Materials:
When embarking on the project of procuring 6 cubic yards of concrete, a meticulous approach to materials is crucial. Here is a detailed list for the required materials:
- Concrete: 6 cubic yards of high-quality concrete mix.
- Rebar: Approximately 2,000 linear feet of #4 rebar for reinforcement.
- Forming Materials: High-grade plywood sheets for constructing forms to mold the concrete.
- Gravel: 3 cubic yards of gravel for a sturdy base.
- Plastic Sheeting: To cover the concrete and protect it during curing.
- Concrete Finish: Tools for finishing the concrete surface smoothly.
DIY Steps:
Following the materials' procurement, the next step involves a meticulous plan and execution. Here are detailed instructions:
- Site Preparation: Clear the area where the concrete will be poured, ensuring a level and compacted base.
- Rebar Installation: Place the rebar strategically to reinforce the concrete structure.
- Form Construction: Build forms according to the desired shape and size of the concrete elements.
- Concrete Mixing: Use a concrete mixer to mix the components thoroughly.
- Pouring and Leveling: Pour the concrete into the forms and level it using screeds.
Technical Aspects:
To ensure a successful outcome, attention to technical details is paramount. Here are essential technical aspects to consider:
- Tools: Concrete mixer, trowels, floats, and vibrating screeds for precise finishing.
- Timing: Work quickly but efficiently to prevent the concrete from setting prematurely.
- Critical Techniques: Proper consolidation of concrete, careful curing, and accurate finishing techniques.
DIY Project Process:
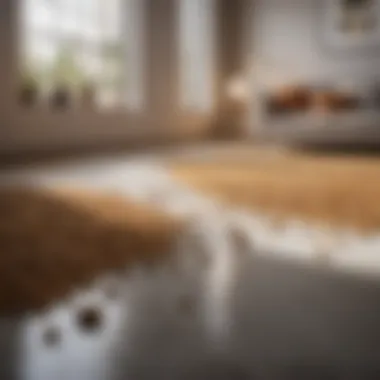
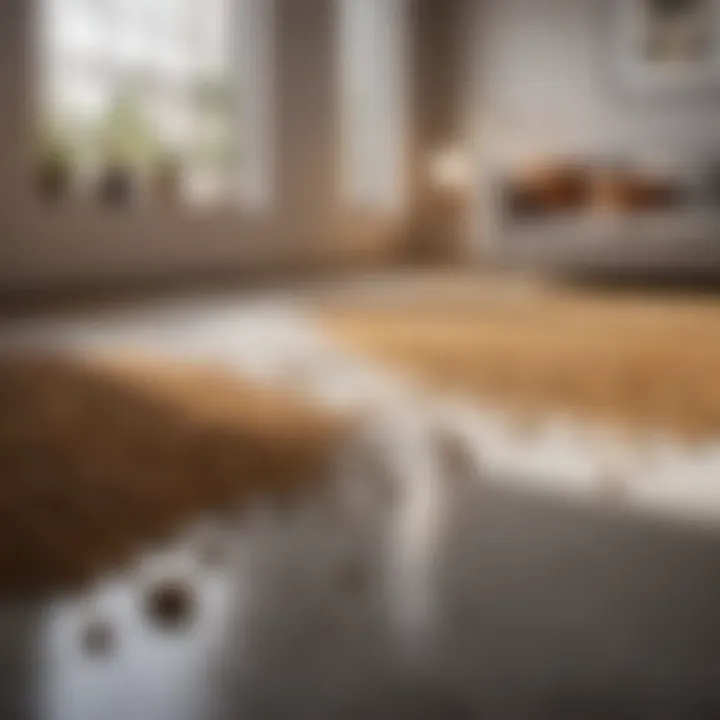
Execution of the project requires a systematic approach. Here is a detailed sequence of steps to follow:
- Concrete Placement: Pour the concrete within 30 minutes of mixing to maintain workability.
- Finishing Touches: Smooth and level the surface using trowels and floats for a polished look.
- Curing Stage: Cover the concrete with plastic sheeting and keep it moist for optimal curing.
Troubleshooting Tips:
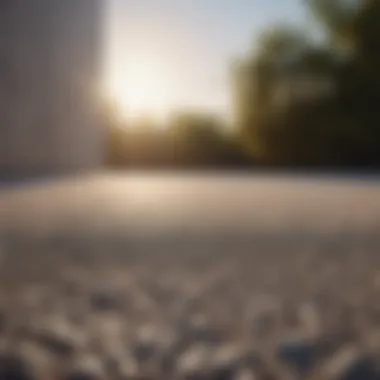
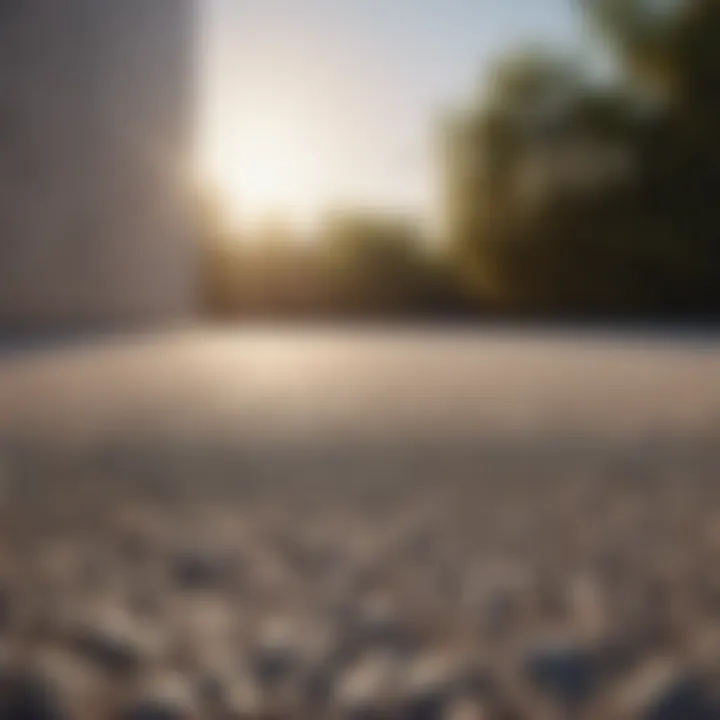
In case of challenges during the project, consider these troubleshooting tips:
- Cracks: Repair cracks by filling with epoxy and smoothing the surface.
- Uneven Finish: Use a grinding tool to level any uneven spots on the concrete surface.
- Curing Issues: Ensure proper curing by misting the concrete regularly to prevent cracking.
Understanding the Cost of Cubic Yards of Concrete
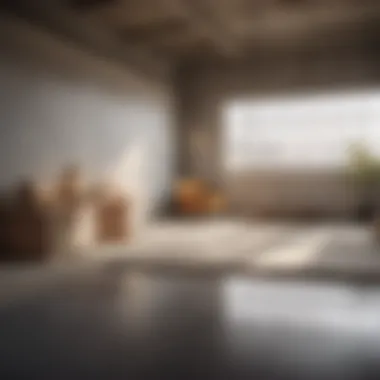
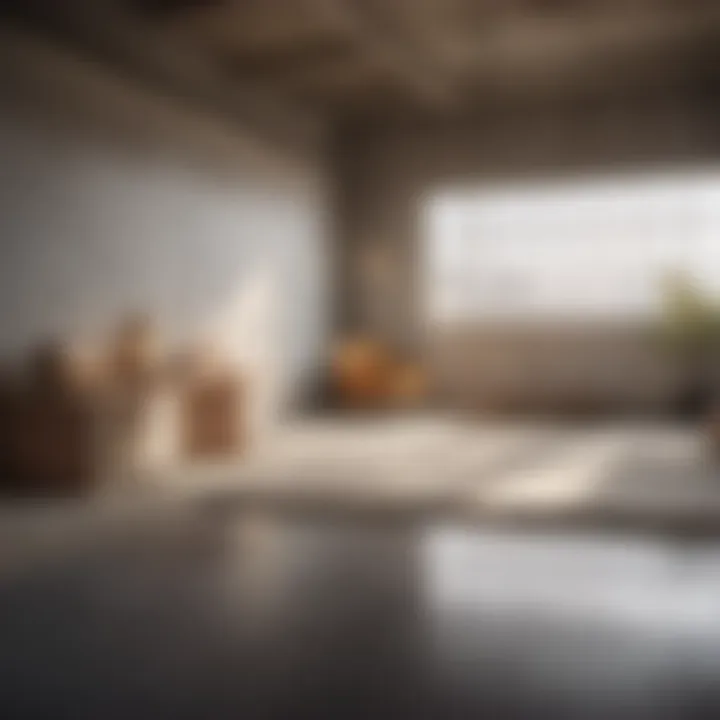
Introduction
In the realm of construction and project management, comprehending the intricacies of concrete procurement is vital. This article serves as a detailed breakdown of what it truly costs to acquire 6 cubic yards of concrete. From the factors influencing pricing to a step-by-step guide on calculating total expenses, we embark on a journey to gain a profound understanding of concrete costs in this comprehensive guide.
Defining the Quantity
The Significance of Cubic Yards in Concrete Measurement
When it comes to construction projects, the quantity of concrete needed is a critical consideration. A cubic yard, being a standard unit of measurement in the construction industry, holds significant importance. In the case of 6 cubic yards, this volume signifies a substantial amount typically required for mid-sized to large-scale projects. The choice of 6 cubic yards as our focal point allows for a practical and realistic exploration of concrete costs, catering to the needs of various construction endeavors. Understanding the implications of this specific quantity sets a solid foundation for delving into the intricacies of concrete procurement.
Importance of Cost Calculation
Understanding the Financial Implications of Concrete Procurement
Cost calculation in concrete procurement goes beyond surface-level evaluation; it delves deep into the financial intricacies of acquiring the essential building material. By comprehending the financial implications involved, stakeholders can make informed decisions regarding project budgets and resource allocation. Analyzing the costs associated with concrete procurement provides a clear picture of the monetary investments required, influencing budgeting strategies and expenditure prioritization. This section sheds light on the nuanced considerations that underpin the financial aspect of concrete procurement, enriching our awareness of the economic dimensions involved in construction projects.
Factors Influencing Pricing
In this section, we delve into the crucial factors that influence the pricing of concrete, offering a detailed analysis to provide a comprehensive understanding of how costs are determined. Factors influencing pricing play a significant role in the procurement process of 6 cubic yards of concrete, impacting the overall budget and project feasibility. By exploring these specific elements, readers can gain insights into the various considerations that affect concrete costs.
Material Quality
Impact of Concrete Grade and Ingredients on Cost
The quality of materials used in concrete, including the grade of concrete and ingredients, holds substantial importance in determining the overall cost of the project. Concrete grade directly influences the strength and durability of the concrete, affecting its final price. Higher-grade concrete with superior ingredients tends to come at a higher cost due to the increased performance and longevity it offers. This aspect is pivotal in ensuring a robust and long-lasting structure, making it a preferred choice for projects where quality is paramount.
The unique feature of the impact of concrete grade and ingredients on cost lies in the balance between quality and price. While high-grade materials come with advantages such as enhanced strength and reduced maintenance needs, they might entail higher initial expenses. However, in the context of this article, prioritizing material quality is essential to secure a reliable and durable construction, even at a potentially increased cost.
Delivery Distance
Logistics and Transportation Costs in Relation to Distance
The delivery distance of concrete to the project site significantly influences the overall pricing due to logistics and transportation expenses. The farther the delivery distance, the higher the costs incurred in transporting the materials, leading to a direct impact on the total expenses. Understanding this logistical aspect is essential for accurate cost estimation and budget planning.
A key characteristic of logistics and transportation costs in relation to distance is the necessity for efficient supply chain management. Proximity to concrete suppliers and optimized transportation routes can mitigate excess costs associated with long delivery distances. While choosing closer suppliers may offer benefits in terms of reduced transportation expenses, it's vital to weigh this against other factors to make cost-effective decisions that align with the project's requirements.
Project Location
Regional Variations Influencing Concrete Prices
Project location plays a pivotal role in influencing concrete prices, with regional variations dictating the cost of materials and services. Different geographical areas may have distinct market dynamics that result in fluctuating concrete prices. Factors such as demand-supply ratios, local regulations, and availability of resources impact pricing decisions, making it essential to consider regional nuances when estimating costs.
The key characteristic of regional variations influencing concrete prices lies in the diverse economic landscapes that shape pricing structures. Understanding these regional differences is crucial for accurate budgeting and cost forecasting. While certain regions may offer cost advantages due to plentiful resources, others might experience price hikes driven by market conditions. By acknowledging these unique features, project planners can adapt their strategies and mitigate potential cost discrepancies, ensuring financial prudence in concrete procurement.
Calculating Total Expenses
In the realm of concrete procurement, understanding the total expenses involved holds paramount significance. The process of determining the cost for acquiring 6 cubic yards of concrete is a critical aspect that demands meticulous attention. Calculating the total expenses not only provides clarity on the financial investment required but also aids in effective budgeting and project management. By delving into the intricacies of cost evaluation, individuals can make informed decisions regarding their concrete procurement needs.
Cost Per Cubic Yard
Determining the average cost of a cubic yard of concrete
One of the key components of calculating total expenses for 6 cubic yards of concrete is determining the average cost per cubic yard. This specific aspect plays a pivotal role in the overall cost estimation process, as it forms the basis for multiplying by the desired quantity. The average cost of a cubic yard of concrete is influenced by various factors such as material quality, delivery distance, and project location.
The unique characteristic of determining the average cost per cubic yard lies in its ability to provide a standardized unit for cost comparison across different suppliers and projects. By establishing this benchmark cost, individuals can gauge the competitiveness of pricing offered by various concrete providers and make informed decisions based on cost-efficiency and quality.
When considering the advantages of determining the average cost per cubic yard, it allows for accurate budget forecasting, helping individuals allocate resources effectively and minimize financial surprises during the concrete procurement process. However, a potential disadvantage of solely relying on this metric is that it may overlook additional expenses that could impact the total cost of acquiring 6 cubic yards of concrete.
Multiplying by Quantity
To arrive at the total expenses for acquiring 6 cubic yards of concrete, the process involves multiplying the average cost per cubic yard by the desired quantity. This multiplication step is crucial in providing an accurate estimate of the overall financial outlay required for the concrete procurement. By incorporating the quantity factor into the cost calculation, individuals can scale their budget according to the specific volume of concrete needed for their project.
The key characteristic of multiplying by quantity lies in its ability to scale the cost proportionally based on the volume of concrete required. This not only simplifies the budgeting process but also ensures that individuals are aware of the cost implications of increasing or decreasing the quantity of concrete for their project.
An advantage of the process of multiplying by quantity is its straightforward approach to cost estimation, allowing individuals to quickly calculate the total expenses based on the cubic yard quantity they intend to procure. However, a potential disadvantage could arise if there are fluctuations in the average cost per cubic yard during the estimation period, leading to potential discrepancies in the final total expenses. It is essential to account for any variances in pricing to ensure an accurate budget projection for securing 6 cubic yards of concrete.
Additional Expenses
In the construction world, when we talk about procuring concrete, it's not just about the cost of the material itself. Additional expenses play a crucial role in the overall budget and must be carefully considered. The section on additional expenses in this article serves as a vital component in highlighting the hidden costs associated with acquiring 6 cubic yards of concrete. These costs can often be overlooked but have a significant impact on the total expenditure.
Labor Costs
Incorporating labor expenses into the overall budget
When delving into the realm of incorporating labor expenses into the overall budget for a concrete project, a key aspect that stands out is the direct influence that labor costs have on the final expenses. Labor expenses encompass the wages of skilled workers involved in the mixing, pouring, and curing of concrete. It is essential to allocate a portion of the budget to labor to ensure the smooth execution of the project.
The characteristic that makes incorporating labor expenses into the overall budget a critical consideration is its direct correlation to the quality and timeliness of the project completion. By factoring in labor costs from the initial planning stages, project managers can ensure that adequate funds are allocated to skilled laborers, thus enhancing the overall efficiency and outcome of the concrete work.
One of the distinct advantages of incorporating labor expenses into the budget is the ability to maintain control over the quality of workmanship. Skilled laborers contribute significantly to the durability and structural integrity of the concrete elements, making it a prudent choice to prioritize labor costs within the overall budget. Additionally, by incorporating labor expenses upfront, project delays due to inadequate workforce or resource allocation can be mitigated, leading to a smoother construction process overall.
Conclusion
This section delves into a comprehensive overview of the entire cost analysis journey, elucidating the nuances of material quality, delivery logistics, project location, labor expenses, and other pivotal factors that influence the final expenses incurred. By encapsulating the essence of cost calculation and additional expenses, the conclusion brings a sense of closure to the readers, leaving them with a thorough understanding of what it truly takes to acquire 6 cubic yards of concrete.
The significance of the conclusion lies in its ability to consolidate information in a digestible manner, making it easier for individuals to grasp the financial intricacies involved in concrete procurement. It serves as a roadmap for homeowners and construction enthusiasts alike, guiding them through the labyrinth of pricing factors and total expenses, empowering them to make informed decisions when embarking on concrete-related projects of their own.
Summary of Costs
Recapitulating the total expenses involved in acquiring cubic yards of concrete
The process of recapitulating the total expenses involved in acquiring 6 cubic yards of concrete is a fundamental aspect of this article, shedding light on the meticulous breakdown of costs incurred in such an endeavor. This section plays a pivotal role in elucidating the financial landscape associated with concrete procurement, offering readers a detailed insight into the various components that contribute to the overall expenditure.
One of the key characteristics of recapitulating the total expenses lies in its ability to provide a comprehensive overview of every cost element involved in acquiring 6 cubic yards of concrete. From material quality to labor expenses, every aspect is meticulously dissected, allowing individuals to gauge the full spectrum of financial implications that accompany such a venture.
The unique feature of this section lies in its practicality and relevance to the readers, as it offers a practical guide on how to navigate the intricacies of cost calculation in the realm of concrete procurement. By highlighting the advantages and disadvantages of each cost factor, individuals can make well-informed decisions when planning their concrete-related projects, ensuring that they stay within budget constraints and achieve optimal financial efficiency.