Unveiling the Intricate Journey of Concrete in a Truck: From Mixing Plant to Construction Site
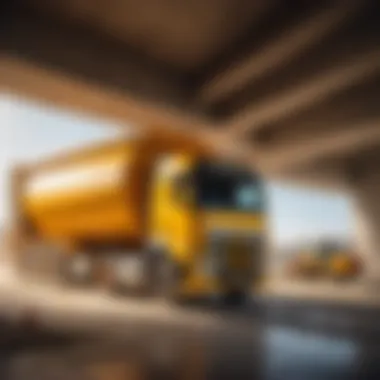
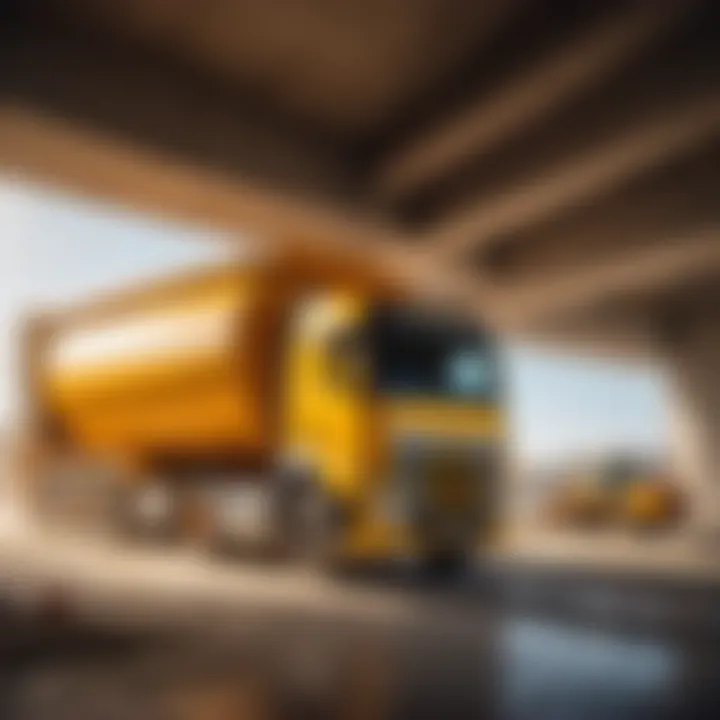
Materials:
- Concrete: 10 cubic meters
- Water: 5 cubic meters
- Aggregates (sand, gravel): 15 cubic meters
DIY Steps:
- Start by gathering all the necessary materials including concrete, water, and aggregates in specific quantities mentioned above.
- Prepare the mixing plant by ensuring it is clean and all equipment is functioning properly.
- Measure out the correct proportions of concrete, water, and aggregates according to the required mix design.
Technical Aspects:
- Tools needed: Concrete mixer truck, mixing plant, measuring instruments.
- Timing specifics: Ensure the concrete is mixed and loaded within a specific time frame to prevent it from setting too early.
- Critical techniques: Properly calibrate the concrete mixer to attain the desired consistency of the concrete mix.
DIY Project Process:
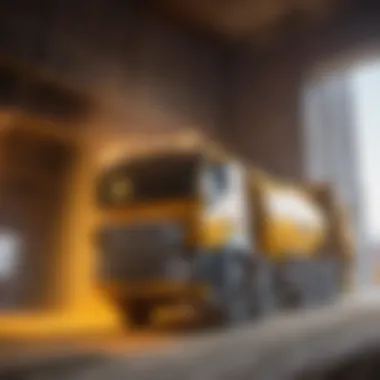
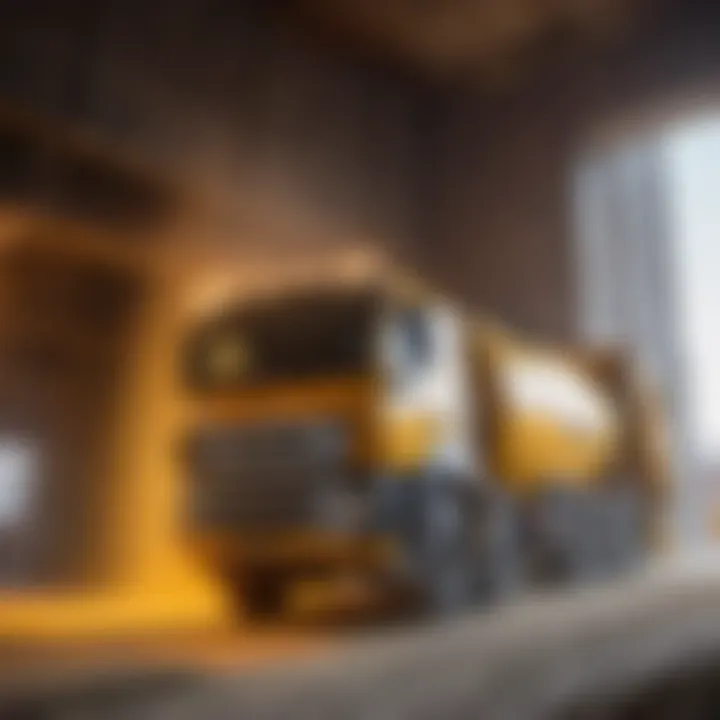
- Once the concrete mix is prepared at the mixing plant, load it onto the concrete mixer truck ensuring proper rotation to prevent segregation.
- Transit the concrete to the construction site within the specified time window to maintain its workability.
- Upon arrival at the construction site, unload the concrete directly into the designated area for pouring.
Troubleshooting Tips:
- If the concrete mix becomes stiff during transit, consider adding water in small increments while remixing to restore its workability.
- In case of delays during transportation, communicate with the site personnel to adjust the pouring schedule accordingly.
Introduction
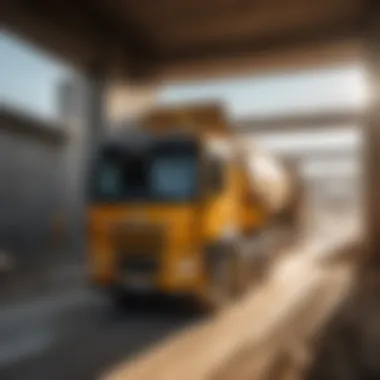
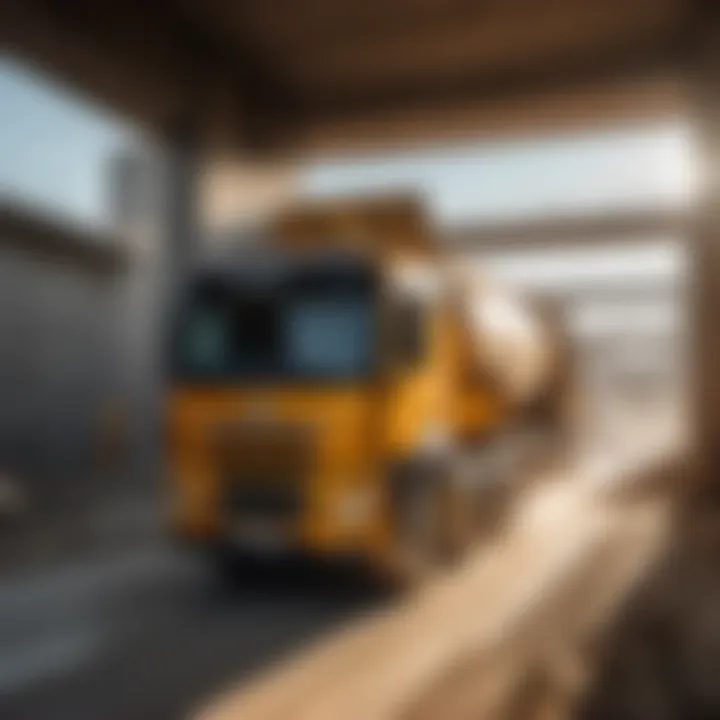
In the world of construction, the journey of concrete in a truck is a critical and fascinating process that underpins the foundation of countless structures we encounter daily. This article delves into the intricacies of this journey, unveiling the meticulous steps involved in transporting concrete from the mixing plant to the construction site. Understanding the nuances of this process is essential for ensuring the durability and quality of the final structure.
Importance of Topic in This Article
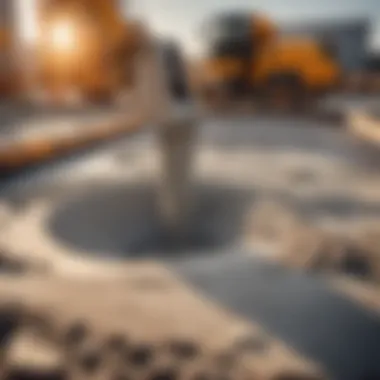
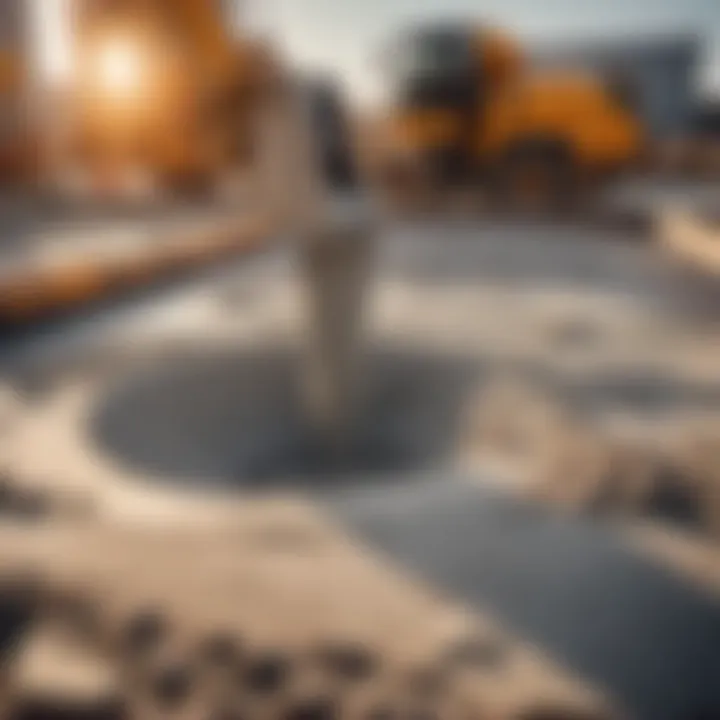
The topic of concrete transportation in a truck holds paramount significance in this narrative due to its direct impact on the structural integrity of buildings and infrastructure. From the precision required at the mixing plant to the careful handling during transit, each stage plays a vital role in determining the overall quality of the concrete used in construction.
Specific Elements
One of the crucial aspects this article will focus on is the coordination and synchronization of operations between the mixing plant and the construction site. This coordination ensures that concrete reaches its destination in optimal conditions, ready to be utilized in various construction applications.
Benefits
By exploring the journey of concrete from the mixing plant to the construction site, readers will gain a thorough understanding of the measures taken to maintain the consistency and quality of the material throughout transit. This knowledge can empower contractors and construction professionals to make informed decisions regarding concrete procurement and utilization.
Considerations about Introduction
The introduction sets the stage for a comprehensive exploration of the concrete transportation process, paving the way for a detailed analysis of each stage involved. Addressing the considerations within this introductory section will provide readers with a holistic view of the challenges and intricacies associated with transporting concrete, thereby enriching their appreciation for this fundamental aspect of construction logistics.
With a focus on precision, quality control, and logistical considerations, this article aims to unravel the layers of complexity surrounding the journey of concrete in a truck, offering readers a deeper insight into the meticulous efforts that go into ensuring the seamless delivery of this indispensable construction material.
The Concrete Mixing Plant
In the journey of concrete in a truck from the mixing plant to the construction site, the concrete mixing plant serves as a crucial starting point. It is here where the raw materials are carefully combined to create the concrete mixture that will eventually be transported to the construction site. The efficiency and accuracy of the mixing plant directly impact the quality of the concrete delivered to the site. Factors such as proper batching of materials, meticulous mixing processes, and stringent quality control measures play a significant role in ensuring the integrity of the final product.
Batching of Raw Materials
Weighing Aggregates
Weighing aggregates is a fundamental aspect of the batching process at the concrete mixing plant. This step involves precisely measuring the different types of aggregates, such as sand, gravel, and crushed stone, that will be used in the concrete mix. The accurate weighing of aggregates is essential for maintaining the desired concrete mix proportions, which directly influence the strength and durability of the final product. By accurately weighing aggregates, the mixing plant can ensure consistency in the concrete composition, leading to high-quality end results.
Measuring Cement
Measuring cement is another critical element of the batching process at the mixing plant. Cement, being the binding agent in concrete, must be measured accurately to achieve the desired concrete strength and properties. The precise measurement of cement ensures that the chemical reactions necessary for concrete to harden and develop strength occur optimally. Maintaining the correct cement-to-aggregate ratio is essential for the overall quality of the concrete mixture, making accurate measurement a key factor in the success of the mixing process.
Adding Water and Admixtures
The addition of water and admixtures during the batching stage plays a vital role in determining the workability and performance of the concrete mix. Water acts as the medium through which the cement binds with the aggregates, while admixtures are incorporated to enhance specific characteristics of the concrete, such as setting time, strength, or durability. Careful consideration of the water-to-cement ratio and the types of admixtures added is crucial in achieving the desired concrete properties. Properly adding water and admixtures at the mixing plant ensures that the resulting concrete mix meets the project specifications and performance requirements.
Mixing Process
Agitation of Ingredients
The mixing process at the plant involves the thorough agitation of ingredients to achieve a uniform and homogenous concrete mix. Proper agitation ensures that all components, including aggregates, cement, water, and admixtures, are evenly distributed throughout the mixture. This meticulous process promotes the hydration of cement particles and the formation of a strong bond between all ingredients. Effective agitation is essential for eliminating any inconsistencies or air voids in the mix, ultimately enhancing the structural integrity and durability of the concrete.
Quality Control Checks
Quality control checks are integral to maintaining the desired concrete quality throughout the mixing process. These checks involve regular inspections and testing of the concrete mixture to verify its consistency, workability, and adherence to project specifications. Quality control measures help identify and rectify any deviations or issues in the mix promptly, ensuring that only top-quality concrete is dispatched for delivery. By conducting thorough quality control checks, the mixing plant can uphold high standards of quality and performance in every batch of concrete produced.
Loading the Concrete Mixer Truck
In the intricate process of transporting concrete from the mixing plant to the construction site, loading the concrete mixer truck stands out as a pivotal step. This section delves into the significance of efficient loading practices, emphasizing specific elements that contribute to ensuring the seamless delivery of high-quality concrete. Among the benefits of meticulous loading are minimized downtime, enhanced consistency in mixing, and maximized operational efficiency. Attention to detail during the loading process is crucial, considering factors such as material wastage, mixing uniformity, and delivery timelines.
Preparation
Cleaning the Drum
Cleaning the drum of the concrete mixer truck is a critical aspect that significantly impacts the overall quality of the concrete during transit. This practice involves removing any residual materials from previous loads, preventing contamination and maintaining the integrity of the new mix. The key characteristic of thorough drum cleaning is its ability to avert cross-contamination, ensuring that each batch of concrete meets the required specifications. This meticulous procedure is a popular choice in this article due to its undisputed role in upholding concrete quality and compliance with industry standards. Despite the time and effort involved, the advantages of clean drum conditions far outweigh any potential disadvantages, guaranteeing consistent and reliable concrete delivery.
Adjusting Drum Speed
The adjustment of drum speed on the concrete mixer truck is another crucial factor that influences the overall mixing process. By regulating the rotation speed of the drum, operators can achieve the desired consistency and homogeneity of the concrete mixture. This key characteristic allows for customized mixing depending on the specific requirements of each job, ensuring optimal results every time. The flexibility offered by adjusting drum speed makes it a beneficial choice for this article, where precision in mixing is paramount. While there may be minor trade-offs in terms of energy consumption or wear on equipment, the advantages of tailored mixing far outweigh these considerations, warranting careful adjustment of drum speed for superior concrete quality.
Pouring Concrete into the Drum
Using Chutes or Conveyors
The utilization of chutes or conveyors for pouring concrete into the drum of the mixer truck streamlines the loading process and enhances efficiency. This specific method allows for the controlled and precise transfer of concrete, minimizing spillage and waste. The key characteristic of using chutes or conveyors lies in its ability to ensure smooth and uniform distribution of the mixture, maximizing the available space within the drum. The popularity of this approach in this article stems from its operational benefits, including time savings and improved safety during loading. Despite potential limitations in terms of reach or maneuverability, the advantages of utilizing chutes or conveyors for loading outweigh the drawbacks, offering a practical solution for efficient concrete placement.
Monitoring Mixing Consistency
Monitoring the mixing consistency of the concrete in the drum is essential for upholding quality standards throughout transit. This aspect involves continuously assessing the uniformity and workability of the mix, adjusting parameters as needed to maintain desired properties. The key characteristic of monitoring mixing consistency is its role in detecting variations or deviations that could compromise the final product. This vigilance is a popular choice in this article, given its critical influence on the structural integrity of the concrete upon arrival at the construction site. While there may be challenges associated with real-time monitoring and adjustments, the benefits of consistent and predictable concrete quality justify the meticulous approach to monitoring mixing consistency.
Ensuring Concrete Quality during Transit
Ensuring concrete quality during transit is a critical aspect of the construction process, as it directly impacts the structural integrity and longevity of the final build. In this section, we will delve into the key elements and considerations that go into maintaining high-quality concrete as it travels from the mixing plant to the construction site.
Concrete, being a sensitive material, is prone to changes in temperature, humidity, and handling during transit. These factors can affect the workability, strength, and durability of the concrete, emphasizing the need for stringent quality control measures throughout the transportation process.
One fundamental factor that significantly influences concrete quality during transit is temperature control. Maintaining the ideal temperature range helps prevent setting issues, ensures proper hydration of cement particles, and enhances the overall strength and durability of the concrete. By carefully monitoring and regulating the concrete's temperature during transit, construction teams can mitigate risks of premature hardening or slump loss, ultimately yielding a superior finished product.
Another crucial consideration for ensuring concrete quality on the move is agitation frequency. Proper agitation helps homogenize the concrete mixture, preventing segregation of ingredients and ensuring uniform distribution of aggregates, cement, water, and admixtures. Optimal agitation frequency not only maintains the desired consistency and workability of the concrete but also minimizes potential issues such as bleeding and delamination.
Considering the significance of temperature control and agitation frequency in safeguarding concrete quality during transit, construction professionals implement robust testing procedures en route to validate the material's integrity. Conducting tests like the slump test and temperature checks at regular intervals allows for real-time assessment of concrete workability and temperature fluctuations, enabling prompt adjustments to uphold quality standards.
Factors Affecting Concrete Quality
Temperature Control
Temperature control plays a paramount role in ensuring the quality and performance of concrete throughout its journey from the mixing plant to the construction site. By maintaining a consistent and suitable temperature environment for the concrete mix, construction teams can enhance workability, strength development, and overall durability.
The key characteristic of temperature control lies in its ability to regulate the exothermic process of hydration within the concrete, influencing the setting time and early-age strength gain. This proactive approach to temperature management is instrumental in preventing thermal differentials within the concrete mass, thereby reducing potential cracking and ensuring a more cohesive and durable final structure.
In the context of this article, temperature control stands out as a pivotal element in preserving concrete quality during transit, as it directly impacts the material's rheological properties and long-term performance. While the disadvantages of insufficient temperature control can manifest in delayed concrete setting or reduced strength development, the benefits of precise temperature management include improved workability, enhanced curing conditions, and minimized risks of thermal cracking.
Agitation Frequency
Agitation frequency serves as a crucial parameter in maintaining homogeneous and well-dispersed concrete mixtures, thereby contributing to the overall quality and consistency of the material during transit. By ensuring adequate mixing cycles, construction teams can prevent particle segregation, optimize paste-to-aggregate bonding, and achieve a uniform distribution of components.
The key characteristic of agitation frequency lies in its capacity to facilitate material homogenization and prevent the formation of clusters or pockets of unmixed constituents within the concrete mix. This thorough mixing process enhances the material's structural integrity, finish quality, and resistance to segregation, ultimately leading to a more durable and aesthetically pleasing end product.
In the context of this article, agitation frequency emerges as a critical factor in maintaining concrete quality during transit, as it directly influences the uniformity, consistency, and performance of the material. While the disadvantages of inadequate agitation frequency may result in undesirable variations in material properties or compromised structural strength, the advantages of optimal mixing cycles encompass improved workability, reduced air voids, and enhanced engineering properties.
Testing Procedures En Route
Slump Test
The slump test serves as a fundamental testing procedure employed to assess the workability and consistency of fresh concrete during transportation. By measuring the degree of cone-shaped slump exhibited by the concrete mixture, construction teams can evaluate its flow characteristics, cohesiveness, and propensity for segregation.
A key characteristic of the slump test is its ability to provide valuable insights into the concrete's plasticity and rheological properties, guiding adjustments in mixing, transportation, or placement practices to achieve the desired workability and performance. This test offers a practical means of validating the concrete mix's suitability for subsequent construction operations, aiding in the prevention of potential quality issues or defects.
In the context of this article, the slump test proves indispensable in ensuring concrete quality during transit, as it allows for real-time assessment of the material's consistency, homogeneity, and slump resistance. While the advantages of conducting slump tests en route encompass enhanced control over material properties, improved constructability, and early detection of potential issues, the disadvantages primarily relate to the additional time and resources required for test execution.
Temperature Checks
Temperature checks represent a critical aspect of quality control measures implemented during concrete transportation, aimed at monitoring and regulating the thermal conditions of the material to uphold desired performance outcomes. By measuring the concrete mix's temperature at regular intervals along its transit route, construction teams can gauge heat loss or gain, assess hydration levels, and prevent detrimental temperature differentials.
The key characteristic of temperature checks lies in their ability to provide insights into the concrete's thermal history and development, facilitating timely interventions to maintain ideal curing conditions and prevent issues like thermal stresses or inadequate strength gain. This monitoring process enables construction professionals to ensure that the concrete remains within the specified temperature range conducive to optimal performance and durability.
In the context of this article, temperature checks play a crucial role in verifying concrete quality during transit by enabling the identification and mitigation of temperature-related risks. While the advantages of conducting temperature checks en route include enhanced quality assurance, reduced potential for thermal cracking, and improved overall durability, the disadvantages may revolve around the need for specialized equipment and trained personnel for accurate temperature monitoring.
Arrival at the Construction Site
The culmination of the journey of concrete in a truck brings us to the pivotal moment of arrival at the construction site. This stage holds paramount importance in the overall process, as it marks the transition from transportation to utilization. Arriving at the designated site in a timely and efficient manner is crucial to maintain project schedules and ensure the concrete is delivered at its peak quality.
Unloading Process
Positioning the Truck
Positioning the truck strategically upon arrival plays a critical role in the seamless unloading of concrete. Proper positioning ensures that the discharge process can be executed smoothly and without delays. The key characteristic of precise positioning is the alignment of the truck's discharge point with the designated pouring area. This alignment optimizes the flow of concrete, minimizes spillage, and enhances overall work efficiency. The unique feature of automated positioning systems further streamlines this process, allowing for precise adjustments to be made with ease. Although manual positioning is also an option, automated systems offer greater accuracy and consistency, reducing the margin for error in this crucial step.
Discharging Concrete
The process of discharging concrete from the truck's drum is a fundamental aspect of the unloading process. Efficient discharge ensures that the concrete can be poured consistently and evenly, contributing to the uniformity and quality of the final structure. The key characteristic of effective concrete discharge is controlled release, which facilitates a steady flow and prevents clumping or segregation. Utilizing chutes or conveyors aids in directing the flow of concrete to the desired location, allowing for precision in placement. The unique feature of adjustable discharge rates enables operators to regulate the volume and speed of concrete release, catering to varying project requirements. While manual discharge methods exist, modern trucks are equipped with advanced mechanisms that enhance efficiency and accuracy, reducing material wastage and ensuring a uniform pour.
Conclusion
In the realm of concrete transportation, the conclusion marks a pivotal stage in the journey from the mixing plant to the construction site. It encapsulates the significance of meticulous planning, expert execution, and quality assurance that underpins the entire process.
One of the key aspects that the conclusion emphasizes is the critical role of coordinated teamwork and communication throughout the transit of concrete. From the batching of raw materials at the mixing plant to the final pour at the construction site, seamless coordination among various stakeholders is paramount to ensure consistency and efficiency in delivering high-quality concrete.
Moreover, the conclusion sheds light on the importance of adhering to stringent industry standards and regulations to guarantee the durability and integrity of the concrete mix. Rigorous quality control checks, such as slump tests and temperature monitoring during transit, are instrumental in identifying any deviations that may compromise the structural strength of the concrete.
Additionally, the conclusion underscores the need for continual maintenance and monitoring of the concrete mixer trucks to prevent any potential malfunctions or delays during transportation. Regular inspection of drum cleanliness, adjustment of drum speed, and adherence to proper loading procedures are essential to safeguard the quality and workability of the concrete.
Furthermore, the conclusion highlights the significance of environmental considerations in concrete transportation. Implementing measures to minimize carbon footprint, such as optimizing transit routes and adopting fuel-efficient practices, not only reduces environmental impact but also contributes to sustainable construction practices.
In essence, the conclusion serves as a comprehensive summary of the intricate journey of concrete in a truck, delineating the challenges, considerations, and best practices that characterize the seamless delivery of this indispensable construction material. It encapsulates the core principles of efficiency, quality, safety, and sustainability that are integral to the successful transportation of concrete from the mixing plant to the construction site.