Materials:
- Bricks: 500 pieces of standard size bricks measuring 3"x4"x8" for a brick wall project
- Mortar mix: 20 bags of high-quality mortar mix suitable for bricklaying
- Sand: 5 cubic yards of fine sand to be mixed with mortar
- Water: Sufficient amount for proper mortar consistency
- Brick ties: 100 pieces of stainless steel brick ties for wall stability
DIY Steps:
- Site Preparation: Clear the work area of debris, ensuring a clean and level surface for construction
- Foundation Layout: Mark the foundation layout using string lines and stakes, following precise measurements for accuracy
- Mortar Mixing: Combine mortar mix, sand, and water in a wheelbarrow, following manufacturer's instructions for the right consistency
- Bricklaying: Lay bricks systematically, starting from corners and using a level to ensure each course is plumb and level
- Joint Finishing: Tool the mortar joints neatly for a professional finish
Technical Aspects:
- Tools: Brick trowel, jointer, level, tape measure, wheelbarrow, mortar board
- Timing: Allow mortar to set for 24 hours before further construction
- Techniques: Buttering bricks properly for strong adhesion, striking joints consistently for uniformity
DIY Project Process:
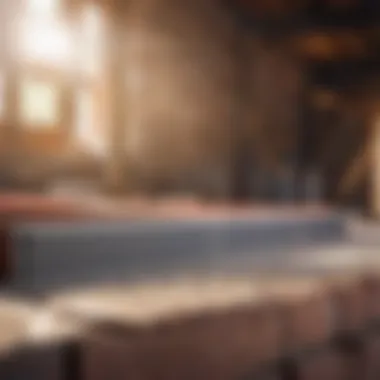
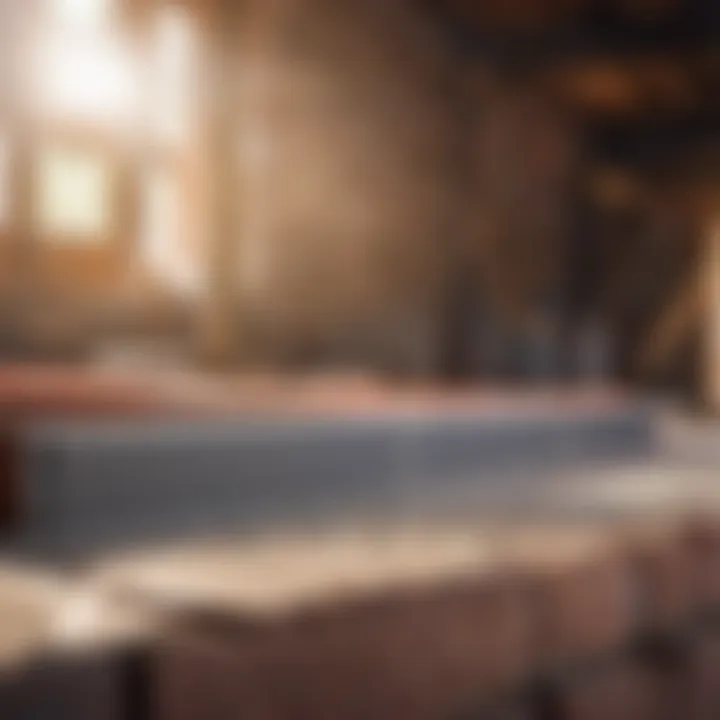
-
Sequential Steps:
- Lay the first course of bricks, applying mortar on the foundation
- Continue stacking the bricks, staggering joints for structural integrity
- Install brick ties at designated intervals for wall reinforcement
-
Troubleshooting Tips:
- If mortar dries too quickly, mist the bricks with water to slow the drying process
- Adjust brick placement immediately if misaligned to prevent structural issues
Labor Costs
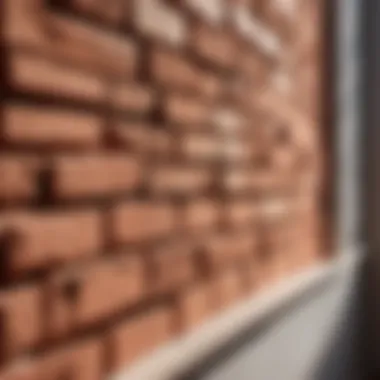
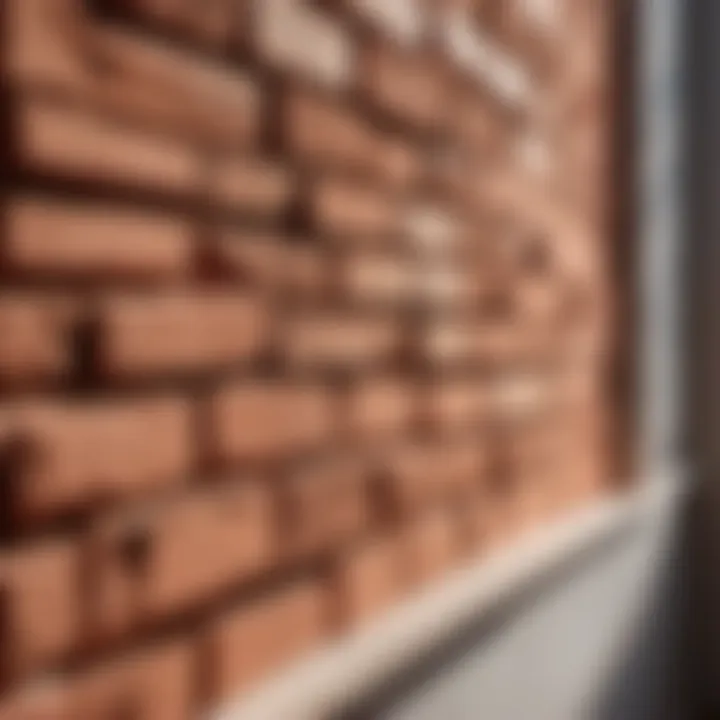
Labor costs play a pivotal role in understanding the overall expense incurred when hiring a bricklayer. In this article, labor costs are explored in depth to provide a nuanced perspective on the financial implications associated with engaging bricklaying services. By delving into labor costs, individuals can gain valuable insights into the breakdown of expenses, ensuring a well-informed approach to budgeting for their project.
Hourly Rates
Factors Influencing Hourly Rates
Factors influencing hourly rates are a crucial aspect to consider when evaluating the cost of hiring a bricklayer. These factors encompass various elements such as the skill level of the bricklayer, market demand, complexity of the project, and geographical location. Understanding these factors allows individuals to make informed decisions about budget allocation and negotiation strategies, ultimately impacting the overall project cost.
Regional Disparities
Regional disparities in hourly rates highlight the varying cost structures across different geographical areas. Factors such as labor market conditions, living expenses, and demand-supply dynamics contribute to these disparities. By acknowledging and assessing regional differences, individuals can adjust their budget expectations accordingly, ensuring optimal cost management for their bricklaying project.
Day Rates
Considerations for Day Rates
Day rates involve a unique set of considerations that influence the overall cost of hiring a bricklayer on a daily basis. Factors like project duration, scope, complexity, and additional services impact day rates significantly. By carefully evaluating these considerations, individuals can strategically plan and budget for the daily expenses associated with bricklaying, fostering cost-effective decision-making.
Impact of Project Scale
The impact of project scale on day rates underscores the correlation between project size and cost implications. Larger projects often require more time, resources, and manpower, leading to increased day rates. Understanding how project scale influences costs enables individuals to anticipate potential budget variations based on the size and scope of their bricklaying endeavor, facilitating effective financial planning.
Project Quotations
Bespoke Quotes
Bespoke quotes offer tailored pricing strategies that cater to the specific needs and requirements of individual projects. These personalized quotes take into account project intricacies, material preferences, design specifications, and client expectations. By opting for bespoke quotes, individuals can ensure a customized approach to cost estimation, aligning the budget with the desired outcomes of their bricklaying project.
Standardized Packages
Standardized packages provide pre-defined pricing structures for common bricklaying services, offering fixed rates for standard project requirements. These packages often include predetermined services, materials, and timelines, simplifying the quoting process for both clients and bricklayers. While standardized packages offer simplicity and clarity in pricing, they may limit customization options based on specific project needs and preferences.
Material Expenses
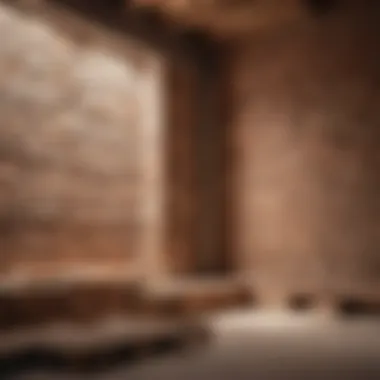
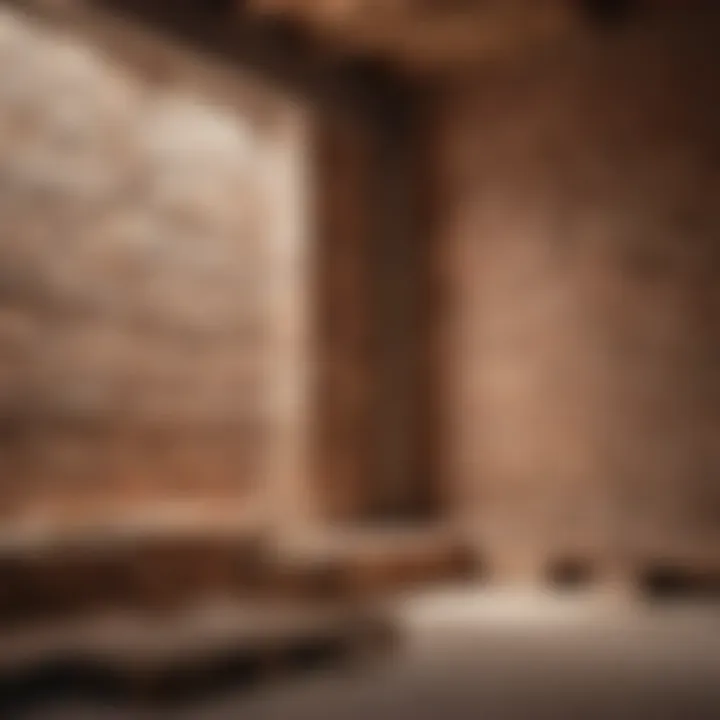
In this article, understanding material expenses is crucial as it forms a significant part of the overall cost breakdown when hiring a bricklayer. Material expenses encompass the costs associated with the bricks, mortar, adhesives, and other supplies necessary for the successful completion of a bricklaying project. For individuals planning a construction or renovation project involving brickwork, being knowledgeable about material expenses ensures an accurate budget allocation and helps avoid unexpected financial burdens. Without a clear grasp of material costs, it can be challenging to control the overall expenditure and achieve the desired outcome.
Brick Types
Cost Variation Across Brick Types
Exploring the cost variation across different types of bricks is pivotal in understanding material expenses deeply. The cost variation is influenced by factors such as the quality, aesthetics, and durability of the bricks. Each type of brick comes at a distinct price point based on its composition and manufacturing process. By comprehending these cost variances, individuals can make informed decisions that align with their budget while also meeting their design preferences and structural requirements. Choosing the right brick type based on cost variation ensures a balance between affordability and architectural appeal.
Quality Differences
The quality differences among brick types play a critical role in material expenses. Higher-quality bricks generally come at a premium price due to their superior strength, weather resistance, and longevity. While opting for high-quality bricks might incur higher upfront costs, their durability can result in long-term savings by reducing the need for frequent repairs or replacements. Understanding the quality disparities allows individuals to prioritize durability and performance, leading to a more sustainable and cost-effective bricklaying investment.
Mortar and Adhesives
Impact on Overall Budget
The choice of mortar and adhesives significantly impacts the overall budget of a bricklaying project. Different types of mortar and adhesives vary in price and performance, influencing the project's cost effectiveness and structural integrity. Selecting high-quality mortar and adhesives may increase upfront expenses but can enhance the project's durability and aesthetics over time, minimizing maintenance costs in the long run. By considering the impact on the overall budget, individuals can make informed decisions that encompass both quality and financial sustainability.
Choosing the Right Products
Choosing the right mortar and adhesives is essential for optimizing material expenses. Factors such as adhesive strength, weather resistance, and compatibility with the chosen bricks should be taken into account when selecting these products. By prioritizing quality and suitability over cost alone, individuals can ensure a reliable and visually appealing brickwork finish. Making informed choices in mortar and adhesive selection promotes efficient project execution, reduces potential rework, and enhances the overall value of the bricklaying endeavor.
Additional Costs
Equipment Rental
Essential Tools and Machinery
The procurement of essential tools and machinery holds paramount importance in the realm of bricklaying projects. These tools encompass a wide array of implements vital for the precise and efficient execution of bricklaying tasks. From trowels and levels to mixers and scaffoldings, each tool serves a distinct purpose in ensuring the quality and durability of the final structure. The characteristic that distinguishes essential tools and machinery lies in their specialized functionality tailored to the intricate requirements of bricklaying. Their utilization not only enhances productivity but also upholds the standards of craftsmanship essential in bricklaying endeavors. However, while these tools are indispensable for the completion of projects, their maintenance and proper handling demand meticulous attention to ensure optimal performance throughout the construction process.
Rental Options
When considering equipment rental as a viable option for accessing necessary tools and machinery, the benefits and advantages become apparent. Rental options provide a cost-effective alternative to outright purchase, preventing the burden of long-term ownership costs. Moreover, by opting for equipment rental, individuals can access a diverse range of specialized tools and machinery tailored to specific project requirements. This flexibility in selection enables project managers to adapt swiftly to changing project dynamics and scale operations accordingly. Despite the advantages rental options offer, one must also consider potential limitations such as availability constraints and adherence to rental terms and conditions. By evaluating the pros and cons of equipment rental, individuals can strategically incorporate this aspect into their financial planning for bricklaying projects, ensuring a balanced approach to resource allocation for optimal outcomes.
Permits and Inspections
Regulatory Requirements
Navigating the landscape of regulatory requirements is fundamental in the context of bricklaying projects. Compliance with building codes, permits, and regulations is imperative to legal and safe construction practices. Regulatory requirements encompass a spectrum of mandates ranging from structural integrity standards to environmental sustainability guidelines. By adhering to these regulations, individuals not only ensure the legal validity of their projects but also contribute to the overall safety and durability of the constructed edifice. The distinctive feature of regulatory requirements lies in their non-negotiable nature, mandating strict adherence to established norms to avoid legal repercussions and project delays. Despite the constraints regulatory requirements impose, their alignment with industry standards and best practices fosters a culture of quality and accountability within the bricklaying domain.
Financial Planning
Amidst the myriad considerations involved in bricklaying projects, financial planning emerges as a critical aspect influencing project viability and sustainability. Effective financial planning entails a thorough assessment of budgetary requirements, resource allocations, and contingency provisions to mitigate financial risks. The key characteristic of financial planning lies in its proactive approach towards resource management and expenditure control, optimizing the utilization of financial resources for maximal project benefit. By incorporating financial planning strategies, individuals can monitor and regulate project finances efficiently, ensuring cost-effectiveness and financial stability throughout the construction phase. However, potential disadvantages such as budget constraints and unforeseen expenses underscore the importance of dynamic financial planning to adapt to evolving project demands and financial dynamics.
Cleanup and Disposal
Waste Management Fees
Addressing waste management fees is imperative in the post-construction phase of bricklaying projects. Proper disposal of construction waste is essential for maintaining cleanliness, safety, and environmental sustainability on-site. Waste management fees encompass the costs associated with waste removal, recycling, and disposal, reflecting the environmental consciousness and responsible construction practices. The key characteristic of waste management fees lies in their direct correlation to the volume and nature of waste generated during construction activities. By implementing efficient waste management strategies, individuals contribute to sustainable construction practices and regulatory compliance, fostering a culture of environmental stewardship within the bricklaying industry.
Post-Project Cleaning
The final stage of a bricklaying project involves post-project cleaning, a crucial activity that ensures the aesthetics and functionality of the constructed structure. Post-project cleaning encompasses thorough cleaning, debris removal, and site restoration to present the project in its completed state. The unique feature of post-project cleaning lies in its transformative impact on the project's visual appeal and usability, setting the stage for project delivery and client satisfaction. Despite its undeniable benefits, post-project cleaning may pose challenges such as time constraints and resource allocation, necessitating strategic planning and coordination to execute cleaning activities efficiently. By prioritizing post-project cleaning, individuals uphold the standards of craftsmanship and presentation characteristic of successful bricklaying projects, solidifying their reputation for quality and excellence in construction.
Cost Management Strategies
Budget Allocation
Prioritizing Expenditure
Prioritizing expenditure is a vital aspect of effective budget allocation when hiring a bricklayer. By carefully assessing the various expenses involved in a bricklaying project, individuals can strategically allocate funds to critical areas, ensuring smooth progress and timely completion. The key characteristic of prioritizing expenditure lies in identifying the most significant cost components and allocating resources accordingly. This method is a popular choice for this article as it allows individuals to focus on essential aspects such as labor, materials, and additional costs, thereby optimizing the overall budget. The unique feature of prioritizing expenditure is its ability to minimize unnecessary spending and enhance cost-effectiveness, ultimately contributing to a well-managed bricklaying project.
Contingency Planning
Contingency planning is another essential element of budget allocation when hiring a bricklayer. In an industry where unexpected challenges and costs can arise, having a contingency plan in place is crucial for mitigating risks and ensuring financial stability throughout the project. The key characteristic of contingency planning is its proactive approach to anticipating potential obstacles and setting aside resources to address them promptly. This method is a beneficial choice for this article as it empowers individuals to prepare for unforeseen circumstances, thereby reducing the impact of sudden budget fluctuations. The unique feature of contingency planning lies in its ability to provide a safety net for financial uncertainties, offering peace of mind and confidence in handling any financial challenges that may arise.
Negotiation Tactics
Effective Communication
Effective communication plays a fundamental role in successful negotiation tactics when hiring a bricklayer. By maintaining clear and transparent communication with the bricklayer regarding project requirements, expectations, and budget constraints, individuals can establish a foundation of trust and collaboration. The key characteristic of effective communication is its ability to foster mutual understanding and alignment between the parties involved, facilitating smoother negotiations and potential cost savings. This method is a popular choice for this article as it promotes constructive dialogue and problem-solving, ultimately leading to more favorable terms and agreements. The unique feature of effective communication is its capacity to prevent misunderstandings and conflicts, ensuring a productive working relationship throughout the project.
Leveraging Competitive Quotes
Leveraging competitive quotes is a strategic tactic for negotiating competitive rates when hiring a bricklayer. By obtaining multiple quotes from different providers and comparing their offerings, individuals can leverage this information to secure favorable pricing and terms. The key characteristic of leveraging competitive quotes is its emphasis on market research and price benchmarking, enabling individuals to make informed decisions based on competitive market rates. This method is a beneficial choice for this article as it empowers individuals to advocate for fair pricing and tailored solutions, maximizing the value of their investment. The unique feature of leveraging competitive quotes lies in its potential to drive cost efficiencies and quality enhancements, creating a win-win situation for both parties involved.
Tracking Expenses
Financial Monitoring Tools
Financial monitoring tools are indispensable for tracking expenses when hiring a bricklayer. By utilizing specialized software or apps to monitor and analyze project costs in real-time, individuals can gain valuable insights into their expenditure patterns and performance metrics. The key characteristic of financial monitoring tools is their ability to provide accurate and up-to-date financial data, enabling proactive decision-making and cost optimization. This method is a beneficial choice for this article as it empowers individuals to stay on top of their budget and expenditure, fostering greater control and accountability. The unique feature of financial monitoring tools is their capacity to streamline financial processes and enhance transparency, facilitating better financial outcomes and project success.
Real-Time Adjustments
Real-time adjustments are a proactive measure for adapting to changing financial circumstances when hiring a bricklayer. By continuously evaluating project expenses and performance metrics, individuals can make timely adjustments to their budget allocation and resource utilization, ensuring financial efficiency and project continuity. The key characteristic of real-time adjustments is their responsiveness to dynamic market conditions and project needs, enabling individuals to pivot quickly and effectively. This method is a popular choice for this article as it supports agile decision-making and risk management, thereby safeguarding against budget overruns and delays. The unique feature of real-time adjustments lies in their capacity to foster adaptability and resilience, empowering individuals to achieve their financial goals and project milestones effectively.