Intro
Constructing a concrete loading dock is no walk in the park, yet for homeowners and logistics experts alike, it stands as a pivotal component of efficient operations. Before diving into numbers, it's crucial to appreciate that loading docks do not just pop up overnight. The costs vary significantly based on various elements such as material selection, design intricacies, and labor dynamics. In this guide, we aim to break down these complexities, offering a deeper understanding of what goes into the pricing.
Materials:
To kick off with a solid foundation—quite literally—having the right materials is essential. Here’s a comprehensive list of materials you'll need:
- Concrete mix: 10 cubic yards (standard for residential docks)
- Reinforcing steel rebar: 3/8 inch, 500 feet
- Gravel base: 3 tons
- Wood formwork: 2x4 inches, cut to required lengths
- Expansion joints: 10 feet
- Dowel bars: 1 inch, 20 pieces
- Concrete curing compound: 1 gallon
- Sealant for concrete: 1 quart
- Admixtures (optional): For improving strength or workability
Preparing this list ensures that once you roll up your sleeves, you waste no time fetching materials.
DIY Steps:
Now that we have our materials lined up, it's time to dig in with clear, precise steps:
-
Plan the Layout
Understand the dimensions and ensure it fits your needs, remembering to allow for truck clearance and space for loading. -
Excavate the Area
Clear and dig out the site to a depth of at least 8 inches. It's vital to consider a slope for drainage. -
Prepare the Base
Lay down gravel to form a sturdy base. Compact it properly to avoid settling later on. -
Set up Formwork
Use the 2x4 wood to create forms that will shape the concrete. Ensure they are level and secure. -
Reinforcement
Place rebar inside the form to strengthen the concrete and prevent cracking. -
Pouring Concrete
Mix concrete according to the manufacturer’s instructions and pour it evenly in the forms. Use a shovel to spread it out evenly. -
Finish the Surface
Use a float to smooth the surface, then add texture as needed to prevent slipping. -
Curing
Apply a curing compound as required. This is essential for durability. -
Seal the Surface
Once fully cured, apply sealant to protect from moisture and chemicals.
Technical Aspects:
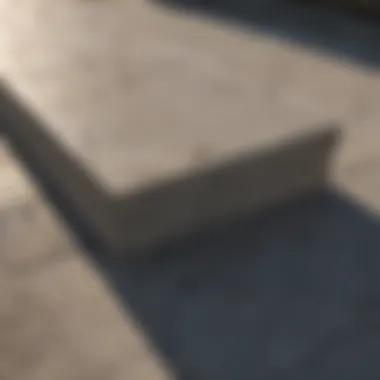
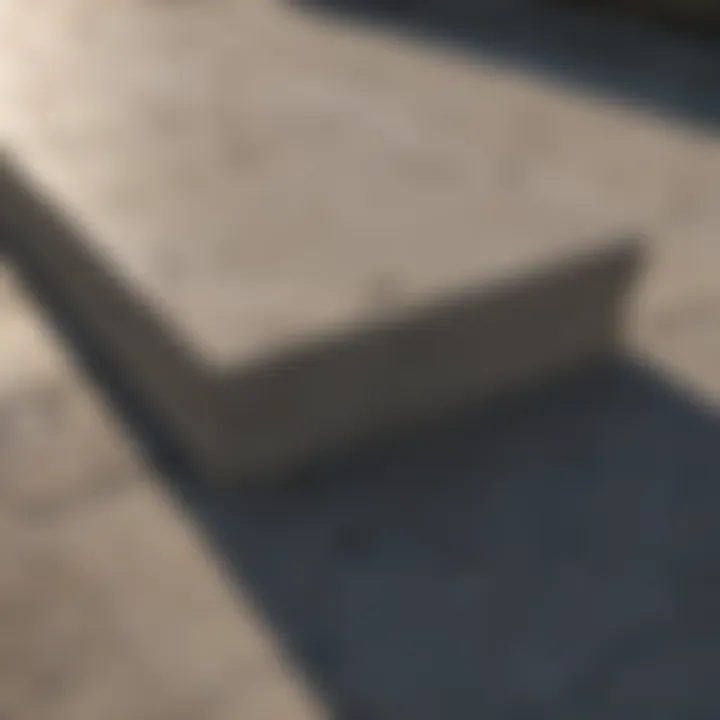
Having a toolbox filled with the right tools is vital. Equip yourself with:
- Shovel
- Concrete mixer or mixing tools
- Vibrating screed
- Trowel and float
- Spirit level
- Compactor (or plate compactor)
- Measuring tape
- Safety gear (gloves, goggles, etc.)
Timing is also crucial. The entire process from planning to finishing can take a few days:
- Site preparation: 1-2 days
- Concrete pouring and finishing: 1 day
- Curing time: At least 7 days before using the dock
DIY Project Process:

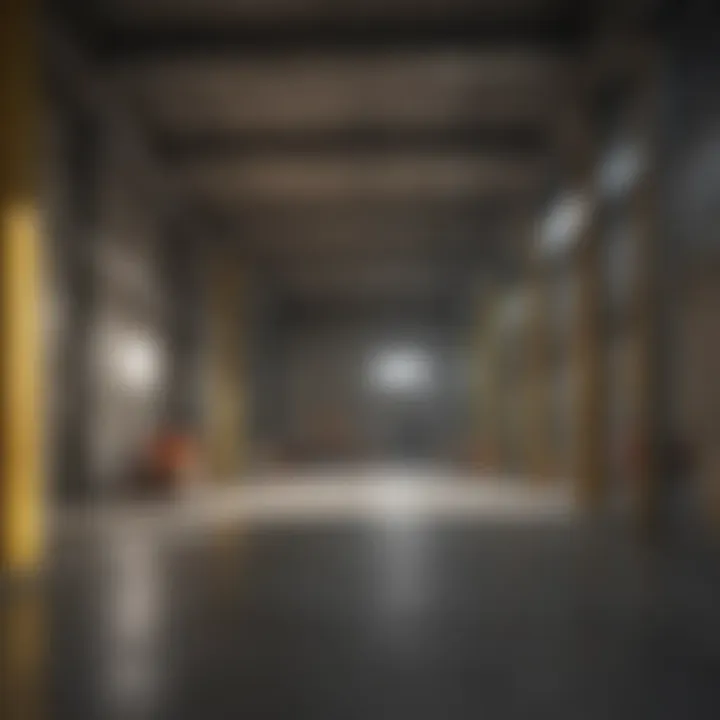
For an effective installation method, follow these sequential steps:
- Initial Survey: Ensure the location is accessible for materials and equipment.
- Excavation and Compaction: Follow through on leveling.
- Base Layer: Ensure gravel is a solid foundation.
- Formwork Securing: Make adjustments before concrete sets.
- Drying Process: Mist the surface during the curing phase for optimal results.
Troubleshooting Tips:
While the task may seem straightforward, hiccups are common. Here are solutions for frequent oversights:
- Uneven Surface: If you find dips, use a trowel to fill them in before curing.
- Cracks: Should they appear after drying, leverage a crack filler accordingly.
- Poor drainage: Ensure the slope is sufficient prior to pouring—a flat area can lead to pooling.
"Proper planning and careful execution can save not just money, but also a lot of headache down the road, ensuring your loading dock serves its purpose without a hitch."
Taking the time to understand the nuances in construction costs and methodologies can go a long way in achieving an ideal loading dock. It’s worth the investment in planning, materials, and labor to elevate functionality.
Prelude to Concrete Loading Docks
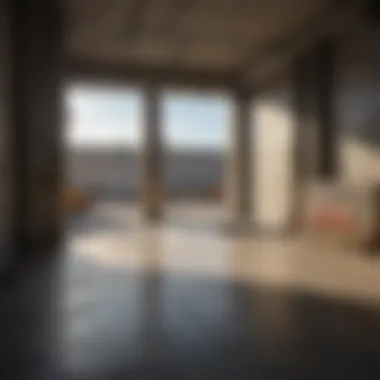
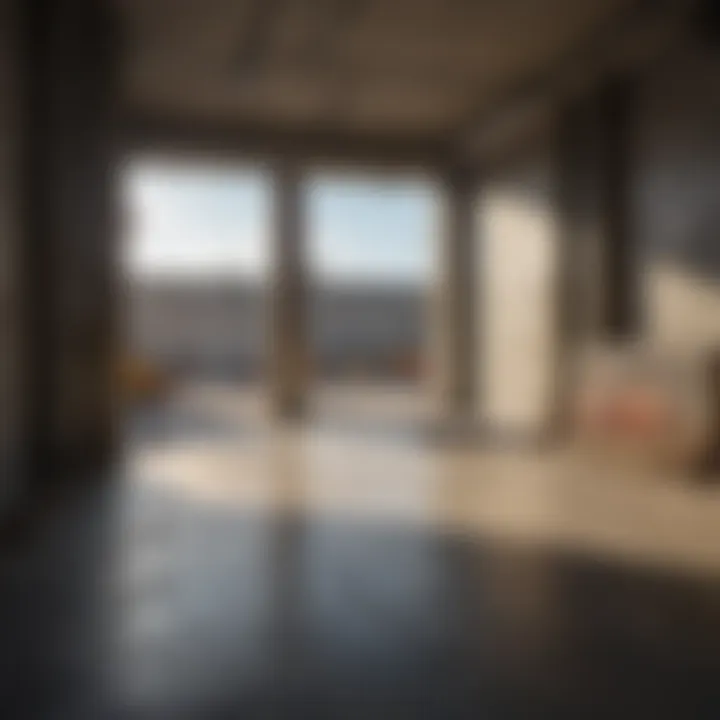
Concrete loading docks are vital components in the logistics and shipping industries. Understanding their construction is essential not only for businesses involved in these sectors but also for homeowners who might encounter loading dock installations in commercial areas. The construction of these docks brings together several factors—material choices, labor implications, and design considerations, creating a mosaic that reflects both the necessity and complexity of logistics operations.
Purpose and Importance
The primary purpose of concrete loading docks is to facilitate the smooth transfer of goods between transportation vehicles and storage areas. They serve as the critical interface in a supply chain operation, significantly influencing efficiency and safety.
From a financial perspective, understanding loading docks can mean the difference between profit and loss, as improper planning can lead to excessive costs. Homeowners and small business owners alike can benefit from grasping how these loading docks operate. Knowing the ins and outs allows for better decisions when hiring contractors or even when managing spaces near commercial properties.
Basic Components of Loading Docks
The basic structure of loading docks incorporates several key components that contribute not only to their functionality but also to their cost. Each component has its unique characteristics and implications for overall expenses.
Dock Levelers
Dock levelers fill the gap between the dock and the trucks or containers. They allow smooth transitions for loading and unloading, making them indispensable for efficient operations. A key characteristic of dock levelers is their adjustable height feature, accommodating various truck sizes. This adaptability proves beneficial in an industry where the size of transport vehicles often varies.
One unique feature of dock levelers is the lip that extends towards the truck bed, creating a secure bridge. However, they come with maintenance considerations; if damaged, they can halt operations, leading to potential financial loss. Overall, investing in reliable dock levelers can enhance loading efficiency and safety.
Traffic Patterns
Traffic patterns at loading docks determine how efficiently vehicles can access and exit the docks. The organization of these patterns is crucial since it minimizes wait times and congestion. A good traffic pattern often utilizes a one-way system, which minimizes the risk of accidents and improves flow.
One standout aspect of thoughtfully designed traffic patterns is that they often feature designated lanes for trucks and pedestrians, enhancing safety. However, poorly laid-out traffic designs can lead to backup and frustration, impacting operational timelines negatively. Therefore, an awareness of traffic considerations is essential for effective dock management.
Safety Features
Safety features are an often-overlooked aspect of loading docks, yet they play a pivotal role in ensuring the smooth operations. Key characteristics include safety barriers, lighting, and signage to direct foot and vehicular traffic. These are all built to mitigate risks associated with the loading and unloading process.
A unique element of safety features is their ability to provide real-time alerts during busy loading and unloading periods, ensuring everyone is aware of upcoming activities. Neglecting safety measures can lead to accidents, a costly mistake from both a financial and operational viewpoint, thus making these features invaluable.
"Investing in proper safety measures not only enhances productivity but ensures a secure environment for workers."
As we delve deeper into these construction considerations, understanding these components will help stakeholders make better-informed decisions about concrete loading docks and their associated expenses.
Factors Affecting Construction Costs
Understanding the myriad factors influencing construction costs is essential for anyone involved in concrete loading dock projects. Recognizing these factors can help in budgeting accurately and making informed choices that align with financial goals. From the type of materials to the labor involved, each element plays a crucial role in determining the overall expenses.
Material Costs
The materials used in constructing a loading dock will often dictate the project's budget. The quantity and quality of materials have a direct impact on pricing and the longevity of the dock. Below are three core aspects to consider:
Concrete Grades
Concrete grades represent the strength and durability of the concrete used. Higher grades typically carry a higher price tag, but they also offer better performance under heavy loads. The primary characteristic of these grades is their tensile strength, measured in megapascals (MPa). Opting for higher-grade concrete is prudent, especially in environments facing heavy freight traffic.
Advantages of higher grades:
- Durability: High-grade concrete withstands severe weather conditions and heavy use.
- Reduced Maintenance: Less frequent repairs or replacements lead to lower long-term costs.
However, the downside is mainly the upfront costs, which can significantly inflate the initial budget.
Reinforcement Bar Options
Reinforcement bars (rebars) are critical for providing strength to concrete structures. The choice between different types of rebar can greatly influence the stability of a loading dock. The most common options are steel, epoxy-coated, and stainless steel. The key characteristic of steel rebar is its strength-to-weight ratio, making it a favored choice for many builders.
Unique features include:
- Steel offers good tensile strength but is prone to rust, requiring protective coatings.
- Epoxy-coated bars resist corrosion, ideal for environments with moisture.
The disadvantage lies in the added costs for specialty rebars like epoxy or stainless steel, but they may save money in repairs down the line.
Finishes and Sealants
The choice of finishes and sealants can be an overlooked aspect of costs but can impact both functionality and aesthetics. The primary function of sealants is to protect concrete from chemical damage and weathering. Common options include epoxy and urethane finishes that provide solid resistance to stains and abrasion.
Unique features include:
- Epoxy finishes create a hard, glossy surface that is highly durable.
- Urethane sealants provide flexibility, adapting to temperature variations.
The trade-off comes with added cost, but investing in higher-quality finishes can substantially extend the lifespan of your loading dock.
Labor Costs
Labor costs are another significant expense that can’t be ignored. The type and skill level of the workers involved heavily influence total costs. There are some vital elements to note:
Skilled vs. Unskilled Labor
Engaging skilled labor typically requires a higher wage but comes with a set of benefits that often outweigh the additional cost. The key characteristic of skilled labor is their expertise and efficiency, allowing for fewer errors and delays.
While unskilled labor may appear more cost-effective initially, the risks associated with mistakes can lead to higher expenses over time. Thus, it’s often smarter to invest in skilled tradesmen when dealing with complicated aspects of loading dock construction.
Project Duration
The length of time taken to complete a project inevitably shapes the overall budget. Extended project durations can ramp up costs quickly, particularly concerning labor and equipment rental. Tight deadlines often require more labor on-site, which in turn raises expenses.
However, rushing a project can compromise quality, resulting in long-term costs due to repairs or remodels.
Local Wage Rates
Wage rates can vary greatly based on geographical location and availability of skilled labor. Understanding local wage rates allows for a more accurate budgeting approach. In urban regions, for instance, labor tends to be pricier due to the cost of living.
Unique features include:
- Comparison of local wage rates can help identify the best places for hiring skilled labor, impacting the ability to stay within budget.
Ignoring local trends in wage rates could lead to unexpected financial stress throughout the project.
An accurate understanding of these costs provides a robust framework for managing budgets effectively and achieving seamless loading dock construction.
Design Considerations and Their Impact
When it comes to constructing concrete loading docks, design considerations play a crucial role. The layout and architectural features of a loading dock directly influence functionality, safety, and, significantly, the overall cost of construction. By carefully evaluating each aspect of design, stakeholders can ensure that their investment leads to a well-planned facility that meets both present and future operational needs. The importance of these decisions stretches beyond initial expenditure, impacting long-term value and efficiency.
Site Layout and Planning
Geographical Layout
The geographical layout of a site can make or break the loading dock's effectiveness. This aspect refers to how the land contours, elevation, and existing infrastructure can affect the planning and construction process. For instance, a site that features ample flat land typically allows for easier construction and reduces the cost of groundwork needed, as opposed to a location with significant slopes or irregular terrain.
A key characteristic of geographical layout is its potential to impact accessibility of routes, which is critical for heavy vehicles. Loading docks that are situated in well-planned geographical positions can optimize traffic flow, thereby enhancing efficiency. A unique feature is when a loading dock is designed close to major transport routes, such as interstates or shipping hubs, offering palpable advantages in terms of reduced transport time and costs.
However, the disadvantages come into play if the location requires extensive grading or earth moving to make it suitable for construction. Those expenses can balloon quickly. Employing the right geographical layout is thus vital, as it not only shapes the logistics but also has long-lasting implications for operation costs.
Accessibility Requirements
Accessibility requirements are about ensuring safe and efficient entry and exit for vehicles, which is another fundamental aspect of feature planning for loading docks. The focus here is to create designs that account for the movement of heavy machinery and freight without congestion or risk of accidents. A well-designed loading dock anticipates the flow of trucks, forklifts, and deliveries efficiently.
A core characteristic of accessibility requirements is that they establish standards for things like loading ramp gradients, door widths, and traffic patterns. This attention to detail is essential for smooth operations and compliance with safety regulations. Unique features often include designated areas for queuing, which can help minimize idle time, reducing wear and tear on both vehicles and the loading dock itself.
On the flip side, overly simplified access routes may lead to bottlenecks, delaying operations which could increase labor costs. Thus, even though accessibility may seem straightforward, it requires a meticulous design approach to ensure that the infrastructure can hold up under the demand of daily operations.
Dock Design Variations
Standard Dock Designs
Standard dock designs are those tried-and-tested layouts that cater to a wide range of operational needs; they are characterized by their reliability and cost-effectiveness. Utilizing a standard design often translates to savings in both time and money since they primarily rely on established blueprints.
There’s significant appeal in using such designs due to their flexibility. A key characteristic here is that they can easily accommodate different types of operations – be it for retail, wholesale, or manufacturing. Their well-defined layouts lead to predictability in operations, allowing for a more streamlined process overall. However, they may face limitations when unusual needs arise requiring specialized equipment or unique processes.
Consequently, while standard designs deliver efficiency, they might not always provide the agility needed for constantly evolving business demands.
Custom Solutions
Custom solutions in dock design represent a shift towards addressing unique operational requirements that standard structures cannot. These solutions are made to fit the particular needs of a business, sometimes tailored to accommodate specific machinery or unusual cargo types. A key characteristic of custom solutions is their potential for maximized operational efficiency wherein every dimension and feature is centered around the specific requirements of the user.
They might feature distinct materials or innovative designs focused on enhancing productivity but, with that, comes the inherent drawback of costs. Custom solutions usually involve higher initial investment but can result in notable efficiencies over time. Furthermore, stakeholders must weigh their preferences carefully – while this unique approach can yield significant advantages in functionality, it could also stretch a budget thin if not approached with due diligence.
In summary, both standard and custom designs bring diverse perspectives to the table. Standard designs are economical and reliable, while custom solutions offer tailored efficiencies that can justify a higher upfront cost. The nuances in design variations are pivotal to understanding how best to budget and manage the construction of concrete loading docks.
Geographical Influences on Costs
Understanding the geographical influences on the construction costs of concrete loading docks is paramount for stakeholders involved in this enterprise. Every location brings its own set of challenges and opportunities, affecting the overall budget and timeline of a project. Factors like regional pricing trends and climate considerations play a critical role in shaping the final costs. When properly analyzed, these geographical elements can lead to better planning and resource allocation.
Regional Pricing Trends
Urban vs. Rural Pricing
Urban locations typically showcase higher construction costs. This is primarily due to dense populations, higher living expenses, and the competition for skilled labor. The sheer volume of projects can strain available resources, leading to increased costs. On the flip side, rural areas often have lower pricing. However, they might present unique challenges such as transportation of materials and fewer qualified contractors.
A key characteristic of urban pricing is the need for specialized equipment and techniques, which can drive up labor rates. Additionally, the demand for quick completion can lead to premium charges. This makes urban projects generally more expensive than their rural counterparts but also often leads to faster accessibility to big markets.
In contrast, rural pricing, while initially more cost-effective, can introduce delays and logistical complications. Subcontractors in rural regions might not have the same level of expertise, impacting the quality of work. There’s also the chance of unforeseen costs related to transporting materials. Thus, when deciding between urban and rural options, understanding these advantages and disadvantages is essential.
State Regulations
State regulations significantly affect construction costs, adding another layer to pricing. Each state enforces its own building codes, which dictate the materials used, construction practices, and safety standards. It’s crucial to navigate these nuances to avoid costly mistakes or fines.
For instance, areas with stringent regulations might see higher costs due to the need for specialized materials or increased inspections. These costs can be seen as beneficial in terms of long-term durability, but they can also surprise newcomers to the industry.
A unique feature of state regulations is the degree to which they encourage or discourage certain construction methods. In some states, eco-friendly materials might receive tax incentives, effectively lowering the overall project cost. On the contrary, states that lack such regulations may leave contractors open to using cheaper, lower-quality alternatives, leading to potential issues down the line. Understanding these regulations and their potential advantages and disadvantages is crucial for effective budgeting and compliance.
Climate Considerations
Temperature Extremes
Temperature can be a major player in construction decisions. Regions that experience extreme temperatures may increase costs because of the need for specialized materials and practices. In colder climates, for example, cement might require additives to set properly at low temperatures, while hot areas might need cooling measures to ensure safe handling of materials.
The unique feature of temperature extremes is their capacity to impact not only the selection of materials but also how the work gets scheduled. Contractors must anticipate delays due to weather, making it a crucial consideration in both budgeting and timeline assessments. Investing in quality materials that can withstand specific climates can pay off in longevity and durability, which balances short-term expenditure with long-term peace of mind.
Precipitation Impacts on Construction
Precipitation is another crucial factor. Excessive rain or snowfall can delay projects significantly, leading to increased labor costs and material wastage. In regions prone to heavy rainfall, a concrete loading dock may require additional drainage features, significantly inflating both material and labor expenses.
A key characteristic of precipitation impacts is the potential for unexpected delays. Such delays can ripple through timelines, causing cascading costs that complicate budgeting. Moreover, choosing the right season for construction may lower these risks significantly; starting in a dry season can ease many cost concerns linked to weather.
Recognizing these climatic influences not only helps manage costs but also guides strategic planning for construction projects. By genuinely understanding both the broader geographical influences and specific environmental conditions, stakeholders can adopt a more informed and strategic approach to concrete loading dock construction.
Regulatory and Compliance Costs
When diving into the construction of concrete loading docks, understanding regulatory and compliance costs can make or break a project. These costs are not just extra numbers to worry about; they are essential checks that ensure the safety and longevity of the construction. From ensuring that the structure can handle the loads expected to meeting environmental standards, every regulatory guideline plays a critical role in both the design and building phases.
Building Codes and Standards
Local Codes
Local codes are the backbone of any construction project. These codes are specific to regions and outline regulations that consider the geographical and cultural nuances of a place. One key characteristic of local codes is that they adapt to the unique weather and soil conditions of the area. This is particularly beneficial, because it guarantees that any loading dock is designed to withstand local challenges, such as heavy rainfall in certain regions or high winds in others. The unique aspect of local codes is how they emphasize safety and structure integrity, which helps avoid costly repairs in the long run. Although navigating these codes can feel like wandering through a maze, adhering to them is crucial to ensure that the construction is not only legal but also practical and durable.
Environmental Regulations
When it comes to construction, environmental regulations can't be overlooked. These guidelines dictate how materials are sourced and waste is managed during the process, reflecting a growing consciousness about sustainability. The primary benefit of these regulations is that they encourage contractors to adopt eco-friendly practices. For example, some projects may require the use of recycled materials or mandate specific waste disposal methods. A unique feature of environmental regulations is their adaptability, as they are often updated to reflect the latest ecological findings. However, the flip side is that these regulations can sometimes slow down the construction process or increase initial costs. Yet, the long-term savings and positive environmental impact often outweigh these challenges.
Permitting Procedures
Navigating through permitting procedures can be a tedious task, yet it is an essential part of ensuring that your loading dock meets all necessary legal requirements.
Application Fees
One of the initial costs associated with this process involves application fees. These fees are usually required for submitting plans for approval and can vary significantly depending on the locality. They often include a range of administrative expenses, but understanding these costs upfront can help in accurate budgeting. The characteristic of these fees is that they tend to increase as the project scope expands. This aspect can be seen as beneficial, as it aligns the fees more with the complexity of the project. However, if one isn't well-prepared for these fees, they can come as a surprise.
Inspection Costs
Inspection costs play an influential role in determining the overall financial layout of your construction. Local governing bodies often require inspections at various stages of the build to ensure compliance with safety codes and standards. These inspection fees can pile up, depending on how many are needed. Yet, they are a necessary check - like a safety net that ensures every brick is laid correctly. The benefit of this is that inspections can catch potential issues before they become expensive repairs later on. However, some might argue that these costs can feel administratively burdensome during a busy project. In the grand scheme, though, they serve to protect both the investment and the safety of future users.
"Navigating the waters of regulation and compliance might feel like a headache, but it’s a step worth taking for a solid and secure structure down the road."
Understanding these regulatory elements not only helps in keeping a project on track but also reinforces the assurance that the loading dock will stand the test of time, both functionally and legally.
Cost Management Strategies
Cost management in concrete loading dock construction is not just about budgeting; it's a strategic imperative that can significantly affect the final outcome of any project. The ability to effectively manage costs will not only ensure that the project remains within budget but also enhances the overall value of the investment. By implementing smart cost management strategies, stakeholders can mitigate unexpected financial strain and ensure that every dollar spent contributes to long-term benefits.
One crucial element of cost management is identifying potential areas where unforeseen expenses might crop up. Think about it: when you’re planning a loading dock construction, the last thing you want is to be hitting the panic button mid-project because of unexpected costs. A well-structured financial plan allows you to allocate resources effectively and provides a buffer for those unpredictable bumps in the road.
Using cost management tools can also offer a clearer picture of financial flow. This might include software for budgeting and forecasting, which can allow project managers to predict costs and track spending in real-time. The advantage of being proactive can’t be overstated.
Budgeting for Unexpected Expenses
Budgeting for unexpected expenses is more than just a line in a financial plan; it's a safety net that can prevent the project from crashing down. Even the best-laid plans can go awry in construction, with variables like labor shortages, material price hikes, or even inclement weather raising their heads. It’s essential to set aside a contingency fund, typically about 10% to 20% of the total project cost, dedicated to handling these unexpected situations.
Important factors to consider when budgeting for unexpected expenses:
- Historical Data: Past projects can provide a benchmark for estimating these surprises.
- Flexibility in Plans: This allows for changes in scope, which often lead to unanticipated costs.
- Regular Reviews: Frequent budget reviews can help catch deviations early and allow for course adjustments.
"By planning for surprises, you're not just reacting to them; you're taking control of the situation."
Selecting Cost-effective Materials
Selecting cost-effective materials is another element that plays a vital role in managing construction costs. While it’s tempting to go for the cheapest option available, that's a recipe for disaster. You need materials that will stand the test of time and provide value without breaking the bank. Generally, it’s about finding that sweet spot between quality and cost.
The intrinsic recommendation here is to evaluate materials based on their lifespan, maintenance needs, and the suitability for the specific loading dock use. For instance, opting for a higher-grade concrete might seem expensive at first glance, but its durability can save money in repairs down the line. Alternatively, choosing recycled materials may be cost-effective while also showing commitment to sustainability.
Guidelines for selecting cost-effective materials:
- Source Locally: This often reduces transportation costs and supports community businesses.
- Compare Suppliers: Don't take the first bid you get—shop around to find the best deal.
- Assess Durability vs. Cost: Long-term performance often outweighs initial expenditure.
By being strategic in your approach to material selection and budgeting, you set the stage for a loading dock that's not only cost-efficient but also built to serve well for many years.
Future Trends in Concrete Loading Dock Construction
In an era where efficiency is king, knowing the future trends in concrete loading dock construction is paramount for stakeholders focused on maximizing both functionality and cost-effectiveness. As industries continue to evolve, so do the methods and materials we employ in creating these crucial infrastructure elements. Taking a forward-looking perspective helps businesses stand out in a competitive market, embracing new energy-saving solutions and innovative designs. Here’s a look at some of the exciting developments on the horizon.
Innovations in Material Technology
When it comes to material technology, the horizon is brightly lit with innovative solutions that promise to transform how loading docks are built. Concrete itself is under constant improvement, with advanced formulations being introduced. For instance, using high-performance concrete blends can enhance durability while reducing overall maintenance costs. Factors like
-
Self-healing concrete: This material contains specific bacteria that can mend cracks autonomously, offering longer lifefields and lowering repair costs.
-
Fiber-reinforced concrete: Adding fibers such as steel or synthetic materials to the mixture improves tensile strength and reduces shrinkage. This is a game-changer for loading docks, which are subject to heavy loads and constant traffic.
Additionally, the adoption of smart materials—those that can respond to environmental changes—can revolutionize dock effectiveness. Picture a concrete surface that adjusts its grip based on weather conditions, such as becoming less slippery during rain. These innovations not only enhance safety but also contribute to the longevity of the construction.
Furthermore, with advances in 3D printing technology, custom loading dock components can be manufactured on-site, reducing waste and cutting down transportation costs. Custom shapes and sizes meet specific needs and help in creating the perfect dock setup.
Sustainability Initiatives
Sustainability isn't just a buzzword; it's becoming a key tenet of modern loading dock construction. As environmental concerns mount, adopting sustainable practices will not only fulfill regulatory obligations but also align businesses with the values of an increasingly eco-conscious clientele. Here’s how sustainability is being woven into the fabric of loading dock projects:
-
Recycled Materials: The use of recycled aggregates in concrete mixes not only cuts costs but also minimizes landfill impact. Companies are leaning toward eco-friendly options that leverage materials from deconstructed buildings or repurposed industrial waste.
-
Energy-efficient Design: Innovations such as solar-powered lighting and water-efficient drainage systems are becoming more common. These systems can greatly reduce energy and water consumption, leading to substantial savings over time.
Consideration for green certifications, like LEED (Leadership in Energy and Environmental Design), is also gaining traction. Achieving these certifications may seem like another hurdle, but they can significantly enhance a company's marketability and open doors to environmentally-focused clients.
Efforts to improve logistics and transportation can further bolster sustainability. Efficient loading dock designs, including better traffic flow, can lower fuel consumption and emissions during loading and unloading activities, enhancing overall operational sustainability.
The future of concrete loading docks lies in innovation and sustainability, offering opportunities to cut down costs while making the construction process more efficient and environmentally friendly.
By recognizing the pressing need for innovation and sustainability in concrete loading dock construction, businesses can position themselves to navigate future challenges successfully while delivering value to their customers.
The End and Recommendations
In wrapping up our exploration of concrete loading dock construction costs, it's essential to consider the pivotal role this section plays in distilling the complex information we've navigated through. The importance of synthesizing insights into key takeaways cannot be overstated, especially for stakeholders who often juggle multiple factors that influence budgets, timelines, and project outcomes. When one zooms in on the conclusions drawn from this article, the significance lies not just in acknowledging the costs but also in strategizing effectively around them.
A comprehensive approach to costing offers numerous benefits. It empowers housewives and homeowners to make informed decisions, allowing them to weigh options carefully and prioritize what truly matters in their projects. This might involve evaluating material choices or ensuring compliance with local regulations. By identifying potential pitfalls—like fluctuating labor costs or permitting delays—homeowners can better anticipate and navigate any hurdles that may arise.
Summarizing Key Points
To crystalize the journey into concrete loading dock costs, let's summarize the critical points covered:
- Material Selection: The grade of concrete, reinforcement options, and finishes drastically affect overall expenses. Prioritizing quality often pays off in the long run.
- Labor Costs: Recognizing the differences between skilled and unskilled labor is vital; the former commands higher wages but delivers superior results.
- Design Variations: Custom solutions may hit harder on the budget but can enhance functionality and aesthetic appeal if well executed.
- Geographical Influences: Costs can vary significantly based on location—urban centers generally present higher expenses compared to rural areas.
- Regulatory Compliance: Understanding local building codes and navigating the permitting landscape can save both time and money.
- Cost Management Strategies: Smart budgeting, especially for unexpected expenses, is crucial to maintaining financial health throughout construction.
Being mindful of these key aspects helps ensure a smoother construction process and promotes successful project completion.
Final Thoughts on Cost Considerations
When diving into the nuances of concrete loading dock costs, one realizes that the landscape is far from straightforward. Homeowners often face decisions that carry weighty financial implications. Yet, pondering these costs goes beyond mere numbers; it fundamentally shapes the experience of how a dock functions within a home or business environment.
As final considerations, it’s wise for homeowners to approach construction with a clear strategy in hand. Continually ask questions like "What value does this particular aspect add?" or "Is this investment going to pay off in functionality or durability?" Such a mindset can lead to better decisions, avoiding the trap of accumulating unnecessary expenditures.
"An informed choice today can prevent headaches tomorrow."
With diligence and a proactive stance towards understanding and managing costs, creating a concrete loading dock can be a rewarding endeavor that stands the test of time.