Materials:
- Spray foam insulation: 20 cans (each canister containing 12 oz of material)
- Protective clothing: Nitrile gloves, safety goggles, respirator mask
- Drop cloths: 5 sheets of 9'x12' plastic sheeting
- Utility knife: to cut insulation to fit
DIY Steps:
-
Preparation: Start by ensuring the work area is well-ventilated and free of any obstructions. Put on protective clothing including nitrile gloves, safety goggles, and a respirator mask.
-
Prepping Surfaces: Lay down drop cloths to protect floors and surfaces from overspray during the application process. This will make cleanup easier once the project is complete.
-
Testing the Equipment: Before beginning the insulation process, check the spray foam insulation cans for any defects or damage. Shake each canister vigorously to ensure proper mixing of the materials.
Technical Aspects:
- Tools: Utility knife, gloves, goggles, respirator mask
- Timing Specifics: Allow sufficient time for the insulation to expand and cure according to the manufacturer's instructions. Typically, this process takes 24-48 hours.
- Critical Techniques: Maintain a consistent spraying distance to achieve even coverage and prevent drips or voids.
DIY Project Process:
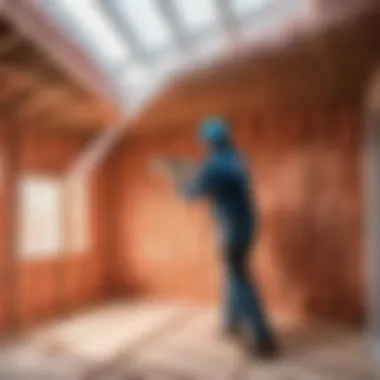
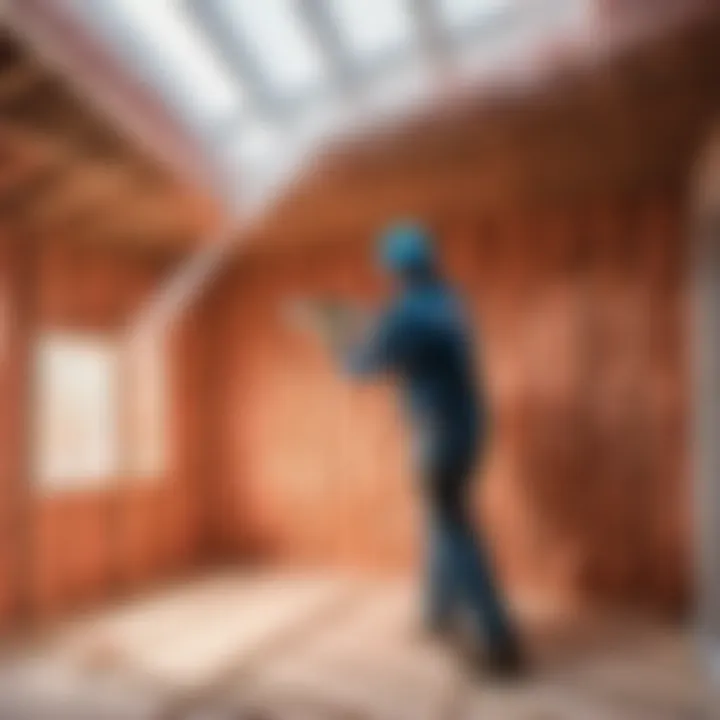
-
Spray Application: Begin by spraying the insulation in a continuous motion, overlapping each pass slightly to ensure thorough coverage. Work in small sections to control the application and avoid wastage.
-
Curing Period: Once the insulation is applied, allow it to expand and cure fully before touching or trimming any excess material. This ensures optimal insulation performance.
-
Trimming Excess: After the insulation has cured, use a utility knife to trim any excess foam protruding beyond the desired surface level. This step helps achieve a neat and finished appearance.
Troubleshooting Tips:

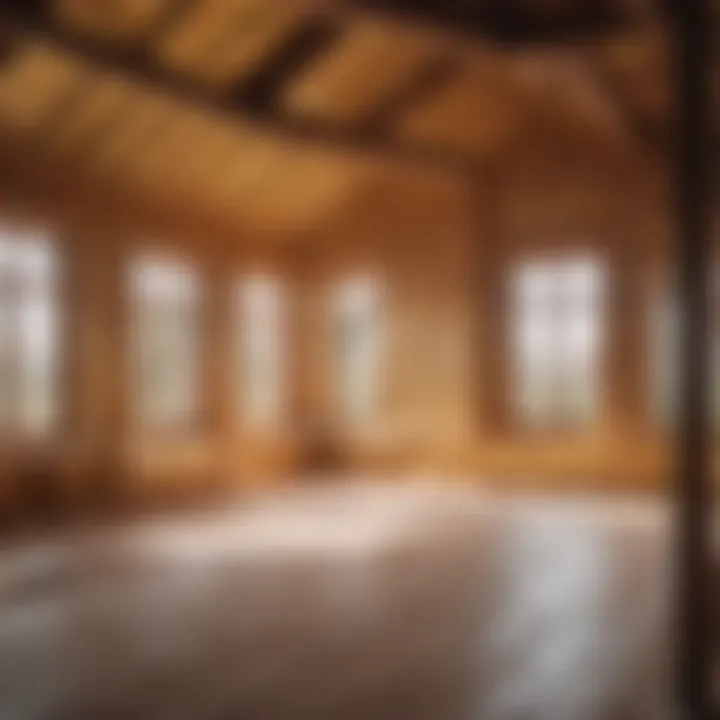
- Uneven Coverage: If you notice areas with uneven insulation coverage, reapply additional foam to ensure consistent thickness throughout.
- Clogged Nozzles: In case of clogging in the spray foam nozzles, clean them immediately with a manufacturer-recommended solvent to maintain optimal performance.
- Overspray Cleanup: Should overspray occur on unintended surfaces, use a solvent recommended by the manufacturer to remove the insulation without causing damage.
Continue the process meticulously to achieve a professionally insulated home. The attention to detail in each step will lead to an efficiently energy-efficient environment while keeping costs in check.
Introduction
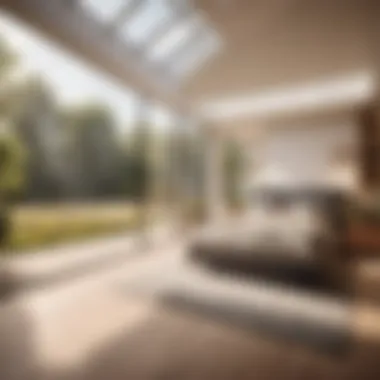
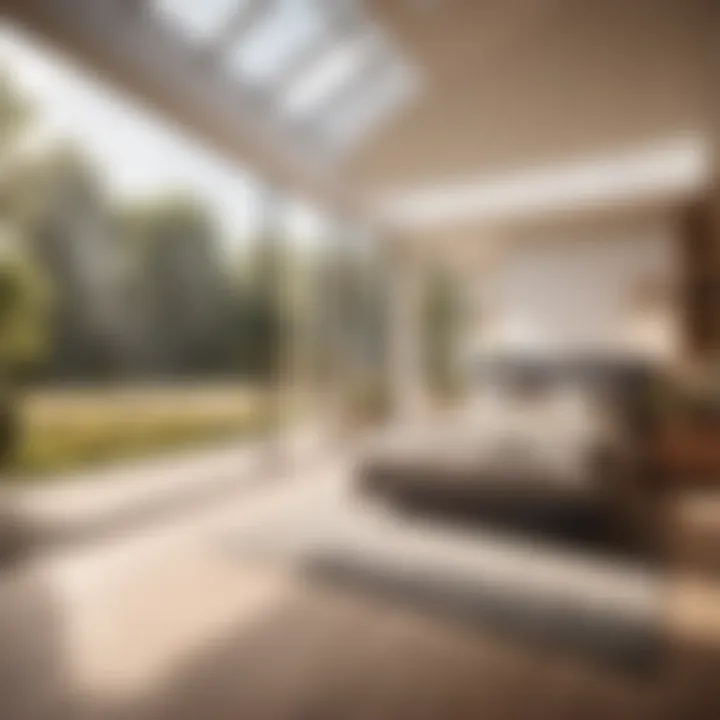
What is Spray Insulation?
Spray insulation stands out as a highly effective method for insulating residential properties, boasting superior insulating properties that conventional insulation materials may not offer. Unlike traditional insulations such as fiberglass or cellulose, spray insulation is applied as a liquid which then expands into a solid insulating material upon application. This unique characteristic allows spray insulation to reach tight spaces, cavities, and corners that other insulation types may struggle to cover adequately.
Moreover, spray insulation forms an airtight seal upon application, minimizing air leakage and providing exceptional thermal resistance. This feature not only enhances the insulation's efficiency but also contributes to improved indoor air quality by preventing dust and allergens from penetrating through the insulation barrier.
Beyond its insulation capabilities, spray insulation serves as a sound barrier, reducing noise transmissions between rooms within the house. This added benefit can significantly improve the overall comfort levels within your home, creating a more peaceful and serene living environment.
In essence, spray insulation emerges as a cutting-edge solution for homeowners seeking high-performance insulation. Its ability to provide comprehensive coverage, enhanced energy efficiency, and improved indoor air quality make it a top choice for those looking to invest in a durable and sustainable insulation solution.
Factors Influencing Cost
Type of Insulation Material
When considering the cost of spraying insulation for your house, the type of insulation material used is a critical factor to analyze. Different insulation materials come with varying price points and efficiency levels. For instance, spray foam insulation tends to be more expensive initially but offers long-term energy savings, while fiberglass insulation may be more budget-friendly but slightly less efficient. Understanding the pros and cons of each type of insulation material can help homeowners choose the one that best suits their needs and budget.
Size of the House
The size of the house is another significant factor that influences the cost of spraying insulation. Larger homes require more insulation material and labor hours to complete the project, leading to higher overall costs. Conversely, smaller houses may have lower insulation costs due to their reduced square footage. It is essential for homeowners to consider the size of their house when estimating the budget for spraying insulation, ensuring that adequate coverage is achieved without overspending.
Complexity of the Project
The complexity of the project plays a key role in determining the cost of insulation. Projects that involve intricate architectural details, multiple stories, or hard-to-reach areas may require additional time and resources for proper insulation coverage. As a result, the complexity of the project can impact the overall cost, requiring homeowners to budget accordingly for any potential challenges that may arise during the insulation process.
Preparation Work Needed
Before spraying insulation in a house, certain preparation work is often required to ensure a smooth and effective application. This preparation work can include cleaning the area to be insulated, sealing any gaps or cracks, and removing obstacles that may hinder the insulation process. The extent of preparation work needed can vary based on the condition of the house and its existing insulation, affecting the overall cost of the project.
Labor Costs
Labor costs represent a significant portion of the total expenses when spraying insulation in a house. Professional insulation contractors charge based on factors such as the size of the project, labor hours involved, and complexity of the work. Homeowners should obtain multiple quotes from reputable contractors to compare labor costs and ensure they are receiving fair pricing for the insulation project. Understanding the breakdown of labor costs provides transparency and helps in budgeting effectively for the overall project cost.
Types of Insulation Materials
In the realm of residential insulation, the choice of insulation material is paramount in determining the effectiveness, longevity, and cost-effectiveness of the insulation. Understanding the various types of insulation materials available is crucial for homeowners looking to make informed decisions about their home improvement projects. Each type has its unique characteristics, benefits, and considerations that influence the overall cost of spraying insulation in a house.
Spray Foam Insulation
Spray foam insulation is a popular option known for its exceptional insulating properties. It is a versatile material that can expand to fill gaps and cracks, creating a seamless barrier against heat loss or gain. This type of insulation provides high R-values, ensuring excellent energy efficiency. However, it tends to be more expensive than other materials due to its superior thermal performance. Homeowners opting for spray foam insulation should consider its upfront cost, long-term savings on energy bills, and the professional installation required for optimal results.
Fiberglass Insulation
Fiberglass insulation is a common and cost-effective choice for many homeowners. It consists of tiny glass fibers that trap air, providing a barrier against heat transfer. Fiberglass insulation is relatively easy to install, making it a budget-friendly option for insulating attics, walls, and floors. While it is an affordable choice upfront, it may require professional installation to ensure proper coverage and effectiveness. Considerations such as R-value, durability, and the presence of formaldehyde should be factored in when evaluating the cost of fiberglass insulation.
Cellulose Insulation
Cellulose insulation is an environmentally friendly option made from recycled paper or cardboard treated with fire-retardant chemicals. It offers good thermal performance and soundproofing qualities, making it a popular choice for homeowners seeking sustainable insulation solutions. The cost of cellulose insulation may vary based on factors such as location, installation method, and desired R-value. Homeowners should also take into account considerations like moisture resistance, settling over time, and the need for proper ventilation when assessing the overall cost of cellulose insulation.
Polyurethane Foam Insulation
Polyurethane foam insulation is known for its high insulating properties and moisture resistance. It can be either sprayed or injected into walls, ceilings, and floors, forming a durable and airtight barrier that reduces energy consumption. While polyurethane foam insulation generally has a higher initial cost compared to other materials, its energy-saving benefits and long-term performance make it a worthwhile investment for homeowners looking to enhance the energy efficiency of their homes. Factors to consider when evaluating the cost of polyurethane foam insulation include the type of polyurethane foam used, the thickness of the application, and the expertise required for installation.
Determining Costs
In the realm of spray insulation for residential houses, determining costs holds paramount significance. This vital step involves a comprehensive breakdown of the expenses associated with the insulation project. By focusing on determining costs, homeowners can gain clarity on the financial aspects essential for planning and executing their insulation endeavor effectively.
Understanding the specific elements that contribute to determining costs is crucial. Factors such as the type of insulation material selected, the size of the house, the complexity of the project, and the labor costs all play a pivotal role in the overall cost estimation. By delving into these elements, homeowners can make informed decisions and tailor their insulation project according to their budget and requirements.
The benefits of accurately determining costs are manifold. Firstly, it ensures that homeowners have a realistic understanding of the financial investment required for the insulation project. This empowers them to set a feasible budget and avoid unexpected expenses along the way. Additionally, by estimating costs upfront, homeowners can identify potential cost-saving opportunities and explore different insulation options that align with their budgetary constraints.
When considering determining costs, it's essential to take into account various considerations. Homeowners should seek quotes from multiple insulation contractors to compare prices and services offered. Conducting thorough research on different insulation materials and their costs can also aid in determining a suitable budget. Furthermore, factoring in any additional expenses, such as preparation work or potential material wastage, is crucial for a comprehensive cost estimation.
Estimating Material Costs
Estimating material costs is a pivotal aspect of determining the overall expenses involved in a spray insulation project. The type and quantity of insulation material needed significantly impact the total cost of the project. Different insulation materials vary in price and performance, making it essential for homeowners to conduct thorough research to select the most cost-effective yet efficient option.
To estimate material costs accurately, homeowners should first assess the area that requires insulation. Calculating the square footage of the walls, ceilings, or floors to be insulated can help determine the amount of material needed. Additionally, considering the R-value and thermal resistance of the insulation material is crucial, as higher-quality materials may come at a higher cost but provide better energy efficiency in the long run.
Moreover, obtaining quotes from various suppliers and insulation manufacturers can aid in comparing prices and finding the best deals. It's also advisable to consult with insulation professionals to gain insights into the most suitable material for specific areas of the house. By investing time in estimating material costs, homeowners can make informed decisions that balance quality, cost-effectiveness, and energy efficiency.
Calculating Labor Costs
Calculating labor costs forms an integral part of understanding the total expenses associated with a spray insulation project. While material costs are significant, the expertise and services provided by insulation professionals also contribute to the overall project cost. By accurately calculating labor costs, homeowners can align their budget and expectations with the services required for a successful insulation installation.
When it comes to calculating labor costs, several factors come into play. The complexity of the project, the time required for installation, and the skill level of the insulation contractors all influence the labor costs. Additionally, the location of the house and market rates for insulation services can impact the overall labor expenses.
To calculate labor costs effectively, homeowners should obtain detailed quotes from licensed insulation contractors. Understanding the breakdown of labor charges, including hourly rates or project-based fees, can provide transparency and clarity regarding the labor expenses. It's advisable to discuss any additional services or unforeseen circumstances that may affect labor costs to avoid budgetary surprises during the project.
Considering Additional Expenses
Apart from material and labor costs, homeowners should also consider various additional expenses that may arise during a spray insulation project. These extra costs can contribute significantly to the overall budget and should be factored in during the planning phase to ensure a comprehensive understanding of the total expenses involved.
One common additional expense to consider is the preparation work needed before insulation installation. This may include cleaning the area, repairing any damages, or removing existing insulation materials. Hiring professionals to handle preparatory tasks can incur additional costs but is crucial for ensuring a smooth and efficient insulation process.
Moreover, homeowners should account for any unexpected material wastage or adjustments required during the installation phase. Allocating a buffer in the budget for such contingencies can prevent budget overruns and accommodate unforeseen circumstances without disrupting the project timeline.
Additionally, considering post-installation costs such as cleanup and disposal of waste materials is essential. Ensuring that the work area is left clean and debris-free after the insulation project adds to the overall cost but contributes to a satisfactory end result.
By proactively considering these additional expenses and integrating them into the overall budget, homeowners can embark on their spray insulation project with a comprehensive financial plan and minimize the risk of cost overages.
Cost Range for Different House Sizes
In the realm of residential insulation, understanding the cost range for different house sizes is a pivotal component. The size of a house directly influences the overall expense of spray insulation, making it a significant factor to consider.
Small, medium, and large houses each present unique challenges and cost implications when it comes to insulating them effectively. Small houses generally require less material and labor compared to their larger counterparts. This is due to their reduced surface area and typically simpler layouts, resulting in a more straightforward insulation process. However, the cost might be higher per square foot due to minimum labor charges.
Medium houses strike a balance between small and large homes in terms of both cost and complexity. With more surface area to cover than small houses but less than large houses, the cost of insulating a medium-sized home falls somewhere in between. It's crucial to consider the intricacies of these homes to accurately estimate the materials required and the labor involved.
Large houses pose a greater challenge due to their extensive surface area and often intricate designs. Insulating a large house demands more material, time, and labor, contributing to higher overall costs. The complexity of insulating large houses can drive up expenses, especially when additional preparation work is needed to ensure thorough coverage and efficiency.
In essence, the cost range for different house sizes enlightens homeowners on the varying financial commitments associated with spray insulation. Understanding how size influences costs can aid in budgeting effectively and planning for an energy-efficient home.
Small Houses
Small houses offer a unique insulation scenario due to their compact size and simpler layouts. Insulating a small house tends to be more straightforward compared to larger residences. The limited surface area reduces the overall material and labor requirements, impacting the cost positively. However, as smaller projects often entail fixed minimum costs, the price per square foot may be higher than larger homes. Homeowners opting to insulate small houses should focus on selecting cost-effective insulation materials.
Medium Houses
Medium houses present a middle ground in terms of insulation cost and complexity. These homes offer a balance between surface area and intricacy, requiring a moderate amount of insulation material and labor. Insulating a medium-sized house involves covering more space than a small dwelling but less than a large estate. It's essential to factor in both the size of the house and the intricacies of its design when estimating costs for insulation. Homeowners with medium houses can benefit from seeking efficient insulation solutions that offer a good balance between cost and effectiveness.
Large Houses
Insulating a large house poses significant challenges due to the extensive surface area and complexity of these residences. Large houses require a substantial amount of insulation material and labor to ensure comprehensive coverage. The intricate designs and architectural features common in large homes contribute to higher costs, as additional preparatory work is often necessary. Homeowners undertaking insulation projects for large houses should allocate sufficient budget to cover the expenses associated with size and complexity.
Conclusion
Spraying insulation in your house is not just about improving energy efficiency; it is an investment in your home's comfort and sustainability. This article has delved deep into the intricate aspects that influence the cost of insulation, shedding light on the critical factors that homeowners should consider. Understanding the cost of spraying insulation allows homeowners to make informed decisions, balancing quality and affordability to achieve long-term benefits.
Throughout this article, we have emphasized that the type of insulation material, the size of the house, the complexity of the project, the preparation work required, and labor costs all play pivotal roles in determining the overall cost. By comprehensively analyzing each of these factors, homeowners can gauge the expenses involved and plan their insulation projects effectively.
One of the key takeaways from this article is the significance of thorough research and cost estimation before initiating an insulation project. By conducting a detailed assessment of material costs, labor expenses, and additional outlays, homeowners can avoid unexpected financial surprises and ensure a smooth and successful insulation process.
Moreover, considering the long-term benefits of a well-insulated home, the cost of spraying insulation can be viewed as a strategic investment rather than a mere expense. Energy savings, increased property value, and enhanced comfort are some of the compelling advantages that justify the initial cost outlay and reinforce the importance of proper insulation in any residential setting.
Final Thoughts
Understanding the cost implications of spraying insulation for your house is a fundamental aspect of home improvement that requires careful consideration. While the upfront expenditure may seem significant, the long-term benefits far outweigh the initial investment. By opting for energy-efficient insulation solutions, homeowners not only enhance their living spaces but also contribute to environmental conservation.
Finalizing the details of an insulation project involves meticulous planning and a clear understanding of the factors that influence costs. Striking a balance between quality, affordability, and effectiveness is crucial in attaining optimal results and maximizing the value of your investment. Ultimately, the decision to spray insulation in your house is not merely about cost; it is a strategic choice towards sustainability and enhanced living standards.