Materials:
- 2 quarts of lawn mower engine oil
- 1 new air filter
- 1 spark plug wrench
- 1 oil filter wrench
- 1 oil pan
- Clean rags
- Safety gloves and goggles
DIY Steps:
- Begin by locating the oil drain plug underneath the lawn mower.
- Place the oil pan beneath the drain plug to catch the old oil.
- Unscrew the drain plug using the appropriate wrench and let the oil drain completely.
- Once the oil has drained, remove the old oil filter using the oil filter wrench.
- Inspect the filter area for any debris and clean it with a rag.
Technical Aspects:
- Timing: Plan for at least 30 minutes to complete the oil change process.
- Tools: Ensure you have the spark plug wrench and oil filter wrench for efficiency.
- Critical Techniques: When installing the new oil filter, make sure it is securely tightened to prevent leaks.
DIY Project Process:
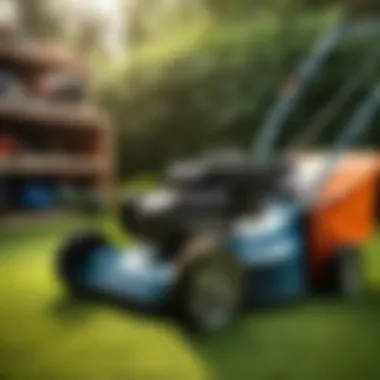
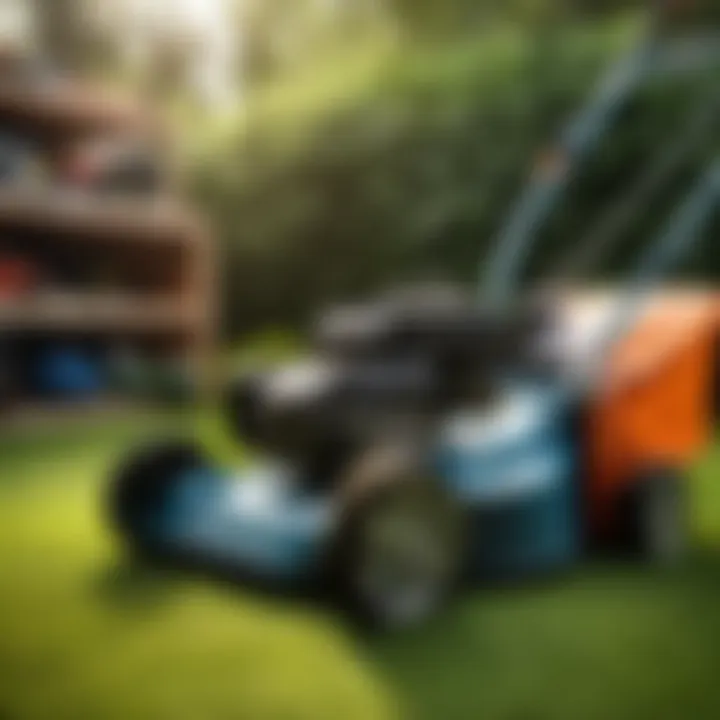
- Install the new oil filter by twisting it on clockwise until snug.
- Replace the drain plug and tighten it to prevent leaks.
Troubleshooting Tips:
- If you encounter resistance when removing the oil filter, apply gentle pressure and twist carefully to avoid damage. Be sure to dispose of the used oil and filter properly.
Understanding Customer Needs
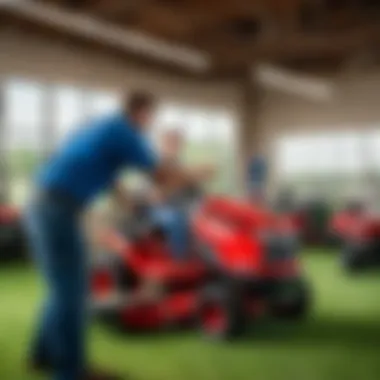
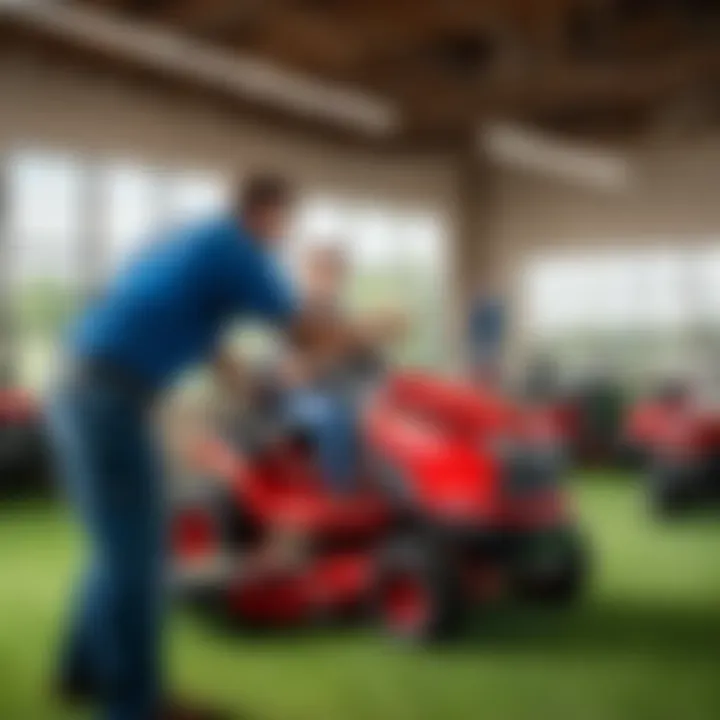
Conducting Customer Surveys
Designing Effective Surveys
Designing effective surveys plays a paramount role in garnering valuable insights into customer preferences and expectations. These surveys serve as a direct line of communication between customers and the repair center, enabling a structured approach to gather feedback. The key characteristic of designing effective surveys lies in their ability to generate specific data pertinent to enhancing service offerings, repair processes, and overall customer experience. This method is a chosen strategy in this article due to its effectiveness in uncovering actionable feedback for continuous improvement. The unique feature of designing effective surveys lies in their capacity to capture nuanced feedback, providing in-depth understanding rather than surface-level responses. While advantageous in gathering detailed insights, designing effective surveys may require careful structuring to avoid overwhelming respondents with excessive questions.
Analyzing Survey Results
Analyzing survey results is a critical stage that follows the process of conducting surveys. It involves dissecting the gathered data to extract meaningful patterns, trends, and areas for enhancement. This analytical process aids in identifying recurring themes, areas of improvement, and customer preferences, thus contributing to informed decision-making within the repair center. The key characteristic of analyzing survey results is its role in transforming raw data into actionable strategies, enabling targeted improvements based on validated feedback. This approach is favored in this article for its ability to translate feedback into tangible operational enhancements. The uniqueness of analyzing survey results lies in its capacity to translate qualitative data into quantifiable metrics, facilitating structured decision-making. While advantageous in providing actionable insights, analyzing survey results requires a systematic approach to ensure accurate interpretation and implementation.
Customer Feedback Analysis
Identifying Common Repair Requests
The process of identifying common repair requests underscores the significance of recognizing prevalent issues and sought-after repair services. By analyzing the most frequent repair requests, repair centers can streamline their service offerings, prioritize stocking essential parts, and optimize repair procedures. The key characteristic of this process lies in its ability to identify trends in customer demands, facilitating proactive responses to common repair needs. This method is a popular choice in this article due to its efficacy in tailoring service provisions to align with customer expectations. The unique feature of identifying common repair requests lies in its predictive nature, enabling repair centers to anticipate future demands and stay ahead of market trends. While advantageous in optimizing service delivery, identifying common repair requests necessitates continuous monitoring and adaptation to evolving customer needs.
Addressing Customer Pain Points
Addressing customer pain points revolves around mitigating customer dissatisfaction by identifying and resolving sources of frustration or inconvenience in the repair process. By acknowledging and addressing pain points, repair centers can enhance customer experience, build loyalty, and establish a reputation for exceptional service. The key characteristic of addressing customer pain points is its focus on empathetic customer engagement, swift issue resolution, and proactive service adjustments. This strategy is beneficial for this article as it emphasizes the importance of empathizing with customers and delivering solutions that alleviate their concerns. The unique feature of addressing customer pain points lies in its ability to turn negative experiences into positive customer interactions, fostering long-term relationships and brand advocacy. While advantageous in enhancing customer satisfaction, addressing customer pain points requires a commitment to ongoing improvements and responsive customer service.
Enhancing Technical Skills
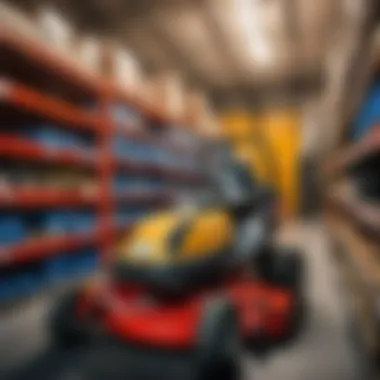
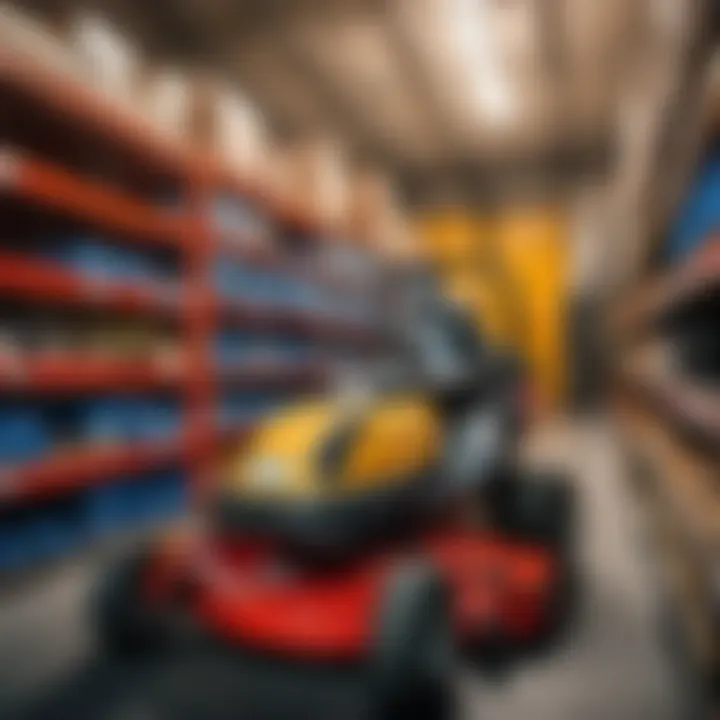
Enhancing technical skills is a crucial aspect of optimizing the operations of a lawn mower repair center. In this article, we delve deep into the significance of honing technical expertise to ensure efficient and top-notch repair services for customers. By focusing on enhancing technical skills, repair center staff can tackle a wide range of issues effectively, leading to improved customer satisfaction and business reputation.
Training Programs
Implementing Training Modules
Implementing training modules plays a pivotal role in developing a knowledgeable and skilled workforce within a repair center. These modules are designed to provide structured learning opportunities for staff members, covering various aspects of lawn mower mechanics and repair techniques. By incorporating specialized training modules, repair center employees can stay up-to-date with the latest industry trends and best practices, ultimately enhancing the quality of service provided to customers.
Certification Programs
Certification programs offer repair center employees the opportunity to gain recognized credentials in the field of lawn mower repair. These programs not only validate the expertise of staff members but also instill a sense of confidence and trust among customers. By completing certification programs, employees demonstrate their commitment to continuous learning and professional development, setting a high standard for repair center operations.
Skill Development Workshops
Hands-on Repair Practice
Hands-on repair practice allows staff members to apply theoretical knowledge in a practical setting, honing their skills through real-life repair scenarios. This hands-on approach not only increases proficiency but also boosts confidence and efficiency when handling customer equipment. Incorporating hands-on repair practice ensures that repair center staff are well-equipped to address a diverse range of repair challenges promptly and effectively.
Advanced Troubleshooting Techniques
Introducing advanced troubleshooting techniques empowers repair center employees to diagnose and resolve complex issues efficiently. By mastering advanced techniques such as diagnostic tools and problem-solving strategies, staff members can offer comprehensive solutions to customers, enhancing the overall service quality. Adopting advanced troubleshooting techniques sets a repair center apart by showcasing an advanced level of technical expertise and problem-solving ability.
Efficient Inventory Management
Efficient inventory management is a critical component of optimizing operations at a lawn mower repair center. It plays a vital role in ensuring that the center has the right parts available at the right time, thereby minimizing downtime and improving overall efficiency. By carefully managing inventory, repair centers can streamline their processes, reduce costs, and enhance customer satisfaction.
Inventory Assessment
Regular Inventory Audits
Regular inventory audits are an essential practice in the efficient management of a repair center's inventory. By conducting regular audits, repair centers can accurately track the availability of parts, identify any discrepancies, and maintain optimal inventory levels. This proactive approach helps in preventing stockouts, avoiding overstock situations, and ensuring that the right parts are always ready for repairs. While regular inventory audits require dedicated time and effort, the benefits in terms of improved inventory accuracy and cost savings make them a sound investment for any repair center.
Identifying Fast-Moving Parts
Identifying fast-moving parts is another crucial aspect of inventory assessment. By recognizing which parts are in high demand and frequently used for repairs, repair centers can prioritize stocking these items to ensure quick turnaround times. Fast-moving parts often represent a significant portion of a repair center's revenue, making their efficient management vital for profitability. By accurately forecasting demand for these parts, repair centers can optimize their inventory levels, reduce holding costs, and improve overall operational efficiency.
Supplier Relationships
Negotiating Bulk Discounts
Negotiating bulk discounts with suppliers can be a strategic way to cut costs and improve profitability in a repair center. By purchasing parts in larger quantities, repair centers can often secure lower prices per unit, leading to significant cost savings over time. Establishing strong supplier relationships built on trust and reliability can facilitate favorable negotiations for bulk discounts, creating a win-win situation for both parties involved. While the initial investment in bulk purchases may seem daunting, the long-term benefits of reduced costs and increased margins make it a worthwhile strategy for repair centers.
Timely Orders Placement
Timely orders placement is imperative for maintaining efficient inventory levels and meeting customer demand promptly. By placing orders proactively based on demand forecasts and repair trends, repair centers can prevent stockouts and avoid unnecessary inventory holding costs. Timely orders placement also helps in streamlining procurement processes, minimizing lead times, and ensuring a continuous supply of parts for repair technicians. While the coordination of timely orders may require precise inventory management software and effective communication with suppliers, the benefits of optimized inventory levels and improved customer service far outweigh the associated challenges.
Streamlining Repair Processes
Workflow Optimization
Standardizing Repair Procedures
Standardizing repair procedures is essential in harmonizing the repair process across all service cases. This approach involves creating a standardized set of steps to be followed for each type of repair, ensuring that no essential task is overlooked or completed haphazardly. One key characteristic of standardizing repair procedures is the establishment of a clear and predictable workflow, which helps technicians work more efficiently and minimizes errors in the repair process. In the context of this article, standardizing repair procedures is a beneficial choice as it promotes consistency, quality control, and customer satisfaction. Despite its advantages, one potential disadvantage of standardization is the rigidity it may introduce to the repair process, which could hinder flexibility in addressing unique repair scenarios.
Implementing Quality Checks
Implementing quality checks involves integrating checkpoints at critical stages of the repair process to ensure that each task meets predefined quality standards. This proactive approach helps identify and rectify any deviations or issues promptly, resulting in enhanced repair outcomes and customer satisfaction. The key characteristic of implementing quality checks lies in its ability to uphold a high standard of repair quality and prevent subpar service delivery. In the context of this article, implementing quality checks is a popular choice due to its effectiveness in maintaining repair quality and customer trust. However, a potential disadvantage of this practice is the additional time and resources required to perform these checks, which could impact overall repair efficiency.
Appointment System
Online Booking Platforms
Online booking platforms play a crucial role in facilitating customer appointments and managing repair center schedules effectively. By allowing customers to book repair services online, repair centers can streamline the appointment booking process, reduce waiting times, and improve overall customer experience. The key characteristic of online booking platforms is their convenience and accessibility, making it easier for customers to secure repair services at their convenience. In the context of this article, online booking platforms are a beneficial choice as they promote customer convenience, reduce administrative workload, and increase service efficiency. Despite their advantages, one potential disadvantage of online booking platforms is the need for technological infrastructure and maintenance to ensure seamless operation.
Efficient Scheduling
Efficient scheduling is critical for optimizing resource utilization and meeting customer demands promptly. By implementing efficient scheduling practices, repair centers can allocate resources effectively, reduce waiting times, and maximize operational efficiency. The key characteristic of efficient scheduling lies in its ability to minimize idle time and ensure that repair tasks are completed in a timely manner. In the context of this article, efficient scheduling is a popular choice for its role in enhancing repair center productivity, customer satisfaction, and overall operational effectiveness. However, one potential disadvantage of efficient scheduling may arise if unforeseen repair complications disrupt the predefined schedule, leading to delays and potential customer dissatisfaction.
Building Customer Trust
Transparency
Transparency is the cornerstone of building customer trust within a lawn mower repair center. By providing detailed repair reports, repair centers can offer customers insight into the work done on their machines. This transparency builds credibility and reassures customers that the repair center is honest and accountable. Detailed repair reports outline the diagnosis, parts replaced, and work completed, giving customers a clear understanding of the service performed.
Providing Detailed Repair Reports
Providing detailed repair reports is essential for customer satisfaction and trust. These reports highlight the specific repairs conducted, the associated costs, and any recommendations for future maintenance. By offering this level of detail, repair centers demonstrate professionalism and commitment to customer service. Customers value transparency and appreciate the information provided in these reports, which helps in creating a transparent and trustworthy relationship.
Clear Communication with Customers
Clear communication with customers is another key component of building trust. Effective communication ensures that customers are kept informed throughout the repair process, from initial assessment to completion. Repair centers that prioritize clear communication build rapport with their customers, establish expectations, and address any concerns promptly. Good communication fosters trust and shows customers that their needs and feedback are valued.
Warranty Policies
Warranty policies play a significant role in enhancing customer trust within a repair center. Customers value clear and understandable warranty terms that protect their investment in mower repairs. By explaining warranty terms clearly and honoring warranty claims, repair centers can instill confidence in their services and demonstrate their commitment to customer satisfaction.
Explaining Warranty Terms Clearly
Explaining warranty terms clearly is essential for customer understanding and satisfaction. Customers appreciate clarity regarding what is covered under warranty, duration, and any conditions or limitations. Clear explanations help customers make informed decisions and feel secure in their choice of repair center. When warranty terms are communicated effectively, customers are more likely to trust the repair center and return for future services.
Honoring Warranty Claims
Honoring warranty claims is a testament to a repair center's integrity and dedication to customer satisfaction. When repair centers promptly and fairly handle warranty claims, they reinforce their commitment to quality service and customer care. By standing behind their warranty policies, repair centers show accountability and build trust with customers, leading to positive relationships and recommendations.