Materials:
DIY Steps:
- Start by clearing the designated area where you plan to lay the concrete blocks. Remove any vegetation, debris, or obstacles that may hinder the installation process.
- Mark out the layout of the blocks using stakes and string, ensuring proper alignment and spacing as per your project design.
- Prepare the foundation by digging at least 4 inches deep and layering it with gravel for proper drainage.
- Mix the cement, sand, and water in a wheelbarrow to create the concrete mixture, ensuring a smooth and workable consistency.
- Begin laying the concrete blocks in the desired pattern, using a level to ensure evenness and straightness of each block.
- Compact the blocks using a vibrating plate compactor to secure them in place and eliminate air gaps.
- Once all blocks are laid and compacted, allow the concrete to cure and set for the recommended timeframe before subjecting it to heavy loads or activity.
Technical Aspects:
Tools: Shovel, level, stakes, string, tape measure, wheelbarrow, vibrating plate compactor Timings: Foundation preparation may take a day, while block laying and compaction can span several days based on the project size Critical techniques: Ensuring proper alignment and leveling of the blocks, creating a sturdy foundation, and compacting the blocks correctly
DIY Project Process:
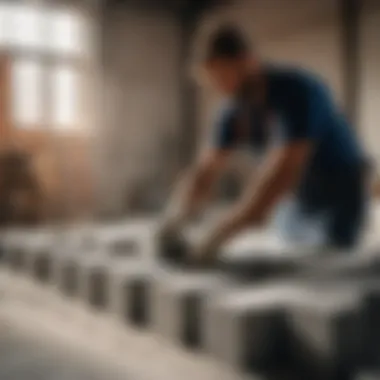
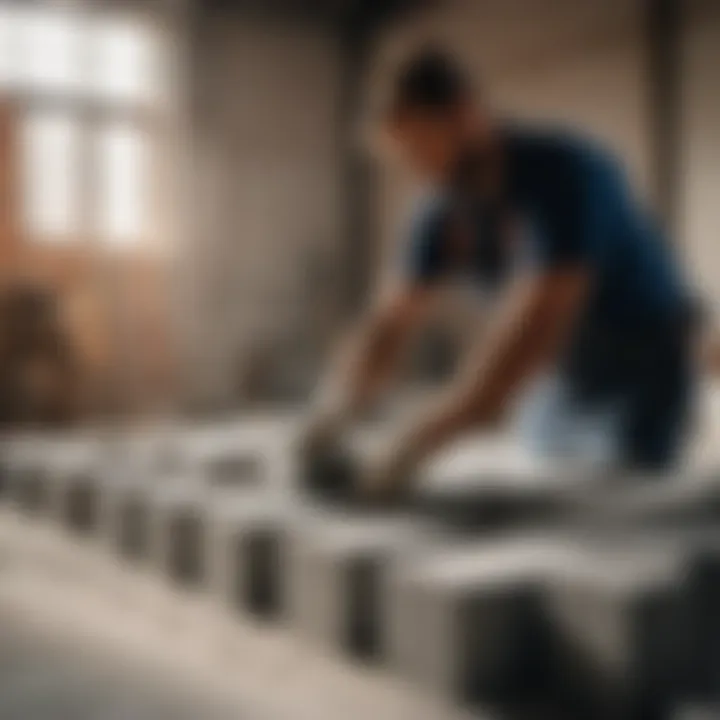
Embarking on this project requires attention to detail and adherence to the step-by-step process outlined above. By following these instructions meticulously, you can achieve a successful outcome while avoiding common mistakes. Should any issues arise during the installation, refer to troubleshooting tips for guidance on adjustments or rectifications.
Exploring the Cost of x Concrete Blocks
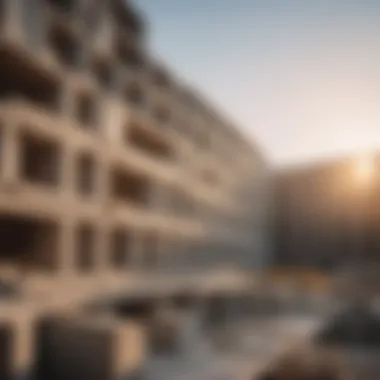
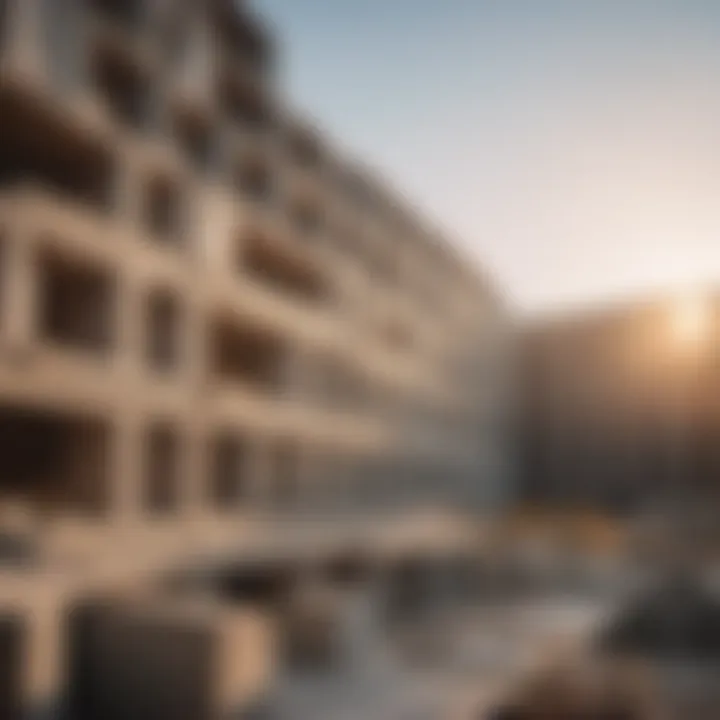
Introduction
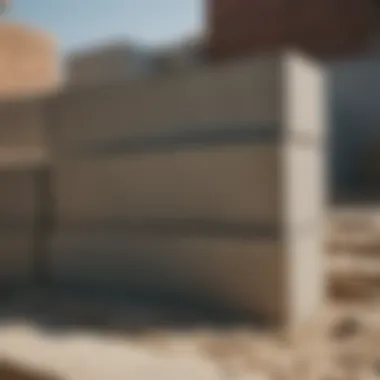
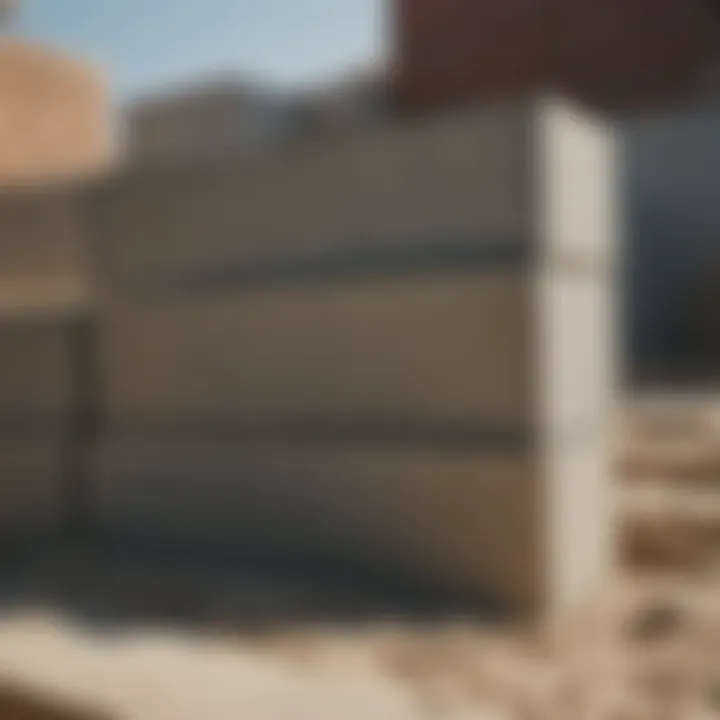
In the realm of construction projects, understanding the detailed costs associated with different materials is paramount to effective budgeting and decision-making. This article aims to provide a comprehensive guide to exploring the cost dynamics of 8 x 16 concrete blocks. By dissecting the intricate web of factors that contribute to the total expenses incurred in procuring these essential construction components, readers will gain valuable insights into optimizing their construction budgets and choices.
What are x Concrete Blocks?
8 x 16 concrete blocks, also known as cement blocks, are essential building materials extensively used in various construction projects. These blocks are manufactured from a mixture of cement, water, and aggregates like sand or gravel. Their standardized size of 8 inches by 16 inches makes them easily stackable and ideal for creating sturdy walls, foundations, and other structural elements in residential, commercial, and industrial settings. Due to their durability and versatility, 8 x 16 concrete blocks are integral components in modern construction practices, offering reliable support and longevity to buildings.
Importance of Understanding Costs
Comprehending the cost implications associated with 8 x 16 concrete blocks is crucial for any construction project. By delving into the intricacies of pricing factors such as material quality, labor costs, and geographical influences, individuals can make informed decisions when planning their construction endeavors. Understanding the costs of these concrete blocks enables project developers, contractors, and homeowners to create accurate budgets, predict expenditures, and avoid potential financial surprises during the construction process. Moreover, a thorough grasp of pricing aspects empowers stakeholders to explore cost-effective alternatives, negotiate better deals, and optimize resource allocation to achieve efficient and economical construction outcomes.
Factors Influencing Cost
Understanding the factors that influence the cost of 8 x 16 concrete blocks is essential in determining the overall expenses associated with construction projects. By delving into material quality, labor costs, and location, individuals can grasp the intricate details that impact pricing decisions. Analyzing these factors provides valuable insights into optimizing budgets and ensuring cost-effective solutions for construction needs.
Material Quality
Impact of Material Grade
When considering the impact of material grade on the cost of 8 x 16 concrete blocks, it is crucial to address the quality of materials used in construction. High-grade materials often contribute to enhanced durability and longevity of the structures. The key characteristic of choosing superior material grades lies in their capability to withstand environmental pressures and maintain structural integrity over time. Utilizing premium material grades guarantees a sound investment in the durability and performance of concrete blocks, making them a popular choice among construction professionals.
Durability Factors
Durability factors play a vital role in determining the longevity and strength of 8 x 16 concrete blocks. Factors such as weather resistance, load-bearing capacity, and sustainability are key considerations when evaluating the durability of construction materials. Understanding the unique features of durability factors allows individuals to weigh the advantages of long-term cost savings against potential disadvantages in upfront expenditure. Investing in durable materials ensures a robust foundation for construction projects, minimizing the need for frequent repairs and replacements.
Labor Costs
Skilled vs. Unskilled Labor
The distinction between skilled and unskilled labor significantly impacts the overall labor costs associated with constructing 8 x 16 concrete blocks. Skilled laborers bring expertise and specialized knowledge to the construction process, ensuring precision and efficiency in project execution. In contrast, unskilled labor may require additional supervision and training, potentially leading to inefficiencies and delays. Choosing skilled labor offers the benefit of quality craftsmanship and timely completion, making it a popular choice for ensuring the successful implementation of construction projects.
Experience Level
The experience level of laborers directly influences the quality and speed of construction activities, thereby affecting labor costs. Experienced workers bring a wealth of knowledge and professionalism to the job site, contributing to enhanced productivity and problem-solving abilities. Their unique feature lies in their ability to handle complex construction challenges efficiently, resulting in smoother project timelines and superior outcomes. While the advantages of experienced labor are substantial, it is essential to consider potential disadvantages such as higher hourly rates, balancing the benefits of expertise against elevated costs.
Location and Market Trends
Regional Price Variations
Understanding regional price variations is critical in assessing the cost of acquiring 8 x 16 concrete blocks. Different geographical areas may experience fluctuations in material costs, labor rates, and transportation expenses, influencing overall project budgets. The key characteristic of regional price variations lies in their impact on the affordability and availability of construction materials, guiding individuals in making informed purchasing decisions. Exploring these factors enables professionals to adapt to regional pricing dynamics, optimizing cost-effective solutions while considering any potential disadvantages in logistical arrangements.
Market Demand
Market demand plays a pivotal role in shaping pricing strategies and cost structures related to construction materials. By evaluating current market trends and demand patterns, individuals can anticipate fluctuations in material costs and adjust budgets accordingly. The key characteristic of market demand lies in its influence on pricing competitiveness and supply chains, driving individuals to explore cost-effective solutions that align with industry demands. Understanding market dynamics empowers stakeholders to make informed decisions, capitalizing on opportunities while mitigating potential disadvantages in unpredictable market conditions.
Calculation of Costs
Material Expenses
Concrete Pricing
Delving into concrete pricing within the realm of 8 x 16 concrete blocks allows us to grasp a fundamental component of construction expenses. Concrete pricing demonstrates a significant impact on the overall cost of the project, as it serves as the foundational material for these blocks. High-quality concrete ensures the durability and structural integrity of the construction, making it a popular and beneficial choice for this article. The unique feature of concrete pricing lies in its versatility, catering to various construction needs while offering a balance between cost-effectiveness and quality assurance.
Additional Materials
Exploring the realm of additional materials sheds light on the supplementary components essential for constructing 8 x 16 concrete blocks. These materials, ranging from reinforcing bars to curing compounds, complement the concrete blocks and contribute to their overall strength and functionality. Each additional material chosen carefully influences the quality and longevity of the construction project, highlighting the importance of incorporating them into the cost calculations. Understanding the advantages and disadvantages of various additional materials aids in making informed decisions that align with the project's requirements and budget constraints.
Labor Charges
Hourly Rates
Unraveling the significance of hourly rates in the context of 8 x 16 concrete blocks unveils the monetary aspect of labor charges. Hourly rates directly impact the labor costs incurred during the construction process, emphasizing the need for efficient and skilful labor to optimize productivity. The key characteristic of hourly rates lies in their direct correlation to project timelines and workforce efficiency, making them a crucial factor in cost estimation. While hourly rates contribute to project expenses, they also reflect the expertise and experience of the labor force, ensuring a balance between quality workmanship and budget considerations.
Total Work Hours
Understanding the dynamics of total work hours provides insight into the time investments required for completing construction tasks involving 8 x 16 concrete blocks. Total work hours encompass the collective effort exerted by the labor force, translating into cumulative labor charges. The efficiency and productivity of workers directly influence the total work hours needed, influencing project timelines and cost implications. By evaluating the unique feature of total work hours, project managers can streamline workflows, enhance productivity, and manage labor costs effectively, aligning with the project's overarching goals and budgetary constraints.
Additional Costs
Transportation Fees
Analyzing transportation fees uncovers a critical aspect of additional costs associated with procuring 8 x 16 concrete blocks. Transporting these construction essentials to the project site incurs fees based on distance, quantity, and logistical requirements. The key characteristic of transportation fees lies in their variability, influenced by regional factors and market trends. While transportation fees add to the overall project expenses, they ensure the timely and efficient delivery of materials, minimizing construction delays and maximizing operational efficiency.
Overhead Expenses
Exploring overhead expenses within the realm of 8 x 16 concrete blocks elucidates the indirect costs essential for project management and execution. Overhead expenses encompass administrative costs, utilities, and facility maintenance, integral to sustaining construction operations. The unique feature of overhead expenses lies in their allocative nature, contributing to the overall project budget without directly impacting material quality or labor efficiency. Balancing overhead expenses with core construction costs ensures a comprehensive budget plan that considers all facets of project execution, fostering transparency and accountability in cost allocation and expenditure management.
Comparison with Other Building Materials
In the realm of construction, comparing different building materials is paramount to making informed decisions regarding project feasibility, durability, and cost-effectiveness. It is a crucial aspect of this article as it provides readers with a comprehensive view of how 8 x 16 concrete blocks stack up against alternative options. By delving into the Cost vs. Benefit Analysis and Long-term Investment Considerations of various materials, individuals can gain valuable insights on why concrete blocks may be the optimal choice for their construction projects.
Cost vs. Benefit Analysis
When conducting a Cost vs. Benefit Analysis between 8 x 16 concrete blocks and other building materials, several factors come into play. The upfront costs of purchasing and using concrete blocks must be weighed against the long-term benefits they offer. Concrete blocks are known for their durability, strength, and fire resistance, making them a solid investment for construction projects requiring stability and structural integrity. While the initial cost of concrete blocks may be higher than some alternatives, their longevity and low maintenance requirements often result in cost savings over time. By evaluating the costs and benefits of concrete blocks in comparison to materials like wood, steel, or brick, readers can make informed decisions based on their specific project needs and budget constraints.
Long-term Investment Considerations
Considering the long-term implications of choosing 8 x 16 concrete blocks over other building materials is essential for any construction project. Concrete blocks are renowned for their longevity and ability to withstand harsh environmental conditions, making them a sustainable and cost-effective choice for both residential and commercial buildings. Unlike wood, which is prone to rot and pest infestations, or steel, which may corrode and require frequent maintenance, concrete blocks offer long-lasting durability with minimal upkeep. Additionally, the thermal mass properties of concrete blocks contribute to energy efficiency, which can result in reduced heating and cooling costs for the structure over time. By taking into account these long-term investment factors, individuals can see the value and longevity that concrete blocks bring to their construction projects.
Conclusion
Understanding the cost involved in acquiring 8 x 16 concrete blocks provides clarity on the overall expenses of a construction project. This knowledge empowers individuals to streamline their budget efficiently, allocate resources effectively, and eliminate any potential financial surprises during the project execution phase. By prioritizing cost analysis and management, stakeholders can enhance cost efficiency, project sustainability, and overall project success.
The analytical breakdown of material costs, labor charges, and additional expenses involved in acquiring 8 x 16 concrete blocks serves as a roadmap for individuals embarking on construction projects. By recognizing the intricate details of cost calculation, individuals can avoid budget overruns, optimize resource allocation, and achieve cost-effective project outcomes. Embracing a structured approach to cost evaluation is vital in ensuring project feasibility, financial prudence, and successful project completion.
Key Takeaways
- Cost Awareness: Understanding the costs associated with 8 x 16 concrete blocks is crucial for effective project budgeting and financial planning.
- Budget Optimization: Analyzing material expenses, labor costs, and additional fees enables stakeholders to optimize budget allocation and enhance cost efficiency.
- Project Success: Prioritizing cost management leads to efficient resource utilization, timely project completion, and enhanced project sustainability.