Materials:
When embarking on a concrete project, it is essential to gather the necessary materials to ensure a smooth and efficient process. The following is a detailed list of materials required for concrete per yard:
- Concrete mix: Purchase high-quality concrete mix from a reputable supplier to ensure durability and strength.
- Water: Clean water is crucial for mixing the concrete to the right consistency.
- Reinforcement materials: Depending on the project scope, consider rebar or wire mesh for added strength.
- Formwork: Use formwork to shape and contain the concrete while it sets.
- Tools: Gather essential tools such as a wheelbarrow, shovel or hoe, trowel, and level for mixing and pouring the concrete.
DIY Steps:
To successfully manage the cost of concrete per yard, it is crucial to follow a systematic approach. Here are detailed instructions on how to navigate the process:
- Planning: Assess the project scope and calculate the volume of concrete needed.
- Budgeting: Create a budget that considers the cost of materials, labor, and additional expenses.
- Sourcing materials: Purchase materials from reliable suppliers to ensure quality.
- Mixing concrete: Follow the recommended guidelines for mixing concrete to achieve the desired consistency.
- Pouring and leveling: Pour the concrete into the formwork and level it using tools like a trowel.
- Curing: Allow the concrete to cure properly to achieve maximum strength and durability.
Technical Aspects:
In addition to materials and steps, paying attention to technical aspects is essential for a successful concrete project. Here are some technical details to consider:
- Timing specifics: Understand the ideal time for each stage of the concrete process, from mixing to curing.
- Tools: Use tools like a concrete mixer, float, and edger to ensure precision and smooth finishing.
- Critical techniques: Master techniques such as screeding and bull floating for a professional finish.
- Quality control: Regularly check for consistency and uniformity during the mixing and pouring process.
DIY Project Process:
Executing a DIY concrete project requires adhering to sequential steps for optimal results. Follow these key steps for a seamless process:
- Preparation: Prepare the site by clearing debris and ensuring a stable base.
- Mixing: Combine the concrete mix and water in the correct ratio for a uniform blend.
- Pouring: Pour the concrete into the formwork, ensuring even distribution and proper leveling.
- Finishing: Use tools to smoothen the surface and add any desired texture or finishing.
- Curing: Allow the concrete to cure undisturbed for the specified time to achieve maximum strength.
Troubleshooting Tips:
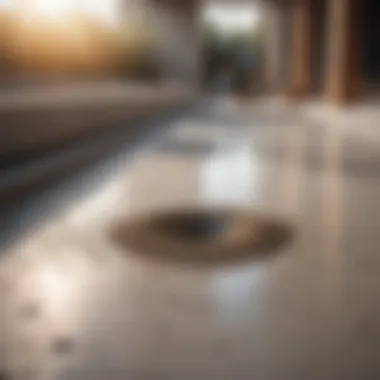

Despite cautious planning, unexpected issues may arise during a concrete project. Here are some troubleshooting tips to address common challenges:
- Cracks: Address cracks by filling them with an appropriate sealant to prevent further damage.
- Uneven surface: Use a grinder or leveling compound to smoothen out any inconsistencies.
- Discoloration: Consider applying a surface treatment to enhance the appearance and cover any discoloration.
By adhering to these detailed steps, homeowners and DIY enthusiasts can navigate the complexities of managing the cost of concrete per yard efficiently. With a focus on precision, quality, and attention to detail, achieving a successful concrete project is within reach.
Factors Influencing Concrete Cost
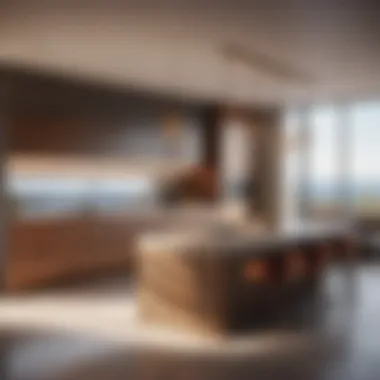

In the realm of construction, the cost of concrete per yard is a crucial element that necessitates a deep dive into the various factors that influence pricing. Understanding these factors can make a substantial difference in cost management and project planning. By dissecting materials, labor, location, and project scope, stakeholders can navigate the complexities of concrete pricing with precision and efficiency.
Materials
Type of Concrete Mix
When considering the cost of concrete per yard, the type of concrete mix used plays a pivotal role in determining overall expenses. Different types of concrete mixes, such as ready-mix, high-strength, or lightweight mixes, come with varying price tags. The choice of concrete mix is dictated by the specific project requirements, including strength, durability, and setting time. Each type has its unique characteristics and applications, influencing both the quality of the final product and the cost implications.
Quality of Aggregates
The quality of aggregates incorporated into the concrete mix directly impacts its performance and longevity. High-quality aggregates enhance the structural integrity of concrete, reducing the risk of cracking and ensuring long-term durability. By selecting premium-grade aggregates, contractors can optimize the concrete mix for strength and longevity, albeit at a higher material cost. Balancing cost with quality is a critical consideration in maximizing the value of concrete per yard.
Additives and Admixtures
Integrating additives and admixtures into the concrete mix allows for customization based on specific project requirements. These additional components can enhance properties such as workability, strength, and curing time, providing tailored solutions for diverse construction needs. While additives and admixtures offer benefits in terms of improved performance and efficiency, they also contribute to the overall cost per yard. Careful selection and dosage of these additives are essential to achieving the desired concrete characteristics without significantly inflating costs.
Labor
Skilled Labor Costs
Skilled labor plays a vital role in the successful execution of concrete projects, impacting both quality and efficiency. Experienced concrete workers command higher wages due to their specialized skills and expertise. Investing in skilled labor ensures precision in concrete placement and finishing, ultimately affecting the project's overall cost. While skilled labor costs may constitute a significant portion of the budget, their contributions are invaluable in delivering high-quality results that withstand the test of time.
Labor Intensity of Project
The labor intensity of a project influences the workforce requirements and, consequently, the overall labor costs per yard of concrete. Projects that demand extensive manual labor, intricate formwork, or tight timelines may incur higher labor expenses due to increased hours and manpower. Balancing labor intensity with project objectives is essential in optimizing efficiency and cost-effectiveness. Efficient planning and resource allocation can mitigate excessive labor costs while maintaining project schedules and quality standards.
Location
Regional Price Variations
Regional factors significantly impact the cost of concrete per yard, with prices varying across different locations. Market dynamics, supply chain logistics, and demand-supply ratios dictate regional price disparities in construction materials, including concrete. Understanding these variations is crucial for accurate cost estimation and budget planning. Procuring concrete from regions with favorable pricing structures can lead to cost savings without compromising material quality.
Accessibility to Concrete Suppliers
The accessibility of concrete suppliers plays a vital role in determining transportation costs and supply chain efficiency. Proximity to concrete plants and distribution centers can lower transportation expenses and streamline material delivery, reducing overall project costs. Establishing strong partnerships with reliable concrete suppliers in close proximity is essential for ensuring a steady and cost-effective supply chain. Accessibility considerations should be integrated into project planning to optimize logistics and minimize construction expenses.
Project Scope
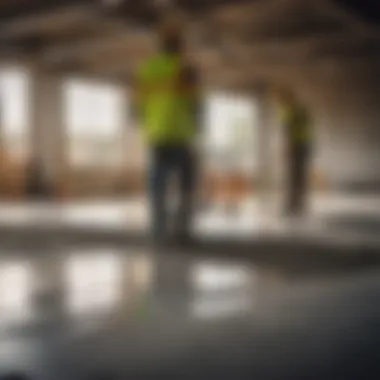

Volume of Concrete Needed
The volume of concrete required for a project directly influences material costs and overall budgeting. Larger project scopes necessitate greater material quantities, escalating expenses accordingly. Efficiently calculating the required concrete volume based on project specifications is essential for accurate cost estimation and resource allocation. Managing the volume of concrete needed ensures optimal material usage and cost control throughout the construction process.
Complexity of Design
The complexity of design elements in a construction project impacts labor, material, and time requirements, consequently affecting the overall cost per yard of concrete. Elaborate designs, intricate patterns, or unique architectural features may demand specialized construction techniques and additional resources, thus elevating project costs. Balancing design complexity with budget constraints is essential in achieving the desired aesthetic and functional outcomes while maintaining cost efficiency. Design considerations should align with cost planning strategies to ensure project feasibility and success.
Calculating Concrete Costs
In the realm of construction, calculating concrete costs holds a pivotal position. When embarking on a project involving concrete, having a clear understanding of the financial implications becomes imperative. This section within the article is designed to shed light on the intricate process of determining concrete costs. By delving into the components that contribute to the overall cost, from materials to labor and overhead, readers will grasp the significance of meticulous cost estimation in project planning. Calculating concrete costs serves as a compass that guides project managers and property owners towards informed decision-making and budget management.
Cost Components
Material Costs per Yard
Material costs per yard constitute a fundamental aspect of the overall expense incurred in concrete projects. The quality and type of materials selected play a crucial role in the durability and appearance of the final structure. By focusing on material costs per yard, project stakeholders can gain insights into the allocation of resources and the impact on project timelines. Understanding the nuances of material costs enables informed decisions that balance quality and affordability, ensuring optimal outcomes for the project at hand.
Labor Costs per Yard
Labor costs per yard are intrinsic to the concrete project's financial landscape. Skilled labor is essential for ensuring the precision and timely execution of construction tasks. Within this context, labor costs per yard reflect the value of expertise and efficiency in project delivery. By exploring labor costs per yard, project planners can assess the human resource aspect of their projects, strategize resource allocation, and optimize operational efficiency.
Overhead and Profit Margin
Overhead and profit margin constitute additional elements that contribute to the comprehensive calculation of concrete costs. Factoring in overhead expenses and profit margins is essential for ensuring the sustainability and growth of construction ventures. This section illuminates the significance of incorporating overhead costs and profit margins into cost calculations, highlighting the balance between operational expenses and financial gains. Understanding overhead and profit margin nuances empowers decision-makers to make financially sound choices that align with project goals and long-term viability.
Cost Optimization Strategies
Bulk Material Purchase
Bulk material purchase strategies offer a cost-effective approach to procuring construction materials in large quantities. By leveraging bulk purchase opportunities, project stakeholders can capitalize on economies of scale, negotiate favorable prices, and streamline supply chain operations. This segment delves into the benefits of bulk material purchases, emphasizing their impact on cost reduction and project budget optimization.
Efficient Project Scheduling
Efficient project scheduling practices play a pivotal role in cost optimization within concrete projects. By meticulously planning and coordinating project timelines, stakeholders can minimize idle time, reduce labor costs, and enhance overall productivity. This section underscores the advantages of efficient project scheduling, such as improved resource management, accelerated project delivery, and cost savings. Embracing efficient scheduling strategies empowers project teams to achieve project milestones efficiently while maximizing cost-efficiency.
Cost Variances
Factors Leading to Cost Fluctuations
Factors leading to cost fluctuations embody the dynamic nature of construction project economics. Understanding these fluctuating elements is essential for mitigating financial risks and budget deviations. By examining the factors that contribute to cost variations, stakeholders can proactively address challenges, adapt to changing market conditions, and optimize cost control measures. This segment elucidates the multifaceted aspects of cost fluctuations, equipping readers with insights to navigate financial uncertainties effectively.
Mitigating Cost Overruns
Mitigating cost overruns is a critical aspect of cost management in concrete projects. Cost overruns pose challenges to project budgets and timelines, underscoring the importance of proactive risk mitigation strategies. This section delves into effective measures for mitigating cost overruns, such as contingency planning, risk assessment, and real-time monitoring. By prioritizing cost overrun mitigation, project stakeholders can enhance project predictability, financial accountability, and overall project success.
Comparative Analysis
Concrete Cost Comparison
Comparison with Other Construction Materials
When evaluating concrete costs per yard, drawing comparisons with other construction materials is essential for a holistic perspective. Concrete stands out due to its durability, versatility, and wide array of applications, making it a go-to choice for many construction projects. Its unique feature lies in its customizable nature, allowing for tailored solutions to meet specific project requirements. While concrete may have higher upfront costs compared to some materials, its longevity and low maintenance needs make it a cost-effective choice in the long run.
Regional Cost Disparities
Regional cost disparities play a significant role in determining concrete prices per yard. Factors such as local demand, availability of raw materials, and transportation costs contribute to price variations across different regions. Understanding these disparities is crucial for construction planning and budgeting purposes. The key characteristic of regional cost disparities is their influence on the overall project budget, as fluctuations can impact the feasibility of a construction endeavor. While regional cost variations may pose challenges, they also present opportunities for cost savings through strategic sourcing and procurement.
Economic Impact
Impact of Economic Factors on Concrete Prices
Economic factors exert a considerable influence on concrete prices per yard. Fluctuations in material costs, labor wages, and market dynamics directly impact the pricing of concrete. By delving into these economic factors, stakeholders can gain insights into the drivers of price variability and make informed decisions regarding project budgeting and resource allocation. The key characteristic of economic factors is their role in shaping the cost landscape of construction projects, highlighting the interplay between monetary policies and industry trends.
Long-Term Cost Considerations
Long-term cost considerations have a significant bearing on concrete pricing sustainability. Assessing the lifecycle costs of concrete, including maintenance, refurbishment, and resilience against environmental factors, is imperative for long-term project viability. The unique feature of long-term cost considerations is their focus on total cost of ownership, emphasizing the importance of durability and longevity in construction materials. While upfront costs are vital, the long-term implications of material choice and project planning underscore the need for a thorough cost-benefit analysis.
Conclusion
Key Takeaways
Understanding Concrete Cost Dynamics
Elucidating the specifics of concrete cost dynamics is paramount in navigating the price terrain within construction projects. Understanding the nuances of how materials, labor, and project intricacies influence costs enables stakeholders to make informed decisions. The key characteristic of this element lies in its ability to highlight the variables that can impact concrete pricing, offering clarity on what drives expenditures in such projects. Its unique feature of providing a granular view of cost components ensures that stakeholders can identify cost-saving opportunities, fostering cost-effective project execution.
Importance of Cost Planning
The importance of cost planning cannot be overstated when considering concrete projects. It plays a pivotal role in ensuring that expenses are managed effectively and resources are allocated efficiently. The key characteristic of cost planning is its proactive approach to anticipating and mitigating potential cost overruns, thereby safeguarding project budgets and timelines. Its unique feature of promoting strategic decision-making based on accurate cost estimates empowers stakeholders to execute projects with financial prudence, setting a strong foundation for successful project outcomes.