Intro
Building a stick built garage can be an exciting endeavor. It offers a functional space for storage, vehicles, or even a workshop. However, understanding the associated costs is crucial for homeowners. Several factors intertwine to determine the total expense. By examining the materials required, labor costs, and other considerations like permits and location, you can make informed decisions for your project.
Materials:
When embarking on the construction of a stick built garage, selecting the right materials is vital. Each component contributes to the overall cost and quality of your project. Here’s a list of the essential materials needed, along with suggested quantities for an average two-car garage of approximately 24 feet by 24 feet:
-
Lumber: 2x4 framing (about 40 pieces), 2x6 for roof rafters (around 20 pieces), plywood for sheathing (about 35 sheets), and OSB for the flooring (about 10 sheets).
-
Roofing Materials: Asphalt shingles (around 20 bundles), roof underlayment (approximately 1,200 square feet), and ridge venting (around 30 feet).
-
Siding: Vinyl siding or wood siding – enough to cover about 1,200 square feet, typically calculated by the height and width of the garage.
-
Insulation: Fiberglass insulation batts (about 150 square feet for walls, depending on your choice of insulation thickness).
-
Doors and Windows: One garage door (consider 16x7 feet for two-car) and two windows (standard size 3x4 feet).
-
Paint and Primer: Enough to cover the siding and trim, generally 5 gallons of exterior paint and 2 gallons of primer, depending on surface area.
-
Concrete: Ready-mix concrete for the foundation slab, approximately 4 cubic yards, assuming a 4-inch thickness.
-
Miscellaneous Supplies: Nails, screws, caulking, and sealant for roofing. It’s wise to have these on hand.
DIY Steps:
Understanding the steps involved also aids in planning. Here, we detail a clear and structured approach:
-
Planning and Design: Start by deciding on dimensions and creating a basic blueprint. Research local building codes and regulations.
-
Site Preparation: Clear the area where the garage will stand, removing any debris or vegetation. Level the ground if necessary.
-
Laying the Foundation: Pour the concrete slab. Ensure it is level and smooth, allowing it to cure properly before proceeding.
-
Framing the Structure: Begin constructing the framework using the 2x4 and 2x6 lumber. Construct walls, ensuring they are square and plumb.
-
Sheathing and Siding: Attach plywood sheathing to the exterior walls. Afterward, install the siding once the sheathing is secure.
-
Roof Installation: Build the roof frame. Install the underlayment and then the shingles.
-
Windows and Doors: Cut out openings for your windows and doors. Install these components securely.
-
Insulation and Drywall: Insulate the garage walls. Hang drywall inside to finish the walls.
-
Painting: Apply primer and paint to both the interior and exterior surfaces.
-
Final Touches: Install lighting and outlets. Ensure everything is in working order to finalize the project.
Technical Aspects:

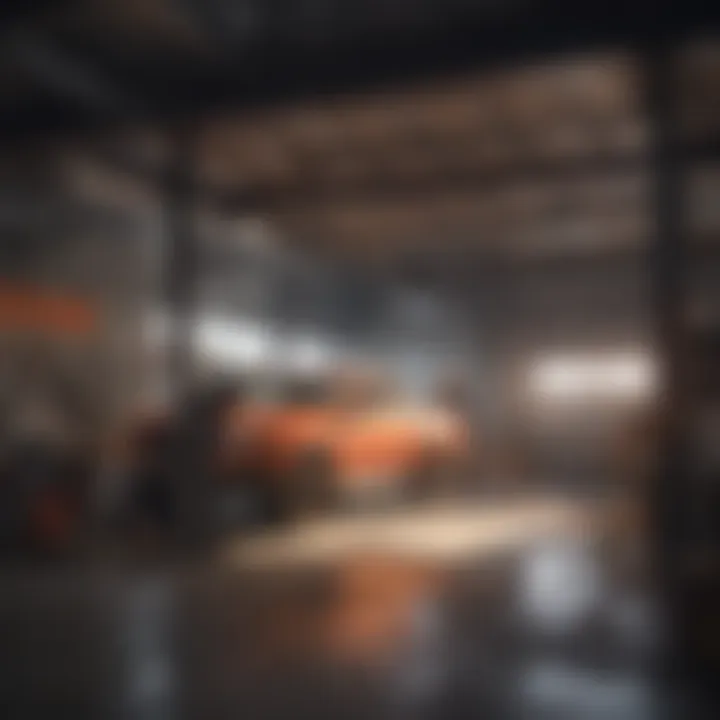
Several tools and techniques enhance the DIY experience. Here’s what you will need:
Tools:
- Circular saw
- Drill and drill bits
- Hammer
- Level
- Tape measure
- Safety goggles and gloves
- Ladder
Timing Specifics:
- Foundation: Allow 1-2 days for the concrete to cure.
- Framing and Sheathing: Typically 3-5 days, depending on help available.
- Roofing and Siding: Another week may be required, depending on the weather.
Techniques:
- Ensure all measurements are accurate before cutting.
- Use a square to maintain right angles.
- Regularly check for levelness as you build.
DIY Project Process:
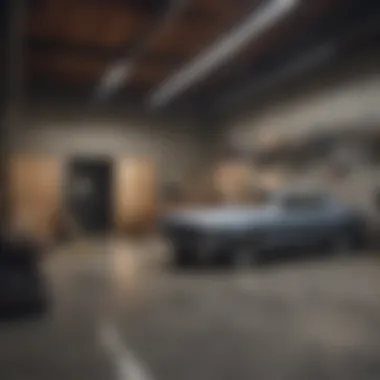
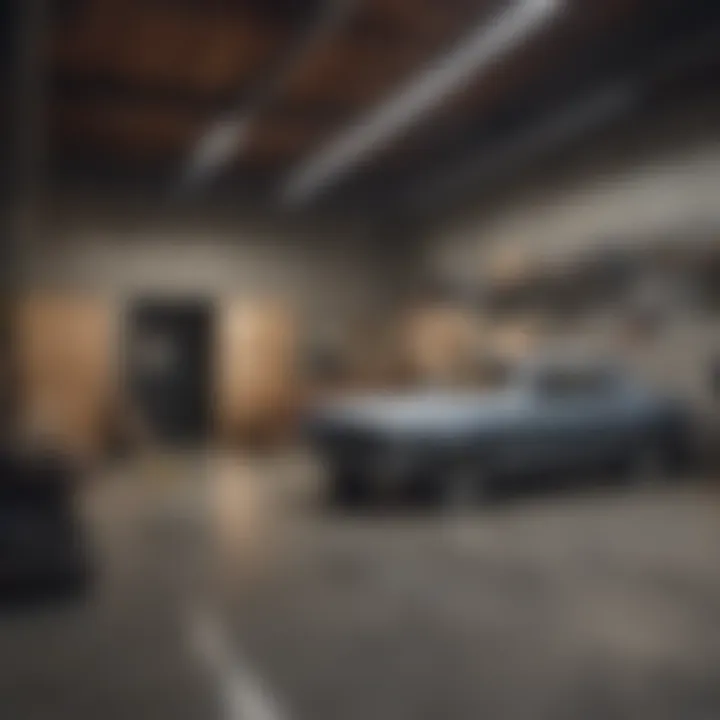
Each phase of the project has its specifics that demand attention:
- Start with a robust foundation as it determines the entire structure's stability.
- Utilize the correct angled cuts for framing, as miscalculations cause issues later.
- Take your time during roof installation; a well-crafted roof enhances durability.
Troubleshooting Tips:
- Misaligned Frames: If walls aren't plumb, adjust during framing stages.
- Leaks: Seal any gaps in windows and doors with quality caulk to avoid moisture infiltration.
- Squeaky Floors: If using wooden frames for the floors, add extra bracing between joists to prevent movement.
Understanding these aspects will ease your construction process and enhance the quality of your finished product.
Intro to Stick Built Garages
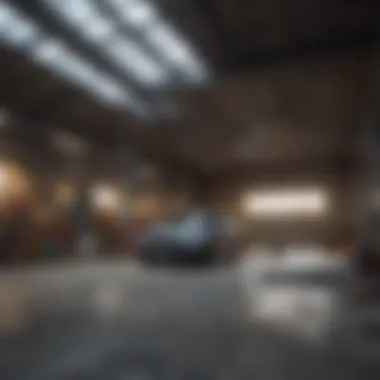
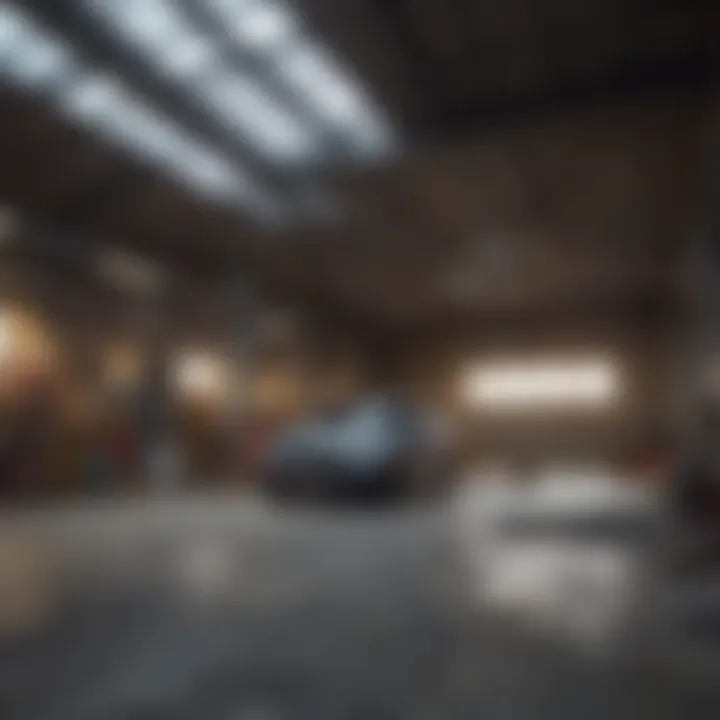
When considering home improvements, adding a garage is often not just a matter of convenience but also a means to increase property value. Stick built garages provide a versatile solution. This section delves into the significance of understanding stick built garages, focusing on what they offer and the factors that come into play during construction.
A stick built garage typically stands out for its assembly method, which is based on using wooden frames. This allows for customization with regard to size, layout, and design. One of the key benefits of this type of construction is its adaptability. Homeowners can choose specific features that align with their requirements and aesthetics.
Importantly, the stick built method usually results in a structure that integrates better with existing homes. Unlike pre-fabricated solutions, these garages can match the design and materials of the house, creating a more cohesive look. However, it is crucial to comprehend that costs can vary greatly based on decisions made during planning and building.
Several considerations also need attention, such as local regulations, site conditions, and material selections. Understanding these factors will empower homeowners to make informed choices, ultimately leading to an efficient construction process.
"Understanding the characteristics of stick built garages allows homeowners to navigate costs and maximize benefits."
Through the subsequent sections, we will explore the various elements influencing the costs associated with these garages. From average costs, material breakdowns, labor expenses, and more, readers will gain comprehensive insight into stick built garage construction.
Defining Stick Built Construction
Defining stick built construction is crucial for understanding the cost of building a garage. This method of construction refers to a framing technique where wooden beams and studs form the structure. It is a traditional approach that has been prevalent in residential construction for decades. This method offers various advantages which can ultimately impact the cost of your garage.
One of the most significant benefits of stick built construction is its adaptability. Homeowners can customize every aspect of their garage, from the size to the layout. This flexibility allows for a wide range of designs that cater to specific needs. Moreover, stick built structures can be easily modified or expanded in the future, fundamentally enhancing their utility and longevity.
Cost-wise, stick-built construction is often more affordable compared to other methods such as poured concrete or prefabricated kits. The availability of lumber and skilled labor in many areas plays a significant role in maintaining competitive pricing. However, it is essential to consider that fluctuations in lumber prices can influence overall costs. Understanding this aspect will help homeowners make informed decisions regarding their budget.
When discussing stick built garages, it is also important to address insulation and energy efficiency. Wood is naturally an insulator, providing better thermal performance than metal structures. This quality promotes energy savings over time, helping to minimize heating and cooling expenses in your garage.
Key considerations in stick built construction include:
- Building Codes: Always check local building codes to ensure compliance.
- Design Preferences: Consider personal aesthetics and functionality needs.
- Structural Longevity: Understand how certain materials and techniques can impact durability.
Finally, the social aspects of stick built construction should not be overlooked. Engaging local contractors who specialize in this construction method increases investment in the community and fosters local economies. Understanding the significance of stick built construction is more than just a financial aspect; it encourages a deeper appreciation for craftsmanship and quality in the home-building process.
Stick built garages offer uniquely customizable options that adapt to homeowner needs, making them a popular choice despite fluctuating material costs.
Cost Overview of Stick Built Garages
Understanding the financial aspect of building a stick built garage is crucial. This section outlines the key costs involved in the process. A comprehensive grasp of these figures helps in budgeting accurately and making informed decisions. Knowing the cost breakdown can also facilitate discussions with contractors and assist in identifying potential areas for savings.
Average Cost Range
When planning for a stick built garage, it's important to establish an average cost range. The total expenses can vary significantly based on several factors, such as location, size, and materials used. For instance, on average, the cost to build a stick built garage can range from $15,000 to $30,000. This estimate typically includes the materials, labor, and basic finishes.
In addition to the standard costs, you should also consider:
- Size: A larger garage will naturally incur higher costs due to more materials and labor.
- Custom Features: Adding windows, insulation, or specific roofing styles can increase overall expenses.
- Location: Prices may vary depending on local construction rates and regulations.
It’s essential to contact local builders for detailed quotes specific to your area.
Factors Influencing Pricing
Various elements can impact the pricing of a stick built garage. Here are the main factors to consider:
- Location: Local building codes and availability of materials can affect costs.
- Labor Costs: The wage rates in your area significantly influence overall expenses. Hiring skilled labor might increase costs but could also improve quality.
- Materials: Prices for lumber, roofing, and other materials can fluctuate. It’s wise to track these changes before committing to purchase.
- Design Complexity: More complex designs typically contribute to higher labor and material costs.
- Permits and Inspections: Local regulations often require permits, which add to the overall cost.
- Time of Year: Costs may increase during peak construction season due to higher demand.
"Budgeting for your garage is not just about the initial investment; think of future expenses too, like maintenance and updates."
By considering these factors, homeowners can better navigate the costs associated with a stick built garage.
Material Costs Breakdown
In the construction of a stick built garage, material costs are a significant factor that can greatly influence the overall budget. Understanding the specifics of these costs can help homeowners make informed decisions during their planning process. This section will delve into the primary materials involved in building a garage, offering insights into their pricing dynamics and market considerations.
Selecting the right materials not only affects the initial cost but also impacts the longevity and maintenance of the structure. As the project moves forward, fluctuations in material costs due to supply chain issues or regional pricing variances can also affect the final expenditure. Here are the main areas of focus:
- Quality of materials often dictates the cost, with higher quality options providing better durability and aesthetic appeal.
- Local market conditions can greatly affect prices; understanding these can lead to smarter buying decisions.
- Project specifics, such as size and design complexity, also play a role in determining the amount and type of materials required.
Lumber Prices
Lumber is essential for the framework of a stick built garage. The price of lumber varies widely based on multiple factors, including type, thickness, and market demand.
For instance, plywood and dimensional lumber are common choices in garage construction. Currently, prices fluctuate depending on seasonal demand and market availability. Recent trends have shown significant price spikes due to supply chain disruptions, making it essential to budget accordingly.
Homeowners should consider purchasing lumber from local suppliers, as this can sometimes result in lower transportation costs. It's also wise to check for any industry discounts or bulk purchasing options.
Roofing Materials
The roofing materials contribute not only to the structural integrity of the garage but also to its aesthetic appearance. Options include asphalt shingles, metal roofing, and tiles. Each material presents different pricing structures and longevity profiles.
- Asphalt shingles are typically more affordable and easy to install, averaging lower initial costs.
- Metal roofing, while usually more expensive upfront, may offer advantages in durability and energy efficiency long-term.
- Tiles can provide a unique look but may come with higher installation costs due to their weight and complexity.
Evaluating weather conditions and local styles can guide the choice of roofing material. Understanding the balance between upfront costs and eventual maintenance can help prioritize spending.
Foundation Materials
Foundation materials are critical to ensuring a stable base for the garage. Concrete is the most common choice, but costs vary based on thickness and preparation requirements.
-
Concrete slab foundations are often seen as the standard, providing a solid base and good moisture resistance. The costs can increase with additional features like insulation or drainage systems.
-
Footings and piers may also be necessary depending on soil conditions; they require extra materials and labor, thereby influencing the total budget even further.
It’s important to consult with a contractor regarding the best foundation type suitable for your geographical area and soil conditions, as this knowledge can prevent unforeseen expenses down the road.
Labor Costs Involved
Labor costs are a crucial element when constructing a stick built garage. These expenses can significantly affect the total cost of the project. Understanding labor costs helps homeowners budget effectively and make informed decisions.
Hiring a Contractor
When hiring a contractor, it is essential to choose one with experience in garage construction. They should offer detailed quotes that include all aspects of the labor involved. Typical rates for contractors may vary based on location and the complexity of the project.
Benefits of Hiring a Contractor:
- Expertise: Contractors often have necessary skills and knowledge to handle unexpected challenges.
- Time Efficiency: They can complete the project faster than most homeowners due to their experience.
- Quality Assurance: A licensed contractor typically guarantees workmanship, reducing stress for the homeowner.
However, hiring a contractor can also lead to higher costs. Always ask for references and review previous work to ensure quality.
DIY vs. Professional Help
Deciding between DIY and hiring professional help can be a significant choice that impacts both cost and outcomes.
DIY Approach:
- Cost Savings: Doing the work yourself can save on labor costs.
- Control: You have full control over the project timeline and the finishing touches.
Nevertheless, the DIY approach requires a strong skill set and considerable time. Mistakes can lead to costly corrections, which might negate any savings.
Professional Help:
- Stress Reduction: Hiring professionals relieves stress, allowing homeowners to focus on other priorities.
- Faster Completion: Experienced workers can often finish the job more quickly.
Ultimately, the decision between DIY and professional assistance depends on the homeowner’s skills, available time, and how comfortable they are with the construction process.
Permits and Regulatory Costs
Understanding the permits and regulatory costs associated with constructing a stick built garage is critical for anyone considering this project. Compliance with local laws ensures that the garage meets safety standards, thereby protecting both the structure and the residents. Failing to secure the necessary permits can lead to legal repercussions and potentially costly fines. Engaging with this topic allows homeowners to plan effectively, avoiding unexpected issues during construction.
Understanding Zoning Laws
Zoning laws dictate how a property can be used and what can be built on it. For garage constructions, these regulations vary significantly from one municipality to another. Homeowners need to check local zoning ordinances to understand specific requirements such as setbacks, height restrictions, and permitted uses.
Having a clear grasp of your local zoning laws can help in several ways:
- Property Usage: It defines what types of structures are allowed in your area.
- Setbacks: There might be requirements for how far from property lines your garage should be located.
- Height Limits: Some neighborhoods impose restrictions on the height of buildings.
Before beginning any construction, consult your local zoning office to gather all relevant information. Not following these regulations could lead to your garage being deemed illegal, forcing you to make costly modifications or even remove it entirely.
Permit Fees
Permit fees are a necessary part of the construction process. These fees vary depending on the size, purpose, and location of your garage. The fees contribute towards ensuring that the construction complies with building codes and local regulations.
Here are some common considerations related to permit fees:
- Varied Costs: Depending on your locality, permit fees can range from a few hundred dollars to over a thousand. Factors influencing this include the garage size, the complexity of the project, and regulatory considerations.
- Additional Inspections: Many permit applications require multiple inspections during and after construction. Each inspection may incur additional fees.
- Time Frame: Obtaining the necessary permits can take time. It's wise to factor this delay into your overall project timeline.
Before commencing with your garage construction, account for these permit fees in your budget. This preparation can prevent financial strain later on and ensure a smooth construction process.
Site Preparation Costs
Site preparation is a fundamental stage in the construction of a stick built garage. Without proper site preparation, issues may arise that compromise the integrity and longevity of the structure. This section lays out key elements involved in site preparation, its benefits, and important considerations for homeowners.
Clearing the Land
Clearing the land is often the first step in site preparation. This involves removing any obstacles such as trees, shrubs, rocks, or debris from the area where the garage will be built. Many people may overlook this phase, but it is crucial. A clear site allows for easier access for construction vehicles and reduces potential hazards during the build.
Factors to keep in mind during this process include:
- Cost of Removal: Hiring professionals to clear large trees or extensive brush can add to the budget.
- Disposal Fees: Consider where the debris will go. Some jurisdictions charge for disposal, which can add costs.
- Environmental Regulation: Be aware of local regulations regarding tree removal or soil disturbance.
Leveling and Grading
Once the land is cleared, the next important step is leveling and grading the site. This process involves adjusting the slope of the land to ensure proper drainage and a stable foundation. A level garage is essential for its functionality and aesthetic value.
Criteria to assess include:
- Drainage Control: Ensure that rainwater will not pool around the foundation, as this can lead to water damage.
- Soil Stability: Proper grading helps to compact the soil which prevents settling or shifting.
- Foundation Construction: A well-leveled site simplifies the foundation building process, which can save time and labor costs.
Through careful site preparation, homeowners can facilitate a smoother construction process that leads to better results with their stick built garage. Investing in this phase reduces the risk of future problems and enhances the structure's overall value.
Important Note: Engaging a licensed contractor for site preparation often pays off in the long run. They have the expertise to address potential issues before construction begins.
Comparative Analysis with Other Garage Types
Understanding the differences between stick built garages and other types, such as prefabricated and metal garages, is essential for homeowners. This analysis not only aids in cost evaluation but also helps in matching the garage type with the intended use, aesthetic preferences, and regional climate. By comparing these options, homeowners can make informed decisions that align with their financial planning and functional requirements.
Stick Built vs. Prefabricated Garages
Stick built garages typically involve traditional building methods using lumber and are often customized to the owner’s specifications. In contrast, prefabricated garages are manufactured off-site and then assembled on location. The key distinctions between these two project types are as follows:
- Cost Factors: Stick built garages generally have higher labor costs due to the on-site construction process. Prefabricated garages may offer lower overall costs since they come ready-made and require less labor to set up.
- Customization: Stick built options allow extensive design flexibility. Homeowners can choose materials, layout, and finishes that suit their stylistic preferences. Prefabricated garages, while they come in various styles, often have limited customization options and predefined designs.
- Construction Time: Stick built garages take longer to complete. This may extend timelines for those in a hurry. Prefabricated garages usually require less time since components are pre-made, allowing for quicker assembly.
In summary, while stick built garages offer personalization and potential longevity, prefabricated garages focus more on ease and speed of construction, appealing to those needing a practical solution.
Stick Built vs. Metal Garages
Metal garages, often made from steel or aluminum, provide a contrasting option to traditional stick built structures. This comparison highlights several important factors:
- Durability: Metal garages typically exhibit greater resistance to weather impacts and pests compared to wood. They often stand firmer against storms and decay. Stick built garages, however, may require regular upkeep to avoid issues such as termites or rot.
- Maintenance: Overall, stick built garages may incur higher maintenance costs due to the nature of wood, which requires treatment against various environmental factors. Metal garages are generally less expensive to maintain as they do not require the same protective measures.
- Aesthetic Appeal: Stick built garages tend to blend seamlessly with traditional homes, offering a more visually pleasing appearance. Metal options may not always complement certain home styles, depending on the surrounding architecture.
Ultimately, the choice between stick built and metal garages hinges on personal preferences, with considerations ranging from budget and functionality to visual alignment with the existing property.
Long-term Cost Considerations
When constructing a stick built garage, it is crucial to think beyond the initial expenditure. Long-term cost considerations play a significant role in ensuring your investment is worthwhile. You should not only focus on what it will cost to build the structure, but also what it will require in terms of maintenance and its potential impact on property value over time. Understanding these aspects will help homeowners make informed choices about their garages.
Maintenance Expenses
Maintenance is an ongoing commitment that homeowners must account for. Even high-quality materials and construction come with their own set of upkeep requirements. Stick built garages usually involve regular checks on roofing, siding, and foundation integrity. These areas can be susceptible to wear and tear, especially in regions with harsh weather conditions. Notably, here are some common maintenance tasks you might face:
- Roof Repairs: Maintaining the roof is essential to prevent leaks and water damage. Regular inspections can help you identify issues early.
- Siding Upkeep: Wooden or vinyl siding may require cleaning or repainting to sustain its appearance and durability.
- Foundation Maintenance: A stable foundation is crucial. Cracks or shifts can lead to costly repairs if not addressed promptly.
Keeping track of these maintenance expenses can prevent unexpected financial burdens in the future. Setting aside a budget dedicated to maintenance will ensure that your stick built garage remains in excellent condition, thus preserving its functionality.
Potential Increases in Property Value
Investing in a stick built garage can also contribute positively to your property value. A well-constructed and maintained garage can appeal to future buyers, offering them additional storage or workspace. Various factors influence how much value a garage can add:
- Quality of Construction: Higher-quality materials and skilled labor typically lead to a more valuable structure.
- Versatility of Use: Homeowners often see garages as multi-functional spaces. A garage can serve as a workshop, hobby area, or even a storage facility.
- Market Demand: Depending on your local real estate market, having an added garage can be a selling point that attracts buyers.
Adding a stick built garage can yield significant return on investment, especially when considering resale value.
Financing Options for Garage Construction
Understanding financing options is essential for homeowners considering the construction of a stick built garage. This decision impacts not just the up-front costs, but also future financial obligations. Knowing the various methods to fund this project can empower homeowners to make informed choices that suit their budgets and financial strategies.
Home Equity Loans
Home equity loans are a popular choice for financing home improvements, including the construction of garages. This option allows homeowners to borrow against the equity they have built in their homes. The main advantage of a home equity loan is the generally lower interest rates compared to other loan types. Moreover, the interest on these loans may be tax-deductible, offering potential financial benefits.
However, there are important considerations to be aware of. To qualify for a home equity loan, homeowners typically need to have a significant amount of equity in their property. This means that those who have recently purchased their home may not be eligible. Additionally, since the garage will become a part of the property, any failure to repay the loan could risk foreclosure. Homeowners must assess their financial situation carefully before proceeding with this option.
Personal Loans
Personal loans provide another feasible option for financing garage construction. Unlike home equity loans, personal loans are unsecured, meaning they do not require collateral. This can be an attractive feature for those who might not want to put their home at risk. Personal loans can also be obtained with a quick approval process, making them suitable for homeowners looking to start their project swiftly.
However, personal loans usually come with higher interest rates than home equity loans. This can mean higher monthly payments, which could strain a homeowner's budget. Borrowers should also be mindful of their credit score, as it can significantly influence the terms and rates they are offered.
In evaluating financing options, homeowners must weigh the pros and cons of each approach based on their specific financial situation and long-term goals.
Culmination
Firstly, understanding the total costs involved—from materials to labor and permits—equips homeowners with the necessary tools to plan and budget effectively. It is not merely about initial expenses; ongoing considerations like maintenance and potential value appreciation of property should be taken into account. This perspective facilitates smarter decision-making, specifically ensuring that financial resources are allocated wisely.
Moreover, the discussion on financing options lays the groundwork for an informed approach to funding the garage project. Options such as home equity loans and personal loans provide various pathways for managing payment, depending on individual financial situations. Evaluating these choices can lead to substantial savings or more favorable repayment conditions.
Lastly, the comparative analysis with other garage types empowers homeowners to contrast not only the costs but also the benefits of stick built garages against alternatives like prefabricated or metal garages. This nuanced understanding directs the choice toward what best suits their needs, preferences, and long-term goals.
"A well-planned project can result in not only a functional garage but also increased property value and enhanced lifestyle."
In summation, this comprehensive insight into the costs associated with stick built garages illuminates a pathway for informed planning and decision-making. Potential garage builders should analyze the factors highlighted in this article, enabling them to turn their construction dreams into reality.