Materials:
- Torque wrench (1/4-inch drive)
- Torque wrench (1/2-inch drive)
- Torque wrench (3/8-inch drive)
- Calibration tool
- Safety goggles
- Work gloves
- User manual
- Protective case
- Pen and notepad
Step-by-Step Instructions:
-
Choose the Right Torque Wrench: Depending on the project requirements, select the appropriate size of torque wrench (1/4-inch, 1/2-inch, or 3/8-inch drive).
-
Calibrate the Torque Wrench: Before use, ensure the torque wrench is calibrated correctly using the calibration tool as per the manufacturer's instructions.
-
Wear Safety Gear: Put on safety goggles and work gloves to protect yourself during the project.
-
Refer to the User Manual: Familiarize yourself with the torque wrench's user manual for specific guidelines and settings.
-
Store Properly: When not in use, store the torque wrench in its protective case to prevent damage.
Technical Aspects:
- Tools: Torque wrench, calibration tool, safety goggles, work gloves
- Timing: Follow project-specific timing guidelines for torque application
- Techniques: Ensure a firm grip on the torque wrench, apply gradual pressure for accurate readings
Sequential Steps:
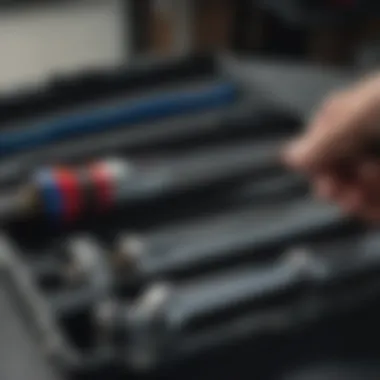
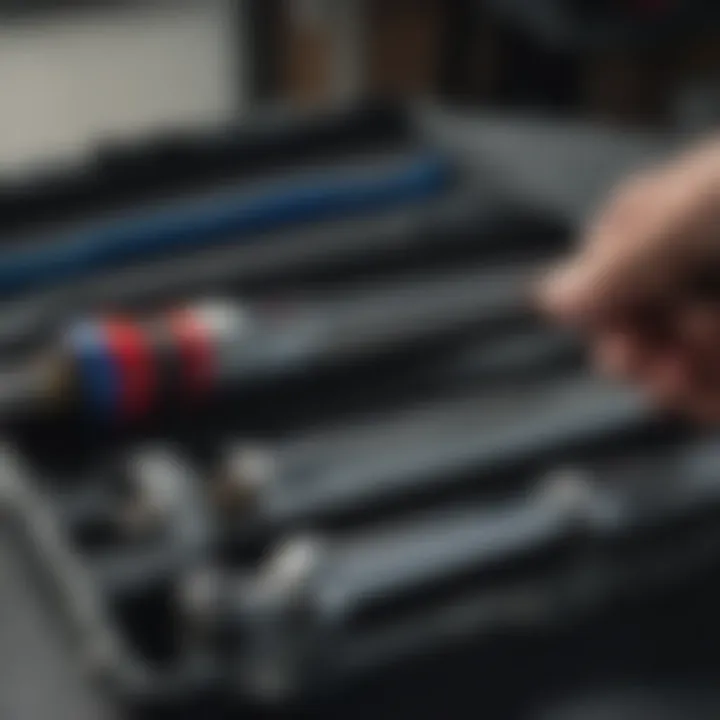
-
Setting Up: Position the torque wrench at the starting point on the fastener.
-
Applying Torque: Slowly turn the torque wrench until the desired torque setting is reached.
-
Debrief Process: After torque application, review the achieved results and make necessary adjustments if required.
Troubleshooting Tips:
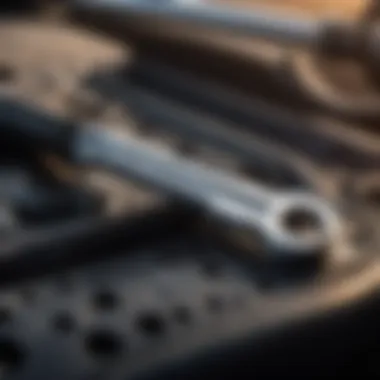
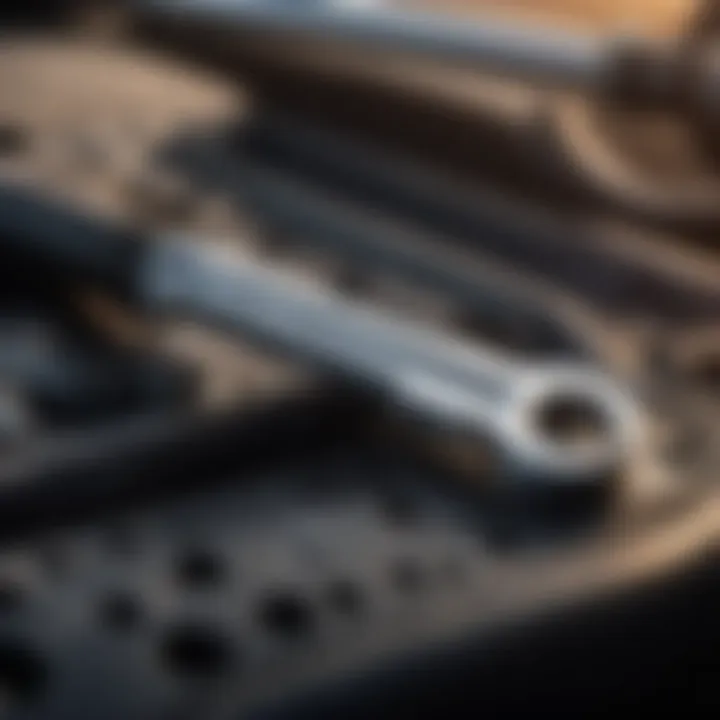
- Over-Torque: If you exceed the recommended torque, back off and retighten gradually.
- Under-Torque: If the torque applied is insufficient, reapply torque until the correct setting is reached.
Introduction
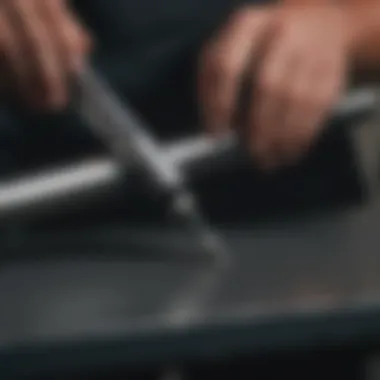
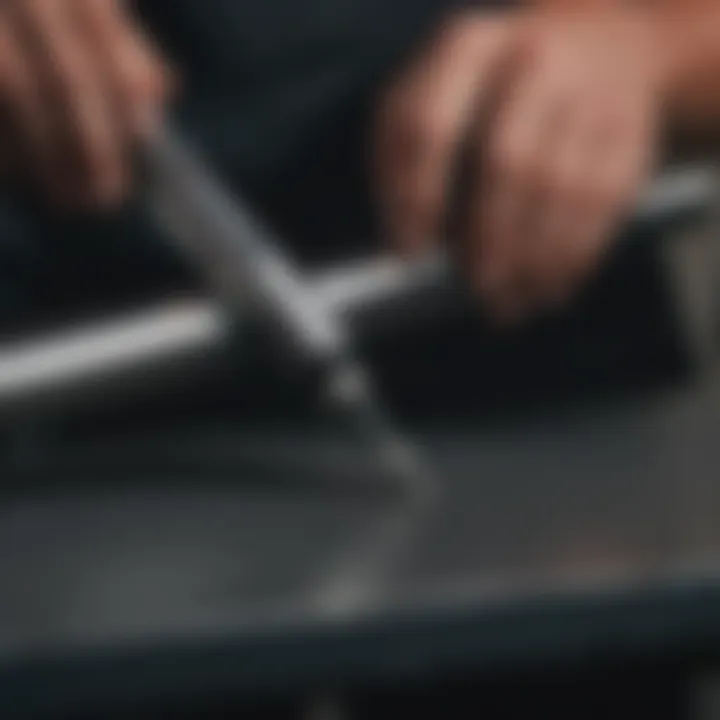
In the realm of mechanical work, precision is paramount, and understanding the dynamics of torque wrench measurement is crucial. This article aims to navigate readers through the intricate science of torque wrenches, shedding light on their significance in ensuring the accuracy and safety of mechanical operations. An in-depth exploration of various aspects such as types of torque wrenches, calibration methods, common mistakes to avoid, and best practices will equip readers with a holistic understanding necessary for success in their mechanical endeavors.
Definition of Torque Wrenches
Understanding torque and its measurement importance
To grasp the essence of torque wrenches, one must first comprehend the fundamental concept of torque and its pivotal role in mechanical processes. Torque refers to the measure of rotational force applied to an object; thus, precise torque measurement is vital for achieving desired outcomes in tightening or loosening applications. The ability to accurately gauge torque not only ensures mechanical integrity but also prevents damage and enhances operational efficiency. Emphasizing the importance of understanding torque and its measurement significance sets the foundation for mastering torque wrench operation in this article.
Types of Torque Wrenches
Click-Type Torque Wrench
The Click-Type Torque Wrench stands out as a popular choice for its straightforward operation and distinct audible click indication of reaching the preset torque value. Known for its reliability and ease of use, this torque wrench is favored in various mechanical settings for its ability to provide precise torque application with a user-friendly approach. Its unique feature lies in the audible click sound upon reaching the desired torque, a practical advantage in ensuring accurate fastening without the need for visual confirmation. However, users should be cautious of potential disadvantages such as limited torque range and dependence on auditory feedback.
Beam-Type Torque Wrench
The Beam-Type Torque Wrench, characterized by its simple yet effective design, offers a visual torque reading through the deflection of a beam mechanism during operation. Its straightforward implementation and lack of need for adjustment or recalibration make it a convenient choice for many mechanical applications. The primary advantage of this torque wrench lies in its direct and reliable torque indication without the use of complex mechanisms. While its simplicity is a notable advantage, users should consider its limited torque range and potential for misinterpretation of readings under certain conditions.
Digital Torque Wrench
The Digital Torque Wrench stands at the forefront of technological advancement in torque measurement, providing precise digital displays of torque values for enhanced accuracy. Its digital interface allows for easy readability and customizable settings, catering to diverse torque requirements in mechanical projects. The unique feature of digital torque measurement offers users the convenience of precise numerical readings, reducing the likelihood of human error associated with analog devices. Despite its exceptional accuracy and user-friendly interface, users need to be mindful of battery dependence and potential electronic malfunctions that may affect performance.
Key Considerations Before Measurement
Proper tool selection
Selecting the appropriate torque wrench for a specific application is critical to achieve optimal results and prevent mechanical discrepancies. Proper tool selection entails matching the torque wrench's capacity and features to the requirements of the task at hand, considering factors such as torque range, accuracy, and ergonomics. By choosing the right tool for the job, users can ensure efficient torque application and minimize the risk of under or over-torquing, leading to improved mechanical outcomes. The advantages of proper tool selection include precise torque control and reduced instances of fastening errors, promoting operational efficiency and equipment longevity.
Equipment calibration
Calibration plays an indispensable role in maintaining the accuracy and reliability of torque wrenches, ensuring consistent performance throughout their lifespan. Regular calibration of torque measurement equipment is essential to verify their accuracy and correct any deviations that may compromise their effectiveness. By calibrating torque wrenches at scheduled intervals or before critical tasks, users can mitigate the risk of inaccuracies and discrepancies in torque application. The benefits of equipment calibration include enhanced operational safety, adherence to industry standards, and overall equipment longevity and effectiveness.
Measuring Torque
Measuring torque in this ultimate guide holds a pivotal role in ensuring precision and safety across various mechanical applications. Torque measurement is a critical aspect of mechanical work, influencing the integrity of connections and the overall performance of machinery. By accurately measuring torque, individuals can guarantee that fasteners are tightened to the specified torque levels, reducing the risk of equipment failure or safety hazards.
Torque measurement not only enhances the operational efficiency of tools but also safeguards against potential damage caused by under or over-tightening. It provides a quantitative assessment of the rotational force applied, aiding in achieving optimal performance in mechanical assemblies.
In this section, we will delve into the different calibration methods, including manual and digital calibration, that play a vital role in achieving accurate torque measurements.
Calibration Methods
Manual Calibration
Manual calibration represents a fundamental aspect of torque wrench measurement, offering a hands-on approach to adjusting and verifying torque levels. It involves manually setting the desired torque value on the wrench, aligning it with the required specifications for a particular task or equipment.
One key characteristic of manual calibration is its simplicity and user control. This method allows individuals to fine-tune torque settings with precision, catering to specific tightening requirements. Manual calibration is a popular choice in this guide due to its versatility and ease of use across a wide range of applications.
The unique feature of manual calibration lies in the tactile feedback it provides, enabling users to physically sense when the torque limit is reached. This tactile sensation enhances the user experience, facilitating accurate torque application without the need for complex equipment.
Digital Calibration
Digital calibration modernizes the torque measurement process by introducing technological advancements that streamline accuracy and efficiency. This method utilizes digital displays and electronic sensors to calibrate torque wrenches with enhanced precision.
An essential aspect of digital calibration is its digital interface, allowing for easy reading and adjustment of torque values. The digital display provides clear and precise torque readings, reducing the potential for human error and ensuring consistency in torque application.
Digital calibration is a beneficial choice in this article due to its convenience and digital accuracy, particularly in demanding or high-precision applications. Users can rely on digital calibration to achieve consistent and reliable torque measurements across various tasks and projects.
The unique feature of digital calibration lies in its data recording capabilities, enabling users to track torque values over time and maintain precise records for maintenance and quality control purposes.
Importance of Accurate Measurements
Ensuring Safety and Precision
Accurate torque measurements play a significant role in ensuring safety and precision in mechanical operations. By maintaining precise torque levels during tightening procedures, individuals can prevent mechanical failures, bolt fatigue, and potential hazards in equipment usage.
A key characteristic of ensuring safety and precision through accurate measurements is the ability to adhere to manufacturer recommendations and industry standards. This practice guarantees that components are assembled correctly, reducing the risk of overloading or structural damage.
Ensuring safety and precision is a popular choice in this guide due to its emphasis on operational safety and equipment longevity. By prioritizing accurate torque measurements, individuals can enhance workplace safety and extend the lifespan of mechanical systems.
The unique feature of ensuring safety and precision lies in its role in promoting quality control and compliance with regulatory standards. By consistently maintaining accurate torque levels, users can demonstrate due diligence in ensuring operational excellence and product reliability.
Common Mistakes to Avoid
Over-Torquing
Over-torquing represents a common mistake in torque applications, leading to excessive tightening beyond the recommended torque values. This practice can result in material deformation, bolt fatigue, or even structural damage, compromising the integrity of mechanical connections.
A key characteristic of over-torquing is the occurrence of exceeding prescribed torque limits, often due to improper torque wrench settings or lack of awareness regarding the required torque specifications. Over-torquing can weaken fasteners and components, ultimately diminishing the effectiveness and longevity of mechanical assemblies.
Over-torquing is a beneficial inclusion in this article to highlight the importance of monitoring and controlling torque levels during fastening operations. By recognizing the risks associated with over-torquing, individuals can adopt preventive measures to safeguard against potential damage and operational inefficiencies.
The unique feature of over-torquing lies in its impact on equipment reliability and safety. By educating users on the implications of over-torquing, this guide aims to promote responsible torque application practices that prioritize equipment performance and longevity.
Under-Torquing
Conversely, under-torquing poses another common mistake that involves insufficient tightening of fasteners below the required torque specifications. This error can lead to loose connections, bolt loosening, or component misalignment, jeopardizing the stability and functionality of mechanical systems.
A key characteristic of under-torquing is the failure to achieve the necessary clamping force required for secure fastening. This can result from inadequate torque application or using the wrong torque values, impacting the overall performance and safety of assembled components.
Under-torquing finds relevance in this article to underscore the significance of meeting specified torque requirements for optimal mechanical performance. By addressing the risks associated with under-torquing, individuals can enhance the reliability and integrity of fastened connections, mitigating the chances of equipment malfunction.
The unique feature of under-torquing lies in its potential impact on operational safety and product quality. By elucidating the consequences of under-torquing, this section aims to educate readers on the importance of achieving proper torque levels for sustainable and efficient mechanical operations.
Best Practices
In the realm of torque wrench measurement, observing best practices is vital to ensuring optimal performance and accuracy in your mechanical endeavors. By adhering to best practices, you can enhance efficiency, maintain precision, and extend the lifespan of your tools. Proper handling and storage, regular calibration, and knowing when to seek professional help are key elements to consider for achieving superior outcomes.
Proper Handling and Storage
Maintaining Accuracy:
Maintaining accuracy is a critical aspect of torque wrench usage. By carefully handling and storing your torque wrench in a suitable environment, you can preserve its precision and reliability. Keeping the tool clean and free from debris, storing it in a protective case, and avoiding extreme temperatures can significantly impact its performance. The key characteristic of maintaining accuracy lies in meticulous attention to detail and a commitment to upholding precise measurements. This approach not only ensures the tool's longevity but also guarantees consistent results in your mechanical tasks. Despite the high maintenance requirements, the benefits of maintaining accuracy far outweigh the effort, making it a popular choice for professionals seeking top-tier performance from their torque wrenches.
Regular Calibration
Ensuring Reliability:
Regular calibration is essential for upholding the reliability of your torque wrench. By calibrating the tool at specified intervals, you can verify its accuracy and detect any deviations promptly. Ensuring reliability through regular calibration involves checking and adjusting the torque settings to align with industry standards and specific project requirements. The key characteristic of this practice is its proactive approach to preempting inaccuracies and maximizing precision. While frequent recalibration may seem time-consuming, the certainty it provides in achieving accurate torque readings is invaluable. Embracing regular calibration as a routine procedure in your mechanical tasks is a beneficial choice for maintaining consistency and reliability in your operations.
Professional Calibration Services
When to Seek Professional Help:
Knowing when to seek professional calibration services is crucial for guaranteeing the accuracy and performance of your torque wrench. Professional calibration services offer expert precision and meticulous adjustments that may surpass what can be achieved through DIY methods. The key characteristic of professional calibration services is their advanced equipment and specialized knowledge, which can rectify even minor discrepancies in torque measurements. Choosing professional help for calibration ensures that your torque wrench meets industry standards and operates optimally for superior results. While there may be a cost associated with professional services, the advantages of impeccable accuracy and reliability make it a worthwhile investment for those who demand peak performance from their tools.