectively fills all voids beneath the slab, creating a supportive base that counteracts future settling. This process contributes to lifting the concrete slab back to its intended level. The foam cures quickly, often within minutes, allowing for minimal downtime and rapid usability post-injection.
Foam injection is also adaptable to various environments and is less invasive than other methods. Furthermore, it is lightweight, reducing the risk of further stress on the soil underneath the slab.
Evaluating Cost and Efficiency
When it comes to cost and efficiency, polyurethane foam injection presents a compelling option. The typical cost of foam injection can vary based on the size of the area to be treated and the depth of the voids. On average, homeowners may expect to spend between $1,000 and $3,000 for residential projects. This price range reflects the quick installation and the long-lasting results that foam can offer.
Several factors should be taken into account while evaluating the value of foam injection:
- Speed of application: As mentioned, foam cures quickly allowing property owners to regain access almost immediately.
- Durability: The longevity of foam makes it a cost-effective solution in the long run, as it does not require frequent reapplication.
- Minimal landscape disruption: The injection process causes less mess compared to mudjacking, maintaining a cleaner worksite post-operation.
"Investing in foam injection can save money on long-term repairs and prolong the life of the concrete slab, making it an attractive option for busy homeowners."
Choosing the Right Method
Selecting an appropriate method for raising a cement slab is critical for a successful outcome. Several factors influence this decision, including the type of settling, the surrounding environment, and the long-term durability desired. Choosing well not only ensures a stable surface but also optimizes costs and minimizes disruptions to daily life.
An informed approach to method selection can significantly affect the quality of the repair. It’s vital to understand each method’s strengths and weaknesses. Personalized evaluations help in making tailored choices that align with specific needs and expectations. Factors such as soil type, moisture levels, and slab load distribution offer essential clues for the right decision.
Factors Influencing Method Selection
When assessing methods for raising a cement slab, several factors come into play:
- Soil Condition: The type of soil beneath the slab influences which technique is most suitable. Soft or loose soil may require more supportive methods like mudjacking.
- Extent of Settling: If the slab has uneven settling, it may necessitate a more intensive approach, such as polyurethane foam injection.
- Cost Considerations: Budget constraints often dictate the choice of method. It is essential to consider both short-term and long-term costs associated with each option.
- Environmental Impacts: Some methods are more environmentally friendly than others. Evaluating how each method affects the surrounding landscape can guide your choice.
"The right method not only addresses the immediate issue but contributes to the longevity of the solution."
Selecting the right method should also involve reviewing customer feedback on different approaches. Historical performance data can provide valuable insights into what has worked effectively in similar situations.
Case Studies and Applications
Real-life examples provide context for method selection in various scenarios.
- Residential Properties: A case study of a home in a damp region illustrated the effectiveness of polyurethane foam injection. Homeowners faced issues with a settled slab under heavy moisture. The foam method allowed rapid lifting with minimal disruption.
- Commercial Buildings: In a commercial setting, mudjacking was employed to address significant settling in a parking structure. The method restored evenness without extensive downtime for the business, proving economical and efficient.
- Old Homes: Older properties often face unique slab challenges. A century-old house experienced foundation issues that were resolved with a careful combination of inspections and mudjacking. Professionals tailored the solution considering the historical integrity of the building.
Understanding these diverse applications underscores the importance of a thoughtful, case-sensitive approach to select the most fitting slab raising method.
Environmental Considerations
Raising a cement slab requires careful attention not just to the methods employed but also to the surrounding environment. Proper environmental considerations can make a significant difference in achieving effective slab raising while minimizing adverse effects on the landscape and maintaining compliance with local regulations. By understanding the implications of slab raising on nature, homeowners can ensure that their actions contribute to both structural integrity and ecological balance.
Impact on Landscape and Surroundings
When raising a cement slab, the impact on the surrounding landscape must be assessed. This includes evaluating how methods like mudjacking or foam injection may alter the topography or affect vegetation and drainage. Here are some key points to consider:
- Erosion: The activities involved in slab raising can disturb the soil, leading to potential erosion. It is essential to plan carefully, ensuring that any displaced material is managed to prevent runoff.
- Vegetation: Directly injecting material beneath a slab can affect root systems of nearby plants. Homeowners should survey vegetation that may be in proximity to the slab and take precautions to avoid damage or displacement.
- Water Drainage: Slab raising techniques can affect water flow. Proper regrading or adjustments may be necessary to ensure water drains away from the house rather than pooling around it.
Implementing practices that consider the landscape can preserve the natural beauty and functionality of the area.
Regulatory Compliance
Alongside environmental impacts, it is crucial to adhere to local regulations during the slab-raising process. Regulations are typically in place to protect both property owners and the environment. Key aspects of regulatory compliance include:
- Permits: Depending on the method chosen for slab raising, a permit may be required. Homeowners should check with local authorities to understand what is needed for their specific situation.
- Environmental Guidelines: Many areas have environmental protection guidelines that dictate how construction and restoration should take place. Adhering to these guidelines can prevent fines and ensure the project meets community standards.
- Safety Regulations: Regulations govern not only environmental factors but also safety practices. Ensuring that safety protocols are followed protects workers and residents during the slab lifting process.
Failing to comply with local regulations can lead to serious consequences, including fines, required removal of work done, or even legal trouble.
By addressing both the impact on the landscape and ensuring regulatory compliance, homeowners can not only enhance the safety and efficacy of slab raising but also contribute positively to their surroundings. This balanced approach fosters responsible property management and helps maintain the ecological integrity of the area.
Costs Associated with Slab Raising
Understanding the costs associated with slab raising is crucial for homeowners and property managers. Investing in this process can safeguard a property’s structural integrity and aesthetic appeal. Without comprehending these financial aspects, one might overlook important factors that contribute to overall satisfaction and value.
First, conducting a slab raising project requires awareness of several cost elements. Among these are labor costs, materials, equipment usage, and potential post-repair yard restoration. Each method, such as mudjacking and polyurethane foam injection, has its distinct pricing structures that affect the total project cost.
Understanding Pricing Structures
The pricing structure for slab raising can vary significantly depending on multiple factors.
- Method Chosen: The choice between mudjacking and foam injection usually affects the total cost. Mudjacking is typically less expensive than foam injection, which has advanced materials that can drive up prices.
- Size and Complexity of the Area: Larger and more complicated projects require more labor and materials, thus increasing costs. A simple patio might incur lower costs compared to a large driveway with extensive settling issues.
- Geographical Location: Prices can vary based on regional labor rates and material availability. Urban areas might inflate costs due to increased demands.
- Site Access: Difficult access or steep slopes might require special equipment, further impacting costs.
While estimating costs, it’s wise to request multiple quotes from professionals. This process aids in understanding the fair market value for services rendered.
Financial Implications for Property Owners
The financial implications of slab raising extend beyond immediate costs. Here are several important aspects homeowners should consider:
- Property Value: Well-maintained slabs enhance property value. A stable and visually appealing exterior can attract potential buyers.
- Avoiding Future Damage: Investing in slab raising may seem costly upfront, but neglecting this can lead to more severe problems. Cracks and deep settling can necessitate much larger repairs in the future.
- Insuring the Investment: Regular maintenance, including slab raising, can protect other investments in the property, like landscaping or foundations, therefore reducing overall costs in the long run.
"A small investment in slab raising today can save homeowners significant costs down the line."
In summary, understanding the costs associated with slab raising not only informs decision-making but also ensures that homeowners make prudent investments in their properties. This knowledge is essential for achieving desired outcomes and enjoying peace of mind with one’s home.
By considering these financial implications, property owners can prioritize slab raising to protect their investments and enhance their living spaces.
Safety and Risk Management
In the process of raising a cement slab, safety and risk management are essential. The work involved often requires heavy equipment and precise techniques that, if not managed properly, can lead to significant hazards. Proper attention to safety measures ensures not only the well-being of the workers but also protects the integrity of the structure being addressed. Neglecting safety considerations can result in injuries or even costly damages. Therefore, every phase of the slab raising process must be approached with a diligent focus on risk management.
Identifying Potential Hazards
Understanding potential hazards is the first step in risk management. During slab raising, several risks may arise, including:
- Injury from Equipment: Heavy machinery like hydraulic jacks or drilling tools can pose dangers to operators and bystanders.
- Ground Stability Issues: If the soil is not adequately assessed, it might collapse during lifting.
- Chemical Exposure: Certain methods, such as polyurethane foam injection, involve chemicals that can be hazardous if appropriate precautions are not taken.
- Noise Pollution: Operating machinery can produce loud sounds that may affect hearing if proper ear protection is not used.
The identification of these hazards allows for the implementation of proper planning. Workers should undergo safety training, including drills on what to do in emergencies. A thorough on-site assessment should also be conducted to evaluate the condition of the interaction zones, ensuring that all risks are recognized before starting any work.
Mitigating Risks during Procedure
Once potential hazards have been identified, it's crucial to take proactive steps to mitigate these risks. Here are some effective strategies to ensure safety during slab raising:
- Workplace Safety Gear: Always wear appropriate personal protective equipment, such as hard hats, gloves, and safety glasses. These tools can greatly reduce the risk of injury.
- Well-Maintained Equipment: Regularly inspect and maintain all equipment to ensure it operates safely and correctly. Damaged equipment should be repaired or replaced immediately to avoid malfunctions during operation.
- Clear Communication: Establish clear signals and communication paths among team members. A lack of communication can lead to accidents when multiple workers are operating heavy machinery in close proximity.
- Emergency Preparedness: Create an emergency plan that defines roles and actions if an incident occurs. This includes first aid procedures and emergency contact information.
- Supervision and Training: Ensure that experienced personnel supervise the procedure. All workers involved should enroll in safety training courses to understand the risks and safety practices specific to slab raising.
By implementing these strategies, the likelihood of accidents can be significantly reduced. A culture of safety encourages everyone involved to remain vigilant and proactive in maintaining a secure working environment.
The emphasis on safety during slab raising not only protects individuals but also ensures the success of the project.
The End
The conclusion of this article serves to encapsulate the pivotal insights into techniques for raising cement slabs. Understanding the potential challenges and methodologies discussed here is crucial for homeowners and property managers alike.
Effective slab raising is not merely an aesthetic concern; it directly impacts structural stability and property value. By investing time in thorough assessment and method selection, owners can avoid common pitfalls associated with slab settling. This understanding fosters informed decision-making, ultimately leading to cost-effective solutions and enhanced safety.
Moreover, the integration of safety protocols and risk management strategies cannot be overstated. As we highlighted, recognizing hazards and effectively balancing risks during slab lifting ensures a smoother process with minimal disruptions.
In sum, engaging with the techniques and considerations discussed in this article equips readers with the essential knowledge needed for slab raising projects.
Summary of Key Takeaways
- Importance of Assessing Condition: Regular examination of slab conditions aids in early detection of potential issues.
- Variety of Methods: Different techniques such as mudjacking and foam injection cater to specific needs and situations.
- Cost and Efficiency: Understanding economic implications helps in budgeting and planning effectively.
- Safety First: Prioritizing safety and recognizing risks is vital for a successful slab raising project.
Future Considerations in Slab Raising
As technology advances, innovations in slab raising techniques will likely emerge. Homeowners should remain informed about these trends and adaptations in the field. Ongoing education about material choices, environmental impacts, and regulatory standards will enhance not only the effectiveness of projects but also sustainability practices within property management.
Moreover, as urban landscapes evolve, the demand for effective solutions to combat settling will increase. Staying ahead by aligning with industry developments will aid homeowners in making informed choices that preserve the integrity of their properties for years to come.