Intro
The process of selecting and installing gas piping is not just a matter of choice; it encompasses a range of technical and financial considerations. Homeowners often find themselves navigating a maze of materials, tools, and costs associated with gas pipe installation. This guide aims to provide clarity on the factors influencing gas pipe costs, ensuring that you are equipped with essential information to make informed decisions.
Understanding the nuances of gas piping can save time and money. The following sections will detail the materials needed, step-by-step instructions for installation, technical aspects of your DIY project, and troubleshooting tips to avoid common pitfalls. All homeowners and contractors should pay attention to these elements to achieve an efficient and safe gas line installation.
Materials:
Before diving into the installation process, it is crucial to compile a comprehensive list of materials needed for gas pipe installation:
- Gas Pipe: Choose between black steel, PVC, or copper depending on local code and application.
- Pipe Fittings: 90-degree elbows, tees, and couplings made from the same material as the pipe.
- Primer and Glue (for PVC): Ensure it is compatible with your chosen pipe type.
- Teflon Tape: For securing threaded joints.
- Pipe Modifiers: Valves, gauges, and regulators as needed.
- Fasteners: Use appropriate brackets and screws for supporting pipes.
- Sealant: Apply to prevent leaks at joints.
Measurements for materials will depend on your specific project requirements. For example: a standard installation might require a 20-foot section of gas pipe, several fittings, and appropriate lengths of sealant tape and glue.
DIY Steps:
Detailed Instructions:
-
Planning and Preparation: Assess the layout of your gas supply needs. Check local codes for compliance.
-
Measuring and Cutting: Measure sections of piping accurately. Use a pipe cutter for clean cuts.
-
Assembly of Pipe Sections: Connect the pipe sections using appropriate fittings. Secure with Teflon tape for threaded connections.
-
Sealing Joints: Once connected, ensure all joints are sealed and secure. Use sealant where necessary.
-
Pressure Testing: After installation, perform a pressure test to check for leaks.
Technical Aspects:
Tools Needed:
- Pipe Cutter
- Adjustable Wrench
- Level
- Pressure Gauge
- Drill (for mounting supports)
Timing Specifics:
The installation process may take several hours, depending on experience level and project complexity. An average DIY project can last between 4 to 6 hours.
Critical Techniques:
- Ensure pipes are aligned correctly before tightening to avoid stress at joints.
- Use a level to check for proper slope in gas lines, especially if draining is necessary.
DIY project Process:
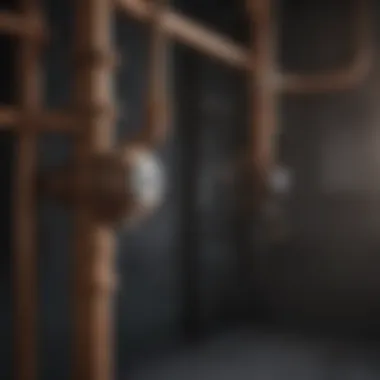
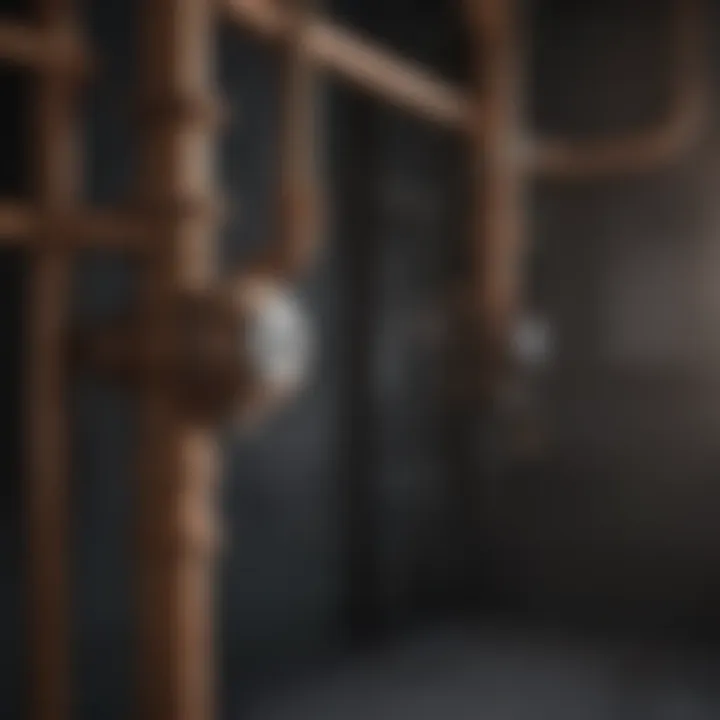
Sequential Steps:
-
Mark Your Pipe: Clearly mark where cuts will be made. This helps avoid unnecessary mistakes.
-
Install Pipe Supports: Before fixing the pipes almost anywhere, set your supports to maintain a stable structure.
-
Connect to a Gas Source: Attach your assembly to the gas line following all safety precautions.
Troubleshooting Tips:
- If leaks are detected during pressure testing, reapply sealant and check connections.
- Adjust pipe supports if there is any sagging or misalignment.
"Proper installation prevents future headaches. Always comply with federal and local regulations."
By emphasizing the importance of careful planning and execution, this guide aims to demystify the complexities of gas pipe installation. Through diligent preparation and adherence to detailed instructions, any homeowner can confidently tackle this essential aspect of home infrastructure.
Prolusion to Gas Pipe Cost
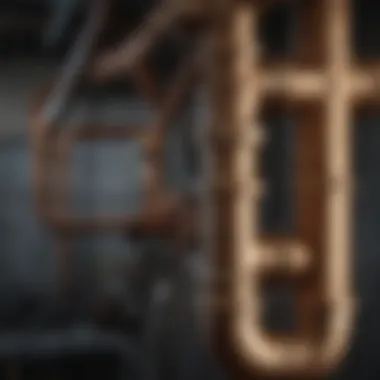
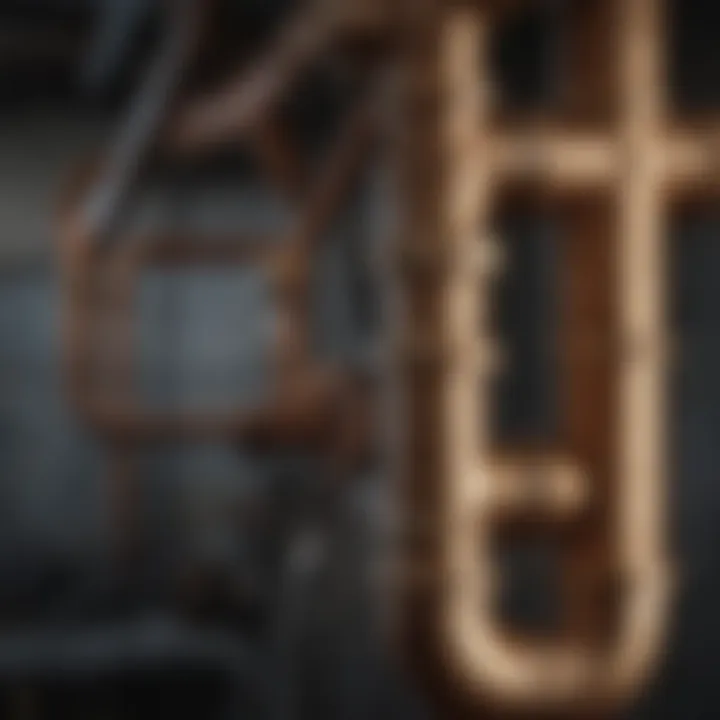
Gas pipe cost is a vital aspect to consider for anyone planning to install or maintain gas piping systems. This component influences budgets significantly, impacting homeowners and contractors alike. Understanding gas pipe cost allows individuals to make informed decisions regarding material selections, installation processes, and ongoing maintenance needs.
When planning for gas pipe installations, the initial cost is just one piece of the puzzle. Factors like longevity, safety, compliance with local regulations, and potential future repairs also play essential roles. Knowing how these costs break down can lead to better residential or commercial project decisions. Moreover, the insight gained from understanding these financial implications aids in budgeting accurately and anticipating additional expenses.
A detailed examination of gas pipe costs can sometimes reveal areas where savings can be achieved. For instance, selecting the right material not only influences the upfront investment but the durability and maintenance expenditures over time as well.
Notably, this article aims to empower readers by providing them with crucial insights into gas pipe costs.
Significance of Understanding Gas Pipe Cost
Grasping gas pipe costs transcends mere numbers; it lays the groundwork for strategic planning. Investment in this area typically ensures safety, efficiency, and reliability in gas distribution. Ignorance of the aspects influencing costs can lead to overspending or unsafe implementations. A comprehensively informed person can better prioritize needs and allocate funds efficiently.
One key consideration is safety. Improper material choices or installation methods have the potential to endanger lives and property. Therefore, understanding costs is not just about financial investment but also about making responsible decisions that safeguard wellbeing.
Managers of residential and commercial properties also benefit from this knowledge. A clear understanding leads to improved negotiations with contractors. It empowers them to seek competitive pricing without compromising quality or safety.
Objectives of the Article
This article aims to accomplish several vital objectives:
- Educate readers about various elements influencing gas pipe costs, providing clarity on terms, materials, and pricing factors.
- Analyze different types of gas pipes, their associated costs, and how they relate to specific applications.
- Outline installation considerations and related expenses, allowing for comprehensive project planning.
- Discuss long-term costs related to maintenance, promoting awareness of lifespan expectations for different materials.
- Explore regional variations to highlight how geographic factors can sway pricing.
- Incorporate case studies that illustrate real-world scenarios, shedding light on practical applications and lessons learned.
By tackling these objectives, the article strives to create a well-rounded resource that caters to homeowners, contractors, and industry professionals seeking practical knowledge about gas pipe systems and their associated costs.
Factors Influencing Gas Pipe Cost
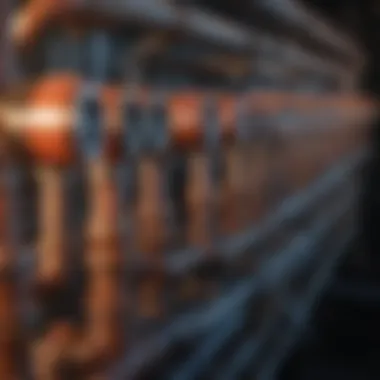
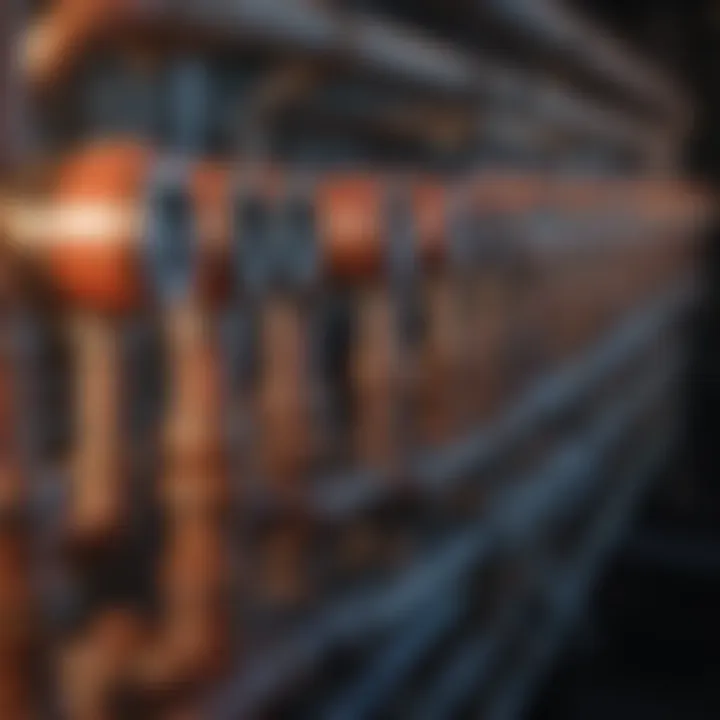
Understanding the factors that influence gas pipe cost is crucial for anyone involved in the procurement and installation of gas piping systems. Various elements contribute to the pricing of gas pipes, including materials used, diameter and length specifications, installation complexity, market dynamics, and regional variances. These factors are interconnected and can significantly impact the final cost.
Material Type
Steel
Steel is a traditional choice for gas piping due to its durability and strength. One significant aspect of steel is its resilience to high pressure, making it suitable for various gas applications. The key characteristic of steel is its capacity to withstand fluctuations in temperature and pressure, which is vital when considering the safety and longevity of a gas system. Steel's popularity stems from its cost-effectiveness and broad availability. However, it does have some unique features such as susceptibility to rust and corrosion, which can lead to increased maintenance costs over time. In the context of gas piping, proper protective coatings and regular inspections are necessary to mitigate these disadvantages.
Polyethylene
Polyethylene has gained traction as a material choice for gas pipes, primarily because of its lightweight nature and resistance to corrosion. This material is beneficial in reducing installation costs due to its easy handling. A unique feature of polyethylene is its flexibility, which allows for easier installation in various environments. This material, however, has limitations regarding temperature; at high temperatures, its performance may decrease, which is a consideration any homeowner should keep in mind. Nonetheless, for most residential applications, polyethylene offers a balance of reliability and cost-effectiveness.
Copper
Copper pipes,commonly used in residential plumbing, also find application in gas piping systems. One advantage of copper is its excellent resistance to corrosion, which enhances its longevity. Copper is a popular choice for smaller installations due to its smooth interior, reducing friction loss. Additionally, copper's capability to handle high temperatures makes it ideal for specific gas applications. However, the drawback is its higher initial cost compared to other materials, which can be a significant consideration for residential projects.
Diameter and Length Specifications
The specifications of diameter and length play a critical role in determining the overall cost of gas pipes. Wider diameter pipes generally have higher material costs, but they may be necessary for certain applications requiring increased gas flow. Furthermore, the length of the pipe directly affects the total quantity required, influencing both material cost and installation labor. In residential projects, selecting the right dimensions is key to optimizing performance while managing expenses.
Installation Complexity
Installation complexity can significantly impact costs. Simple setups may require less specialized labor, thus reducing costs. In contrast, complex installations that demand additional labor or specialized skills can elevate the overall expenditure. For example, if significant alterations to the existing structure are needed, various additional costs such as labor and tools can add up quickly.
Market Demand and Supply Fluctuations
Market demand and supply impact pricing in various ways. When demand for gas piping materials spikes, the costs tend to rise. Conversely, if there is a surplus, prices may decrease. Keeping abreast of market conditions can aid in strategic purchasing decisions.
Regional Pricing Variances
Finally, regional pricing variances must be acknowledged. Costs of gas pipes can fluctuate based on location due to differences in local regulations, labor costs, and material availability. Being informed about these variances can help homeowners and contractors budget more effectively for gas pipe installations.
Types of Gas Pipes and Costs
Understanding the types of gas pipes and their associated costs is essential for homeowners and contractors alike. This section focuses on the practical implications of choosing the right gas pipe material and construction type. Knowing how different pipes compare in terms of cost, longevity, and flexibility is vital for making informed decisions. The type of pipe selected can affect installation complexity, safety, and long-term maintenance expenses.
Conventional Steel Pipes
Conventional steel pipes are a common choice for gas piping. They are renowned for their strength and durability. Steel can withstand high pressure, making it suitable for various gas distribution applications. Typically, these pipes are coated to resist rust and corrosion. However, the initial cost for materials can be higher compared to alternatives like polyethylene.
Steel pipes also require specific installation methods. A trained professional is necessary for welding and fitting, which adds to labor costs. Additionally, the weight of steel may contribute to higher transportation fees if considerable lengths are involved.
Flexible vs. Rigid Pipes
Flexible and rigid pipes serve distinct functions in gas distribution. Flexible pipes are made of materials like polyethylene, enabling easier installation in tight spaces. They can absorb ground movement, which reduces the chance of leaks. However, flexible pipes may not be suitable for high-pressure applications and generally have a shorter life span.
Rigid pipes, on the other hand, are typically more resistant to damage and can withstand higher pressures. They are more time-consuming and labor-intensive to install. The decision between flexible and rigid pipes often comes down to site-specific considerations and expected load conditions.
Cost Comparisons Among Materials
Cost is a significant factor when selecting gas pipes. A thorough comparison among materials helps in making a budget-conservative choice.
- Conventional Steel: While offering durability, the costs for steel can be on the higher side due to labor and material requirements. This may range roughly between $15 and $25 per foot, depending on various factors.
- Polyethylene: More affordable and often priced at $1 to $3 per foot, this material is gaining popularity for its flexibility and ease of installation. However, it may not be acceptable for all installations.
- Copper: This material is another option, typically costing around $3 to $6 per foot. Copper is durable but can be more expensive when considering the fittings and skilled labor for installation.
Choosing the right material ultimately relies on specific project needs, budget restrictions, and region. Residents can benefit from getting multiple quotes from contractors who specialize in gas installation.
Installation Costs and Considerations
Understanding installation costs and considerations is critical when dealing with gas piping systems. The expenses associated with installing gas pipes can vary significantly based on multiple factors, which impacts the overall budget for any gas-related project. Considering these costs is essential for effective planning and resource allocation.
Labor Costs
Labor costs are among the most significant expenses in the installation of gas pipes. These costs encompass wages for skilled personnel required for the task, such as plumbers or gas fitters. Depending on the complexity of the installation, labor costs can rise or fall. For instance, if the installation is straightforward, labor expenses might be on the lower end. However, intricate installations that require special tools or techniques will demand higher wages.
Additionally, it is crucial to consider that labor markets fluctuate. In regions where skilled labor is scarce, the demand may increase wages, driving up overall installation costs. This makes it necessary for homeowners and contractors to conduct thorough research on local pricing trends before beginning any project.
Permits and Regulatory Fees
Acquiring permits is another essential factor in the installation process. Most regions require specific permits for gas pipe installations to ensure safety and compliance with local regulations. This regulatory oversight comes with associated fees that can vary based on location and complexity of the installation. Failing to obtain necessary permits can lead to fines and prolonged project timelines, so this step should never be overlooked.
Moreover, it is advisable to consult local authorities to fully understand the requirements in the area. The process might seem tedious, but it ultimately protects all parties involved and ensures safe practices throughout the gas piping installation.
Tools and Equipment Expenses
Lastly, the costs related to tools and equipment for gas pipe installation cannot be ignored. Proper tools ensure that the installation is carried out correctly, minimizing the risk of leaks or other issues. Costs can vary significantly depending on whether the contractor owns the required tools or must rent or purchase them. For complex projects, specialized tools may be necessary, which can add substantially to the overall budget.
Investing in high-quality tools can lead to better outcomes and reduced maintenance in the future. Therefore, it is wise to weigh out the options when deciding on the best tools or equipment before starting the installation.
Key Takeaway: Planning for installation costs requires careful attention to labor, permits, and tools. Underestimating any of these aspects can lead to unexpected challenges, negatively impacting timelines and budgets.
By addressing installation costs and considerations early in the planning phase, homeowners and contractors can make informed decisions, paving a smoother path towards successful gas pipe installation.
Maintenance and Long-Term Costs
When considering gas piping systems, the dimension of maintenance and long-term costs becomes significant. Proper maintenance not only prolongs the life of the gas pipes but also provides safety assurance and operational efficiency. Ignoring maintenance may lead to increased costs over time due to repairs or replacements. Understanding these costs is critical for homeowners and contractors alike. Here are several key elements to consider regarding maintenance and long-term costs.
Inspection Fees
Regular inspections are essential to ensure the integrity and functionality of gas piping. Inspection fees can vary based on the type of gas system, its location, and the frequency of the inspections. During an inspection, a professional assesses the condition of gas pipes, identifies potential issues, and provides recommendations for maintenance. Investors must understand that the cost of inspections often pays off through avoided emergencies and reductions in repair costs.
- Frequency of Inspections: It is advisable to inspect gas pipes annually. For older systems, more frequent inspections may be necessary.
- Cost Estimates: Inspection fees might range from $150 to $500 depending on the size and complexity of the system.
Repair and Replacement Costs
Gas pipes may require repairs or even complete replacements over their lifetime. Various factors influence these costs:
- Type of Damage: The extent of the damage determines whether repairing a section is feasible or if full replacement is needed. Minor leaks may only need short repairs, while corrosion or significant structural failure necessitates full replacement of the pipe.
- Material of Pipes: Different materials exhibit varying longevity and susceptibility to damage. For example, steel pipes may rust and need more frequent replacement compared to polyethylene pipes.
- Labor Costs: Skilled labor is necessary for repair and replacement, and hourly rates can vary globally. According to recent market data, labor costs can contribute significantly to the overall expense, often comprising up to 50% of the total repair or replacement costs.
Factors Affecting Longevity
The lifespan of gas pipes is determined by several factors:
- Material Quality: High-quality materials significantly enhance durability. Steel and copper generally have a longer lifespan compared to cheaper alternatives like PVC.
- Environmental Conditions: Exposure to harsh weather or corrosive substances can accelerate deterioration. For homeowners, protecting the environment around the piping system is crucial.
- Installation Practices: Proper installation affects the longevity. If pipes are not fitted correctly, this can lead to leaks and subsequent damage.
- Regular Maintenance: Proactive maintenance and prompt repairs ensure longevity. Ignoring small issues can lead to bigger complications that considerably shorten the lifespan.
"An ounce of prevention is worth a pound of cure." This quote resonates well when dealing with gas piping systems. By investing in maintenance, one can mitigate future vulnerabilities and costs.
Case Studies: Gas Pipe Cost Analysis
Case studies on gas pipe cost offer a practical lens through which various installations can be evaluated. This section brings to light real-world scenarios that illustrate the complexities involved in gas pipe installation, helping readers understand how different factors come into play. Analyzing these case studies helps in drawing meaningful conclusions regarding costs, materials, labor, and the unique challenges related to different environments.
Understanding the cost-related decisions made in these case studies allows homeowners and industry professionals to learn from past experiences. The cases will highlight the financial implications of specific choices and the resultant impacts on performance and safety.
Residential Installations
In residential installations, the cost of gas piping can vary widely based on multiple factors. For instance, the type of material selected plays a crucial role in the overall expenditure. When homeowners opt for polyethylene pipes, the initial costs might be lower compared to steel pipes, but the longevity and maintenance might differ. This balance of cost versus durability is a common theme in residential gas pipe choices.
Installation complexity also comes into play. If a home requires extensive renovations to accommodate gas pipes, additional labor costs may arise. For instance:
- Existing infrastructure: Older homes might have outdated systems requiring more modifications.
- Permitting processes: Ensuring compliance can introduce unexpected fees.
Homeowners should factor in these considerations to make well-informed choices.
Commercial Projects
Commercial gas pipe installations typically involve larger systems that impact budgeting differently than residential projects. In these cases, the scale of the installation can be one of the biggest cost determinants. The following aspects are essential:
- Design requirements: Commercial setups often necessitate custom design solutions which can escalate costs.
- Material choices: Here, the use of rigid steel pipes is popular due to their durability in high-traffic areas. While these investments are significant upfront, they may save money on replacements and repairs down the line.
Considering long-term operational costs is key when evaluating commercial project budgets. Companies often choose to invest in higher quality systems that reduce maintenance frequency and ensure safety standards.
Industrial Applications
Industrial applications represent the most complex scenarios for gas pipe installations. The unique requirements of these settings can greatly influence costs. Factors to consider include:
- Size and scope of operations: Industrial setups often utilize larger diameter pipes, which significantly increases raw material costs.
- Safety regulations: Compliance with rigorous safety standards affects both installation and ongoing maintenance costs.
- Supply chain issues: Fluctuations in material availability can cause sudden price changes, creating a challenge for project budgets.
Analyzing various industrial case studies illustrates how a comprehensive cost assessment can lead to better planning and execution of gas piping systems. Understanding these factors can provide insights into making strategic decisions that align with both budget constraints and safety requirements.
By examining real-life case studies, homeowners and professionals gain clarity on potential costs and pitfalls, helping them to minimize future expenses.
Closure and Recommendations
Understanding the intricacies of gas pipe cost is essential for making informed decisions that impact not only budget but also safety and longevity. This section synthesizes the insights gathered throughout the article, emerging with practical recommendations for homeowners and industry professionals alike. Gas pipe systems form the backbone of your heating and cooking needs, so investing time in comprehending their cost implications is beneficial.
Summary of Key Insights
Several critical aspects have been reviewed. First, material choice plays a pivotal role in determining overall costs. While steel pipes are resilient and commonly used, options like polyethylene may lead to reduced installation expenses due to their flexibility and lighter weight. Likewise, the diameter and length of pipes have a direct correlation with material expenses, as larger and longer pipes typically incur higher costs.
The installation complexity introduces additional financial considerations, affecting both labor costs and permitting fees. These fees vary regionally, influenced by local regulations and demand for services.
Sustaining these pipe systems involves not just initial investment but also long-term maintenance costs. Factors such as inspection and repair proximity can reshape budget forecasting, making it clear why these elements are integral to overall cost assessments. The major takeaway is that holistic planning can lead to optimal selection and management of gas piping solutions.
Future Trends in Gas Pipe Costs
Looking forward, several emerging trends may affect gas pipe costs. Increased attention to sustainability and environmental impact could lead to the adoption of greener materials, which may influence traditional pricing structures. Innovations in manufacturing techniques might also reduce costs associated with production, allowing more competitive pricing in the marketplace.
Another significant trend is the technological advancements in installation processes. Automation might ease labor demands, which could translate to lower installation fees over time. Moreover, as smart home technologies become prevalent, systems that incorporate energy efficiency will likely attract focus, further reshaping what homeowners consider in gas piping expenses.