Materials:
To start planning for a concrete slab project, it is crucial to gather all the necessary materials. Listed below are the detailed materials required with exact measurements:
- Concrete mix: X cubic yards
- Rebar: X feet
- Gravel: X cubic yards
- Wooden stakes: X pieces
- Plastic sheeting: X rolls
- Concrete forms: X pieces
- String lines: X feet
- Level: X units
- Trowel: X units
DIY Steps:
When embarking on a concrete slab project, follow these detailed instructions for a smooth process:
- Prepare the site by clearing debris and ensuring a leveled surface.
- Install the wooden stakes and use string lines to mark the boundaries.
- Dig trenches for the forms, ensuring the proper depth for the slab.
- Place the gravel, rebar, and plastic sheeting in the excavated area.
- Mix the concrete according to manufacturer instructions and pour it into the forms.
- Use the trowel to level the concrete and remove air bubbles.
Technical Aspects:
To enhance the quality and uniqueness of your DIY project, consider the following technical aspects:
- Use a vibrating screed for leveling concrete efficiently.
- Timing is crucial; ensure the concrete is poured and leveled promptly.
- Employ proper techniques for curing the concrete to prevent cracking.
- Utilize protective gear such as goggles and gloves when working with concrete.
DIY Project Process:
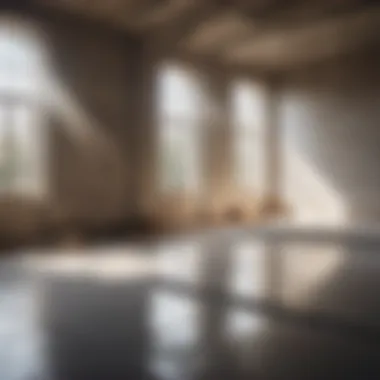
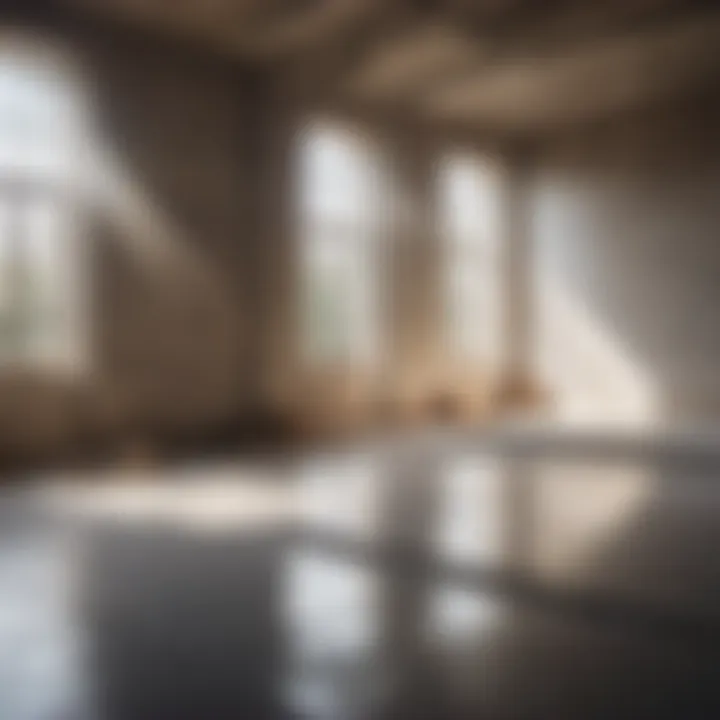
Executing the concrete slab installation involves the following sequential steps:
- Excavate the site and prepare it for concrete placement.
- Place the forms and reinforcement materials accurately.
- Mix and pour the concrete, ensuring a consistent thickness.
- Smooth and level the surface with a trowel for a polished finish.
Troubleshooting Tips:
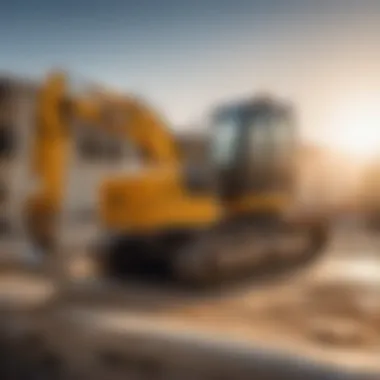
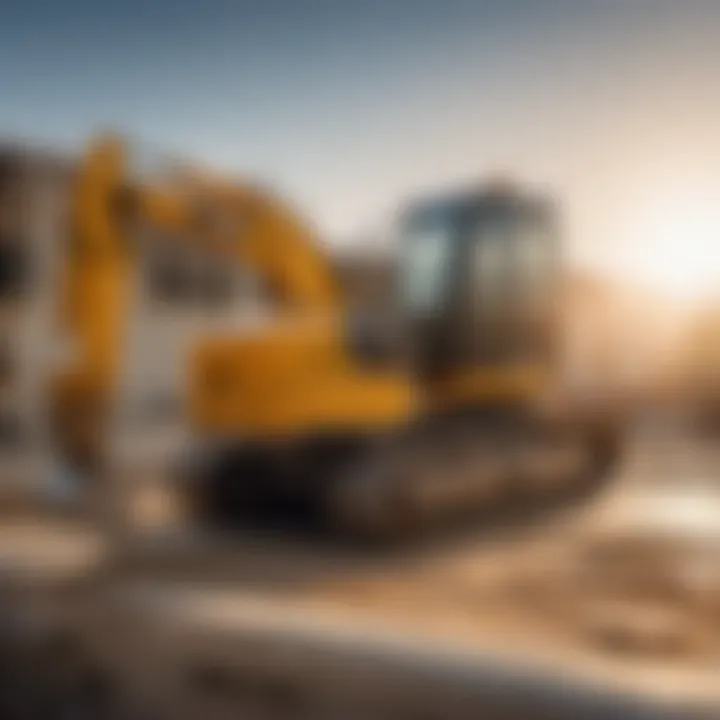
For potential issues that may arise during the project, consider these troubleshooting tips:
- If the concrete sets too quickly, adjust the mix proportions for longer working time.
- In case of cracks, repair them promptly using a concrete patching compound.
- For uneven surfaces, use a grinder to level the concrete effectively.
Factors Influencing Square Foot Cost
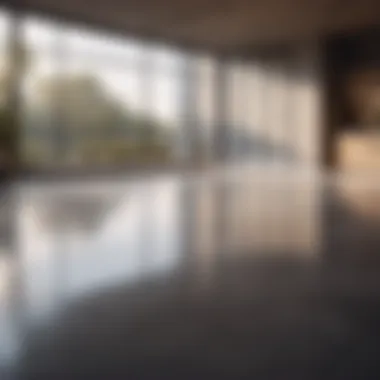
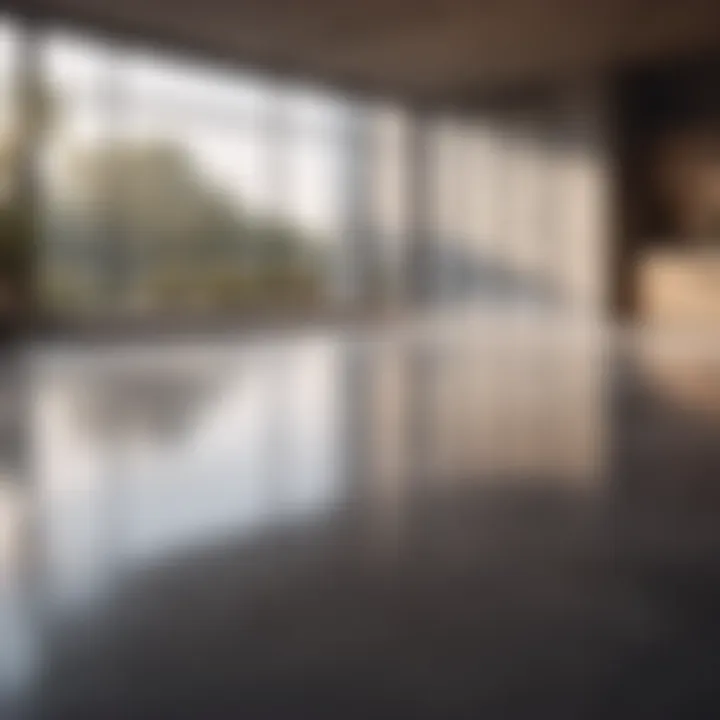
Understanding the square foot cost for a concrete slab involves analyzing various factors that significantly influence pricing considerations. Material costs, labor costs, and equipment costs play pivotal roles in determining the overall cost of constructing a concrete slab. By understanding these factors in-depth, individuals can make informed decisions about their construction projects, ensuring cost-effectiveness and quality outcomes.
Material Costs
When considering material costs for a concrete slab, several key elements come into play.
Types of Concrete
Types of concrete, such as ready-mix, high-strength, or stamped concrete, impact both the quality and price of the slab. Ready-mix concrete offers convenience and consistent quality, while high-strength concrete provides durability for heavy traffic areas. Stamped concrete adds aesthetic appeal but comes at a higher cost due to customization. Each type has its advantages and considerations, allowing individuals to choose based on their specific needs and budget.
Reinforcement Materials
Reinforcement materials like rebar or wire mesh enhance the structural integrity of the concrete slab. Rebar provides additional strength, especially in areas prone to cracking or shifting. Wire mesh offers a cost-effective solution for supporting the concrete. Understanding the role of reinforcement materials helps in reinforcing the slab appropriately, increasing longevity and reducing maintenance costs.
Additives and Finishes
Additives such as accelerators, retarders, or fiber reinforcements, along with finishes like sealers or coatings, add functionality and aesthetics to the concrete slab. Accelerators expedite the curing process, retarders slow it down for intricate designs, and fiber reinforcements enhance durability. Finishes protect the slab from external elements and enhance its visual appeal. By incorporating the right additives and finishes, individuals can achieve a customized and durable concrete slab that meets their requirements.
Labor Costs
Labor costs are a significant component in the total square foot cost for a concrete slab.
Skilled Labor vs. Unskilled Labor
The choice between skilled and unskilled labor impacts the quality and efficiency of the construction process. Skilled laborers possess specialized expertise in concrete work, ensuring precise execution and quality outcomes. Unskilled labor, while cost-effective, may lead to mistakes and rework, ultimately affecting the project timeline and budget. Selecting the appropriate labor type is crucial for achieving the desired results within the set budget.
Union vs. Non-Union Workers
The decision to hire union or non-union workers also affects labor costs and project management. Union workers often adhere to specific standards and regulations, potentially increasing costs but guaranteeing adherence to industry norms. Non-union workers may offer flexibility but require thorough supervision to maintain quality standards. By considering the pros and cons of each labor type, individuals can align their choices with their project requirements and budget constraints.
Equipment Costs
Equipment costs encompass the tools and machinery required for the concrete slab construction process.
Tools and Machinery
Specialized tools like concrete mixers, finishing tools, and safety equipment are essential for efficient and safe construction. Machinery such as excavators or dump trucks aids in site preparation and material transportation. Investing in quality tools and machinery ensures smooth project execution, minimizes delays, and enhances overall construction quality.
Rental Costs
In cases where purchasing equipment is not feasible, renting machines becomes a cost-efficient alternative. Rental costs vary based on the duration and type of equipment needed. While renting allows flexibility and cost savings, it is essential to factor in rental terms and availability to prevent project delays. Balancing owned equipment with rented machinery helps optimize costs and resources for successful concrete slab construction.
Calculating the Total Cost
In the realm of concrete slab construction, understanding and accurately calculating the total cost is a pivotal step in the planning process. The total cost encompasses various crucial components that directly impact the budget and feasibility of the project. By delving deep into the calculation process, individuals can gain a comprehensive understanding of the financial aspects involved in constructing a concrete slab.
Measurement Considerations
Square Footage
Square footage plays a fundamental role in determining the overall cost of a concrete slab. It involves measuring the area where the slab will be laid, guiding the quantity of materials required for the project. Square footage acts as a pivotal metric in estimating the total expenses involved in terms of materials, labor, and equipment. Understanding the square footage allows for precise budgeting and resource allocation, ensuring the project stays within financial constraints.
Thickness of the Slab
The thickness of the concrete slab is a critical factor in cost estimation. It directly impacts the amount of materials needed for the project, influencing the overall cost. A thicker slab requires more concrete and reinforcement materials, affecting the labor and equipment expenses as well. By analyzing the ideal thickness based on structural requirements and budget considerations, individuals can optimize the cost-effectiveness of the project, balancing durability and financial investment.
Cost Estimation Formulas
Base Cost per Square Foot
The base cost per square foot serves as a foundational element in estimating the total project cost. It encompasses the basic expenses involved in material acquisition, labor compensation, and equipment utilization. By calculating the base cost per square foot, individuals can establish a starting point for budget planning, allowing them to gauge the financial scope of the project accurately. This figure forms the basis for additional cost calculations and aids in developing a comprehensive budget framework.
Additional Costs
In addition to the base cost per square foot, accounting for additional costs is essential for a thorough cost estimation process. Additional costs may include expenses such as permits, inspections, site preparation, and unforeseen contingencies. By factoring in these supplementary costs, individuals can create a more robust budget plan that accounts for all potential expenditures, mitigating financial risks and ensuring a smooth project execution.
Variable Costs and Miscellaneous Expenses
In the realm of constructing a concrete slab, variable costs and miscellaneous expenses play a crucial role that cannot be overlooked. These expenses add layers of complexity to the overall cost estimation, requiring meticulous attention to detail. From site preparation to transportation, understanding and accounting for these variable costs is essential for an accurate budget projection. By delving deep into the specifics of these expenses, one can gain a holistic view of the financial implications involved in concrete slab construction.
Site Preparation Costs
Grading and Excavation
Grading and excavation are foundational elements in the construction process of a concrete slab. The precise grading and excavation of the site set the stage for a sturdy and durable foundation. It involves leveling the ground, removing obstacles, and creating the necessary layout for the concrete slab. The key characteristic of grading and excavation lies in its ability to ensure the proper positioning and support for the slab, ultimately influencing its longevity and structural integrity. While it may entail additional costs, the benefits of investing in accurate grading and excavation far outweigh the risks of cutting corners. Proper grading and excavation reduce the risk of uneven settling, cracks, and other structural issues, making it a crucial aspect of concrete slab construction.
Temporary Structures
Temporary structures serve as support systems during the construction phase of a concrete slab. These structures encompass forms, beams, and other temporary components essential for the pouring and setting of the concrete. The key characteristic of temporary structures is their adaptability and versatility in accommodating the specific needs of the project. Their temporary nature allows for flexibility in design and construction, facilitating a smooth workflow. While temporary structures may incur additional expenses, their advantages lie in providing a safe and efficient environment for the concrete pouring and curing processes. Moreover, these structures enhance precision and accuracy, contributing to the overall quality of the concrete slab.
Transportation Costs
Delivery Charges
Transporting materials to the construction site incurs delivery charges, a significant component of overall transportation costs. Delivery charges pertain to the transportation of concrete, reinforcement materials, additives, and equipment to the site. The key characteristic of delivery charges is their direct impact on project timelines and logistics. Efficient delivery services are pivotal in ensuring a seamless construction process, avoiding delays and disruptions. While delivery charges add to the project expenses, their advantages lie in expediting the construction timeline and minimizing downtime. Timely material delivery enhances productivity and workflow efficiency, essential for meeting project deadlines and quality standards.
Handling Fees
Handling fees encompass the costs associated with the unloading and distribution of materials onsite. These fees account for the labor and equipment involved in handling delivered materials, transferring them to the designated areas, and preparing them for use in construction. The key characteristic of handling fees is their contribution to the logistical efficiency of the construction site. Efficient handling practices streamline the workflow, reduce operational bottlenecks, and optimize material utilization. While handling fees constitute a portion of transportation costs, their advantages manifest in improved site organization, resource allocation, and overall project management. Effective handling procedures minimize material wastage and streamline construction operations, optimizing the construction process.
Economic Considerations
Economic considerations play a pivotal role in the realm of understanding square foot cost for a concrete slab. In this article, delving into economic aspects sheds light on the financial intricacies of slab construction. By analyzing market trends and evaluating cost-benefit factors, individuals can make informed decisions regarding their concrete projects. Understanding the economic landscape ensures a cost-effective and sustainable approach to construction.
Market Trends
Supply and Demand
Supply and demand dynamics are fundamental in the construction industry. The specificity of supply and demand within the concrete sector affects pricing structures and project feasibility. The interplay between the availability of concrete materials and the market demand influences cost fluctuations. Recognizing these fluctuations allows project managers to strategize effectively, ensuring optimal budget utilization and project timelines. Although subject to market variables, a thorough comprehension of supply and demand empowers stakeholders to make informed decisions and navigate cost fluctuations adeptly.
Inflation Rates
Inflation rates exert a significant impact on concrete slab construction costs. Understanding the correlation between inflation and material costs is crucial for accurate project budgeting. Inflation rates influence the pricing of raw materials, impacting overall construction expenses. Mitigating the effects of inflation involves strategic planning and adapting to market trends. Through adjusting cost estimations and procuring materials effectively, project teams can minimize the adverse effects of inflation on their construction projects. Conclusively, vigilance towards inflation rates is essential for successful project budgeting and economic sustainability.
Cost-Benefit Analysis
Longevity of Concrete Slabs
The longevity of concrete slabs is a critical aspect of cost-benefit analysis in construction projects. Assessing the durability and lifespan of concrete structures directly affects long-term maintenance costs. Investing in high-quality materials and construction practices enhances the longevity of slabs, minimizing the need for frequent repairs or replacements. Longevity considerations not only ensure structural integrity but also contribute to long-term cost savings. By prioritizing durability, stakeholders can optimize their investments and enjoy sustained benefits from their concrete slabs.
Maintenance Costs
Maintenance costs constitute a significant component of the overall expenditure associated with concrete slabs. Understanding the maintenance requirements of concrete structures aids in budget allocation and long-term planning. Regular maintenance minimizes the risk of structural degradation and prolongs the lifespan of concrete slabs. While maintenance costs are inevitable, proactive upkeep measures can mitigate unforeseen expenses and preserve the integrity of the construction. Prioritizing maintenance as a strategic expense promotes the longevity and resilience of concrete slabs, ensuring optimal functionality and aesthetic appeal over time.